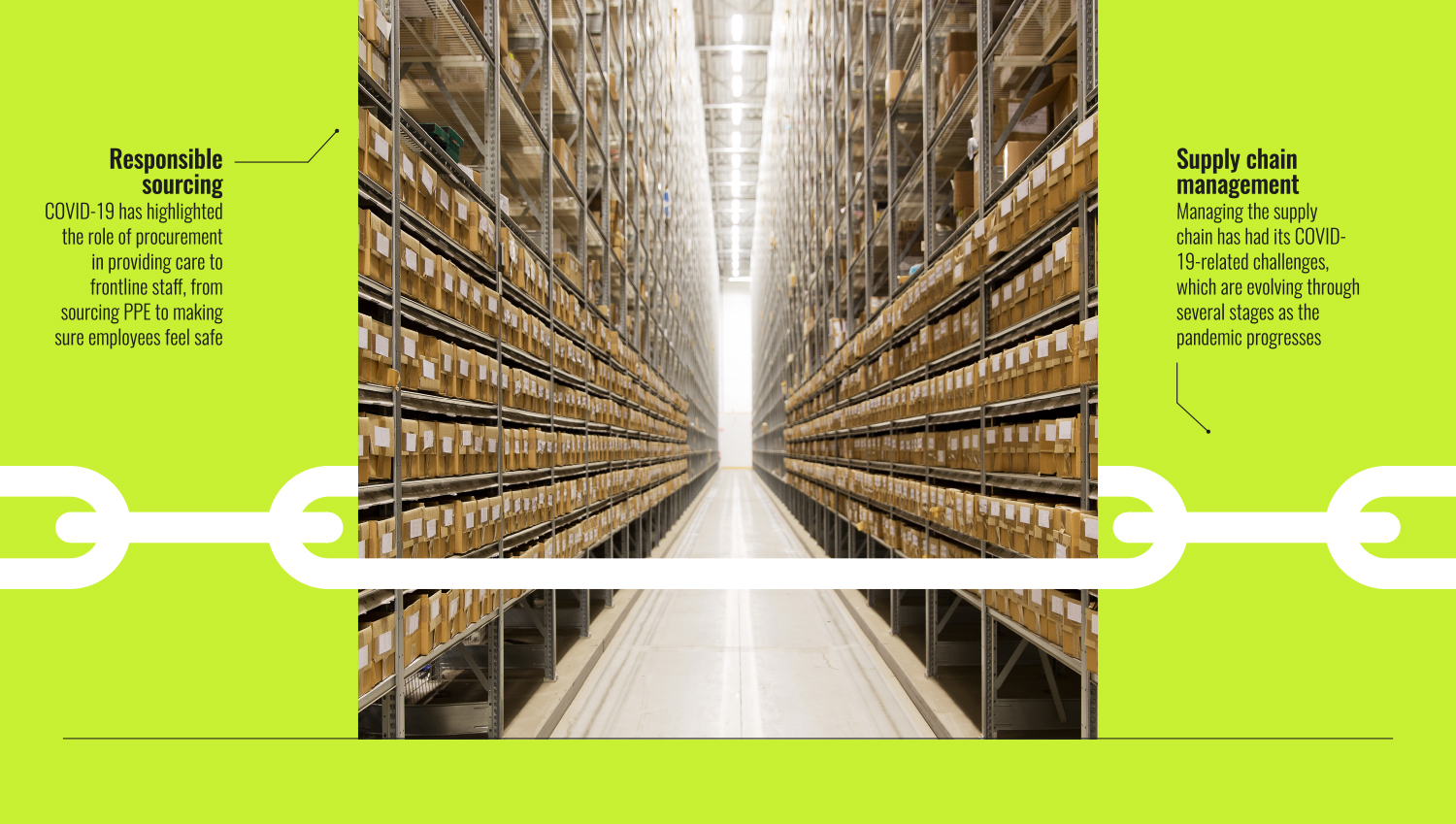
Although people might not want, need or be able to travel around much this year, the same certainly isn’t true for goods and some services. Exemplary procurement is usually a key part of facilities management and COVID-19 has, if anything, highlighted this even more.
So it is timely that RICS is producing a code of practice on the topic, reflecting procurement’s position as an essential value driver and organisational influencer. It is, after all, responsible for up to 70% of companies’ revenue, according to CIPS research, which means that small reductions in costs can have a huge impact on profits. The RICS Procurement Code also aims to take a stand on corruption, something that CIPS says can add up to 10% to business costs globally.
Duty of care to staff
The Code highlights the issue of responsible sourcing instead of a “by any means necessary” approach. In the time of COVID-19, that could include things such as “having a duty of care to front line staff”, explains Angela Love, director of Active Workplace Solutions. Such an approach would cover everything from simple, practical measures such as making sure staff have hand sanitiser and a spare mask in their pockets, to “having someone to speak to, if they don’t feel comfortable going into a certain environment”. She adds: “We’ve had to change shift patterns too, so, for example, we don’t mix teams of decorators with teams of electricians, and multi-task teams of cleaners and handymen would all keep in their bubbles.”
John Crombie, head of quality, health, safety and environment (QHSE) UK & Ireland with FM services provider Atalian Servest, adds that it too prioritises responsible sourcing. “Whenever we take on a contract, we vet their existing suppliers very carefully and, if necessary, help them achieve the high standards we work to,” he says. What has generally helped in the past few months, he says, has been the use of a business continuity and disaster recovery document. “That’s enabled us to provide the right level of critical care, whether that’s fire alarm maintenance, PPE allocation for our staff in care homes, or any issues in the universities we serve.”
Managing the supply chain
Erland Rendall MRICS, director and owner of consultant Atorus, says the way the supply chain has been managed during COVID-19 has evolved through several stages, from getting IT hardware physically to people’s homes in the first few weeks, to sourcing items such as hazard tape for summer’s partial return to work with between 20-50% occupancy. Now it means “considering the knock-on effect to certain services such as insurance. That laptop in someone’s home – is it covered, for instance? The cleanliness of the hardware itself also needs to be considered. Has it been bacterially cleaned along with the screen, cables, mouse and keyboard? Any business or entity needed to consider this along with the testing and resilience of data connections, system security and access as well as the insurance policy cover for such elements of hardware that were no longer in the office location."
It’s also presented challenges in terms of maintenance and managing the providers that supply these services. “Instead of the usual balance of planned and reactive, the current situation has thrown up a set of scenarios that are short-term focused, rather than what’s going to happen next month or next year,” says Rendall.
That said, the brave new world of procurement has thrown up some positives this year. In terms of both clients and suppliers, “we have forged some really strong relationships”, says Love.
COVID-19 may have put procurement under greater pressure but FMs have come out fighting and, with the new RICS code, they will be even better placed to provide robust responses and reassurance.
“Instead of the usual balance of planned and reactive, the current situation has thrown up a set of scenarios that are short-term focused” Erland Rendall MRICS, Atorus