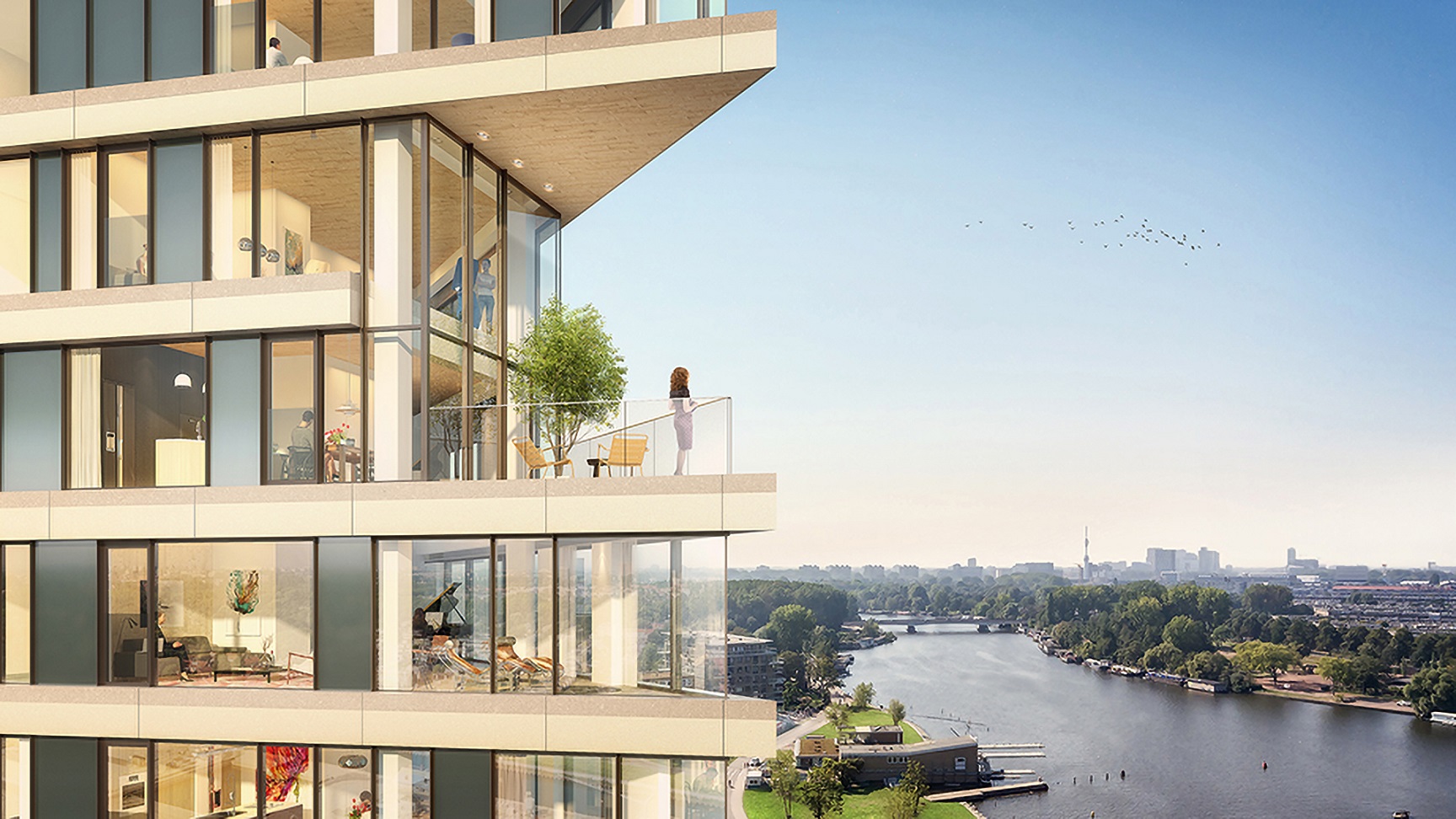
The HAUT building in Amsterdam
The world’s tallest wooden tower, Mjøstårnet stands almost alone overlooking Norway’s largest lake. At 18 floors, it would be a minnow next to the monoliths of global cities, but at Lake Mjøsa, 100km north of Oslo, Mjøstårnet dominates the landscape.
Like London’s The Shard, Mjøstårnet was conceived by an architectural doodle on a napkin. Unlike the Shard, the structure is made of Norwegian spruce, which you might recognise as the tree standing in Trafalgar Square each Christmas – an annual gift from the Norwegian government for British support during the Second World War.
The tower, containing apartments, a hotel and office space, was completed in 2019 and represents the high watermark in a new race to build tall in timber. Unlike the progression of steel towers, where innovation and a desire to increase density unlocked new peaks, this race is driven by the need to cut into the carbon footprint of buildings and construction, currently an eye-watering 39% of total global emissions, according to the United Nations.
Timber “is absolutely, completely the future”, says Ron Bakker, founding partner at London-based PLP Architecture. “It’s our only renewable structural material, and it has no penalty for the environment if we use it correctly. In fact, it’s got a negative carbon count, because every time we use it in construction we capture some carbon and hold onto it.”
Bakker is one of a growing number of timber evangelists seeking to prove not only that wood is kinder to the environment than concrete and steel, but that it is also at least as safe from a fire perspective. Studies also suggest it speeds up the construction process and can even reduce stress levels of a building’s inhabitants.
Critics say the research carried out to date on fire safety is inadequate, and that timber tall buildings are a new typology of construction and should be treated as such. That means building codes drafted for concrete and steel, and before tall timber buildings were even thought possible, shouldn’t apply.
Mass engineered timber
Although wood has been used for the construction of homes for thousands of years, innovation gathered pace in the 1990s with the emergence of mass engineered timber (MET) in Austria. MET is a group of building products that includes glued laminated timber, or glulam, and cross laminated timber, known as CLT. Both are made of layers of wood, which are then bonded with structural adhesives. CLT layers are stacked at perpendicular angles and are predominantly used for walls, floors and ceilings. Glulam boards are made with the grain aligned in the same direction. These are used for columns, beams and truss elements.
“What you end up with is pretty impressive,” says Mark Farmer MRICS, chief executive at real estate and construction consultant Cast. Mass engineered timber enables “bigger spans with beams, which take more load with columns and walls, then you start seeing timber being used in ways we’ve not seen before. It has moved from playing a secondary role, mostly for esthetics, to the primary structural frame.”
At Mjøstårnet, the main load is handled by glulam trusses along the facades, internal columns and beams, according to a 2017 paper by Rune Abrahamsen, chief executive of Moelven, the Norwegian lumber company that manufactured the timber. The CLT walls are used to bear the weight of elevators and staircases. They do not contribute to the building’s horizontal stability.
Glulam trusses handle forces in both horizontal and vertical directions and give the building the necessary stiffness. However, due to the building’s “slender” design, concrete floors had to be added at levels 12 to 18 to ensure the structure was heavier at the top, according to Abrahamsen’s paper. This ensures movement would not compromise comfort for people living in the apartments. This is a common feature in tall timber buildings: the design presents so many challenges that engineers almost always resort to trusty concrete and steel to overcome obstacles.
Indeed, last year when the Council on Tall Buildings and Urban Habitat (CTBUH), the standard-bearer for tall buildings, certified Mjøstårnet as the world’s tallest timber building, it also published a criteria stating that “an ‘all-timber’ structure may include the use of localised non-timber connections between timber elements”. That means “a floor system of concrete planks, or concrete slab on top of timber beams, is still considered a ‘timber’ structure, as the concrete elements are not acting as the primary structure”.
At present, the limits haven’t pushed much beyond 80m, but PLP’s conceptual project, the Oakwood Timber Tower, suggests the technology is there to build as high as 300m. The project would create more than 1,000 flats in a 1m ft2 (93,000 m2) mixed-use tower in central London. Computer-generated images show the building from the south bank of the River Thames, soaring over London’s skyline, its wooden braced structure at odds with the pale stone of St Paul’s Cathedral.
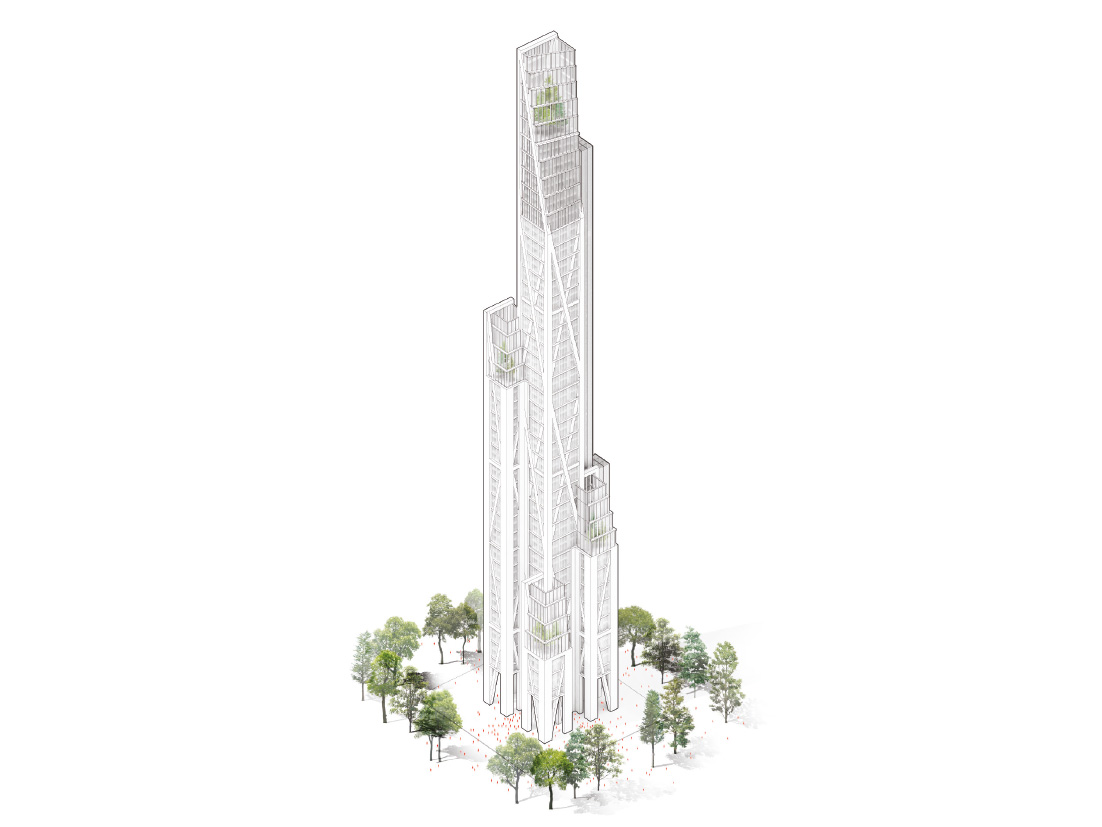
That braced structure with diagonal columns is intended to transfer the force of the wind down into the foundations. The wooden columns at the base of the building are an enormous 2.5m x 2.5m. More common steel columns in the same location would be around 1m squared.
Some movement at the top of all tall buildings is common. The tops of towers can sway in the wind by as much as 2m, but usually it’s almost undetectable by humans, although Bakker says you would notice unnerving waves in a full bathtub. However, there’s enough g-force in timber tall towers to compromise comfort. “Timber is so light that its movement is different. It has much less inertia than concrete or steel, so it behaves a little bit like a whip,” says Bakker. “It’s common to add weight at the tops of towers in the form of swimming pools, roof gardens or steel plates in a couple of floors.”
Part of the mix
For Thijs Croon, project developer at Amsterdam-based Lingotto, it was the technical challenges of building a 73m timber tower on a waterfront site in an asymmetrical shape with foundations 30m deep that made him relinquish plans to build purely in timber and opt for a concrete core.
“It’s a bit more concrete than we initially wanted, but we’re happy, we’re not ashamed of that,” he says. “All wooden buildings tend to be hybrids, but the more wood you use, the less concrete, steel and stone you use. That’s the CO2 story.”
Croon had been inspired to use timber after a visit to the Believe in Better building on Sky’s campus in Osterley, west London, which upon completion in 2014 was the tallest commercial timber structure in the UK. “Once you visit a building like that you reach out to touch the columns, you touch the walls,” says Croon. “In a concrete building that’s not what you do. You don’t want to touch and hug it.”
The feeling Croon describes is borne out by research. A 2010 study by researchers at the University of British Columbia established a link between wood and wellbeing. The presence of visual wood surfaces in a room lowered sympathetic nervous system activation, which is responsible for physiological stress responses in humans.
Although the environmental and wellbeing advantages of timber appear inarguable, its use will always be curtailed if concerns over fire cannot be addressed. The 2017 Grenfell Tower fire caused 72 deaths and 70 injuries and put the spotlight on the construction industry’s use of combustible materials in residential buildings.
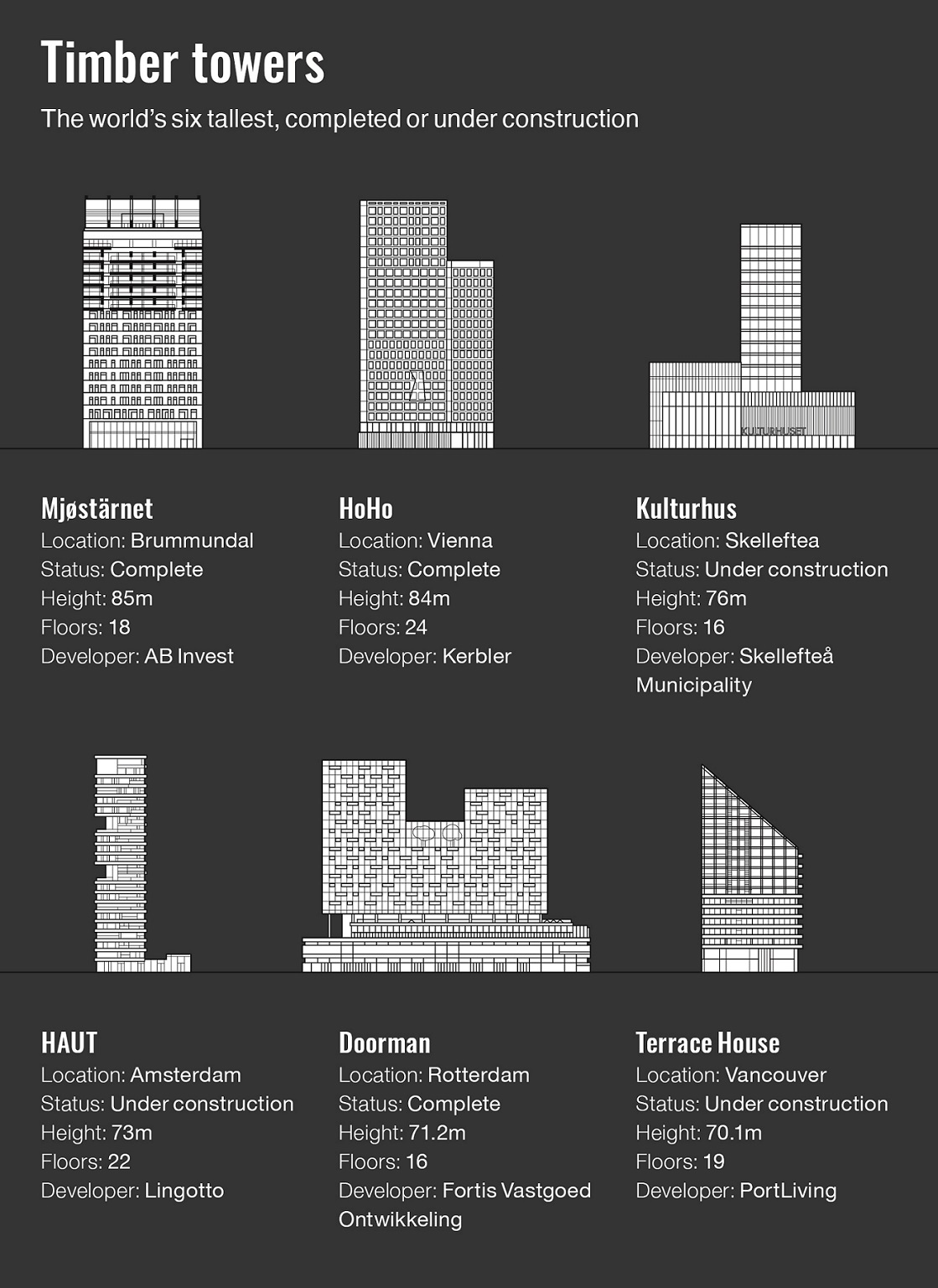
The government launched an independent Review of Building Regulations and Fire Safety, led by Dame Judith Hackitt, and a raft of consultations on regulatory changes followed, one of which included a ban on the use of combustible materials on the external walls of habitable buildings over 18m high.
Then in June 2019, terrifying footage from local residents showed fire sweeping across a block of flats in Barking, east London. Following the fire, safety inspections unearthed from the previous January had singled out the building’s wooden balconies as posing a “significant hazard”, according to BBC news reports, adding to public scrutiny of timber as a building material.
Key to unlocking MET as a structural building material has been its fire resistant properties. Timber is a charring material. Research states that thick sections such as beams, without other heat sources, will extinguish themselves, leaving the inner sections relatively undamaged and intact.
That includes the glulam beams at Mjøstårnet. Even Andersen, fire consultant with Sweco Norge, the company responsible for fire safety in the building, said in 2018 that even after long exposure to fire the tower “will have a sufficiently great load-bearing core of fresh wood”.
In fact, among all the design challenges presented by tall timber buildings, fire “is probably one of the easier ones”, says PLP’s Bakker. But how tall timber performs in a real scenario, including whether burnout occurs, remains too little explored, according to a March paper by Edinburgh University school of engineering professors Angus Law and Rory Haddon.
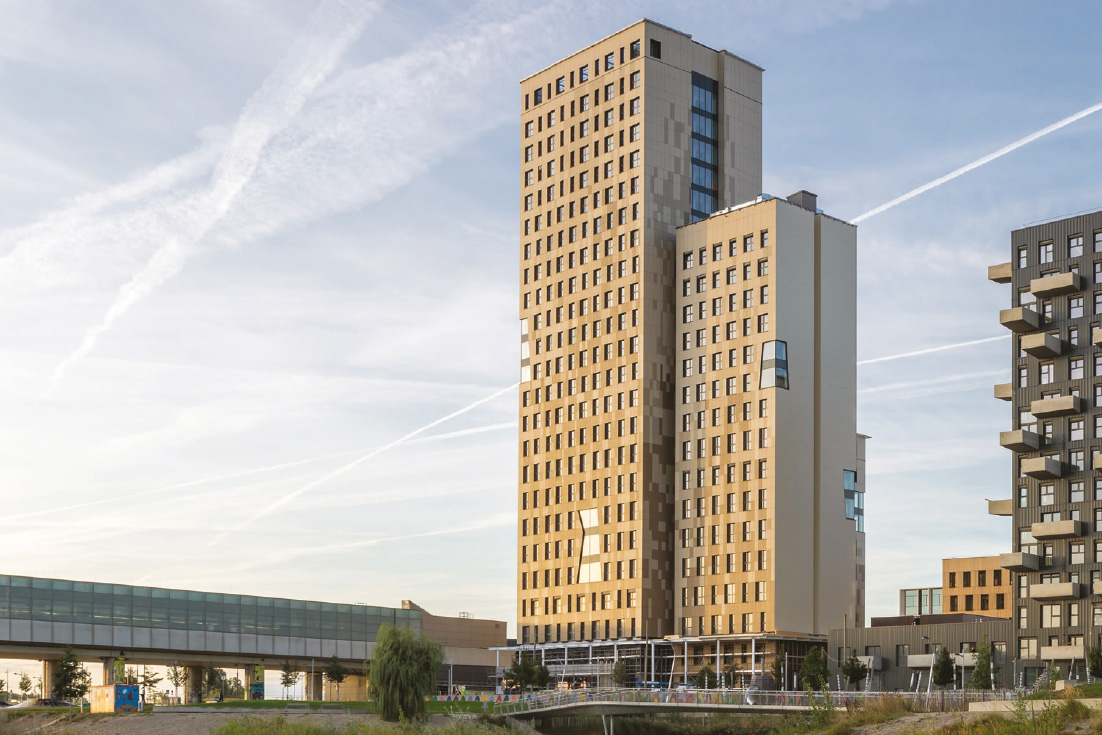
High-level scrutiny
Tall timber buildings is a new typology of construction that doesn’t have the same underpinning knowledge and, as a result, must be given a higher level of interrogation than we’ve previously seen, says Luke Bisby, chair of fire and structures at the University of Edinburgh’s school of engineering, and a colleague of Law and Haddon.“Most structural engineers do not have the proper understanding of fire dynamics, so their only option if asked to design one of these is to couch designs within the existing framework that they’ve always used,” he says. “The problem is, unlike more common building materials, timber burns.”
To ensure timber buildings are safe, says Bisby, engineers and architects have a choice. First, they can use established methods to ensure the structure doesn’t burn, which includes encapsulating the timber in fire-resistant materials and other techniques. This demands a “level of care that goes above and beyond what is considered typical in the construction industry… making timber buildings less attractive economically.” The other option is to account for the burning wood and properly understand whether or not a fire will burn out, and if it will, how long that will take, he says. To fully understand that, more research is necessary. “If your entire structure is exposed timber then we don’t have the underpinning knowledge yet to provide assurance that that fire is going to go out,” says Bisby. “That’s why structural engineers by and large can’t be given the authority to make these decisions.”
An attempt to standardise fire safety guidance by a coalition of global construction industry bodies that includes RICS may go some way to alleviating uncertainties. The International Fire Safety Standard, to be launched at the UN in October, will attempt to abolish “inconsistent approaches to the assessment and regulation of fire safety” that can lead to loss of confidence by governments, investors and the public or, in extreme cases, the loss of life, says RICS Global Building Standards Director Gary Strong FRICS.
For now, progress in tall timber construction is likely to be led by countries in mainland Europe or North America. It could be Sweden, where ministers are eager to utilise crop forests that are underused as a result of the declining use of paper. It could be the Netherlands, where local governments are pushing developers to do more for the environment, or it could be France, which, from 2022 will require public buildings to be made of at least 50% timber.
“I think we’ll see use of wood for two, three, four-storey buildings really balloon in the next 10 years,” says Bakker. “There’s real momentum gathering in terms of sustainability and a enerational shift where young people are not just interested in sustainability, but they are expecting it.”