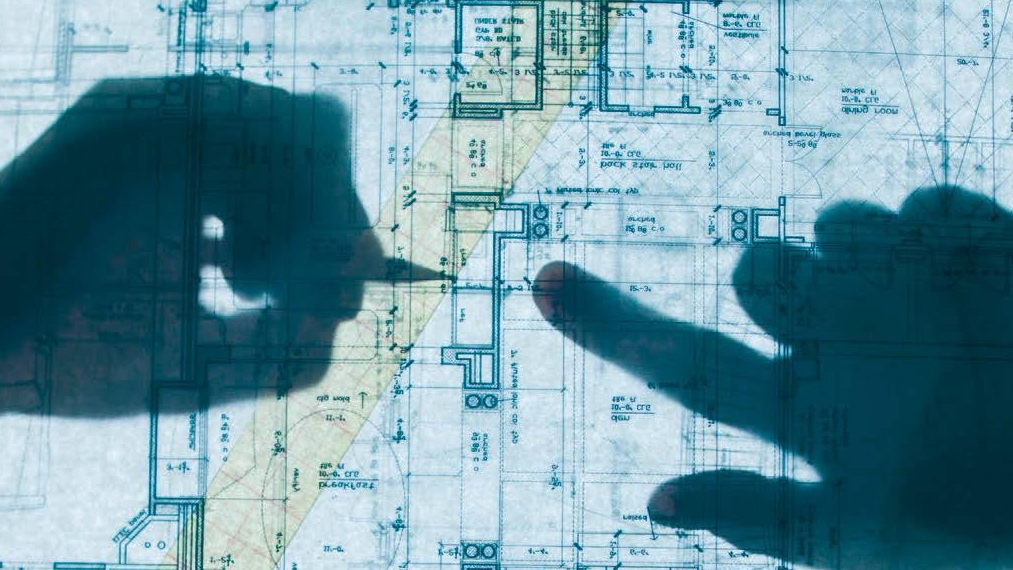
With the difficulty of procuring traditional skills, the promise of increased productivity and, to some degree, because everyone else seems to be doing so, more housebuilders are now exploring modern methods of construction (MMC).
Many builders and manufacturers cite the potential for improved quality as their underlying motivation. This is reflected in the NHBC Foundation report Modern methods of construction: Whos doing what?, which lists increased quality as the primary reason. The logic is that off-site manufacture or simpler technologies can reduce the number of defects, as well as supporting faster build times, greater efficiency, lower costs for rework or claims, and improved quality in the finished home.
At NHBC, we have seen growing interest in all MMC systems, from site-based methods to whole-house volumetric products and panelised systems. We carry out a review of each system to determine whether it can be accepted as part of the construction of a home.
"The three areas we focus on when reviewing MMC are design, manufacture and constrution - but design underpins everything"
Our appraisal of different systems does not consider the commercial benefits proposed by MMC manufacturers; instead, it asks only whether they can comply with the NHBC standards. In essence, whichever way homes are built, they should be long-lasting and meet the reasonable expectations of homeowners.
Manufacturers from around the world submit systems for review, and given the myriad that NHBC has seen, we have gained unique insights — into what works, and into the common issues that mean a product fails to meet an acceptable quality.
Principal areas of risk
The three areas we focus on when reviewing MMC are design, manufacture and construction. While the method of manufacture and construction are important, many of the key risks with MMC are mitigated in the design; without a complete and viable design the method of manufacture, quality procedures, tolerances, construction method and interfaces with site conditions cannot be determined. Design underpins everything.
The more common pitfalls are as follows.
-
Incomplete design:
The rigour required to complete the detailed design of an MMC system is often overlooked. The drawings and specification of all components go beyond what is required in conventional construction, principally because manufacture is often carried out by unskilled operatives. Take the example of a mastic joint; good practice in one MMC manufacturer's specification sets out the colour, location, length, width and allowable tolerance as well as the temperature at which it can be installed and how frequently it is inspected. The detail and accompanying procedures for all elements should not be underestimated.
-
Clearly defined scope:
No single MMC system is suitable for all sites, building shapes or planning requirements though these restrictions are often not defined by the manufacturer. However, the best designs seem to come from a simple, core product to which further features may be added. When MMC systems have a clearly defined scope, the limits of applicability and permitted environmental conditions can be fully specified. This then allows any variations to be fully designed and detailed.
-
Durability:
Basic principles are being ignored in many MMC designs, particularly with respect to water ingress. The leaky condominium crisis in British Columbia, Canada between 1985 and 2000, when 50,000 homes were affected by damp, is an important history lesson in this respect. Similar problems have been reported in other countries including the USA, Sweden and New Zealand leading to the development of the so-called four Ds of moisture management: deflect moisture away, using overhangs and flashings; drain moisture when it gets past the cladding; dry the structure by providing ventilation; and choose durable materials that do not degrade when wet.
-
Sequence of assembly:
Most MMC systems involve assembly of elements off site to form a panel or volumetric unit. The design of the joint between modules is complex because it needs to transfer structural load as well as retaining the integrity of fire protection, moisture and air barriers. Good practice will allow for lapping of these critical membranes, visible inspection of the integrity of joints and consideration of how these connections are formed on site.
-
Specification of products:
All materials used in construction should be fit for their intended purpose and certified as such. This means that, for many MMC systems, product specification and procurement needs to be completed well in advance of manufacture, and often before work starts on site. Good-quality MMC system manufacturers understand this, and their design process and programmes recognise the detail required to generate complete product specifications at an early stage.
-
Spread of flame:
Volumetric MMC systems - that is, 3D modules delivered to a site - introduce voids between the walls of modules and intermediate floors. Factory-fitted fire barriers are then often hidden from view so the inspection of this safety-critical element needs to be considered at design stage. Another common issue concerns the subfloor void. Some volumetric modules sit on foundations supported only at the corners, creating a void in the subfloor beneath the party wall. Where a compartment wall sits above these foundations, designers should consider how the void is subdivided on the party wall line.
-
Setting out and site works:
The risks associated with installing MMC on site are well documented. While it is often appreciated that the tolerances in groundworks or podium construction need to be tighter to accept highly engineered, factory-assembled modules, MMC designers also need to understand the realities of site conditions and to build in greater tolerance, to allow their systems to be effectively and efficiently assembled. Commonly, designers will address the interface between the MMC systems and foundations but will not pay sufficient attention to incoming services - how the drains, water, electricity and telecommunications are to be connected.
To conclude there is no short cut when bringing MMC systems to market, and investment in research and development is certainly critical. It is no coincidence that the most successful MMC systems have a fully developed design well before manufacture begins. Early investment in design will help to provide high-quality homes that meet the needs of those who live in them.
Related competencies include: Construction technology and environmental services Design and specification Inspection