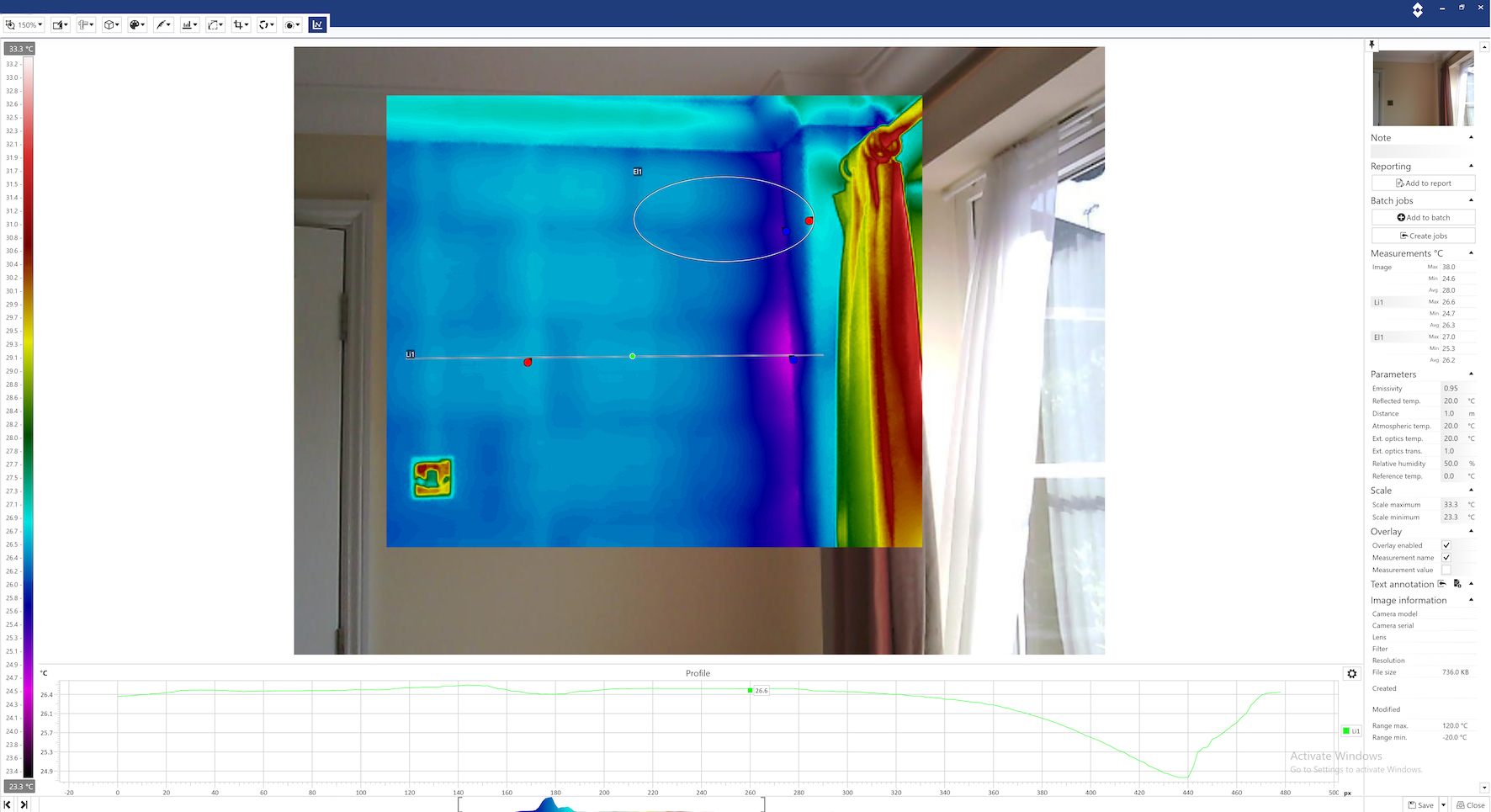
An introduction to building thermography © Richard Bedford Surveying Ltd
Everything above absolute zero, –273.15 ºC, emits thermal radiation to varying extents, and most of the emitted thermal radiation belongs to the infrared (IR) end of the spectrum, invisible to the human eye.
Depending on its intensity, the environmental conditions and the characteristics of the surface emitting it, temperatures can be determined by using thermal imaging cameras. Thermal images, or thermograms, are created using a number of radiometric pixels on a thermal imaging camera’s sensor, commonly known as a focal plane array. These images comprise thermal patterns using different colours or shades of grey.
Enhanced inspection technique
Building applications are a relatively new and exciting area for thermography as a way for surveyors to enhance their inspections.
- dampness
- missing or incomplete insulation
- thermal comfort issues
- cold bridging leading to condensation or mould
- leaks from underfloor heating pipework
- electrical overheating issues that could lead to fire
- failed double or triple glazing to windows
- external issues associated with de-bonding of render or other cladding.
Of particular interest to many surveyors however, including those inspecting sensitive properties such as listed buildings, is the fact that building thermography is completely non-invasive and comparatively quick. It enables swift and efficient inspections of, for example, a roof surface that may not be safe to stand on, or a ceiling too high to inspect without access equipment such as scaffolding.
Thermographic inspection of a building; to the left, a thermogram taken in the morning, and to the right a thermogram of the same building at night. The latter is taken sufficiently after sunset to give a more accurate representation of potential issues as it is not affected by solar loading.
Types of inspection
There are two main types of inspection in which surveyors may use building thermography – qualitative and quantitative.
Qualitative inspections do not involve any formal recording of temperatures. Instead they relate to the analysis of thermal images to determine whether defects or anomalies are present in the property being inspected.
A simple example of this could be where an internal wall shows a darker blue area, as in the thermogram below; in this instance, the colour indicates a surface colder than its surroundings. Once this is determined, all likely causes of cold surfaces need to be taken into account and then either rejected or accepted as the probable reason.
It is crucial to note that cold surfaces can be caused by a number of factors including dampness, missing or incomplete insulation, structural cold bridging or the effects of air infiltration and other convective forces. Surveyors should therefore always confirm the cause rather than rely solely on any single inspection technique. Critically, suspected dampness should always be confirmed through the use of a damp meter as well as thermal imaging.
With qualitative inspections, no temperature measurements are recorded. To the left: the colder area is noted due to the suspected presence of an uninsulated, boxed-in soil pipe to the right of the image. The thermogram also confirms that the rear wall is made up in blockwork with the presence of hidden electrical conduits indicated by two light vertical lines, neither of which are visible to the naked eye. To the right: a thermogram of a hot cup of coffee showing the effects of convection, conduction, emissivity and the effect of viewing angle.
Quantitative inspections involve recording temperatures, and as such the requirements for the surveyor and their thermographic competency are much higher. This is because a thermal imaging camera only assesses the total intensity of thermal radiation it receives, which not only comes from the intended target such as a wall, ceiling or the like, but also from a number of other environmental sources.
To make matters even more complicated, the surveyor needs to make other adjustments to allow for the varying emissivity levels of the surfaces of materials being inspected. For example, human skin has a very high emissivity of 0.97 or 97%, whereas that of a polished metal surface may only be 0.15 or 15%.
A high-emissivity surface will give off a considerable percentage of its thermal energy in the form of thermal radiation and therefore can be recorded with greater confidence. A low-emissivity surface releases much less, and a large percentage of what is actually seen by a thermal imaging camera could in fact be radiation reflected from elsewhere.
Therefore, formal training and certification is essential should a surveyor wish to undertake any form of quantitative inspection.
In quantitative inspections, temperature measurements are recorded. Adjustments need to be made to allow for surface emissivity, reflected apparent temperature, environmental conditions and distance, although some of these adjustments can be made in dedicated software after an inspection. To the left: a thermogram showing the external inspection of a dwelling. To the right: a internal inspection thermogram showing a domestic lightbulb.
The importance of training
Surveyors are strongly advised to undertake formal training if they intend to reproduce any thermographic inspections in their reports, because they are highly likely to be asked – in the worst-case scenario while standing in front of a judge – whether they are competent and formally trained in thermography.
It is possible for surveyors to use thermography as they would any other inspection method and their thermal camera as just another tool, without their reports containing any thermal images or reference to the technique. However, when thermography is referred to in reports or any use is made of quantitative inspection, a surveyor is immediately at greater risk of scrutiny – and rightfully so.
I believe that even where surveyors carry out informal qualitative inspections they would benefit tremendously from a minimum level of training. I say this as thermography is a quite complex science in its own right, and the unwary surveyor is likely to misidentify anomalies and defects. Day or foundation courses and various kinds of higher learning are available from a number of specialist thermography training organisations.
“Surveyors are strongly advised to undertake formal training if they intend to reproduce any thermographic inspections in their reports”
Equipment requirements
I am often contacted by fellow surveyors and other property professionals on this subject, as many want to embrace thermography but are not sure what equipment to buy.
Assuming you have, or plan to take, some kind of training, my first question is: what do you want to do? Do you want to use thermography as an additional tool to help identify defects relating to internal damp or missing insulation, for example, but do not intend to include any thermographic information in your written reports?
If you will not be recording any apparent temperatures formally then this makes your inspection qualitative in nature. Where this is the case, you may choose to use an entry-level camera, which presently cost around £650. However, if you want to undertake more formal inspections and incorporate your findings into a report, you may need to upgrade to a higher-specification device, and these can cost more than £2,000 at present.
A higher-specification camera will also be needed as soon as you step outside a building. As a surveyor offering external inspections and reports, you will need to purchase one with a minimum IR resolution of 320 x 240 pixels and a thermal sensitivity of 60 millikelvin or even greater precision, in my opinion.
The IR resolution of a thermal imaging camera represents the number of pixels in the images it produces. With higher resolution, each image contains more information: more pixels, more detail, and a greater likelihood of getting an accurate measurement. In general terms, meanwhile, thermal sensitivity describes the smallest temperature difference you can see with the camera.
The cost of a thermal imaging camera rises steeply with every incremental increase in IR resolution and thermal sensitivity. Overall costs involved can be significant and do not relate solely to the purchase: the camera will need to be calibrated annually if used quantitatively, and it will also require dedicated software to analyse thermograms and produce reports. It would be prudent to fully insure the not insignificant investment made as well.
Finally, formal training currently ranges in cost from around £400 for a one-day foundation course to £1,700 and beyond for higher-level courses.