While construction growth over the coming decade is likely to benefit from technological developments in the industry, it will also have to address environmental imperatives.
With this in mind, the recent RICS Global construction and infrastructure conference considered, among other issues, how to build sustainable, efficient and intelligent urban environments. One panel in particular focused on construction's role in adapting to climate change.
Bhavya Kukrety, the managing director of engineering and project management consultancy Meinhardt Singapore, and Heather Evans, partner and global lead of sustainability for Rider Levett Bucknall (RLB), explored strategies for building resilience and how the industry can contribute to climate change mitigation, in a session moderated by RICS head of professional practice for construction Amit Patel MRICS.
Amit Patel: From a consultancy point of view, what's changed in the past five years in terms of sustainability in construction?
Heather Evans: It has been a transformational time. Before COVID-19, sustainability was often seen as a nice-to-have option, but not necessarily central to the construction industry. We've seen a significant transformation since then, not only in terms of what our clients need but also what the regulation and guidance is saying as well.
Our clients around the world, whether public or private, are considering not just what they can do to look good but also what they can do to innovate and make sure that they're creating buildings and infrastructure fit for the future.
AP: Bhavya, I'm interested in how this is affecting infrastructure, particularly the work that you do.
Bhavya Kukrety: Singapore is quite committed to the transition to sustainability, and has been for the past ten to 15 years. But in the infrastructure sector it has been tough for us in all the countries including Singapore, to be quite honest, because there are a lot of moving parts, including digitisation of existing infrastructure assets.
As engineers, we are trying to change the way we think about urban infrastructure. There is still some way to go, from considerations such as urban financing to material choice and client requirements.
It needs us to move from a mathematical model and instead consider the actual impact of a product or material that we use on the site. A lot more inclusion in terms of input from a diverse group of professionals and positive thinking is needed for the next 15–20 years from all industry leaders.
AP: I do think we are in the infancy of this movement; it's just about to take off. What does this shift look like from a client's point of view, Heather?
HE: It differs between sectors and global regions. There is a huge variation in terms of the maturity of net-zero policy and climate change adaptation, as well as access to green finance.
We've seen a huge effort across the UK and Europe, particularly in the private sector. That is predominantly down to reporting regulations, but it is also a result of the availability of green finance.
Being able to draw on such funding or enjoy a preferential rate of lending has made the private sector sit up and think how it can demonstrate that it is doing well, but also change its practices to be a sustainable organisation with future-fit assets.
From a compliance perspective, there's far more regulation than there has ever been before; but voluntary reporting has also increased due to stakeholder and societal demand.
Businesses want to know that their projects are going to be sustainable, not just from the climate perspective but also for our people and communities.
AP: Have we as professionals got the skills and capacity to ensure this?
HE: This is a question I'm passionate about: how we can transform our existing skill sets to meet the industry's future needs?
As built environment consultants, we have fantastic transferable skills that can enable us to become sustainability advocates.
Right now, though, construction has a skills gap that we need to address by attracting more people into the industry – not just new joiners, but those from different industries, and those looking to return to work.
Construction historically hasn't been the fastest adopter of innovative ideas, so the green skills revolution is a great way for us to demonstrate how forward-thinking we can be.
AP: Bhavya, could you discuss some of the work your company is doing, and what barriers you face?
BK: As engineers, we intervene in construction projects at grassroots level. We try to look at the project from the perspective of a contractor, or a resident – what do they know about noise levels, last-mile connectivity, impact of digital technology and its affect on the industry?
Singapore is way ahead in this regard, and we are trying to promote such practices in the rest of Asia and the Middle East region to make progress.
We are trying to be realistic about sustainability on the ground, to cultivate an understanding of how much embodied carbon is present when you use a particular material, and how operational carbon can be minimised.
To us this is the larger challenge in the infrastructure industry, because I would emphasise that the market still looks to optimise for cost rather than sustainability.
AP: Looking at the supply chain, do you think it has caught up with market demand for more sustainable construction products?
BK: This is an important question, and my answer is that it has not.
When you are looking at the huge demand for glass and for steel, and sand, there are very few recycled materials that can replace these important construction components.
A lot of research is ongoing, but looking at the scale of mass mixed-use development projects in various regions, its applicability is sometimes challenging. I think recycled material can meet a lot of the demand from, say, an interiors or furnishings perspective or even building-level infrastructure.
But when it comes to the massive demand created by kilometres of pipeline, roads or rail networks, the industry has yet to advance to that level.
AP: Heather, from a consultant's point of view, when a client has high aspirations for a net-zero building how are those passed down the supply chain to the contractors, subcontractors and even manufacturers of goods and services?
HE: It's an important aspect to explore, because construction as an industry doesn't have particularly large profit margins, and our risk appetite generally is pretty low.
New and innovative ways of generating energy do require a significant capital expenditure, but the longer-term benefits are there, with differing ways to fund green energy generation too. It goes back to the case for collaboration; this work can't be done in silos.
We have to make sure we are not passing risk along, because the vast majority of the construction and infrastructure supply chain is made up of SMEs that cannot accept it. So as an industry we need to think about the wider benefit and consider how we can transform for the future.
Bhavya Kukrety is managing director at Meinhardt Singapore
Contact Bhayva: Email
Amit Patel is head of professional practice – construction, RICS
Contact Amit: Email
Lead the way on decarbonisation with RICS training
Get to grips with RICS' Whole life carbon assessment for the built environment, and contribute to shaping the future of sustainability in the built environment.
Our new training options, crafted by industry experts who help set the standards, are designed to equip you with the necessary skills.
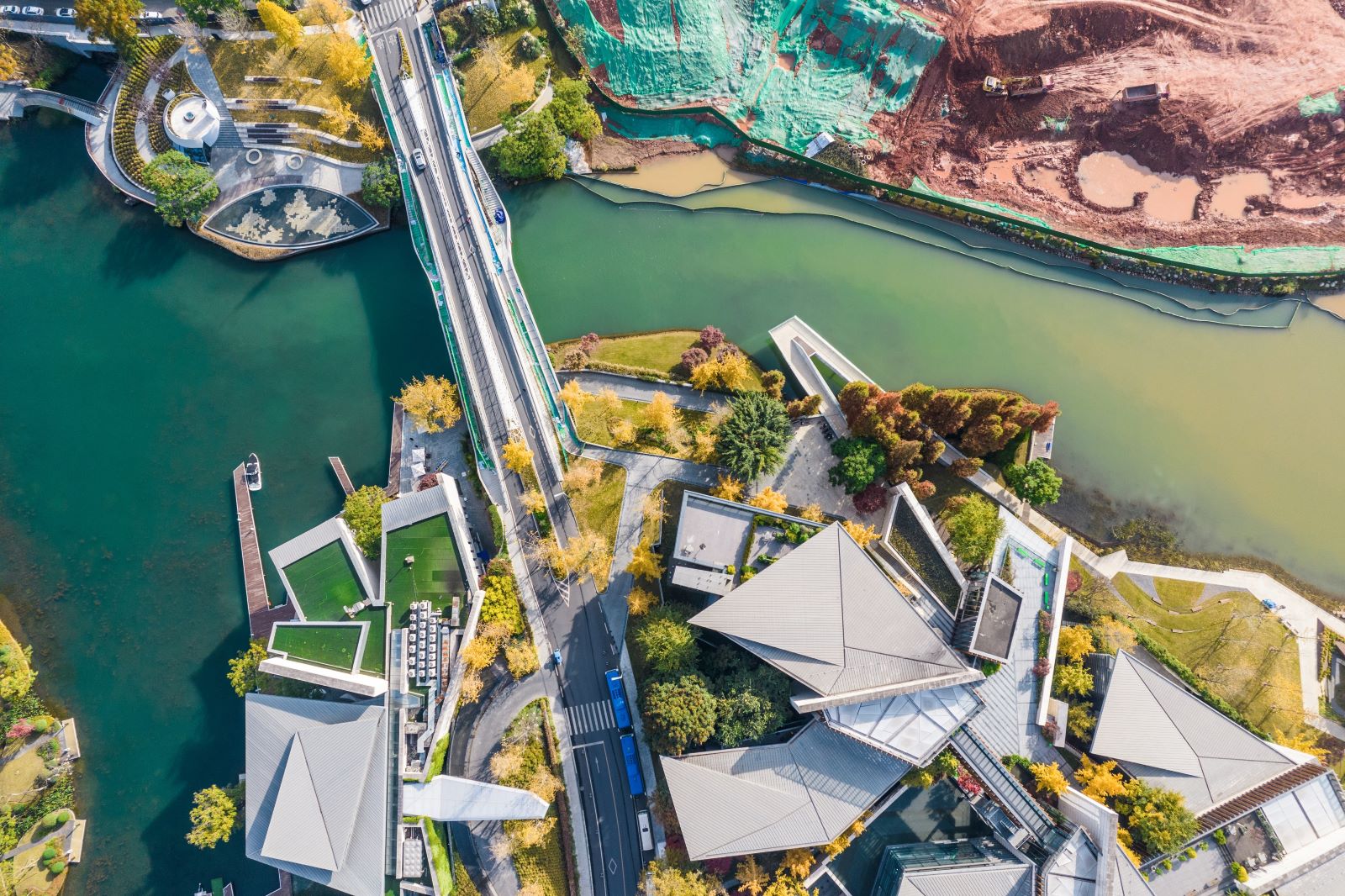