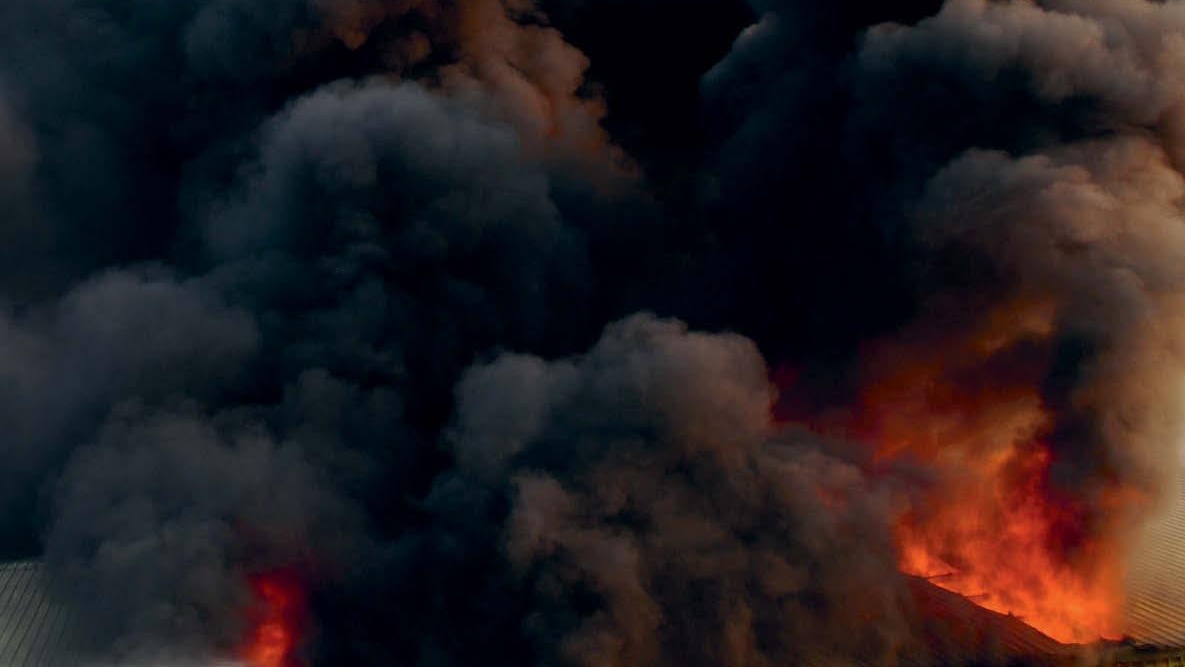
In May, BBC1's Watchdog exposed issues with missing cavity barriers in more than 650 new UK dwellings.
This is not an entirely new issue, and work has been done over the years to maintain awareness of the importance of cavity barriers and their correct installation; but the construction industry is inconsistent in meeting Building Regulations requirements.
Cavity barriers are present on almost every building, being used to close concealed spaces and prevent penetration of smoke or flame. The cavities in wall and ceiling voids are a pathway for fire to spread, and are normally be fitted with barriers during construction. Approved Document B gives clear guidance on what cavity barriers are, and when and where they should be installed; there are only one or two situations when they are not required.
Approved Document B2 and BS 9991 both state that, where barriers are necessary, they should have a minimum of 30 minutes' integrity and offer 15 minutes' insulation. Both documents also allow cavity barriers to provide only 30 minutes' integrity for the perimeter of windows; clause 19.2 of BS 9991 and Approved Document B cite 0.5mm-thick steel and 38mm timber as suitable cavity barrier materials. If correctly followed, this guidance means that cavity barriers, compartmentation in roof voids and fire-rated ducts and dampers will comply with the regulations.
The crucial issues in barrier performance are the quality of work and product selection. However, a Building Research Establishment (BRE) review carried out between 2003 and 2013 found that applications to building control bodies to confirm that cavity barriers and compartmentation in roof voids are compliant often fail to provide sufficient detail to allow them to do so. The completed compartmentation is frequently not being seen by building control bodies or audited by the contractor before construction itself is completed.
The performance of cavity barriers in external wall construction, even those incorporating combustible material such as a timber frame, has demonstrated that all commonly used types can inhibit the spread of fire for a reasonable period when specified correctly and installed in accordance with the manufacturer's instructions. This performance is, however, compromised if any gaps are present or if the barrier is not correctly fitted.
- 11 were solely related to compartmentation in roof voids
- ten were solely related to issues with cavity barriers
- six of the fires combined the two issues above
- four were related to ductwork
- one was related to ductwork and compartmentation in roof voids
- one was related to ductwork and cavity barriers.
- BRE found that the main issues were as follows:
- there were seven cases where the junction of the compartment wall and roof was either not fire-stopped or the fire-stopping was found to be inadequate
- there were three where push-fit cavity barriers were either moved after construction or poorly fitted in the first place
- 20 involved missing or poorly installed cavity barriers
- two cases involved ducts passing through compartment walls without being fire-stopped
- there were five cases where mineral wool in wire mesh was used as a cavity barrier in a roof space but proved inadequate due to holes in the material.
"The crucial issues in barrier performance are the quality of work and product selection"
Only three cases were identified where compartmentation in the roof space was effective and had prevented further fire spread.
The largest single issue in all the fires remains that of construction quality. BRE's study found that poor-quality work with inappropriate materials is the main reason for the inadequate protection of concealed spaces. Design, specification, installation and inspection of fire safety measures for such spaces are also inconsistent; however, guidance is available to ensure that the unseen spread of fire and smoke is inhibited, as required by the Building Regulations.
Work is also being done following the Hackitt review's recommendations to ensure that materials are easily identifiable, design changes are tracked and – through initiatives such as toolbox talks – installers are able to identify the correct routine. The clear failings in the developments highlighted by the BBC and the BRE have shown, too, the important role that independent third-party accreditation schemes play in ensuring cavity barrier products are installed correctly. This was reinforced by the value placed on increased inspection and the clerk of works role in the Hackitt review.
Getting cavity barriers correct starts during detailed design to ensure the works comply at construction stage; on some large schemes this extends to the planning stage, to ensure the products specified in the planning application work as a system during construction. Manufacturers and organisations such as the Association for Specialist Fire Protection provide technical guidance to ensure the correct product is installed in the appropriate location. For those working on buildings more than 18m high, any cladding should follow the approved and tested system when installed. Currently, desktop assessments that allow for variations in the system are prohibited, while the scope of their use is being redefined.
Specified products should be clearly marked on plans, and if the final product selection is yet to be undertaken then surveyors should make any approvals conditional on the proposed products being assessed before ordering or installation.
Not all installation processes are the same, so designers and surveyors should familiarise themselves with whichever one is being installed. The contractor should also be recording the process and, through quality assurance, be able to prove that installations accord with the product specification. The surveyor should then be able to check that the correct product is installed in the correct location, or have sufficient evidence to do so when modern methods of construction are used and it isn't possible to see cavity barriers being factory-installed.
Internal cavity barriers to roof or ceiling and to floor voids should be specified in the same way. Care should be taken by designers to ensure it is possible to repair any damaged barriers, and surveyors need to make sure that as a result of the works the building is not left in a state that is less compliant.
Indeed, a recent Built Environment Journal article by Assent Building Control director Martin Conlon emphasises this need to make certain that, when work is undertaken to existing premises, we don't hand over buildings or floors where defects have not been addressed.
So the construction industry still has work to do; but, following evidence provided to the Grenfell Tower inquiry and the issues raised by Watchdog, there is a greater understanding of what must be done to ensure the regulatory requirements are met.
John Miles is a technical and business development manager at Assent Building Control johnmiles@assentbc.co.uk
Related competencies include: Building control inspections, Fire safety