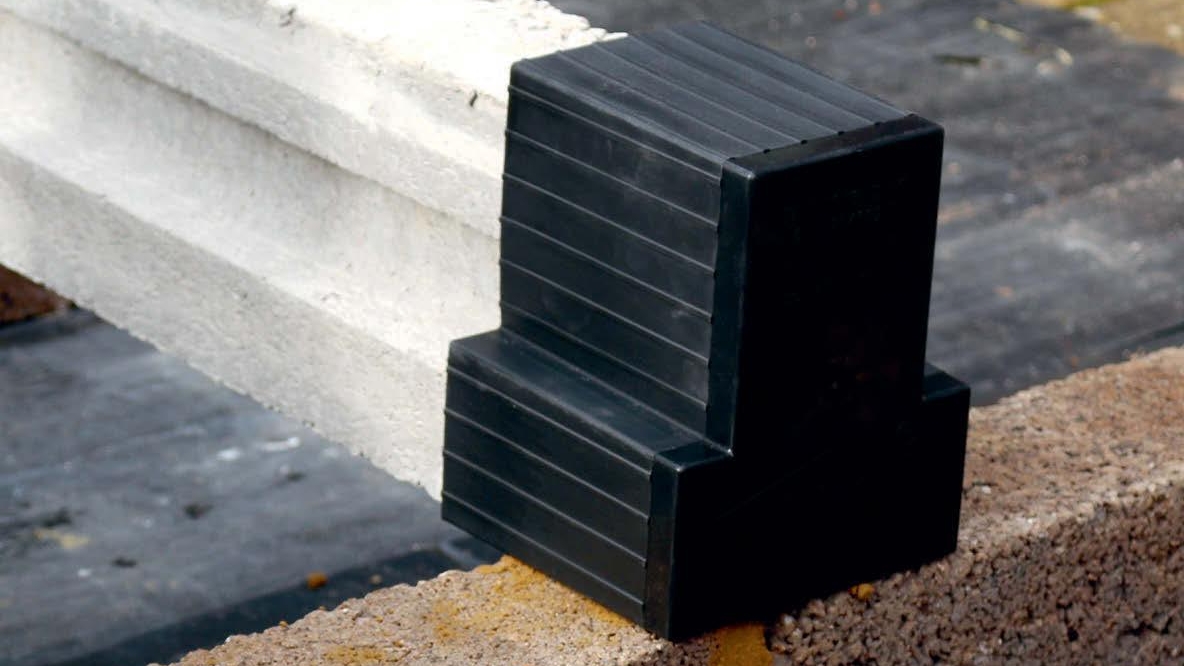
IMAGES © K-KAPS
Around 69 per cent of UK new-build housing and domestic extension ground floors are now being constructed with block and beam systems, according to analysis published by BDS Marketing Research in 2018. But, compared to the more traditional use of concrete slabs for the ground floor, such systems present various challenges when it comes to ensuring adequate damp protection.
The relevant requirement is described in Approved Document C, section 4.17: 'Any suspended floor of in situ or precast concrete, including beam and block floors next to the ground will meet the requirement if it will adequately prevent the passage of moisture to the upper surface and if the reinforcement is protected against moisture'. While the requirement is clear, though, it is not universally understood or met, with protection of the reinforcement against moisture being a particular issue.
Prevention of moisture passage to the upper surface is reasonably easy to achieve by the common practice of laying damp-proof course on the internal foundation wall before the beams are installed. However, a 3.6m length of concrete beam can easily exceed 130kg, which does make manoeuvring difficult and potentially hazardous. It is essential that appropriate manual handling procedures are followed and good care taken to ensure that the damp-proof material is not moved or compromised as the beams are laid on it.
The manufacturing process for the beams does leave them with rough surfaces, which combined with their weight means the damp-proof material can easily be moved, punctured or torn as the beams are positioned. Concrete floor beams are manufactured in 150m lengths and then cut to stock or bespoke sizes. Once cut, though, the internal steel wire reinforcement ends are exposed leaving them without the requisite 40mm depth of concrete covering to provide protection.
With the beam ends exposed to damp and moisture in the foundation void below the main building damp-proof course level, there is potential for long-term corrosion of the reinforcement; although there is no current evidence to support this, it may affect the structural integrity of the building. Protecting the exposed ends of these steel reinforcing bars is the concern of the second part of Approved Document C section 4.17. This is somewhat more challenging and less straightforward than upper surface protection.
Building control surveyors familiar with both parts of the section are now rightly asking for the beam ends to be protected. There has until recently not been any fully effective way of doing this and the three most common methods have been: painting with a bitumen compound which has an inherently limited lifespan and can be very messy to apply particularly in inclement site conditions using an extra-wide strip of damp-proof membrane for the upper service protection and lapping that up and over the beam ends; this does provide a degree of protection but can trap water beneath the concrete floor structure should there be a flood or any excessive water ingress creating a wrap from the damp-proof membrane and gaffer tape around the ends of the beams but this is far from fully effective takes at least ten minutes per beam and adds to the manual handling risks as beams need to be lifted by more than one person to enable wrapping.
Faced with the challenge of wrapping numerous beams on several residential projects during 2016 Hertfordshire builder Kevin Nutkins had a moment of inspiration when he realised that far more effective protection would be provided by a pre-formed end cap than a wrap. A moulded plastic cap reduces the application time to a few seconds per beam and most importantly significantly reduces the need for manual handling because it can be fitted before the beam is put in position.
Nutkins decided to explore his idea further; over 18 months he refined the design settling on injection-moulded recycled polyethylene as the most appropriate material for the cap. A 3D-printed prototype helped determine the sizing and initial samples were produced. Extensive testing at BRE confirmed that the material surpasses all ISO requirements for damp-protection material as well as its suitability for use as an in-ground building product. The product development continued with the cap now named the K-KAP gaining registered product status with LABC and inclusion in its approved products scheme; the design also has both UK and international patents pending.
The K-KAP is simply slid over the end of the concrete beams providing protection from moisture and damp ingress. Should the beam need to be cut to size the cap can be removed and replaced once cutting is complete. Part of the proprietary design ensures it spans the width of the supporting foundation wall. If used on all beam ends this feature provides protection that fully meets Approved Document C section 4.17 requirements for upper surface and reinforcement protection.
The photo above shows how a cap works: it provides consistent effective protection from any moisture ingress to surface and beam end. The beams should be placed in position with the K-KAPs fitted and laid on the internal foundation walls. The beam-to-beam spacing is determined by the first infill blocks being set at the ends of the beams covering the caps; the remainder of the infill blocks can then be installed.
The end blocks are lifted to allow the infill slips to be set in place on a bed of mortar after which the blocks are set in mortar above them. The floor surface is covered with a mortar slurry that fills any gaps and binds all the floor components before the internal block walls are constructed. The first course of blocks for the internal wall would sit on a standard mortar bed with the top of the proprietary caps being covered by the damp-proof course material.
For construction of floors where a building is being extended the K-KAP can be pre-installed in the cut-out wall pockets ensuring the hidden beam ends are fully protected.
Capping offers a number of advantages over more common methods of moisture protection. It provides full protection is simple to install in all conditions saves time and reduces manual handling risk and it makes building control inspections easier because the complete protection is easily visible to the surveyor.
Gary Little is commercial manager at K-Kaps glittle@k-kaps.com
Related competencies include: Construction technology and environmental services