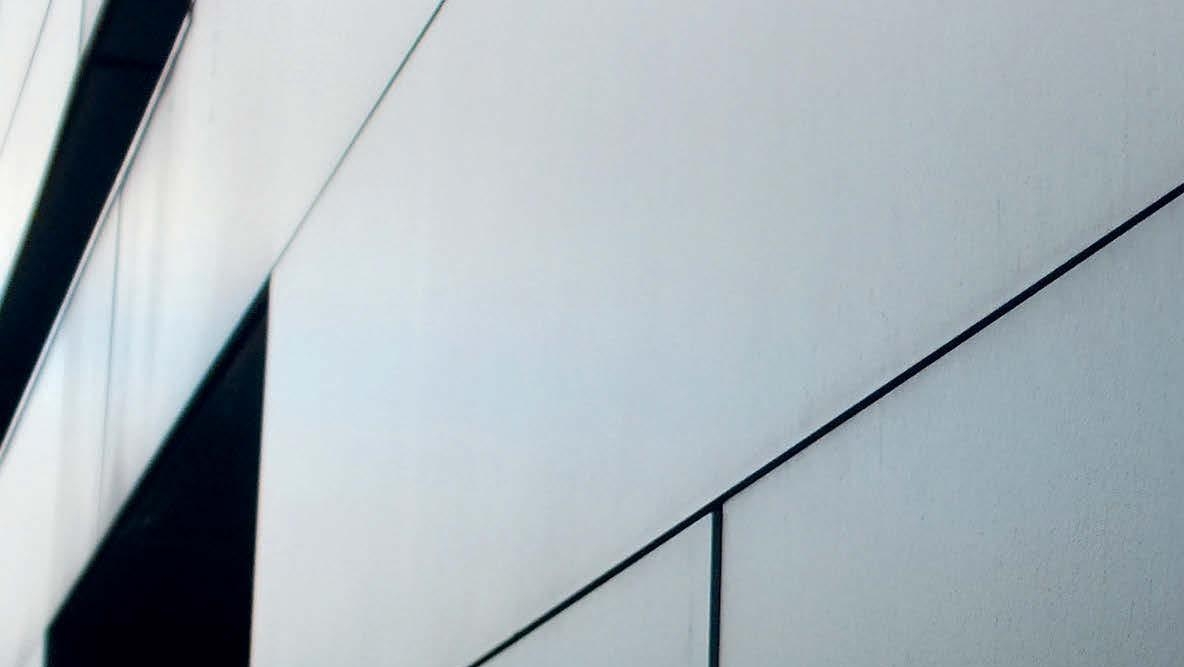
It is not surprising that queries about cladding have, in recent years, consistently topped the list of technical concerns on commercial property transactions. In addition to their fire and life safety implications, these issues have the potential to frustrate deals and affect asset liquidity.
Building surveying has always been an incredibly broad and challenging profession. The job requires us to connect our knowledge of design and construction technology with contract practice and risk management; to interpret a building's history and project it into the future; to understand costs; and to communicate with specialists and appreciate the views of multiple stakeholders.
By using all these skills, surveyors should be able to offer clients concise advice with some commercial insight. Yet cladding and fire safety might represent the biggest technical challenge the profession has faced since the dangers of asbestos became publicised, and suitably skilled and experienced building surveyors can play a crucial role in managing investigations and overseeing remedial works.
This article therefore discusses the current regulatory framework, the kinds of cladding system that consistently cause concern, the processes that may be adopted to investigate them, and the commercial implications.
Part B and Approved Document B
The functional fire safety requirements are defined in Part B of the Building Regulations, with B4 stating: 'The external walls of the building shall adequately resist the spread of fire over the walls'.
The most widely used method of demonstrating compliance with Part B is to follow the government recommendations in Approved Document B. However, doing so is not mandatory and alternative fire engineering approaches may achieve an adequate level of fire safety.
Before December 2018, the Building Regulations did not rule out the use of combustible materials in the external walls of high-rise buildings where upper floors exceed 18m in height. In such circumstances, Approved Document B allowed for the submission of evidence that the entire external cladding system had been classified to BR 135 Fire Performance of External Thermal Insulation for Walls of Multistorey Buildings, using data from full-scale fire tests that had been conducted in line with BS 8414.
Where combustible materials are identified in existing high-rise cladding systems, an audit trail incorporating a BR 135 assessment – together with evidence that the system was installed correctly, as designed – may provide assurance that the design did align with Approved Document B at the time it was installed.
However, BR 135 assessments do not offer blanket approval for a material or system type. It is not unusual for such assessments to be entirely missing, or for the reports to be based on a generic arrangement of materials that bear little resemblance to those found on site.
Although a Building Regulations final certificate should arguably provide the necessary assurance that Part B and other relevant criteria have been satisfied, these certificates are invariably caveated such that they do not provide absolute evidence of regulatory compliance. Building Regulation 38 states that fire safety information must be provided at project completion or before occupation, so information to support the final certificate should be sought.
It is important to remember that the principle objective of Part B and Approved Document B alike is the preservation of human life. While life safety should be a given for any property, asset protection is not; therefore, the Building Regulations and guidance should be viewed as minimum standards rather than an assurance that a fire will not start or spread.
A fire at online grocer Ocado's automated distribution centre in Andover in February this year prevented it from fulfilling up to 65,000 orders a week. This serves as a reminder that fire can have a huge impact on business continuity, reputation and, in this instance, share price. It is prudent to consider these implications, and specialist fire engineering can add value when it comes to enhancing existing assets and designing new developments.
In December 2018, Building Regulation 7 was expanded in England to restrict the use of combustible materials that fall short of the Euroclass A2-s1 d0 standard in the external walls of buildings with any storey 18m above ground level that contains a dwelling, institution or room for residential purposes. Although this has been widely referred to as a ban, other properties such as commercial premises, hotels, hostels and boarding houses do not fall under its scope, and combustible materials may still be justifiable in such buildings whether they are above or below 18m in height.
'Cladding and fire safety might represent the biggest technical challenge the profession has faced since the dangers of asbestos became publicised'
Under the Building (Scotland) Amendment Regulations 2019, which came into force on 1 October, the situation is similar albeit more robust. The changes apply to both domestic and non-domestic properties and stipulate a ban on combustible materials in wall cladding where buildings have a storey height of more than 11m; that is, 7m lower than in England.
Regardless of whether there is a robust audit trail to demonstrate regulatory compliance at the time of construction, the English and Scottish situations force a commercial comparison between buildings with combustible cladding materials and those without. Where combustible materials are present, especially on high-rise residential assets, there could be a potential risk to asset liquidity and reputation.
The UK government has published numerous advice notes on the building safety website that bring together test results and extensive industry insight on existing assets, covering everything from remediation of metal composite and aluminium composite material (ACM), urgent life safety interventions known as interim measures, combustible insulation and smoke ventilation.
Surveyors need to be aware of this information and keep abreast of any changes. They would also be well advised to act on such information, taking specialist advice as necessary, particularly as the Health and Safety Executive would refer to such guidance in the event of an issue. Although most of the advice notes are intended for owners of residential buildings of 18m or more in height, some are caveated such that the principles may also apply to other use classes and buildings below 18m. Where risks might be present, specialist fire engineering input should be obtained.
Component complexity
Developments in material technology, changing design tastes, cost factors and specialisation of production have resulted in a situation where external walls are made up of many different components, manufactured and installed by multiple different parties.
This means that it can be difficult to find or rely on appropriate documentation, and a superficial visual inspection might result in misleading conclusions. Facades must then be primarily considered a system rather than a collection of unrelated components.
A modern non-load-bearing facade system has three main sections: the external cladding, thermal insulation and the backing wall. All three parts may promote fire spread, and even combinations that have been demonstrated in tests to be safe might be problematic depending on the kind of materials used and their extent, arrangement and installation.
Modern construction products are highly dependent on organic materials derived from oil. Although materials such as plastics and foams can be modified with fire-retardant additives – sometimes referred to as FR grades – that reduce the rate of ignition or flammability, this terminology can be misleading since all organic materials are ultimately combustible and fall short of Euroclass A2-s1 d0.
The potential issues with rainscreens clad in materials such as combustible ACM panels, for instance, include a propensity for rapid external fire spread, which can be accelerated by a ventilated cavity acting as a chimney, and fire compartments that cross over one another.
ACM can be visually identified at the cut edge by a plastic core sandwiched between two wafer-thin skins of metal. Although such identification is tricky with folded- or tray-profile panels, ACM usually produces a sharp mitred edge in contrast to the shallower radius of a folded, solid-metal panel. Of course, testing is the only way to determine categorically the type of core or filler material.
High-pressure laminates (HPLs) meanwhile combine compressed wood and resin, and their use on high-rise residential buildings is cause for concern given their combustibility and potential for external fire spread. HPL is one of many materials that is no longer acceptable on new buildings that fall under the scope of Building Regulation 7.
For existing buildings, government advice is that low-grade HPL panels of Euroclass C or D, used with combustible insulation on residential buildings more than 18m high, represent a notable fire hazard. However, it is acknowledged that fire-retardant, though ultimately still combustible, HPL panels used with stone or mineral wool insulation may be acceptable, if supported by a relevant BR 135 assessment.
External wall insulation (EWI) systems, while often faced with non-combustible materials such as brick slips, can conceal combustible insulation that may not be picked up from visual inspection alone. The other potential issue identified by the government is that EWI systems may, in some situations, be at increased risk of deterioration, resulting in materials debonding or falling.
EWI systems should be reviewed to ensure that they are in sound condition, have been adequately designed to account for both wind loads and the weight of the structure, and installed properly. The risk of falling material could be compounded in situations where the surface is already damaged and the action of trapped moisture or frost may accelerate its deterioration.
Due to their relative thinness and excellent thermal efficiency, it is unsurprising that plastic-based thermoset insulation such as polyisocyanurate (PIR) and phenolic foam had become the default choice for modern cladding systems. These materials are incredibly widely used, often acceptably so, but the audit trail for buildings above 18m must be considered.
Although PIR and phenolic foams typically form a protective char layer when exposed to flames, it must be remembered that all forms of foam insulation are ultimately combustible and are no longer acceptable on residential buildings within the scope of Building Regulation 7.
Foam insulation is also found in structurally insulated panels (SIPs), and an audit trail should be sought for these. SIPs and built-up backing walls may incorporate sheathing layers such as plywood, oriented strand board and cement particle boards, which are combustible and need to be factored in to the assessment of fire risk.
Concealed fires
Cavities are common in external walls to enable drainage and ventilation, and to limit the internal passage of moisture. However, extensive cavities have the potential to spread smoke and flames from one compartment to another, and a cavity acting in effect as a chimney can accelerate this spread. Fire may enter an external wall cavity from the interior or exterior of a building; for example, if it breaks out through window openings or penetrations such as extract ducts or electrical sockets in the internal leaf of the external wall.
Part B3.4 of 2010 states that: 'The building shall be designed and constructed so that the unseen spread of fire and smoke within concealed spaces in its structure and fabric is inhibited.' Approved Document B in turn makes recommendations as to the location of cavity barriers, and this includes around openings such as windows, and at the junction between every wall and floor in a fire-resisting compartment.
- Open-state cavity barriers: these incorporate an intumescent layer that maintains ventilation paths when cold but expands to close the cavity when activated by the heat of a fire.
- Full-fill cavity barriers: these completely close the cavity and are used in situations where ventilation or drainage paths need not be maintained, such as at vertical compartment wall junctions.
Installation and fixing details are crucial, and it is not uncommon to find cavity barriers missing or inadequately secured and therefore at risk of becoming displaced and failing to perform as intended. Cavity barriers are relatively simple to install and most manufacturers supply them with mechanical fixings, but it can be very difficult to remediate poorly fitted or unsuitable barriers.
The whole or partial removal of cladding panels may be necessary to gain access to the barriers, and remediation in handset brickwork or an EWI cladding system can be far more disruptive and costly once access and preliminaries are considered.
Intrusive investigation
Initial information about cladding systems may be gathered during more general surveys, for example from operation and maintenance manuals as part of the technical due diligence process. But the limitations of visual surveys and the risks of overreliance on potentially inaccurate documentation are still important to bear in mind.
In many cases, intrusive surveys will be necessary to establish the composition of the cladding system, and the quality and completeness of the installation. A typical study would include specialist advice from a facade cladding engineer with a contractor in attendance as well, and there would also be input from a testing laboratory and assessment by a fire engineer.
Samples from multiple points in the system are normally needed to obtain a comprehensive picture of the way it works, but access restrictions, possible road closures and disruption to occupants all need to be considered. Although experienced building surveyors are well placed to coordinate this process, it remains as important as ever to ensure that the scope of service is achievable and does not extend into the disciplines of facade engineering or fire engineering.
Professional indemnity insurance (PII) providers are carefully considering policy coverage to limit their exposure to cladding and fire safety claims, and some form of restriction, exclusion or aggregate cap is increasingly becoming standard (see Built Environment Journal September/October, p.18). The upshot is that direct appointments of specialists by clients remains preferable, rather than appointment as sub-consultants. Limitations on the scope and liability of specialist input must be duly assessed to ensure that the reporting output is sufficient and PII cover is adequate.
'All forms of foam insulation are ultimately combustible and are no longer acceptable on residential buildings under the scope of Building Regulation 7'
We can expect cladding safety concerns to continue to evolve, likewise government advice and insurance requirements. For existing assets the situation is complicated, but government advice notes should be considered, with specialist input and an audit trail sought to show that cladding systems complied with the regulations that applied at the time of construction. Evidence that systems were constructed properly and in line with the original design should also be identified.
Suitably trained and experienced surveyors can contribute positively by managing the process, coordinating investigations and, managing the remedial works. There are substantial risks and pitfalls to bear in mind, but involvement with specialist investigations and complicated repair works play to a building surveyor's core skills.
Simon Young is an associate at Tuffin Ferraby Taylor syoung@tftconsultants.com
Related competencies include: Construction technology and environmental services, Fire safety Inspection