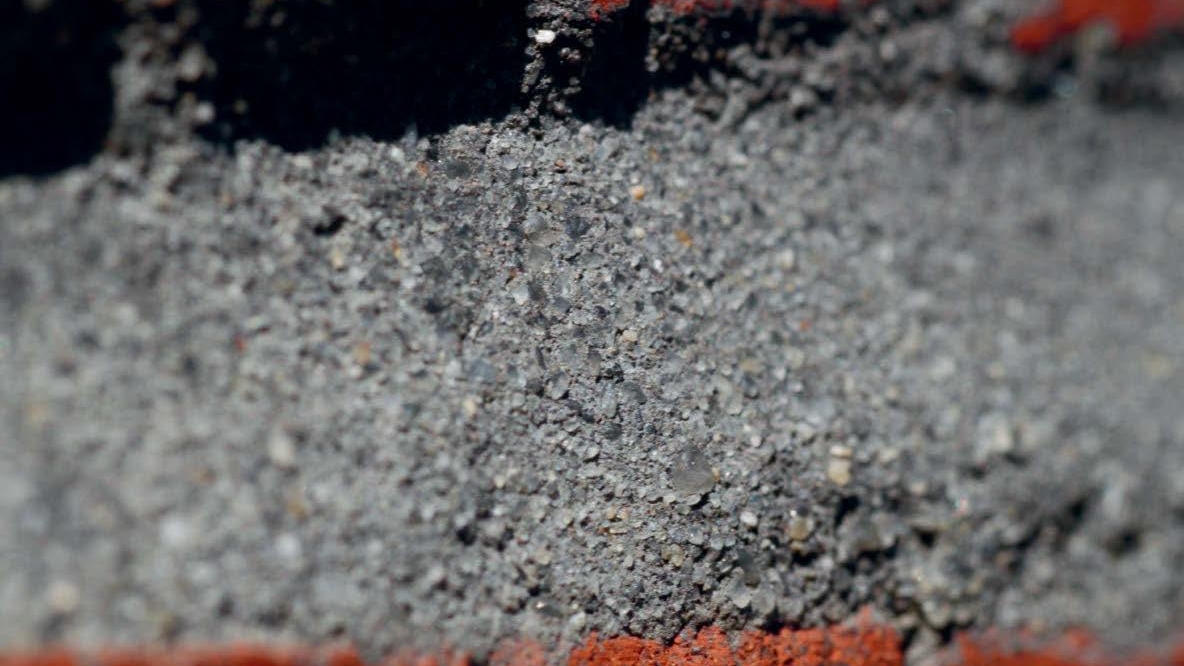
© Giovanni Pesce
In December 2018, BBC2's Victoria Derbyshire programme reported that mortar in the brickwork of hundreds of new builds had been found to be crumbling and powdery, a story picked up by the New Home Blog.
While this brought the issue to public attention, specialists had been aware of it since at least 2003, although the extent of the problem was probably unknown to most of them until recently. The two blog posts by retired construction manager Phil Waller plus a third instalment provide a detailed technical analysis.
The problem is simple: the mortar used in a number of new dwellings in the UK can be easily brushed or lightly scraped from joints and washed away by rain. As a consequence, some are already experiencing major structural problems that need repair or, more commonly, demolition and reconstruction.
"The mortar used in a number of new UK dwellings can be easily washed away by rain"
This suggests that the quality of the mortar used is not of the required industry, standard specifically BS EN 1996-1-1: 2005 + A1: 2012 Eurocode 6: Design of masonry structures. General rules for reinforced and unreinforced masonry structures, although that in turn refers to further standards such as BS EN 998-2: 2016. As in the case reported by the BBC, insufficient cement in the mixture is the probable cause of this problem, which is well known to have a negative effect on the physical and mechanical characteristics of mortars, affecting the structural stability of a building. The problem cannot therefore be considered a minor defect.
At present, there are no agreed UK or European tests that can be carried out on site to evaluate the compressive strength of a hardened mortar. This is an important consideration, given that compressive strength is the characteristic used by BS EN 1996-1-1: 2005 + A1: 2012 – and thus by the NHBC and other regulatory documents – to classify the mix.
Mortar make-up
At the centre of the problem is the hardened mortar, which is laid in layers just 10mm thick, 100–300mm wide, and several metres long. Testing the mechanical properties of this is difficult, if not impossible, because of the physical conditions.
Although small samples of mortars can be removed, testing is challenging as equipment must be adapted to their size; consequently, it is impossible to use any current standard for this process. More importantly, any sample removed from a mortar joint is likely to crack while being removed, and this can substantially affect the results of the mechanical tests.
Any test results would therefore be unlikely to prove that the mortar had not been produced to the right standard, for instance if it were necessary to do so in court. The problem is not so much the difficulty of testing such mortar; rather, that traditional testing techniques cannot produce any meaningful results.
The only way to assess the mechanical properties of the mortar and obtain reliable results that could be used in a court would be to cast some cubes of mortar at the same time it is laid in the wall, and to test these in the conventional way. However, there is currently no regulation requiring the production and testing of such cubes because this would entail further costs and additional time, as samples would need testing 28 days after casting.
It is still possible, though, to get an idea of the mortars' mechanical properties by methods such as brushing or scraping the joints with a flat-blade screwdriver or even a finger. If this removes a substantial amount of material with no or very little pressure, and if the material removed is powdery, then the mortar is showing signs of weakness.
It is important to emphasise that any tests – even if carried out by a professional with equipment such as a scratch tester – do not actually provide information on compressive strength, because these tests are affected by various factors such as joint finish, mortar type and sand type. However, research, including this piece, has found a correlation between the so-called scratch index and the cement content.
Any test that involves brushing and scraping can only be used as a possible symptom of a problem, not as evidence of the wrong cement-to-sand ratio. But further evidence of mortars' mechanical properties can be gathered by looking at signs such as holes, cracks and even erosion where water has run down the surface of walls. All the same, it is best not to assess the quality of mortars on the basis of visual inspections alone, because even if the mortar looks fine on the surface its strength may not be of an industry standard beneath, where, for instance, the wall ties are located.
Laboratory investigation
If after an initial inspection the surveyor suspects that further investigation is needed, mortar samples can be sent to laboratories for testing; a list of certified labs is available from the UK Accreditation Service. These cannot test for compressive strength either, but they can investigate other, related properties such as the cement-to-sand ratio.
Because of factors such as the cost of materials, various types of blended cement are currently used instead of the more traditional CEM I, once called Portland cement; for instance, CEM II Portland fly-ash cement is currently a widely used alternative.
These blended cements are well known among specialists, being perfectly suited for masonry mortars and providing the minimum compressive strength required by surveyors. However, the complex chemical composition of such cements makes it more difficult to assess the actual binder content in the mortars when set. In fact, mortars with such blends contain less Portland cement but, because of the other components, their mechanical properties are equivalent to those of mortar made exclusively with CEM I Portland cement.
In addition, some chemical compounds that enable cement identification during mortar analysis are themselves difficult to detect, and even laboratories specialising in mortar analysis find it hard to assess the original cement-to-sand ratio of the mix. Any result can then only be a rough estimate that rarely enables labs to establish definitively whether a mortar was produced according to the requirements listed in the specifications or not.
This being the current situation, the building surveyors group at Northumbria University is looking to develop on-site tests to assess the mortars' compressive strength. The problem could be more easily solved by requiring lab testing of mortar samples taken from sites so that housebuilders can ensure they comply with current regulations. But until such testing is mandated, we can only try to make correct identifications in as many cases as possible, and train specialists to deal with the problem.
Although this is an issue that the whole construction industry should recognise and try to resolve, building surveyors should be directly involved because they are the professionals who have to assess the quality of the mortar and seek further advice if needed.
Mark Kirk and Giovanni Pesce are senior lecturers at the Department of Architecture and Built Environment at Northumbria University
mark.kirk@northumbria.ac.uk
giovanni.pesce@northumbria.ac.uk
Related competencies include: Building pathology, Inspection