A bungalow retrofitted to the PAS 2035 standard © Baily Garner
Given recent news coverage of mould and damp in UK homes, it is worth reiterating the importance of airtightness to the ventilation strategy for any given building, to keep dwellings moisture free, as well as its role in retrofit to ensure occupant comfort and conserve energy.
Airtightness is the resistance of the building envelope to infiltration when ventilators are closed. The greater the airtightness at a given pressure difference between the inside and outside environments, the lower the infiltration. There is a standardised way of testing this, which is governed by the Air Tightness Testing & Measurement Association (ATTMA).
ATTMA was set up to promote technical excellence and commercial effectiveness in testing, and to stop individuals or companies claiming to be testers when they are not adequately trained in the use of the equipment or sufficiently able to interpret results.
Testing process depends on scale
Testing is carried out by ensuring air pressure in the property is a consistent 50Pa. The rate at which pressure changes is then measured over a period of time to understand how airtight it is, in cubic metres of air lost per hour for each square metre of the building envelope (m3/(h.m2)).
This process is generally carried out by means of a blower door, a large fan placed in the main entrance doorway. All ventilation points – passive vents, windows, and fans – are sealed, and the pressure within the property is then measured to gauge how much air is lost from the building.
More recently, the need to undertake such testing at scale has seen the emergence of pulse testing, as part of a process outlined in PAS 2035:2019.
The scale of testing required can be seen, for instance, in the number of projects covered by the Social Housing Decarbonisation Fund, which alone totals around 50,000 dwellings.
Pulse testing can be set up more speedily than blower doors, using a machine placed in a central location that sends a periodic air pulse to maintain a much lower pressure of 4Pa. Software then converts this value to something comparable to the blower door test.
Both approaches are recognised by ATTMA. However, air testers tend to regard blower door tests as slightly more accurate. A pulse test may also not cover a large property, so two machines would be needed.
Retrofit professionals at my firm, Baily Garner, have – after some experience – decided to use blower door tests to establish strong archetype design for individual properties in a street or estate, and pulse testing for large-scale assessment, given the lower cost of this approach.
Regulation and guidance tighten requirements
The 2021 edition of the Conservation of Fuel and Power: Approved Document L sets the minimum airtightness requirement for a new-build property at 8m3/(h.m2) at 50Pa; it had been 10m3/(h.m2) as 50Pa under the previous version of the document.
When calculating energy performance certificate (EPC) ratings using the standard assessment procedure (SAP), the software RdSAP assumes an airtightness of 15m3/(h.m2) at 50Pa, with the option to input a value if known.
Meanwhile, PAS 2035:2019 states that: 'When the insulation and airtightness of the building fabric are improved, adequate ventilation should be maintained.'
This is because the more airtight a building is, the less natural ventilation it receives. Enabling a building to breathe naturally is considered incredibly important.
Airtightness, however, represents a good compromise between breathability and heat loss as ventilation and space heating are both easier to control with greater airtightness.
They mean the building gets the ventilation that the fabric requires to prevent the build-up of condensation. Ultimately, less heat is lost through uncontrolled ventilation, resulting in reduced energy consumption and saving carbon.
'Ventilation and space heating heat are both easier to control with greater airtightness'
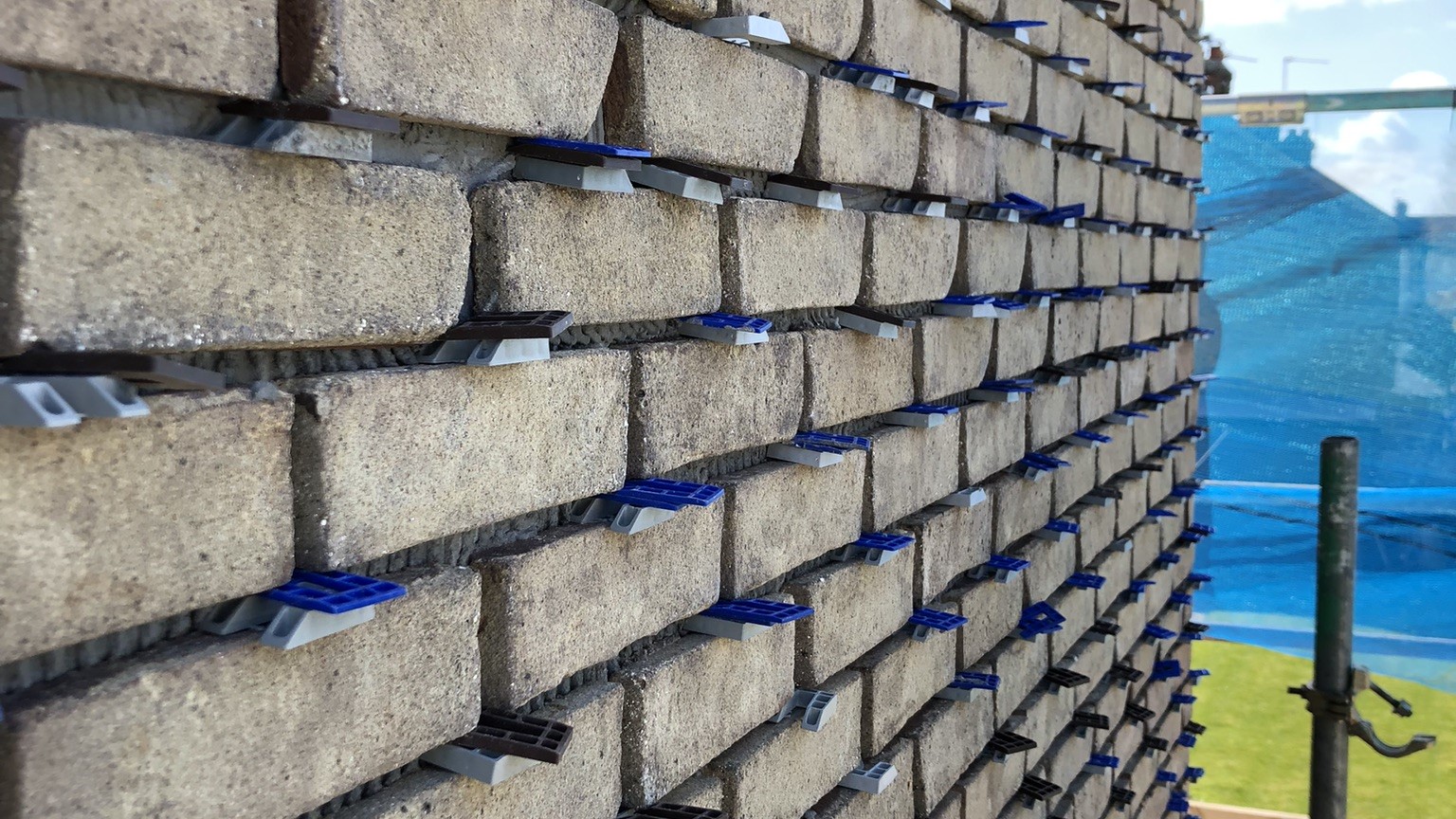
Brick slip setting out on an externally insulated end of terrace house subject to a full retrofit © Baily Garner
What to assess and when
In terms of airtightness, wet-masonry build – that is bricks or blocks with mortar or render – generally performs better than non-traditional build systems such as Orlit, Cornish, No-Fines or Unity.
Pre-war properties often feature a suspended timber floor and a fireplace that needs to be ventilated, and accordingly are not particularly airtight. More modern buildings are often built with a minimum standard of airtightness in mind, such as that under Part L.
PAS 2035:2019 makes provision for testing before, during or after installation of the energy efficiency measures specified by the designer. Such testing assesses the accuracy of the design and emphasises the importance of the ventilation system.
The standard also recommends that testing is best undertaken as part of the initial assessment work, to understand the physical limitations of the building before specifying improvement measures.
As part of such testing, an experienced operative is often able to provide an idea of areas where air is escaping, due to their understanding of the main leakage points in different types of property, by using a smoke pen. Alongside thermographic or infrared images, such understanding can help target areas for specification.
A mid-works air test is also recommended by PAS 2035:2019 to ensure the target set is achievable. This provides a relatively inexpensive reassurance that, following the installation of fabric measures such as insulation, other measures such as ventilation systems will complement the ventilation strategy.
Modelling and mitigation help maintain comfort
Many whole-house ventilation systems, such as mechanical ventilation with heat recovery, require a specific airtightness level to ensure efficiency. Similarly, individual intermittent extract ventilation systems are unlikely to work efficiently in a very airtight property.
Airtightness can also affect an SAP score – by anywhere up to 15% – and potentially have an impact on the EPC rating as well.
Furthermore, changing the airtightness and ventilation of a property creates a condensation risk. As well as following guidance and Approved Documents F and L, we therefore recommend modelling thermal bridging, which shows the potential condensation risk from retrofitting and can thus inform the mitigation strategy.
However, thermal comfort is an equally important consideration: a draughty or less airtight building means uncontrolled heat loss. Mitigating this, through airtightness and a suitable ventilation strategy, will enable occupants' comfort and help keep energy spend as low as possible.
'Changing the airtightness and ventilation of the property creates a condensation risk'
Holistic thinking will enable compliance
As a rule, whenever measures are installed to the building fabric, airtightness is affected. These may include:
- draughtproofing
- filling penetrations for pipes, wires, redundant holes or uncontrolled passive vents
- controlled ventilation, such as trickle vents or closing intermittent extract ventilation systems
- new windows and doors
- floor, wall or loft insulation
- specialist airtightness paint.
Where there are other standards than PAS 2035:2019, such as EnerPHit, there will be a compliance issue associated with airtightness. Apart from Approved Document L, applicable to new fabric elements and new-build dwellings, or other very specific standards, such as Energiesprong or EnerPHit, there are no dedicated criteria for airtightness.
Any retrofit or refurbishment will affect the whole installation, as the resultant airtightness will have an impact on heat loss, SAP score, energy use and – by association – the intended outcomes of the project.
For a dwelling to achieve net zero by 2050, it is the sum of the retrofit that must be compliant, rather than the individual items themselves. Understanding and testing airtightness helps to achieve this.
Ben Nixon MRICS is a partner at Baily Garner
Contact Ben: Email
Related competencies include: Building pathology, Construction technology and environmental services, Design and specification, Legal/regulatory compliance