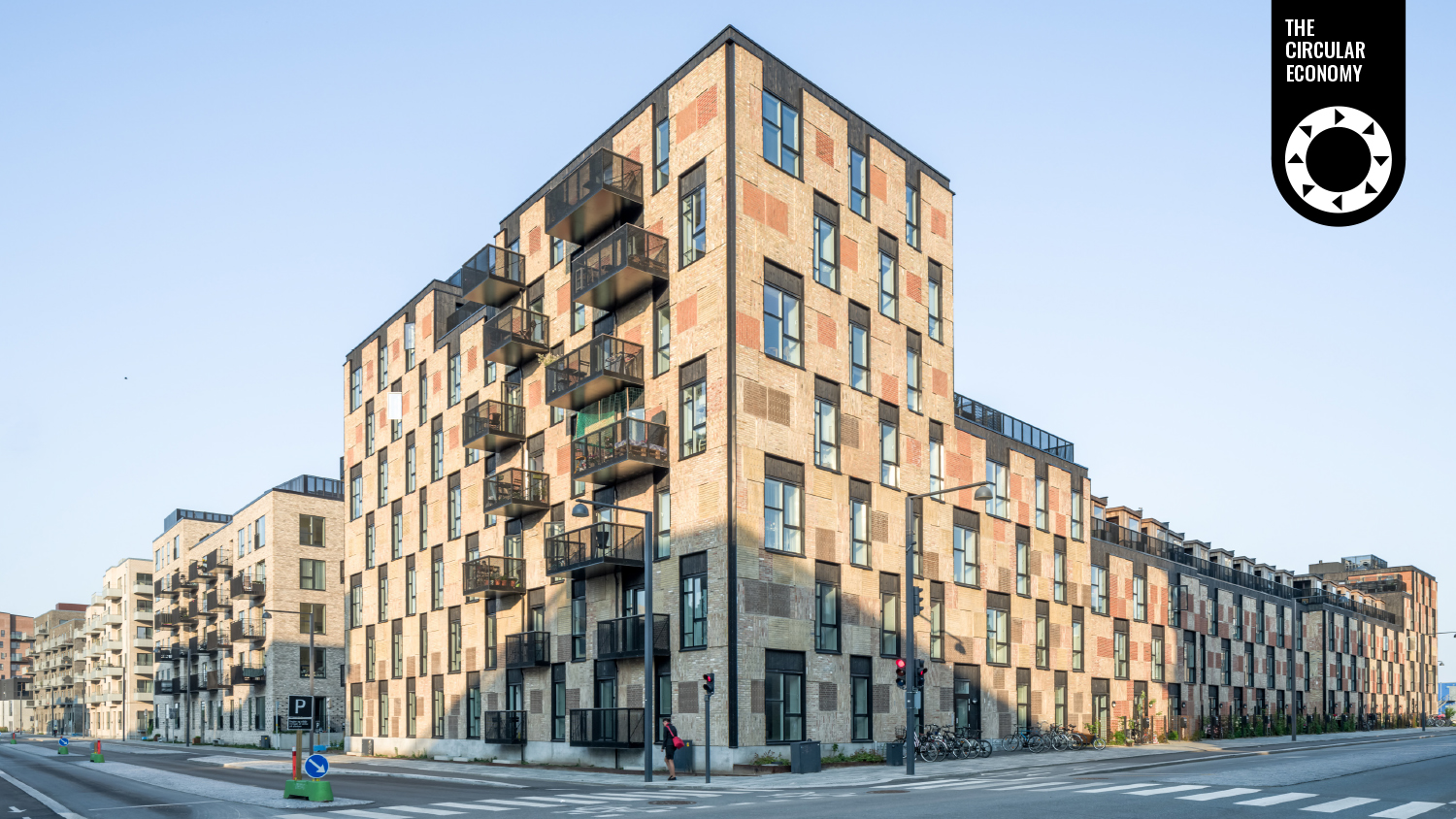
Lendager Group, The Resource Rows. Image: Rasmus Hjortshøj / COAST Studio
Construction consumes huge volumes of raw material and produces an inordinate amount of waste. Rather than engage in the familiar cycle of demolish and replace or refreshing fit-outs every few years, isn’t it time we saw buildings as mines for materials that should be harvested and reused to create the architecture of tomorrow?
Such is the argument put forward by supporters of the circular economy, who want to eliminate waste and ensure that products and materials recirculate and retain their value for as long as possible.
Salvaged materials typically have much lower embodied carbon than newly manufactured materials because the carbon used to make them has already been spent. The more the industry can use, the better the prospects for the planet.
Consultants worldwide have engaged in various efforts to harvest, upcycle and resell materials and components from buildings, and at the vanguard are a few innovators trying to demonstrate how the model can be scaled up to create a stable market to serve the industry with safe and reliable products.
Adjusting the value chains
Changes to current practices are needed to stimulate the supply of reused materials, to create upcycled products with adequate quality and durability, and rejig traditional construction value chains to ensure that everyone is along for the ride.
Market demand for salvaged products is generally high (developers and tenants are increasingly keen to demonstrate their green credentials to clients) but encouraging supply and finding people with the inclination to take materials out of old buildings remains a barrier.
Andreas Englund is business developer at the Swedish Environmental Research Institute, which is developing a prototype national platform called CCbuild to stimulate a circular economy in Sweden’s building sector. He says: “If the perception is that reuse is not profitable, it’s not done at the scale that we need. So we had to put the emphasis on supply to get the material out of old buildings and stimulate real-estate owners and constructors rebuilding and demolishing buildings to provide materials to the market.”
“If you can open up a building and see what's inside and then categorise it you can start the process. Early information is the key” Andreas Englund, Swedish Environmental Research Institute
Library of materials
The institute is developing a new digital marketplace for reused material and an associated database of available products. The focus is on office buildings and commercial real estate, which have a particularly high carbon footprint because interiors are frequently remodelled, and products such as doors, suspended ceilings and glass partitions can be frequently extracted and resold or recirculated.
The onus is on “early inventory” and the system encourages tenants who are about to leave a property to list items suitable for reuse in a digital product database. These can then be browsed and purchased by other tenants, contractors or real-estate owners looking for more sustainable products. Larger real-estate owners can access an internal marketplace within the platform and assign materials to other locations within their own building, or wider estate.
“Expanding uptake of reuse requires new methodologies, but the major barrier is access to information. If you can open up a building and see what's inside and then categorise it, you can start the process. Early information is the key to getting things rolling,” says Englund.
The lack of storage for reused materials in the period between a building being torn down and someone making a purchase is a stumbling block for the market. The service may therefore include a “preliminarily purchase” mechanism to allow specifiers to pre-order items installed in buildings slated for demolition ready for when their own project hits site.
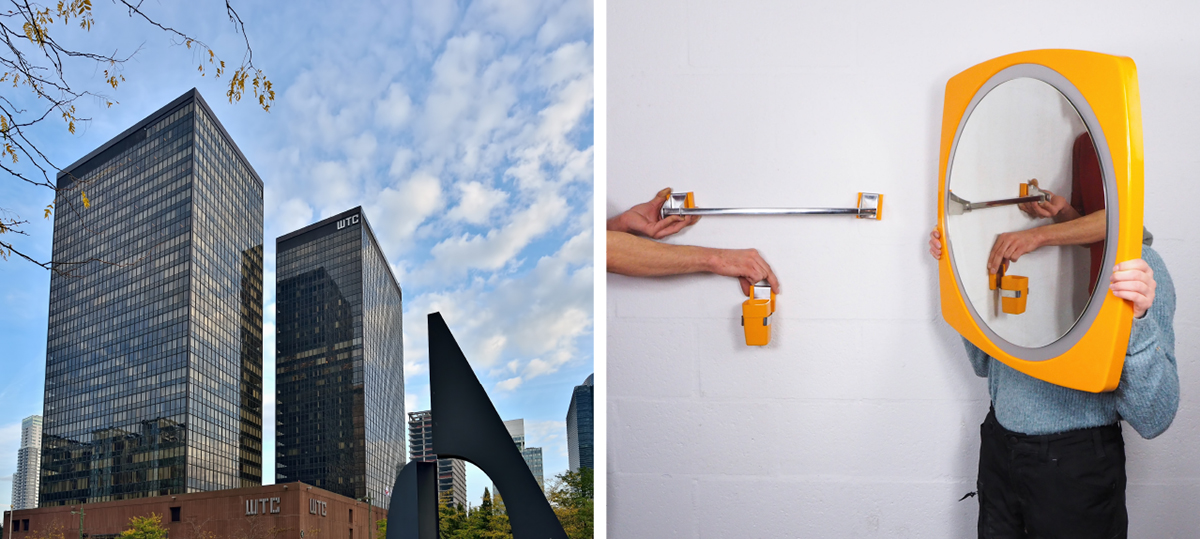
Demand for salvaged materials is strong in Europe and although many reclamation and salvage dealers have experience of reusing building elements, they are largely overlooked by construction, even when projects have circular ambitions.
In an effort to help specifiers tap into this resource, the three-year project NWE Interreg FCRBE (Facilitating the circulation of reclaimed building elements in Northwestern Europe), backed by the European Regional Development Fund, is preparing a directory of some 1,500 suppliers that contribute towards the de-construction/re-construction industry.
The project, led by Belgium-based Rotor Deconstruction (which is currently dismantling large parts of the World Trade Centre of Brussels for resale) aims to boost the amount of reclaimed building elements circulated in the region by 50% by 2032. Other partners include Bellastock, Salvo (a UK organisation active in the promotion of reuse since the 1990s) and the University of Brighton.
Making it official
Various ideas will be tested through 36 pilots on large deconstruction projects, including a pre-demolition audit method, designed to maximise the uptake of reusable elements normally discarded as waste.
Michaël Ghyoot, an architect and Rotor collaborator, says: “There are many reasons why reuse is often overlooked, such as the need for speed on the demolition site, or a lack of knowledge of reuse opportunities. A good way to address this is to conduct more systematic reclamation audits prior to demolition, and our open-source guidelines will help people carry out these inventories.”
A long-term goal is to get public authorities to mandate these inventories before demolition work. Also in development is a handbook that outlines strategies to integrate reuse, specifically in the context of large-scale building projects and public tenders.
Materials reappropriation is tricky when main contractors or clients are unwilling to shoulder the additional risk associated with sourcing and installing unfamiliar products that had a previous life.

Denmark-based architect Lendager Group has responded to scepticism by restructuring its business to function both as demolition contractor and materials manufacturer. The practice has set up several spin-off companies that produce innovative upcycled products, such as windows, recycled wood, brick panels, concrete and textiles to sell into projects.
These combine existing manufacturing techniques with new methods that see waste as a resource. For example, new window frames are fitted with old glazing to create a product that exceeds building standards for thermal performance. A partnership with brewing company Carlsberg uses waste plastic from beer kegs as a new component material for façades and furniture.
“Changing the value chain and engaging with it at different points gives us the disadvantage of suddenly being in competition with other project stakeholders, but it also creates a bridge,” says Anders Lendager, partner and owner of Lendager Group. “If we can open the risk box very early in a project, when doing preliminary designs, we’re already talking about the economy behind materials, where we need to harvest them and the risk implied for the client and the contractor.”
Key to success is ensuring that upcycled materials are cost neutral and at least as durable as regular products, he adds. The firm’s projects are becoming larger and more complex, a 45m high rise planned for Aarhus in Denmark, will be built mostly in mass timber, with solar shading on the facades made from upcycled windmill sails.
“These things are really difficult to scale, even on our projects, but we see an openness towards it and growing interest, which drives us forward” Anders Lendager, Lendager Group
The ‘eBay’ of used materials
As operational emissions in buildings continue to reduce and embodied energy rises up the sustainability agenda, expect more innovative reuse solutions to emerge as the sector pushes to deliver on more stringent targets.
Materials that are not viable for reuse on construction projects could be reappropriated by other businesses, in the process helping developers and constructors meet their ESG goals, boost social impact and even attain points that would contribute to a better environmental rating.
Globechain is a platform similar to eBay – but where all products are free – that connects large corporate companies or multinationals to charities and small businesses keen to reuse and redistribute unneeded items.
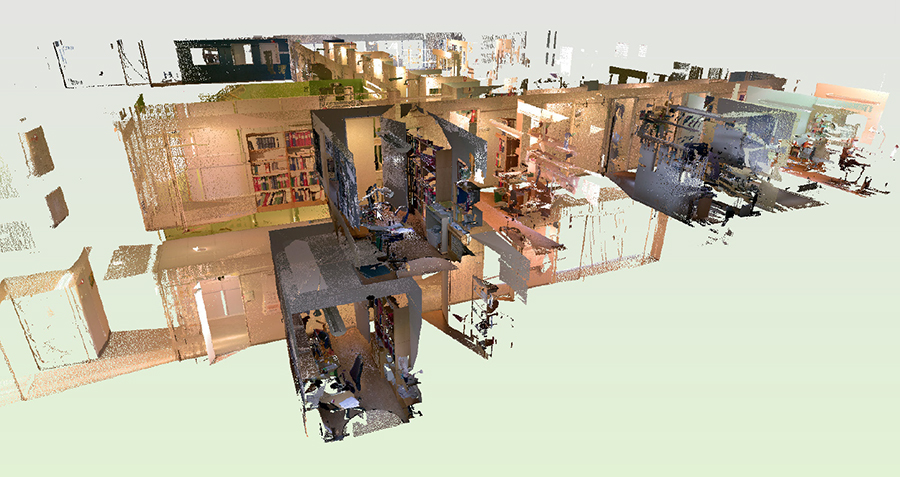
Big contractors such as Mace, Wates and Skanska regularly list on the platform and, to date, the service has diverted some 6m kg from landfill. Clients pay either an annual membership, or a pay-as-you-go fee to list items, and Globechain claims this works out much cheaper than costs associated with skip hire, incineration, landfill tax and so on.
It's normally quick to find a new home for materials, avoiding the need for long-term storage, says May Al-Karooni, CEO and founder of Globechain. “We have a massive network, so most items are requested in less than 24 hours of being listed – one very big restaurant chain doing a refurbishment offloaded its stock in just five minutes.
More and more, contractors are being asked when they tender for projects to prove sustainability in the supply chain, and using Globechain makes them eligible for one point in the BREEAM rating system under either ‘demolition and refurb’ or ‘innovation’, because we're classed as innovative tech.”
Completing the circle
Circular principals are making inroads into the sector, but various challenges remain if materials reuse is to gain widespread acceptance. More needs to be done around the testing and certification of salvaged materials, to ensure they attain similar legal guarantees as new products. Regulations may require a refresh to encourage circular behaviours, in the UK for example, most refurbishment projects still attract 20% VAT, whereas newbuilds pay nothing.
Then there’s the need to override entrenched conservatism in the building sector. “It takes one second to have an idea in construction but 10 years to implement it,” says Lendager. “These things are really difficult to scale, even on our projects, but we see an openness towards it and growing interest, which drives us forward.”
Read From Principles to Practices: Realising the value of circular economy in real estate, a report led by Arup and the Ellen MacArthur Foundation in collaboration with RICS. This article is the first in a series exploring the built environment’s role in advancing the circular economy. The next instalment will focus on how jobs in the sector might evolve to accommodate more circular principles.