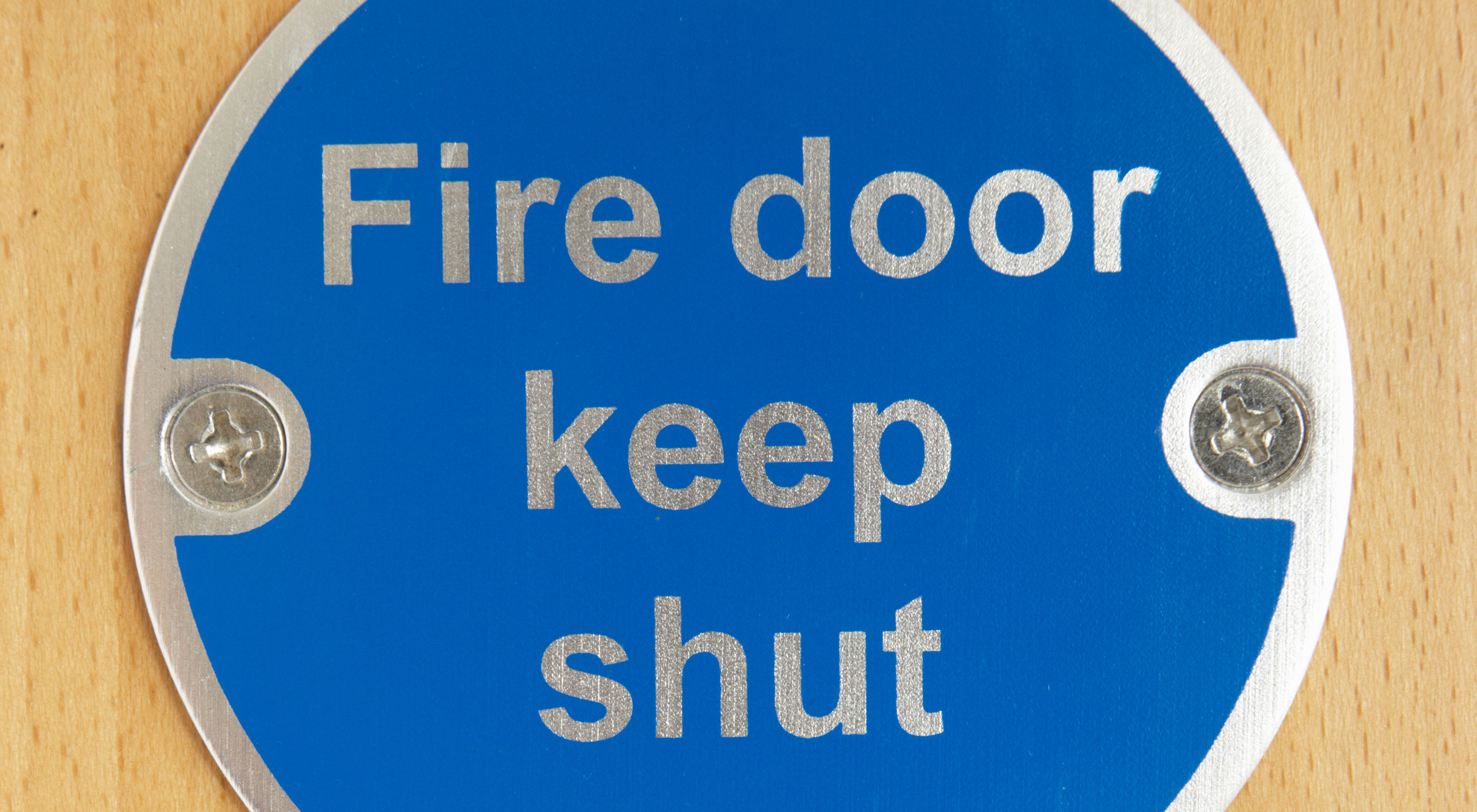
“You rarely find a fully compliant fire door”: these were the words repeatedly shared by a fire risk assessment expert, during a presentation I attended recently. Sadly, it is often the case that we find fire door failures when inspecting a building, even if we have been called in for another reason.
One significant project with Trident Building Consultancy, for instance, involved surveying 7 high-rise residential tower blocks 2 months after the Grenfell Tower tragedy. They were purpose-built 1960s towers and, following an internal and external refurbishment programme in 2015, they featured a similar aluminium composite materials cladding system to Grenfell.
Intrusive survey
In line with other work being done on this project to assess the installation standards of critical fire safety components, an intrusive survey was carried out on a sample of 7 fire doors. From my initial inspection of the doors it was clear that the installation standards were poor as I could clearly see daylight between the door and frame and at the threshold. I carried out further intrusive investigations by removing architraves to check and see if door frames had been installed correctly, following removal I could see that the back of the door frame was packed with pink foam, which does not provide any sort of fire barrier. The door frame installations were not compliant with the manufacturer’s test data and, as a result, would not provide the level of fire resistance required to comply with the building’s fire strategy.
Fire compartmentation survey
Following my initial investigations, I organised a 2-week fire compartmentation inspection survey programme across the blocks, managing a team of 10 chartered surveyors to complete this work. The survey included a detailed review of product data sheets, manufacturer’s test data, installation records and an inspection of all fire stopping and fire door installations. We put together a report for each block advising the building owner of all the necessary remedial works needed to make the tower blocks safe. This included the replacement of doors, door frames and ironmongery and the installation or replacement of proprietary fire stopping products.
The fire doors were the worst failings: despite being an essential part of fire compartmentation, they did not meet the installation standards as set out in the manufacturer’s BS476:22 fire test data. The doors that were installed were a fire risk themselves. It was advised that they were replaced with certified fire door sets, installed by operatives who are members of a third-party certification scheme for fire door installations.
Since this project, I have seen many more buildings needing full replacement of fire doors, the most recent being 2 high-rise blocks in West Yorkshire. As a result of our inspection, more than 100 doors were replaced, and a full programme of third-party approved fire-stopping has been carried out.
Lack of understanding
There seems to be a lack of understanding about the importance of fire doors, particularly on the part of building owners, so this fundamental part of compartmentation falls by the wayside. Consequently, there is often a failure to keep maintenance records, missing or incorrect signage, locked fire doors and fanlight windows above them being replaced with plywood, which doesn’t offer the necessary fire resistance.
- missing or painted-over intumescent cold smoke seals, which compromise fire and smoke resistance
- integrated ventilation grilles without any fire resistance
- excessive gaps between the door, frame and threshold
- additional untested ironmongery installations
- door closers not performing as intended
“There seems to be a lack of understanding about the importance of fire doors, particularly on the part of building owners”
Clerk of works
It is not all doom and gloom, though. On a recent project for a new care home, it was refreshing to see how having a clerk of works present improved fire door installations. The carpenters were fitting the doors extremely tight into the frame to allow for the timber shrinkage that occurs when the building heats up and the plaster finishes dry out. Once the moisture levels had stabilised, final adjustments were made to the doors, which ensured that gaps between the door, frame and threshold did not shrink and then exceed the maximum acceptable standard of 4mm stated in the manufacturer’s fire test data. I have never seen this method being used before, but it prevented anyone having to go back and rectify the doors following installation.
In addition to having a clerk of works on new-build projects, I support the incoming compulsory competency register for fire door installers, in line with the recommendations in the Industry Response Group report Raising the bar. I also recommend that only complete fire door sets are specified, having been tested by a third-party certification scheme such as BWF-CERTIFIRE, to provide full traceability.
In recent months, COVID-19 has affected almost everything, including fire doors. Many buildings have been left empty for prolonged periods of time without adequate levels of heating, and this subsequently increases moisture content within the air which can cause timber fire doors to swell. Prior to reoccupation of these buildings, building owners should carry out checks to ensure doors are closing into the frames and operating as intended.
It is our collective responsibility to create safer buildings, and I strive for the day where compliant fire doors are the norm. There is a lot to do to persuade everyone in the industry to reach for the same standards.
Gary Strong, RICS’ global building standards director, comments: “Regular inspections of fire doors in existing properties, according to their risk profile, are essential. If there are any doubts about the doors or integrity around the frames, these should be checked.”