Since the COVID-19 pandemic began in early 2020, access to basic materials in a reasonable timeframe has been fraught with difficulties. The war in Ukraine and rampant inflation have only served to complicate conditions, although as we enter the fourth year of the pandemic China is relaxing lockdown rules.
In December, Builders Merchants Federation (BMF) CEO John Newcomb reported that overall availability of construction materials was gradually returning to the level it had been before the pandemic. Towards the end of the year, the cost of many such materials had fallen, although they still remained significantly higher than they had been before the UK left the EU.
Even these reductions in price could be short-lived, however, with manufacturers of energy-intensive products such as bricks, cement, glass, insulation and plasterboard warning of significant increases as energy costs continue to rise.
In January, British Steel announced a hike of £75 per tonne, on top of last year's increases of a combined £250. Furthermore, birch plywood, widely used in construction, cannot be sourced from Russia due to sanctions, while alternatives from Latvia or Finland are in short supply.
Pandemic continues to affect Chinese output
In China, many factories will also have closed in the weeks around the lunar new year, which was celebrated from 22 January to 5 February. There was also a marked increase in travel as people visited their families, but with lockdown rules relaxing this may only have exacerbated the ongoing COVID-19 surge in the country.
Numerous Chinese factories have already been shut down or are operating on much longer waiting times due to the current wave of the virus, which has also had an impact on freight bookings. Congestion is building at some ports, with Qingdao – the sixth largest port in the world – reporting that it is operating with only a quarter of its usual labour force.
That China's COVID-19 wave has not caused greater disruption is largely a result of the collapse in US manufacturing orders, due to a drop in American consumer spending and the ongoing US–China trade war. How the country handles the ongoing surge in infections in the coming months, and whether or not manufacturers and shipping companies can mitigate the delays and the increased costs, will have a significant bearing on trade for the rest of 2023.
Industrial action leads to shipping delays
The cost of shipping from Asia to the US west coast fell by 90% in 2022, while rates to the eastern seaboard fell by 77%. Asia to Europe rates are also down by 72% year on year, although they remain far above their 2019 levels, which suggests a return to pre-pandemic shipping prices is not on the cards.
Last year saw mixed fortunes for shipping as labour disputes around the world increased significantly. Bloomberg reports that there were at least 38 instances of protests or strikes at global ports, up from just eight the previous year. Further upheaval is expected in 2023.
Last year, workers at Liverpool docks in the UK rejected the offer of a 7% pay increase and took strike action, which saw the trade union Unite negotiate pay rises worth between 14.3% and 18.5% in November. Workers at Felixstowe docks went on strike the following month, winning pay increases of 8.5% as well as a £1,000 bonus.
However, a protracted labour dispute has been running since July in a number of ports on the west coast of the US. Dockers are currently working without a contract, but the threat of a strike remains. During 2020 and 2021, congestion levels at Los Angeles and Long Beach docks reached a crisis point, which saw shipping companies redirect traffic to the east coast.
Although congestion levels are now returning to normal, there is a continued preference for the ports on the eastern seaboard, due in part to the labour dispute. Congestion at New York and New Jersey docks is easing, but it remains high in the south east of the country and in Houston, Texas.
Sea-Intelligence CEO Alan Murphy reports that the overall on-time rate is improving, having risen to 56.6% from a low of 30.4% in January 2022. But this is far below the pre-2019 levels, as illustrated by Figures 1 and 2.
Japan is looking to test new supply routes to ports in Canada, Mexico and east coast US as soon as March, in preference to opening new routes to west coast ports.
The war in Ukraine has also significantly affected Japanese trade with Europe as exporters can no longer use Russian airspace or the trans-Siberian railway, while shipping to the US was affected by congestion at its west coast ports.
Semiconductor supply remains sluggish
Newcomb notes, too, that gas boilers and other products containing semiconductors remain hard to come by. The supply of semiconductors was badly affected by both the COVID-19 pandemic and subsequent changes in ordering processes. While car manufacturers reduced or eliminated demand in the early months of 2020, producers of consumer goods filled the order books in response.
Semiconductors are particularly important in the construction of smart buildings, in the automation of lights, heating, ventilation and air conditioning for instance. In addition, they are also found in vehicles, computers, phones and many other devices. The demand for more, better and faster semiconductors is therefore not likely to fall – which may therefore frustrate progress on smart building projects.
New factories are being planned in China, Taiwan, the US, Japan and Korea to meet new demand, but it will take between one and two years before they are operational. Unfortunately, shortages in construction materials and labour to build the factories are causing additional delays.
On 7 October, the US announced restrictions on the provision of equipment and services to Chinese semiconductor companies as part of the ongoing dispute between the two countries, in order to slow production. While the impact of this policy has not yet been fully felt, it seems reasonable to assume that it will cause further shortages, as Chinese-produced semiconductors are now likely to remain in China. If the trade war continues to heat up this year, then the global construction sector will experience additional disruption.
Certificate in Construction Project Management
Learn about the core elements of a construction project lifecycle and apply essential skills to plan and oversee projects of various sizes and complexity
Wednesday, March 15, 2023
10:00 - 17:00 GMT
48 CPD hours
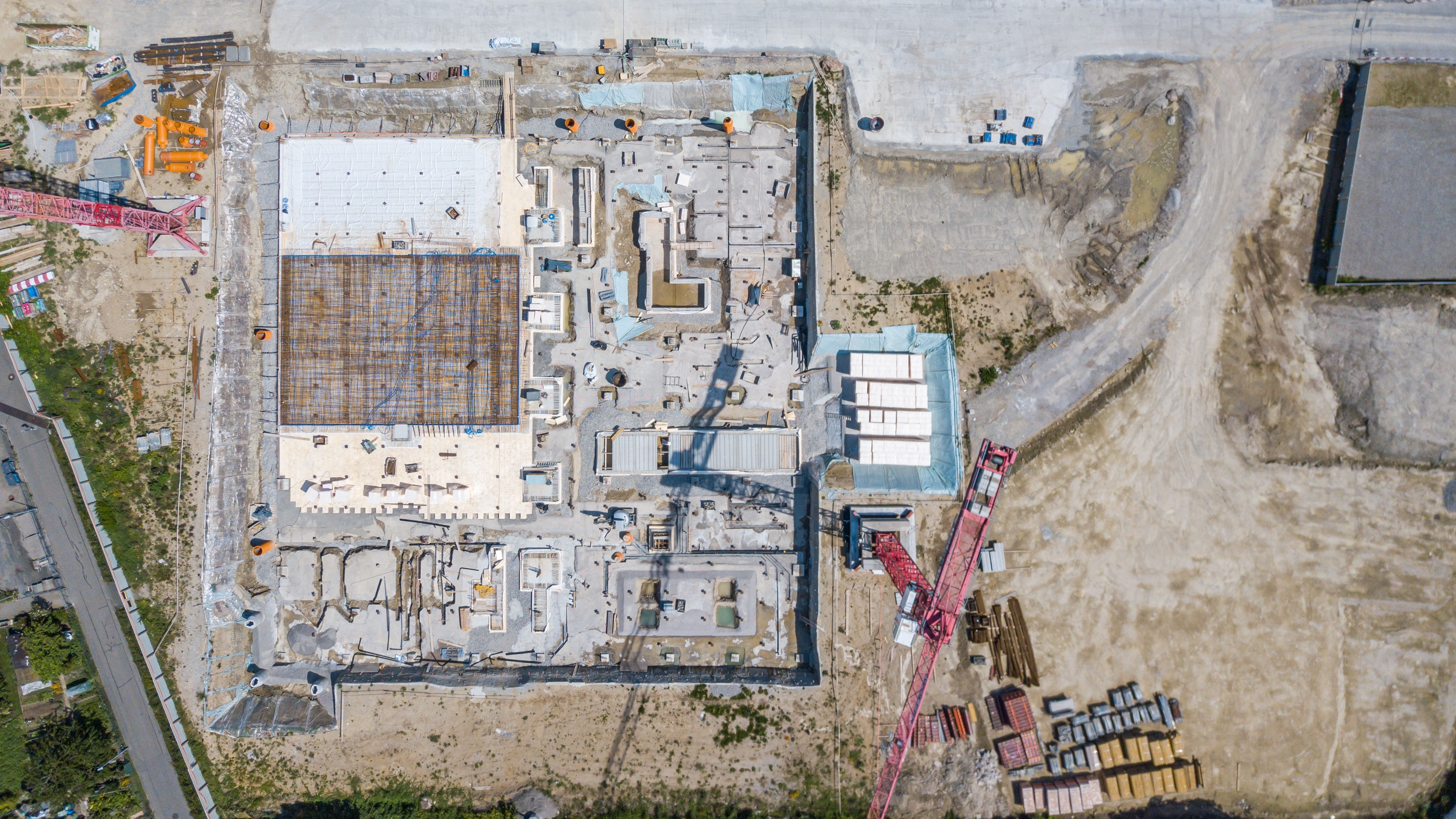