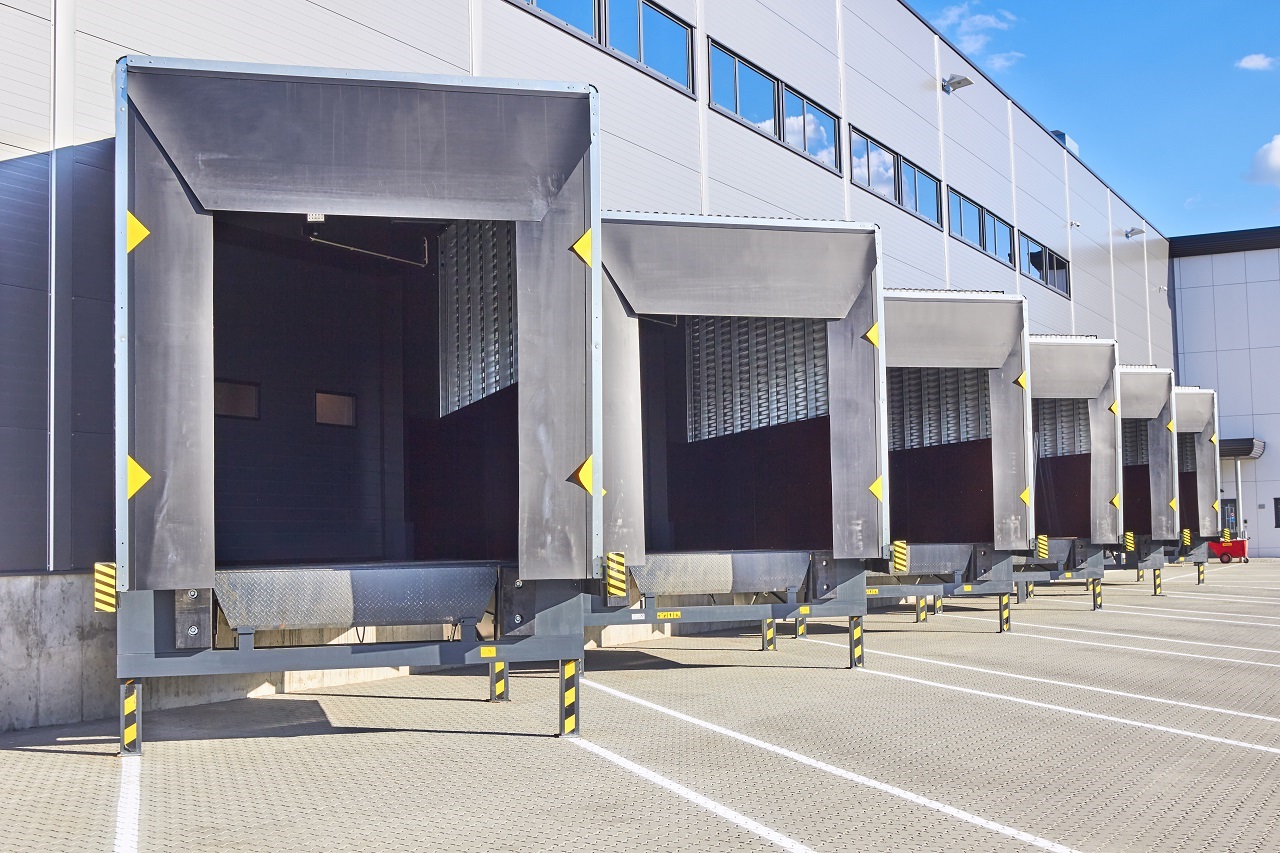
COVID-19 and the associated lock-downs has challenged supply chains and distribution networks in ways unprecedented in the history of advanced economies. Some have adapted remarkably well, others are scrambling to find workable solutions, and some have simply collapsed.
Challenges have extended across all supply chain activities, from sourcing, through transport and distribution, to the adoption of safe working practices. A common factor for many supply chains has been radical change in retailers’, manufacturers’ and shippers’ requirements for warehousing and warehouse-related activities. In some cases sales activity has slowed to a standstill and firms need somewhere, anywhere, to de-stuff containers and store goods that are still coming in from suppliers. In other sectors, health and groceries most obviously, demand has soared. However, the need to maintain safe distances while increasing throughput raises the floor-space requirement even further.
E-commerce and home delivery – services to which much retail activity is moving – is notoriously hungry for warehousing/distribution centre space. Manufacturers too have backlogs, not only of finished goods that retailers cannot currently take, but also of raw materials, intermediate and part-finished goods that are waiting on disrupted supply lines.
Mitigation and resilience
According to a report recently published by property consultants JLL entitled COVID-19: global real estate implications, the disruption to global supply chains will significantly impact the industrial and logistics property sector worldwide. The report notes that the ‘outbreak is likely to elevate the issue of supply chain risk mitigation and resilience’, making it likely businesses will start re-shoring or near sourcing, as well as diversifying sourcing, resulting in additional regional demand for industrial facilities.
The report also points out that there could be a reversal of thinking on running lean supply chains with low inventory cover, leading to businesses deciding to increase their inventory levels in the long term – all of which would increase demand for warehousing space.
Clearly, businesses will need to look carefully at how they adapt their supply chains for a new reality post COVID-19, and importantly, how they flex their warehouse space requirements to build in resilience.
Amid the frenzied acquisition of warehouse space, it is hard to discern much implementation of deep, pre-existing, strategy. This is strange as although the combination of depth, reach and scale of the COVID-19 impact is certainly unprecedented, supply chain shocks are very common.
COVID-19 counts as a natural disaster, but there are others. Regionally, many supply chains have not fully recovered from February’s floods in the UK. Weather ‘events’ in far-away places – floods in Bangladesh, typhoons in the Philippines – are an accepted hazard for the apparel industry. Globally, the effects of the Japanese tsunami of 2011 on sectors from automotive to electronics are well remembered. And it can seem that ‘100-year events’ now happen every month.
Other circumstances that impact on warehousing requirements have a more human element. ‘Preparation for Brexit’ has become a regular event, rather than the one-off that most businesses anticipated. More generally, many companies see predictable activity peaks in the run up to Christmas, Easter, or the summer – weather permitting. But how should this stock be managed? Is there a cleverer way of flexing storage capacity with demand, improving efficiency and customer service, while keeping costs to a minimum?
Clearly, going forward, companies need an intelligent strategy for their warehousing requirements. They know there will be peaks and troughs in activity, although they may vary in the confidence with which they can predict either timing or scale. They also know that to use their own assets to fully provision against short-term peak demand would be hugely expensive.
Typical strategy
So, the typical ‘strategy’ is to identify a ‘core capacity’, probably linked in some way to average throughput over the year. This will be served from the business’ own assets or through long-term contracts with third party logistics suppliers and might account for 90% or 95% of annual activity. Peaks that exceed that capacity are accommodated by short-term leasing of ‘emergency’ warehousing on a spot market.
On the face of it, this may sound like a reasonable strategy. But there are several problems. Firstly, emergency warehousing of that nature does not come cheap. Short leases are expensive, if the peak is for an event like Black Friday or Christmas there will be many other companies looking for space and driving prices up – and available space may not be in an ideal location for efficient transport and distribution.
Secondly, and depending on the profile of the various peaks and troughs and how they overlap, that ‘core capacity’ may spend much of the year seriously underused.
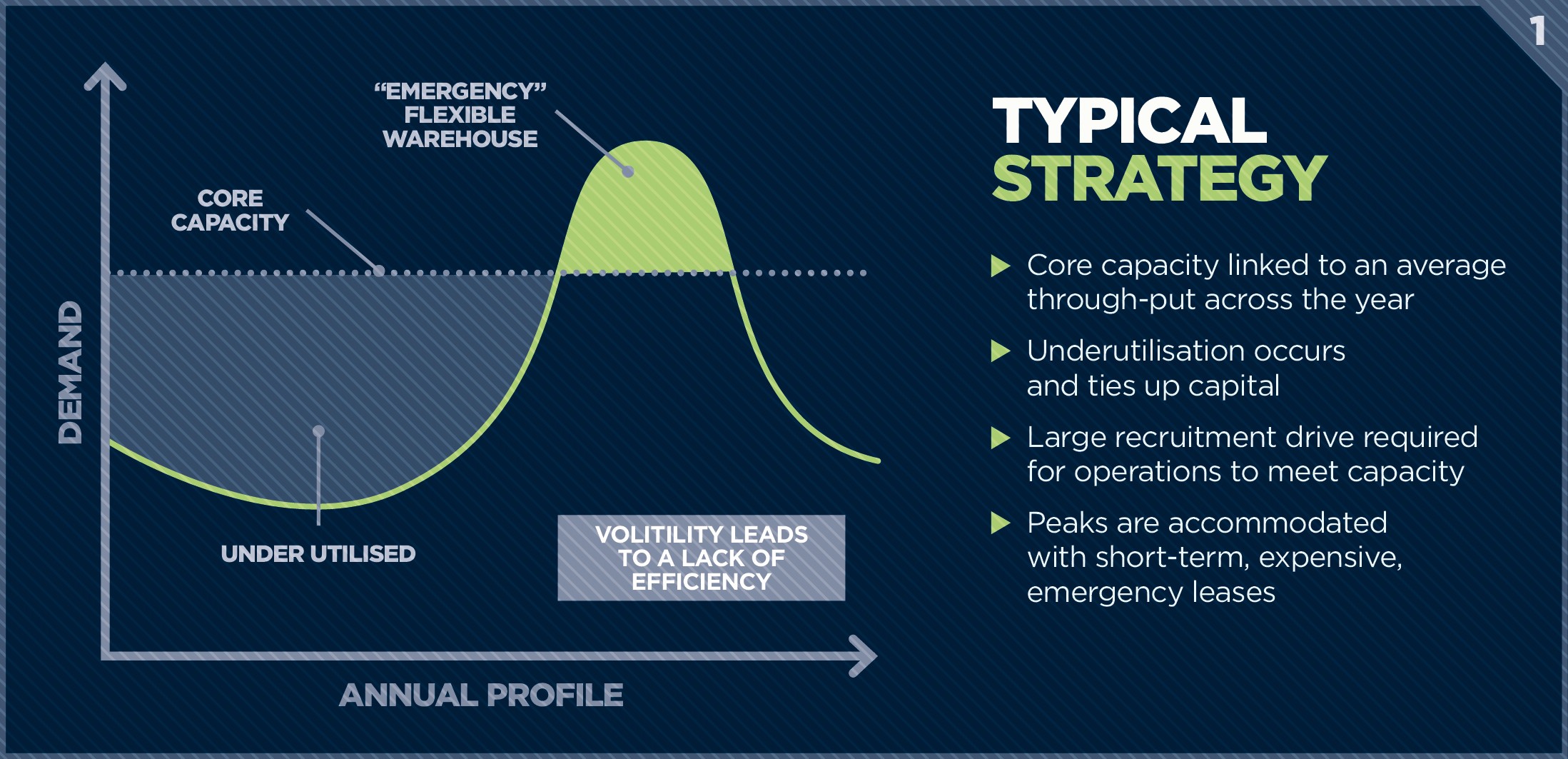
Resilient strategy
However, there is an alternative strategy, which is to significantly lower the ‘core capacity’ of in-house or 3PL warehousing, and accept that coping with peaks, whether predicted or not, is far from an ‘emergency’ but a normal way of operating. This approach requires access to a range of sites, suitable in terms of size, location, duration of availability, access to labour, IT and other facilities. By tapping into the network of resources available through an independent space broker, and by working with them on a long-term partnership basis, a coherent plan can be developed that builds resilience into the supply chain. But this relationship needs to be year-round, not ‘just for Christmas’.
As situations develop, forecasts firm up and requirements crystallise, a rolling shortlist of possible solutions can be maintained. Likely sites can be inspected in advance and assessed to ensure that robust processes and continuity are assured. Continuous assessment and analysis can enable the early securing of the best facilities at a reasonable cost – far preferable to those available under an emergency spot transaction. And because all this is planned, business can be switched in and out of the additional facilities seamlessly, with minimal impact on the costs and efficiencies of the supply chain and the customers it serves.
"As situations develop, forecasts firm up and requirements crystallise, a rolling shortlist of possible solutions can be maintained"
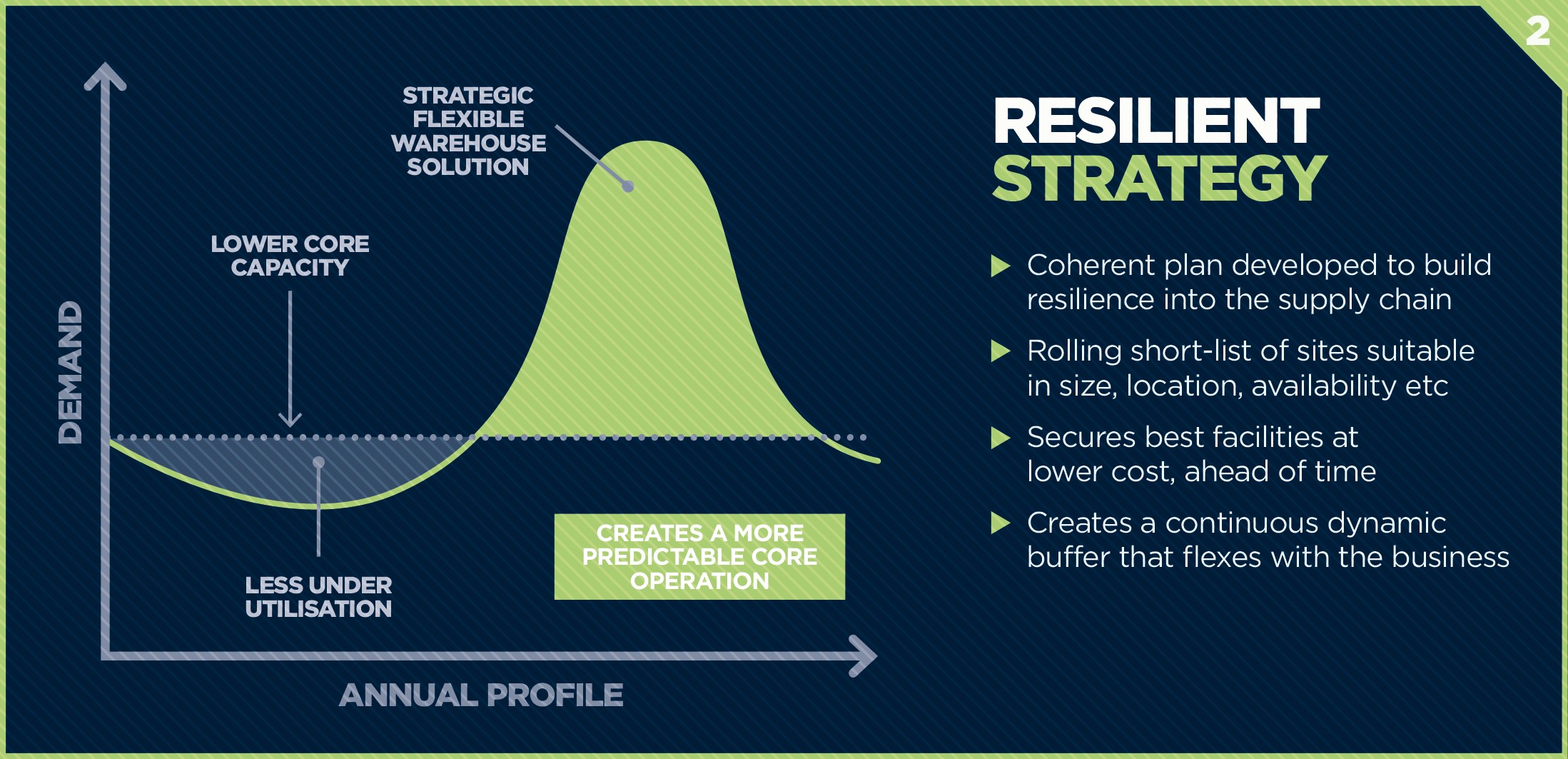
COVID-19 is certainly unprecedented in scale, but the problems in supply chain inventory and storage that it is exposing are pre-existing and, not uncommon. The world is increasingly uncertain, and our ability to manipulate supply and demand to our convenience is much diminished.
For many, ‘core’ or ‘steady state’ inventory is a decreasing proportion of the whole: much more is falling into the unpredictable, higher-risk segment and that has a big impact on warehousing strategy.
Businesses that win out will take a strategic approach to using flexible storage space on a planned, on-going and coordinated basis, creating a continuous dynamic buffer that flexes with the business. They will work with a specialist space broker/facilitator, not to locate a shed at the last minute, but to analyse the supply chain, the inventory requirements and characteristics, as well as the resulting warehousing needs and solutions.
Related competencies include: Business planning, Planning and development management, Property management
Bis Henderson Whitepaper: Warehouse space: a new strategy for a new reality