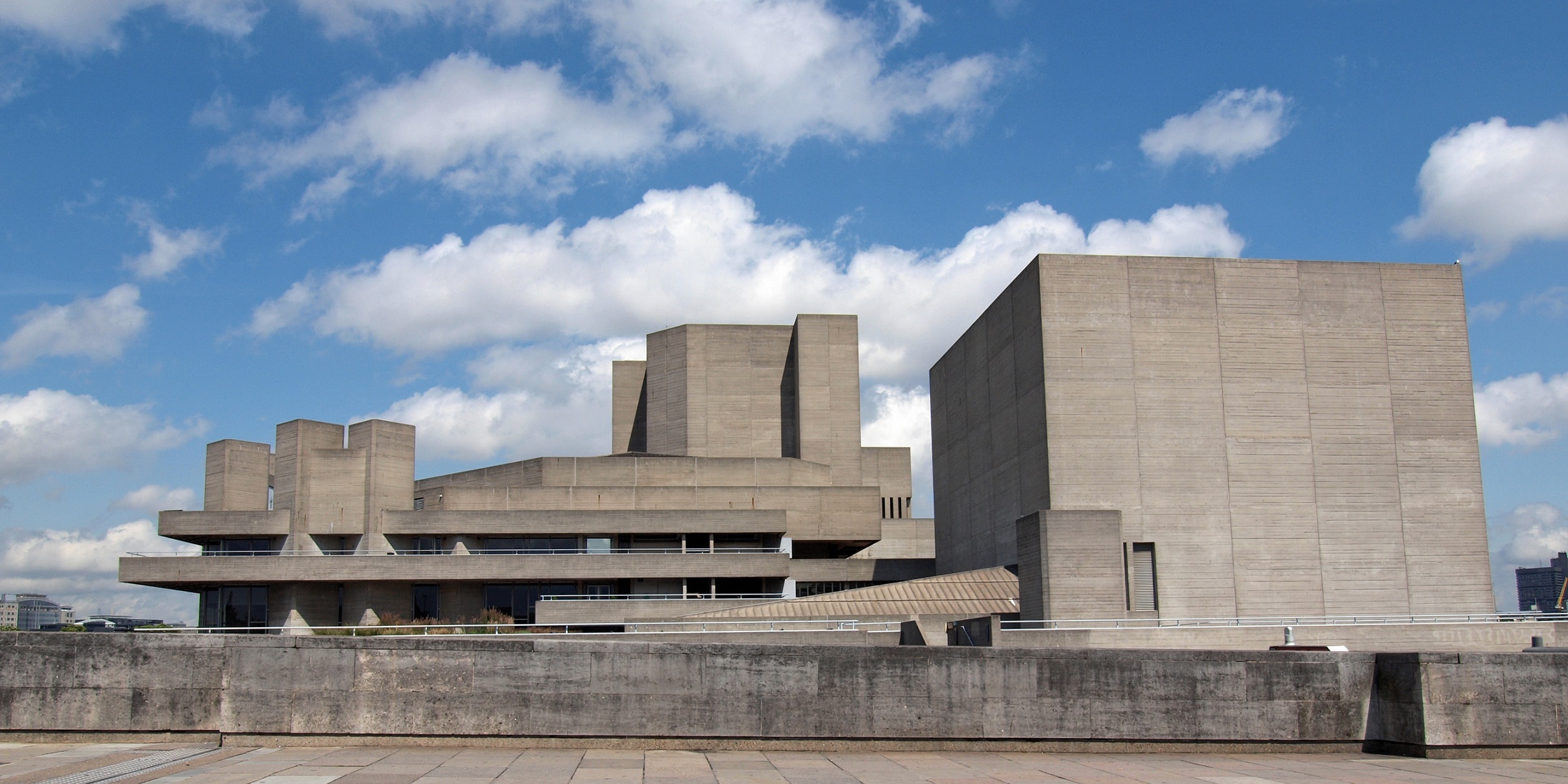
The Royal National Theatre in London, commonly known as the National Theatre, an iconic example of brutalist architecture. The building is Grade 2 listed and has undergone various repairs over the years
The development of Portland cement and concrete in the 19th and 20th centuries revolutionised the construction industry, and resulted in a wealth of concrete architecture. However, the materials used and the way they deteriorate were not well understood, leading to the use of unsuitable constituents and designs that were not adequately durable.
Reinforced concrete structures are particularly at risk, as it was wrongly assumed by many engineers and architects that encasing the reinforcement in concrete would protect it in perpetuity. As a result, an ever-growing number of historically significant concrete structures require ongoing conservation and repair.
Material deterioration
We now know that concrete is susceptible to deterioration from several different mechanisms, which can be divided into three broad categories.
-
Chemical mechanisms:
these include carbonation, chloride contamination, alkali-aggregate reaction and sulphate attack.
-
Physical mechanisms:
these include environmental effects such as freeze–thaw cycles, weathering and salt crystallisation, but physical deterioration can also result from structural loading, abrasion, impact damage, shrinkage and expansion.
-
Biological mechanisms:
these include the propagation of invasive plants and micro-organisms on the concrete surface.
The most serious forms of deterioration are those that ultimately lead to the corrosion of the steel reinforcement. The reinforcement not only supplies crucial tensile strength that diminishes with corrosion, but as it corrodes also forms highly expansive products, which can cause the surrounding concrete to crack and, eventually, break off.
While steel can corrode due to moisture ingress through obvious defects and cracks in the concrete surface, this can also occur as a result of mechanisms that cause no damage and leave no visible signs on the surface until the corrosion is already advanced. For example, while carbonation of concrete is not in itself generally problematic, the reaction of alkaline hydroxides with carbonic acid formed from atmospheric moisture and carbon dioxide reduces the pH of the concrete, which in turn causes the breakdown of the passivating oxide layer on steel reinforcement that prevents corrosion. As carbonation is a time-dependent process, historic structures are particularly at risk.
Localised breakdown of this protective oxide layer can also occur as a result of reaction with chloride ions that are present in the concrete. Chloride-induced corrosion usually happens when there is ingress of substances such as de-icing salts or sea air from external sources, but some structures may suffer from internal contamination. The latter is more common in historic buildings than in modern ones, as calcium chloride was used in concrete admixtures before 1976, when there were no controls to prevent the use of contaminated aggregate and mix water.
Both carbonation and chloride-induced corrosion are also particularly common in historic structures because the engineers who worked on them did not comprehend the need for sufficient concrete cover depth to protect the steel. Furthermore, the link between concrete’s permeability and its water-to-cement ratio and curing conditions, among other factors, were not understood. The durability of these structures suffers as a result.
“The most serious forms of deterioration are those that ultimately lead to the corrosion of the steel reinforcement”
Protection and restoration
It is possible to reverse some of the effects of the carbonation and chloride ingress using electrochemical treatments. Following carbonation, the alkalinity of the concrete can be restored by passing an electrical current from an external anode through it to the reinforcement and applying an alkaline electrolyte to the surface of the concrete itself. The electrolyte is drawn through the concrete by the current, restoring the alkalinity of the concrete as it does so by saturating the pores with an alkaline solution, while electrolysis at the reinforcement surface simultaneously produces a high pH around the steel. Chloride extraction can be achieved in a similar way, as chloride ions are drawn out of the concrete towards the anode while the re-alkalisation occurs.
Electrochemical systems can also be used proactively to protect steel reinforcement. Cathodic protection, which has been used in reinforced concrete structures since the 1970s, has become increasingly common to reduce the rate and extent of corrosion. There are two types of cathodic protection.
-
Impressed current cathodic protection (ICCP):
this active system conducts direct current to the steel via fixed anodes and an external power supply.
-
Galvanic protection:
this is in contrast a passive system that conducts a direct current from a sacrificial anode made of metal with a lower potential than that of the reinforcement.
While electrochemical treatments and protection can be used to extend the life of reinforced concrete structures, they can be expensive and require specialised expertise to implement. As they need a current to be passed through the reinforcement they are also invasive, while ICCP systems require monitoring and control terminals to be installed as well.
In areas where spalling has occurred the concrete has to be repaired, and such repairs can take two forms. Patch repairs, which can be hand-applied, poured or sprayed, are the most common form, but where larger volumes are required or there is significant corrosion of the reinforcing steel it may be necessary to replace entire elements. Achieving a successful patch repair can be challenging – particularly for historic buildings, which can be much more complex to repair than contemporary structures.
There are conflicting perspectives on the way patch repairs on historic structures should be approached. One argument is that the performance of the repair and its long-term protection of the steel below is the priority; another is that historical authenticity of the material is important and repairs should be a like-for-like replacement in order to look and perform like the original. Both of these approaches have their limits.
Contemporary performance-based repair mortars are usually pre-batched proprietary products that may contain modified cement designed to be compatible with modern concrete, but can be significantly different from historic concrete. This has the potential to result in repairs that are mechanically incompatible and – as they vary in colour, texture and porosity – unsightly and damaging to the historic aesthetic of the structure.
Even when every effort is made to match the appearance of the substrate, proprietary materials may weather differently, and may thus be unsatisfactory in the long term. For example, to match the colour of the original concrete, a repair product may have a coloured pigment added before application, but the colour of some pigments may change over time, so the two materials will not match in the long term. Some polymer-modified repair materials do not weather or soil as much as the surrounding material and so the patched area may always stand out as being a new repair.
The use of like-for-like materials is also complicated. The assumption is that this approach will provide a material close to the original in composition and that, as a result, will perform like the original both mechanically and aesthetically. In theory, these materials should use the same mix constituents and cement type as the substrate; however, in reality, the chemical composition of cement has changed significantly over the past 200 years due to changes in manufacturing processes, so even if unmodified Portland cement is used there is no guarantee it will look or perform exactly like the original. Sourcing suitable aggregates can also be a challenge if the original quarries have closed, or the aggregates used were of poor quality or chemically reactive and contributed to the deterioration of the concrete in the first place.
There are also significant challenges in assessing the original concrete to formulate a repair material. As it has chemically altered due to hydration and carbonation of the cement, it can be difficult to ascertain the original mix design accurately, and to do so may require a larger sample of the material to be removed from the historic concrete than allowable. Allowable sample size varies depending on the material and the test required. With a listed building, for example, you have to get permission from the secretary of the Department of Culture, Media and Sport to remove material.
Furthermore, even if the original constituents are already known or can be accurately determined, the amount of water in the mix and the conditions under which it cures are key factors affecting the way the hardened material forms at a microstructural level, changing its porosity and subsequent mechanical and weathering properties.
"There are conflicting perspectives on the way patch repairs on historic structures should be approached."
In some cases, deterioration can be prevented by applying a protective surface treatment such as the following.
-
Hydrophobic treatments:
these produce a water-repellent surface by coating, but not filling, the internal pores. As no film is formed on the concrete surface, they have little effect on the appearance; however, some hydrophobic treatments will not work on concrete that is already carbonated.
-
Impregnation treatments:
these partially or completely fill the pores, effectively reducing the porosity and adding surface strength, but they may lead to the formation of a thin surface film.
-
Coatings:
these include paint or epoxies and produce a thicker protective film that is an effective barrier; however, their use in most historic structures is inappropriate as they completely change the appearance.
Regardless of the strategy that is applied, all treatments and repairs should follow conservation principles and be reversible and re-treatable. Where patch repairs are to be made or surface treatments applied, trials and mock-ups should be carried out to ensure the materials are compatible, and all repair work should be carried out by qualified contractors who have proven conservation experience.