In recent years, lenders, investors, owners and occupiers have been seen to talk of the importance of environmental, social and governance (ESG) criteria, and have often made aspirational commitments to reduce carbon emissions.
However, we are now past those early days of glossy ESG brochures and ambitious targets to achieve net zero, and have realised the true scale of the challenge.
Every real-estate and construction decision effectively now needs to be viewed in terms of its carbon impact.
Construction project performance can no longer just be thought of in terms of time, cost and quality, with carbon emissions now being a critical factor in every decision as well.
Industry adopting more sustainable practices
Pressure to reduce carbon is now pushing the industry towards net zero, and main contractors, subcontractors and supply-chain partners have all made similar commitments to shift towards eco-friendly practices.
Significant progress has been made across the industry. Increasingly, changes to procurement methods are influencing carbon performance on projects, particularly off-site construction of building components and the reuse of materials.
There are also now certified schemes for specifying reused materials, such as environmental product declarations (EPDs). These enable materials to be deconstructed, certified and reused on new projects to reduce carbon.
Meanwhile, where refurbishment is viable, planning policy is effectively preventing redevelopment on the grounds of carbon and environmental impact.
This was demonstrated recently with Marks & Spencer's high-profile Oxford Street store in London, where demolition and replacement were rejected in favour of reusing the existing building, largely on environmental and sustainability grounds.
Other than planning policy, however, there is no regulation as yet relating to the reduction of carbon emissions in the built environment, whether whole-life, in use or embodied.
But it is surely only a matter of time before such a measure is introduced.
Process and perception inhibit reuse
There is ever-increasing motivation from the top down and bottom up to reduce carbon emissions in the built environment, and to reuse materials and support a circular economy.
But other market pressures and legislative requirements can make this process hugely challenging during due diligence and construction work.
While perceptions are changing and significant progress has been made, the commercial requirements of institutional investors, lawyers, lettings and marketing processes are hurdles for project design teams.
Warranty provisions, aesthetics and perceptions of marketability often sadly mean that new installations are still selected instead of reusing building components.
The insurance market, building and fire regulations, manufacturers' requirements, and evidence of maintenance and fire integrity, are just some of the criteria that add significant complications for consultants and contractors when trying to retain existing building components on projects.
Due diligence, meeting regulation and similar processes are, of course, critical to demonstrate compliance and performance; but market perceptions of buildings are more subjective.
Progress has certainly been made, but the supply chain and market are needing to continually adapt to make the reuse of existing components more acceptable, compliant and easier to achieve in practice.
'The supply chain and market are needing to continually adapt to make the reuse of existing components more acceptable, compliant and easier to achieve in practice'
Repurposing products hits a wall
A simple example of why further change is needed is the difficulty of reusing raised access floors in refurbishment projects: these regularly find themselves high on the list of projects' embodied carbon, at around 5% of total carbon on a new-build project.
The supply chain has found ways to recycle tiles, refurbishing and repurposing them in the same or other buildings.
These tiles don't, however, have the same warranty provision or shine as new products, meaning their reuse is rejected as they detract from speculative marketing to prospective tenants and buyers.
The rest of the raised-floor system is even worse. For instance, the stands pedestals that raise the tiles and create a void below for cabling and other services are typically fixed to a floor screed mechanically or adhesively, so cannot be reused.
But surely it is a matter of time before raised floors are fully demountable and can simply be dismantled, tested, re-warranted and reinstated?
Perhaps a more technical example is the reuse of wall finishes on projects, particularly drylining. Is it feasible for existing plasterboard to be tested to demonstrate its performance – particularly fire compartmentation – and warranted?
For the purposes of simplicity and compliance, those responsible decide in many instances to remove existing plasterboard and install new.
But the industry is beginning to work through these and similar issues to support a circular economy model.
Simplifying testing could help pass tipping point
A final consideration is that the testing and due diligence required to enable reuse of materials is hugely intensive – hundreds of surveys and tests can be needed on a single project.
While testing and due diligence is always necessary to some degree, the process has to be as simple as possible to enable reuse of materials. Currently, these lengthy testing processes may be preventing reuse in some instances.
The built environment and real-estate markets could be at a tipping point, though.
Acceptance of material reuse as a viable approach is increasing, potentially at the expense of commercial factors. But further progress is needed to enable full participation in the circular economy and sustainable practices.
This continuing shift in market mindset is essential to align the industry with the goal of reducing carbon emissions and to mitigate the environmental impacts of its activities.
RICS champions sustainability across professions
With the built environment estimated to be responsible for around 40% of global carbon emissions, RICS is championing sustainable practices across the built and natural environment. We are also empowering professionals to embed sustainability considerations into the way they work and better measure environmental impacts.
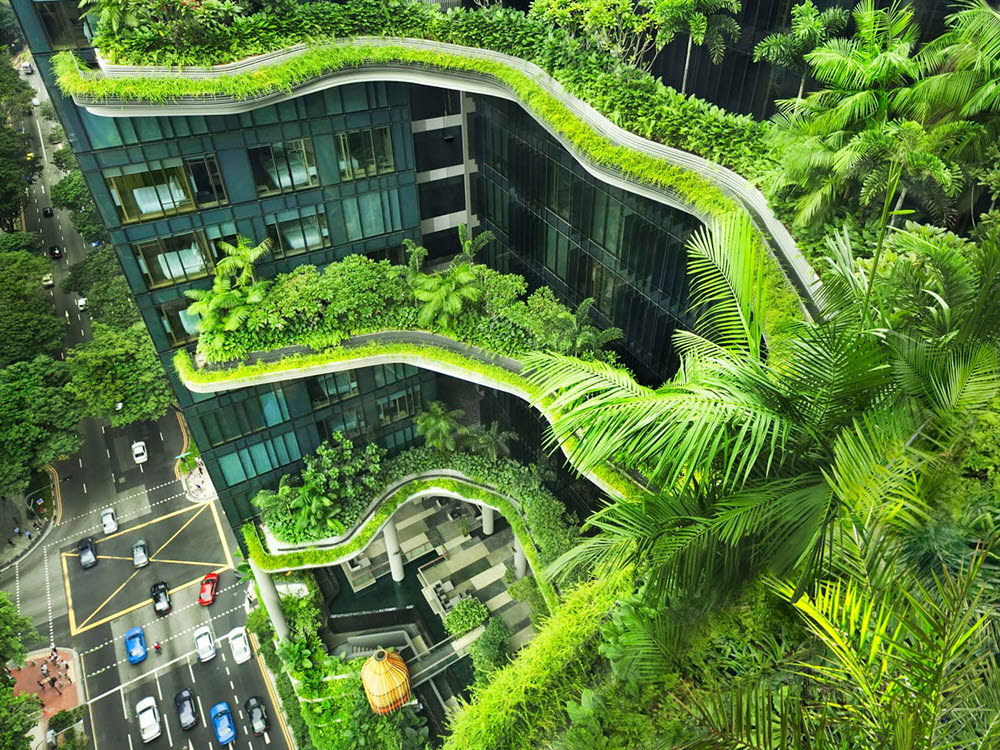