The performance of the roof is essential for any building. However, sometimes the ‘fifth wall’ is overlooked despite its importance to the overall structure and its job of keeping the worst of the weather at bay.
“When you look at any detached building, you tend to look at the four walls, you don’t look at the fifth façade – the roof,” says Chris Lee, single ply product manager for roofing manufacturer, Bauder. “It’s the one part nobody ever sees.”
Until it becomes a necessity.
This can be due to the age of the roof, that it’s in need of surveying because of a change in ownership, the owner may want to improve the building’s thermal performance, or to upgrade the roof by installing solar photovoltaic panels for renewable energy.
However, attention is often paid to the roof because of water-related problems. “The consequence of a poorly designed roof can be condensation. And in the case of metal roofs, corrosion,” says Lee.
“It is not uncommon for condensation to be confused with a leaking roof, and the reality is that older installations may well have little or no insulation and almost certainly less than the current building regulations require.”
In these instances, the existing metal roof will need either to be repaired or upgraded. So, what are the surveyors’ main challenges to deliver a lightweight and cost-effective solution on this type of refurbishment project that also thermally upgrades the building? Initially, work starts with establishing the kind of metal roof involved, with most broken down to three types:
- Fully supported
- Built up metal roofs/standing seams
- Composite panels
Condensation risk analysis
To make sure the overlay is specified correctly, a condensation risk analysis test is carried out early in the design stage so that the dew point is not compromised by the overlaid system. This indicates what level of thermal upgrade might be needed before a specification can be produced and a budget price provided.
The correct type of fasteners must be specified according to the existing metal roof finish, with a wind load calculation carried out to ensure the right frequency of fasteners are used.
It starts with a ‘pull out’ test early in the process, says Lee, “as feasibility for the overlay needs to be established”. Bauder works with several fastener partners, who use specialist tooling to pierce the top layer of the metal roof, screw into it and then ascertain the pull out and pull through values.
“This allows us to determine the strength of the existing structure and is also an opportunity to take dimensions of the existing metal roof,” says Lee. That helps to understand what the existing assembly is – whether it’s composite panel/built up system or fully supported.
“If the existing metal roof is too corroded or fatigued then it may be that an overlay is simply not possible; by carrying out a survey at an early stage we can identify areas that may otherwise not have been considered. For example, how thick is the existing metal? Is it aluminium, or steel? This will have a big influence over the type of specification we can put together,” says Lee.
“We need to determine what is causing the issues; whether it is moisture build up from condensation, water ingress due to failing waterproofing, or in some cases a combination of both. It is essential that all investigations are carried out in advance to ensure the correct specification is produced.”
Bauder’s Profiled PIR Infill Overlay System is mainly for refurbishing profiled sheet metal roofs or increasing their thermal performance. In the latter example, it can bring the construction up to current building regulation requirements.
PIR insulation infill boards are cut on site to match the existing sheets and can support an additional layer of BauderPIR FA Flatboard Insulation. “It’s lightweight, and the structure won’t have more demands put on it,” says Lee.
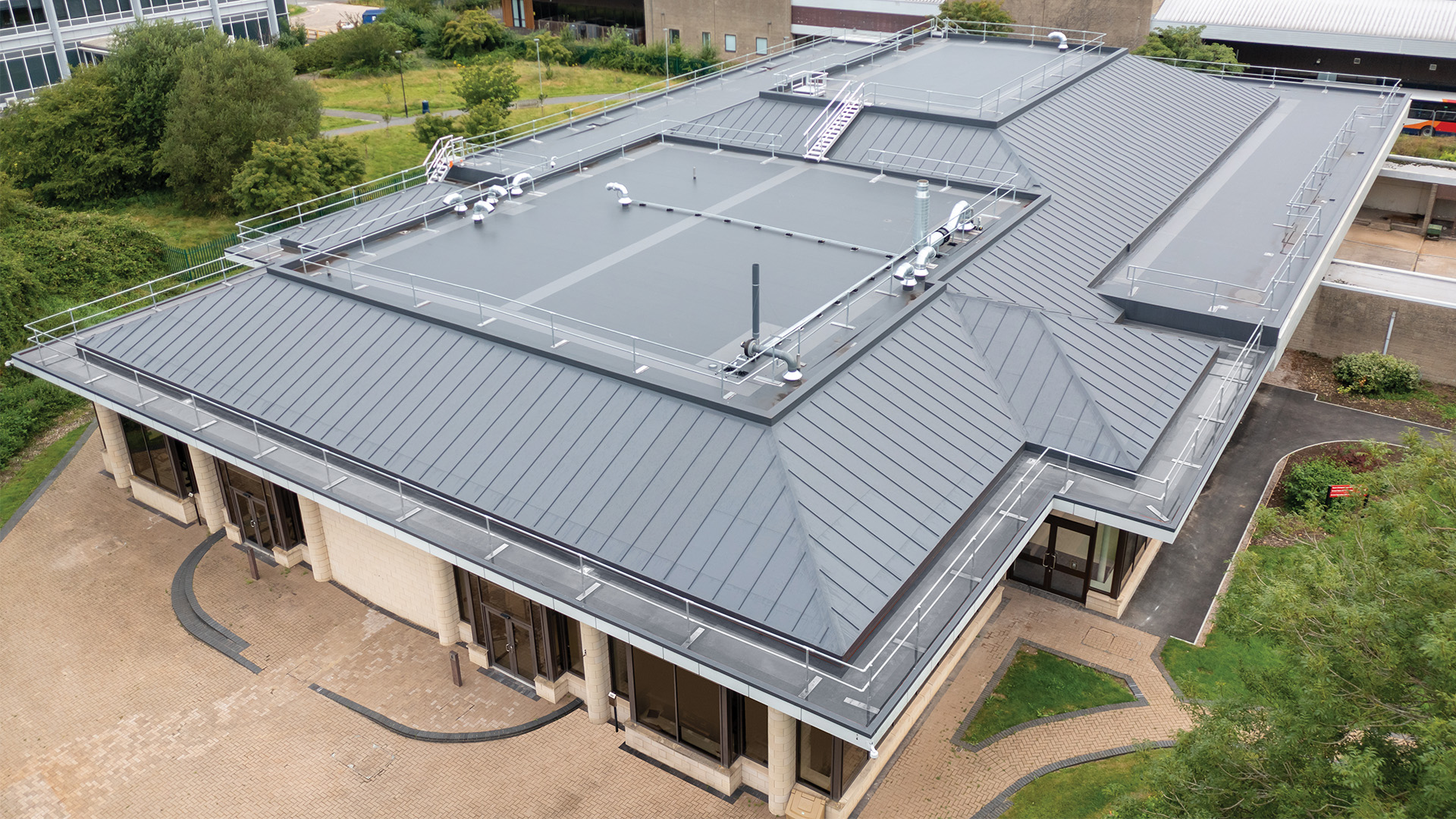
University of the West of England
"The consequence of a poorly designed roof can be condensation. And in the case of metal roofs, corrosion" Chris Lee, Bauder
Working at height
When starting any job, the first thing Lee says to all his colleagues is ‘safety, first and foremost.’ “You are working from height, which is a risk, and roofs can be fragile, sometimes self-supporting. The other factor is the condition of existing rooflights.”
Years of accumulative dirt and UV damage means many may be clogged, with restricted light. However, this is a chance to either replace or remove the rooflights as simply overlaying them with the Profiled PIR Infill system is not an option.
Of course, developers and landlords could over-clad a metal roof with another metal roof, says Lee, “but if condensation is a root cause of your problem, it just pushes it down the road.”
He adds: “You can use a liquid overlay, which is not uncommon as a temporary measure … but this can be expensive to put on top of a metal roof and you are not upgrading the insulation.
“With our system, you get an upgrade of insulation and single ply as a lightweight single layer membrane solution. From a cost perspective, it’s competitive, plus you get better thermal performance.
“In essence we are providing a new waterproofing solution to a failing metal roof that will last at least 35 years, that will improve the building’s thermal performance and will do so while minimising disruption to the internal workings.
Ultimately, says Lee, we need to remove the opportunity for condensation and water ingress so the fifth façade is one they don’t have to think about for a long time.
Case study: University of the West of England
When the University of West of England’s (UWE) W Block became dated and the existing single ply waterproofing and composite panels were aged and failing, the university embarked on a full refurbishment to transition the building into a modern faculty centre for fine print research.
Bauder Thermofol single ply system was chosen to overlay the existing single ply and pitched composite panels due to its lightweight properties and versatility. This membrane can successfully join the existing single ply and metal composite panel areas together to form one continuous roof covering inclusive of a thermal upgrade.
It was important to maintain the look of the old roof. “There are flat roof areas combined with the metal roof where we completed the work, simulating the appearance of the previous roof,” says Chris Lee, single ply product manager at Bauder, adding this was achieved by using anthracite colour membrane and decorative profiles.
UWE is, says Lee, a good example of Bauder recreating what was there before, “but it will have a more modern appearance because of the decorative profile.” The other real benefit, says Lee, is that the way Bauder works reduces the impact on those using the building below: the university has over 30,000 students and 3,000 staff.
“Unnecessary noise during refurbishment is kept to a minimum as we’re not removing any of the existing roof element – it gets continually waterproofed as we go across,” says Lee. This means it shouldn’t disrupt the internal workings of the building and those below should be able to continue as normal throughout the refurbishment.
Despite the challenges of working in mid-winter, the project was an overwhelming success, as demonstrated by it being shortlisted by the Single Ply Roofing Association (SPRA) for Best Refurbishment 2021 and Best Sustainability 2021 awards.