UK adoption of building-applied photovoltaic (BAPV) systems has surged in recent years, prompted by a reduction of installation costs and a wider focus on sustainability.
However, the increasing deployment of BAPV presents fire safety challenges, including risks to property, operational continuity and life safety. These stem from design flaws, installation errors, component defects and environmental factors.
A study of 58 PV-related fires by Building Research Establishment attributes 36% of these to poor installation practices, 12% to faulty products, 5% to system design errors and 47% to unknown causes.
Meanwhile, an audit by Clean Energy Associates of more than 600 rooftop PV systems across 14 countries in 2023 reveals that 97% exhibited a defect of any kind.
Poorly trained installers increase the likelihood of mismatched connectors, improper wiring and inadequate grounding. Environmental factors also contribute to ignition risks, with rodents and birds damaging panels and cabling, or nesting in components.
Plastics and fire dynamics increase vulnerability
Some BAPV systems include plastic components such as frames, mounts and back sheets, which can contribute to fire development once a fire has begun because they can be made of combustible materials. The use of PV systems with non-combustible components, like metal frames, can significantly reduce these risks, but systems incorporating plastics remain widespread.
Installed systems also significantly alter the dynamics of fire spread on a roof; the gap between angled panels and the roof creates a stack effect, for instance, enabling heat and smoke to accumulate and spread rapidly beneath the system.
A panel that is heated by fire can also radiate back down to the roof materials below, which accelerates fire propagation. These dynamics are influenced by panel inclination, array geometry and roof composition. However, current roof fire-testing standards fail to account for these.
Altered fire dynamics increase the vulnerability of roof assemblies, particularly when combustible membranes, insulation or other materials are present beneath the panels.
Even if a BAPV system itself is non-combustible, these dynamics can lead to fire performance failures in roofs that meet statutory guidance in Fire Safety: Approved Document B.
If a fire mitigation layer is used between the PV system and roof to reduce risk, this can exacerbate secondary issues such as moisture retention, drainage problems and material decay. These may undermine the roof in the long term and invalidate any warranties.
Meanwhile, bird mitigation strategies such as nets may trap debris and worsen risks, though laser deterrents or trained birds of prey could be used.
Why funding's allocation of responsibility threatens safety
Fire safety is also affected by BAPV funding structures, which define responsibilities for design, installation and long-term maintenance.
Under power purchase agreements (PPAs), for instance, third-party investors fund the installation and retain ownership and maintenance responsibilities, while the building owner or operator purchases the energy generated.
This arrangement can create a disconnect between system maintenance and building users, meaning fire safety may be overlooked. However, technically savvy system owners are often more inclined to maintain systems, to optimise output and returns.
An alternative to this is a rental model, where landlords fund BAPV while tenants benefit from the energy output and typically assume maintenance responsibilities, though the division of roles frequently leads to accountability gaps as well.
Tenants may lack the motivation, expertise or resources needed for maintenance, jeopardising fire safety, while poorly defined agreements or miscommunication can increase the risk of inadequate upkeep.
Self-funded models in turn mean that tenants independently finance and install systems. These projects often prioritise short-term cost savings, which can result in contractors compromising safety and quality. Inadequate oversight and a focus on minimising capital expenditure can lead to poorly designed and installed systems.
Lack of regulation prompts private-sector guidance
UK fire safety regulations are goal-based, focusing on outcomes rather than prescribing methods. Fire safety: Approved Document B and BS 9999: 2017 Fire safety in the design, management and use of buildings. Code of practice both lack specific provision for BAPV systems.
Critical aspects, such as panel inclination, gap height, roof material combustibility, access and array geometry, remain inadequately understood. This lack of specificity results in inconsistent application of fire safety measures, with projects often relying on variable levels of industry knowledge.
In the absence of statutory guidance, insurers had to shape fire safety standards for BAPV systems. Documents such as RC62: Recommendations for fire safety with PV panel installations, jointly developed by RISC Authority and the Fire Protection Association – along with prescriptive standards from insurers such as Aviva, FM and Swiss – offer recommendations on installation, material selection and system design.
These standards often include requirements for maximum array sizes, minimum offset distances, like clearance between the edge of the roof and panels, and non-combustible materials beneath PV systems.
While effective for reducing property losses, these standards focus primarily on minimising claim costs and protecting assets rather than addressing broader goals, like life safety, environmental, social, and governance-related targets, or cost. Stakeholders must adapt these recommendations to suit specific project needs to develop a tailored package of safety measures.
Third-party certifications such as the Microgeneration Certification Scheme (MCS) – which only covers systems of 50kW or less – and those provided by the National Inspection Council for Electrical Installation Contracting also play a key role in safeguarding safety and quality.
However, fragmented supply chains complicate consistent application. While main contractors may hold certifications subcontractors may not, leading to variations in quality. If a non-certified subcontractor is working under an MCS umbrella scheme with a larger company, the work they carry out will be classified as MCS-compliant.
'In the absence of statutory guidance, insurers had to shape fire safety standards for BAPV systems'
Design critical to reduce risks and enable access
Proper design and routing of cabling is also critical. Cables can be elevated off combustible roofing materials and housed in robust, fireproof and ventilated containment.
Routing cables externally or in fire-resistant enclosures enhance protection. The design should avoid sharp bends to reduce mechanical stress and ensure durability.
Structural integrity is likewise essential, particularly with the increased frequency of extreme weather. Systems must be designed to withstand high winds and hail using durable mounting systems and components to reduce the likelihood of damage that may cause electrical faults.
Furthermore, systems must be designed for safe and practical access to enable both maintenance and emergency interventions. The former requires sufficient spacing for cleaning and inspections, without which debris such as leaves, dirt and vermin nests can accumulate as potential fuel for fires and obstruct ventilation, raising the likelihood of overheating.
Maintenance protocols should include the regular use of thermal imaging tools to detect and address micro cracks in PV panels as well. These are often caused by hailstorms, bird impacts or physical damage, and can create hot spots leading to localised overheating and potential ignition.
Firefighters will also require pathways through arrays and unobstructed roof edges in the event of an emergency. At the same time, access points such as internal stairs should be secured to prevent unauthorised use, reducing risks of vandalism and system damage. Careful planning must balance safety, security and functionality to mitigate long-term risks.
How technology can support competent working practices
Panel-level electronics, including DC optimisers, arc fault detection systems and rapid shutdown devices, can isolate faults and mitigate the risk of ignition from arcing, where electricity jumps across two points, and cell hot spots, where a cell or group of cells become defective and dissipates power instead of producing it.
Remote monitoring systems also improve risk management by enabling real-time tracking of temperature, electrical performance and potential anomalies. Drones and roof-based robots equipped with thermal imaging can complement manual inspections.
However, the use of advanced technologies such as these must be paired with systemic improvements to address underlying risks. Fragmented supply chains, cost-driven procurement models and weak regulatory frameworks often create the conditions for hazards.
Even the best tools cannot compensate for poorly designed or installed systems. Effective risk management begins with engaging competent design and construction teams who prioritise robust safety standards.
Cost–benefit analysis is essential. Expensive technologies should not overshadow the importance of getting the basics right, such as proper system design, component selection and installation.
RICS Fire Safety Conference
15-16 October | 08:30 – 13:20 BST | Online
The fire safety landscape across the UK and Ireland is changing rapidly. With the Building Safety Act 2022 in force and the government’s acceptance of all the Grenfell Inquiry phase 2 report recommendations, built environment professionals must now meet stricter legal duties, deliver higher standards of safety, and manage more complex risks throughout a building's lifecycle.
The conference will help you to find out what the fire safety reforms mean for you and your projects. You will hear directly from regulators, practitioners, and policy leaders tackling the challenges of compliance, competence, and collaboration, and understand how national frameworks and the Building Safety Act 2022 impact your daily responsibilities.
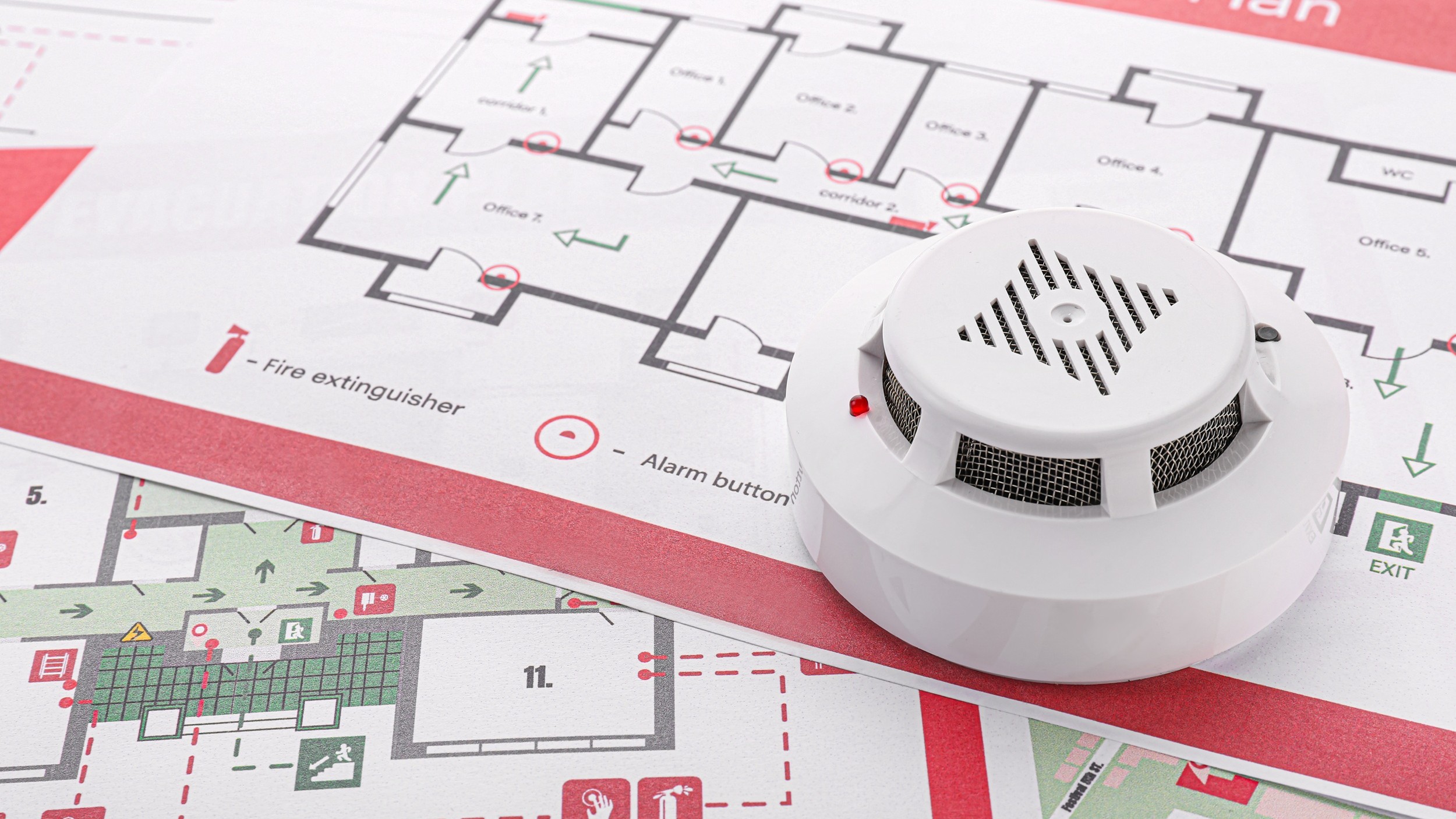