In the social sciences unintended consequences are grouped into three basic types. The first two are unexpected benefits and unexpected drawbacks, while the third is perverse results – where the effect is contrary to what was originally intended.
Several new or substantially revised Building Regulations and Approved Documents issued in the past few years could well fall into these categories. When considered on their own merits, they have sought to address specific problems; however, in the detail of their implementation, there have been a number of consequences that may not have been apparent at the time of drafting or publication.
These may have an impact on the design or appearance of the building, or require materials that are not available, or even give rise to conflicts with other parts of the Approved Documents.
Grenfell Tower prompts regulatory revisions
There have been some very good reasons for the changes. For example, following the horrific fire at Grenfell Tower in 2017, Approved Document B – which sets out the requirements for fire safety in buildings – was significantly restructured and revised in 2019.
It has continued to be reviewed and updated since, however, as the investigations and causes of the fire continue to unfold, with further updates in 2020 and 2022.
One of the principal concerns that came out of the Grenfell Tower tragedy was how future fires could be contained to prevent them spreading across the external face of buildings.
While the second phase of the inquiry has yet to issue the final report, the inquiry also identified multiple failures of life safety systems and other factors – albeit that the cladding and the rate of fire spread was the most visible and enduring image.
At the time of the fire, the Building Regulations Part B, Requirement B4 already required that 'the external walls of the building shall adequately resist the spread of fire over the walls and from one building to another, having regard to the height, use and position of the building.'
As with other parts of the Building Regulations, how this was to be achieved was not specifically mandated in the regulations themselves, and guidance in Approved Document B stated that the facing material of the external wall and insulation above 18m should be non-combustible.
However, the UK government thought this was not sufficiently clear or robust enough to prevent further tragedies from occurring.
Therefore, a change was made to the actual mandatory requirements of the Building Regulations rather than just to Approved Document B, as would normally be the case, although this too was amended.
Building Regulation 7(2) was introduced to require that the whole wall build-up be non-combustible, with certain exemptions set out in regulation 7(3). This solely applied to 'relevant buildings', which were essentially defined as residential buildings with an occupied floor 18m or more above ground level.
If this requirement had only appeared in the approved document, it would have represented one way of complying, and other ways would have been permissible. However, as it was incorporated into the Building Regulations themselves, it is an absolute requirement.
Therefore, there is no alternative but to use materials that are non-combustible in the external wall build-up, apart from the exemptions under regulation 7(3).
Requirements pose problems for minor components
Regulation 7(2) uses the European Classification A2-s1, d0 or A1, which is based on materials' reaction to fire, to define non-combustible. To achieve this classification, products need to be tested to BS EN 13501-1: 2018.
When the requirement was introduced, some products – mainly major components such as cladding systems or plasterboard – had been tested to this standard, but many had not.
Yet what caused the construction industry the biggest headaches were the minor components that are necessary to construct a functioning external wall but were inadvertently missed from the list of exemptions in regulation 7(3).
For instance, cavity trays were not included in the exemptions unless they were in a traditional brick-and-block cavity wall. Not many buildings of more than 18m use this typology, so therefore most trays would need to be classified as A2-s1, d0 or A1.
Unfortunately, there were at the time no such products on the market tested to BS EN 13501-1. To prevent the construction industry grinding to a halt while suitable trays were developed, tested and manufactured at scale, alternative solutions had to be developed quickly.
Workaround raises issues in turn
Luckily, Approved Document B's Appendix B: Performance of materials, products and structures states that 'Materials covered by the Classification Without Further Testing (CWFT) process can be found by accessing the European Commission's website'.
A European Commission decision notice 96/603/EC of 1996 listed materials deemed to be class A – that is, non-combustible – without further testing. This includes aluminium, lead and zinc, and so contractors began to purchase these materials with the intention of using them for cavity trays.
However, these materials are difficult to work with, being quite sharp when cut and not very malleable, particularly when forming complex corners.
They also needed to be sealed at junctions to maintain watertightness, as required by Approved Document C, and created significant thermal bridging issues through the insulation. Warranty providers were not convinced by this approach.
When it became clear there was a problem, the UK government issued a specific relaxation from regulation 7(2) for cavity trays in June 2022, in the form of a direction under the Building Act 1984.
This gave a temporary dispensation of 18 months to those who wanted to use combustible cavity trays. Despite this, contractors still seem wary of using combustible trays as the long-term uncertainty is thought too much of a risk.
'Contractors still seem wary of using combustible trays, as the long-term uncertainty is thought too much of a risk'
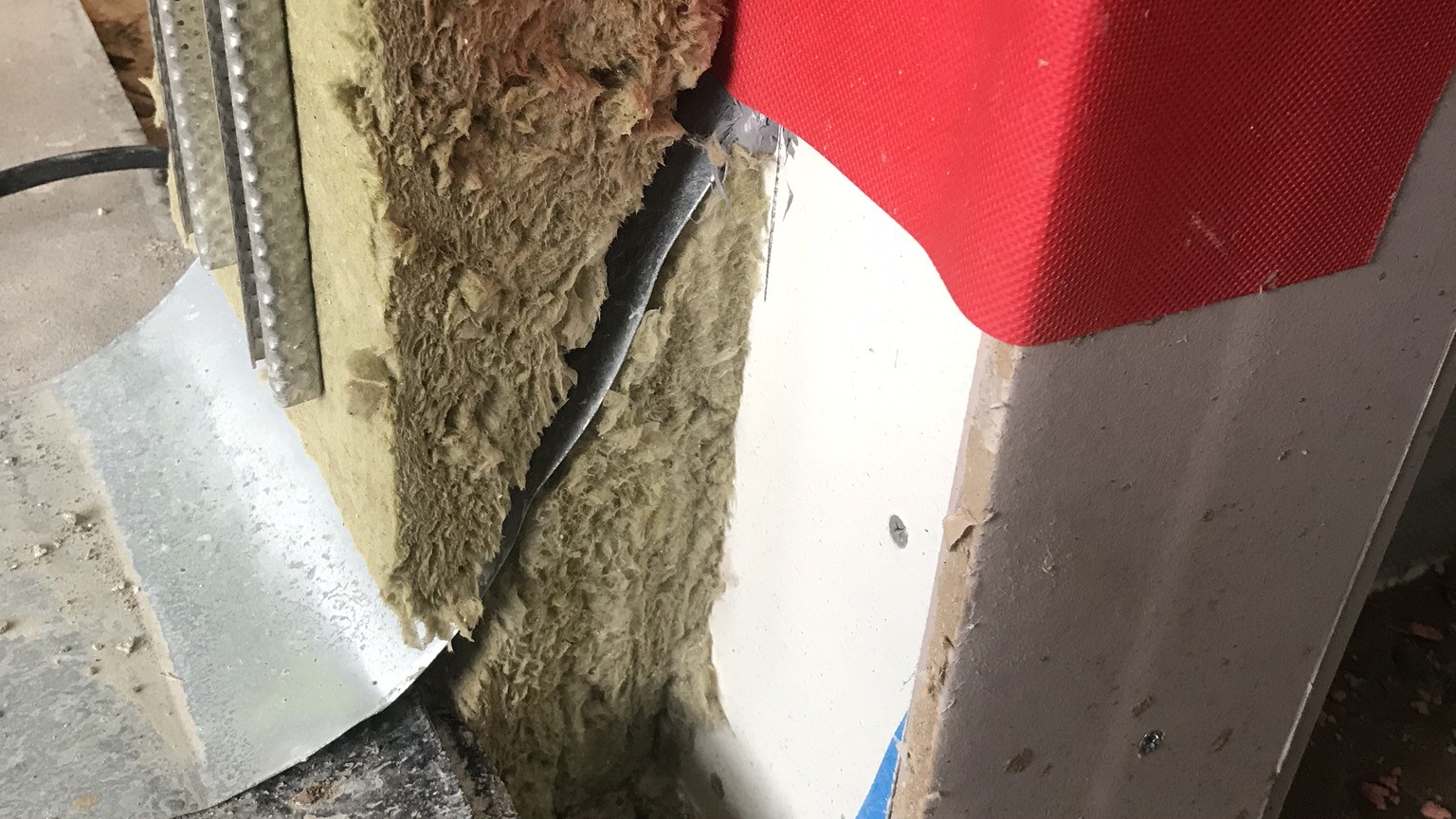
A typical cavity tray installation © Levitt Bernstein
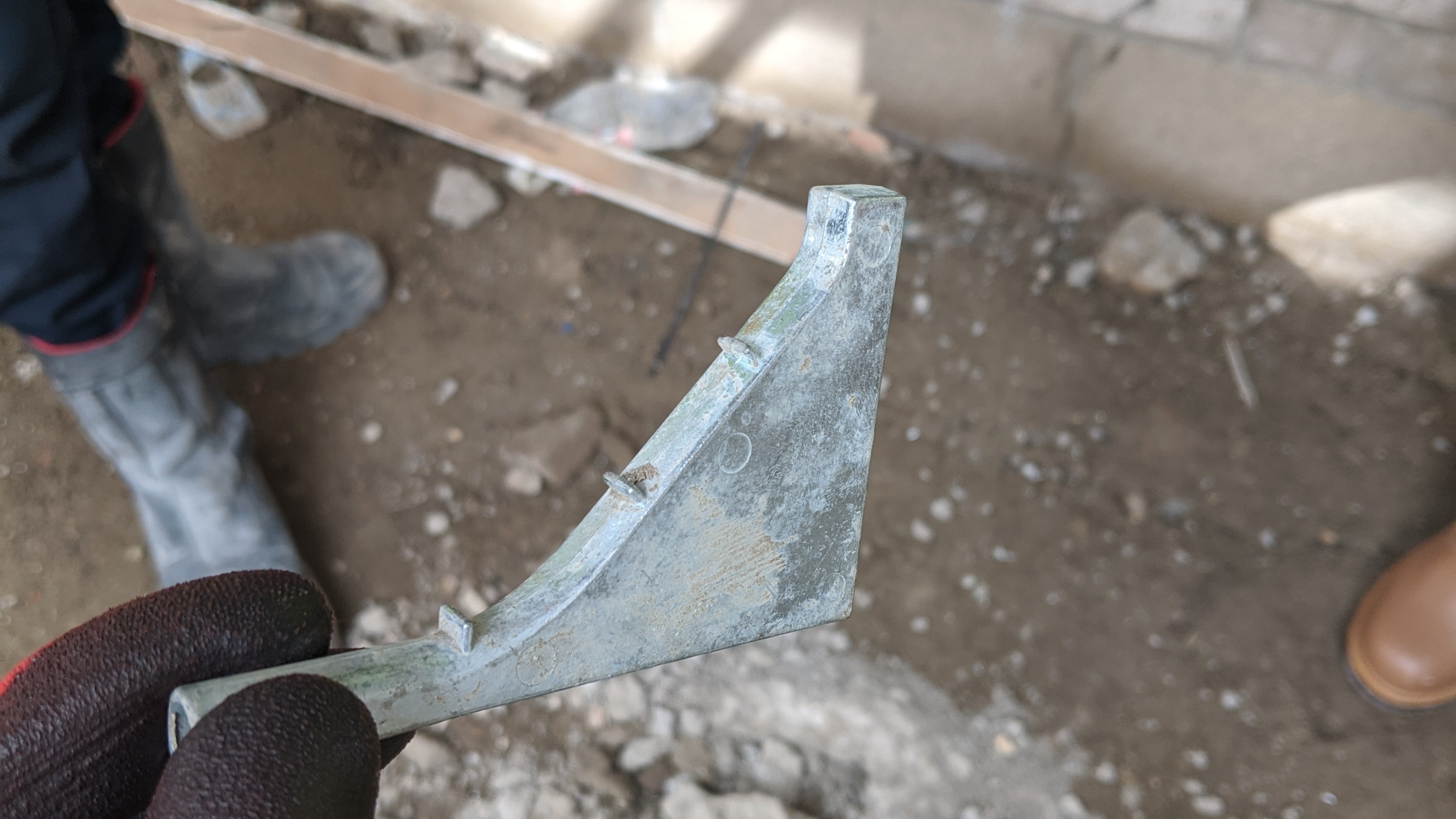
Cast-metal weepholes are replacing plastic ones – at a cost © Levitt Bernstein
Thermal bridging remains to be resolved
While a handful of manufacturers have brought class-A cavity trays to market that are suitably tested, certified and approved by warranty providers, these mostly still cause thermal bridging issues.
This is of particular concern when trying to meet the requirements of Approved Document L on the conservation of fuel and power, because the bridging caused by small elements has a disproportionate effect on the building performance when high levels of insulation are used.
Cavity weep vents were also not included in the exemptions listed in regulation 7(3).
This may have been because no products were available to be tested to BS EN 13501-1. As vents are small components that are essentially surrounded by bricks, which are non-combustible, the chances of fire being propagated across the external face of a building from weephole to weephole appear to be negligible.
Nevertheless, as regulation 7(2) is an absolute requirement, non-combustible weepholes are now required in relevant buildings.
Again, it took a little while, but a couple of products are now available. Yet there is a problem of cost and the associated fire risk as combustible weepholes cost a few pence, whereas non-combustible ones cost a few pounds.
Regulation fails to appreciate building complexity
These examples illustrate how today's buildings are assemblies of complex, high-performing components. Even the simplest need to meet various stringent requirements.
It is increasingly hard to source products that meet all the performance requirements, are certified and approved by third parties and are affordable. The unintended consequences of the regulation do not make this any easier.
In the next article, I will look at further unintended consequences of changes to Approved Document B, with a focus on building materials and balconies.
Tony Hall is a technical design director at Levitt Bernstein
Contact Tony: Email
Related competencies include: Fire safety, Legal/regulatory compliance