Sri Lanka is largely known for its growing tourism sector, beautiful tea plantations and massive clothing industry. This long history in garment manufacturing sometimes raises questions about the working conditions in older factory buildings, mainly because of the hot and humid climate, combined with insufficiently ventilated and often noisy working spaces.
So when the opportunity arose to renovate an old factory building in capital city Colombo Jordan Parnass Digital Architecture (JPDA) sought to make drastic improvements in the energy efficiency of the building and the working environment. The goal was to design a state-of-the-art factory that would achieve the Passivhaus certification. Working with a project team across the globe, the Passivhaus Institut was charged with benchmarking verification and certification of the retrofitted factory in Colombos Katunayake district.
Pioneering sustainability
The Star Garments Innovation Centre is the first Passivhaus-certified building in Sri Lanka, assessed against the stringent EnerPHit standard that was designed by the institute for the renovation of existing buildings. The project's location in a hot and humid climate, and its use as a manufacturing facility meant increased attention was paid to strategies that would reduce solar gain as well as lowering heat from equipment and occupants. Controlling the humidity is not only essential for achieving the Passivhaus certification, but also in ensuring better thermal comfort for the workers.
JPDA, which is based in New York, also recruited Steven Winter Associates (SWA) to provide technical assistance to the project team. SWA's responsibilities for this project included Passivhaus design analysis and recommendations, mechanical design review and airtightness testing. In 2016, SWA conducted a utility analysis of the factory building before any renovations were made to predict and later be able to verify the energy that the innovation centre could save by being designed to the EnerPHit standard.
The main challenges identified in this feasibility study were the lack of equipment and construction materials necessary to achieving an energy efficient building, such as energy recovery ventilation units, sealing tapes for airtightness and air barriers. Moreover, it was difficult to establish measured primary energy use and resultant costs as distinct from industrial process loads. The occupancy and usage patterns are generally complex and needed to be thoroughly analysed.
The goal was to create a regional model of a highly energy-efficient building and get local experience for future developments, while maintaining cultural identity and working processes such as the relation between exterior and interior spaces, and internal organisation such as a ground-floor semi-exterior lunch eating area.
"The goal was to design a state-of-the-art factory that would achieve the Passivhaus certification"
After extensive research and multiple calculated variants, the predicted outcomes were a potential reduction of 50 per cent in primary energy consumption and a payback period of seven years if the load-bearing steel structure were to be re-used. The primary energy calculation by end use done with the Passivhaus Planning Package (PHPP) is seen in Figure 1.
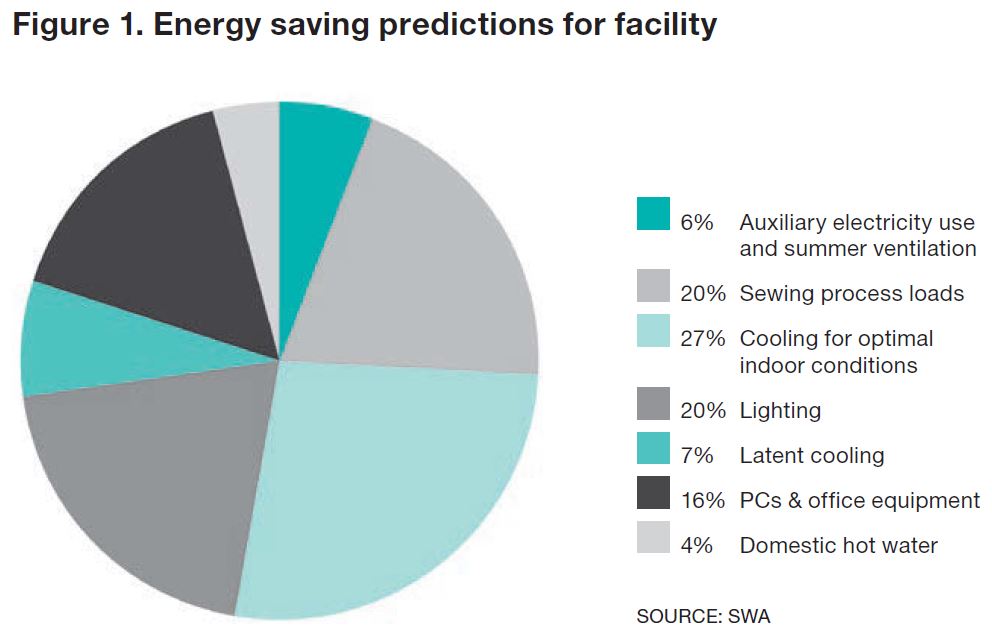
A series of measures were chosen for the refurbishment to address different features of the building, such as the exposed aesthetic structural steel frame with masonry infill, the unconditioned interior spaces below treated areas, and re-use of the existing concrete slab that forms the foundations. A high-performing curtain wall with double glazing and a solar heat gain coefficient of 0.22 allowing only 22 per cent of solar radiation to enter the building was also proposed, in conjunction with strategically designed overhangs and external shading screens to reduce the building's overall heat gain. JPDA created a physical mock-up of the typical connection between window and wall to help the contractor visualise the assembly sequence and methodology on site.
The upper floor of the factory is the main production area, and after refurbishment it features a broad column-free space. The lower area perimeter is pulled back up to a full bay, the length of a structural opening between load-bearing pillars, in some areas to provide natural shading, and is dedicated to offices and meeting rooms.
An exterior insulated finish system continuously wraps both existing and new structural components and reduces thermal bridging, while the new roof is made of prefabricated sandwich panels. All exterior surface coatings have been specified as low absorption or highly reflective to reduce cooling loads further.
To minimise the chance of thermal bridging, a fluid-applied thermal break was used at the purlins where they penetrate the insulation layer to connect to the columns. Advanced dehumidification controls use waste heat from the cooling system to enhance capacity sustainably.
One of the main challenges was the on-site coordination and quality assurance of the work. Without having previous experience in Passivhaus building, the contractor completed the renovations successfully with the help of JPDA, SWA and the Passivhaus Institut. Checklists were developed to guide the step-by-step building process and assure quality.
In-use figures are now available for almost the first two years of the refurbished building's occupation, so we can see how much energy was saved in comparison to the old building. Furthermore, we can compare the annual energy use predicted by the PHPP with the actual usage measured.
After a year of occupancy, the innovation centre has reduced annual energy use by around 54 per cent compared with the previous factory building's performance. It is also noteworthy that the monthly utility data shows the centre's energy use is around nine per cent lower than the predicted energy use over the course of the year on average.
During the consultancy and certification process the Passivhaus Institut has actively contributed consultancy on the refurbishment. Everyone who was involved benefited from the pioneering work of this Sri Lankan project.
Many of the measures employed – including continuous exterior insulation highly efficient windows variable refrigerant flow heat pumps for cooling with wraparound heat pipe for enhanced dehumidification capacity and balanced ventilation with heat recovery – could be used in future buildings in tropical climates. The entire project team is excited to see the potential growth of Passivhaus construction in such regions as a result of the innovation centre's success. To honour these ground-breaking achievements, the Passivhaus Institut has awarded the centre the EnerPHit Pilot Project Certification.
Dragos Arnautu is architect and energy consultant at the Passivhaus Institut in Darmstadt Germany. He is grateful to Jordan Parnass of JPDA and Dylan Martello of SWA for their contributions dragos.arnautu@passiv.de
Related competencies: Sustainability