An example of toughened glass fracture due to nickel sulphite inclusions © TFT
As discussed in my previous article, a number of materials are the cause of significant defects commonly identified in technical due diligence (TDD) building surveys.
Although some modern and current materials – such as toughened glass and magnesium oxide (MgO) boards – can be widely used they can still cause issues in relatively modern settings. Meanwhile, asbestos remains a problem, particularly as the construction industry continues to come across it while refurbishing existing building stock.
Toughened glass presents shatter risk
The use of toughened glass is widespread because it is long-lasting and durable. It is frequently used where safety glass is required, for example at low level where it could be impacted.
The wide range of types vary according to location, purpose, aesthetics, cost, health and safety, and sustainability. The toughened glass is heated in an oven during manufacture to strengthen it. This means that if it does break in use it forms dice-like fragments that are sufficiently small to avoid causing injury.
Nevertheless, it can be classed as problematic because it can spontaneously shatter due to the presence of nickel sulphide (NiS). While NiS occurs in all heated glass, the effects are more pronounced in toughened varieties because of the temperature extremes during manufacture and resulting chemical reactions.
When undertaking a TDD inspection, therefore, we as building surveyors should review not only whether toughened glass is present but confirm its age, location and whether it is in the inner or outer pane of an insulated unit.
We must also consider the following specific points.
-
Toughened glass does not tend to break spontaneously within a year of manufacture, but breakages peak between four and six years. The likelihood then falls, in particular after ten years. However, some breakages have been known to occur more than 20 years after manufacture.
-
The likelihood of failure can be significantly reduced by heat soak testing (HST), using elevated temperatures to stimulate the transformation of crystals that cause fracture. This process identifies around 90% of glass that would fail. However, HST is not without issues – for example, inadequate calibration of heat soak ovens – so it does not shatter the predicted percentage of glass panes containing NiS. Furthermore, while HST is routine for high-profile projects, glass does not tend to be tested on low-rise or lower-value properties. Note that where glass is tested there should be a kitemark and HST confirmation, but this is not always the case.
-
Toughened glass may be used at height in the outer pane of insulated glass or in single-pane glass, but must be subject to a risk assessment in accordance with Centre for Window and Cladding Technology (CWCT). As part of a zero-risk approach, facade consultants and designers now typically advise against the use of toughened glass at height, where there is still a risk it may fall on to building users or pedestrians below. In these locations – for example in high-level atrium glazing or balcony glazing – the use of laminated glass or laminated toughened glass combinations is considered best practice.
'Toughened glass is frequently used where safety glass is required, for example at low level where it could be impacted'
Asbestos may pose bigger threat than ever
The use of blue and brown asbestos by the UK construction industry was banned in 1985, and white asbestos was subsequently banned in 1999. However, exposure to asbestos and the associated health problems – the substance being carcinogenic and causing serious lung diseases – remains a significant risk even today. With refurbishments increasing in frequency, for example as part of efforts to improve building energy performance, the dangers are arguably greater than ever before.
While Health and Safety Executive (HSE) guidance has been to actively discourage the unnecessary removal of sound asbestos material, MPs have recently called for asbestos to be removed from all commercial and public buildings within 40 years.
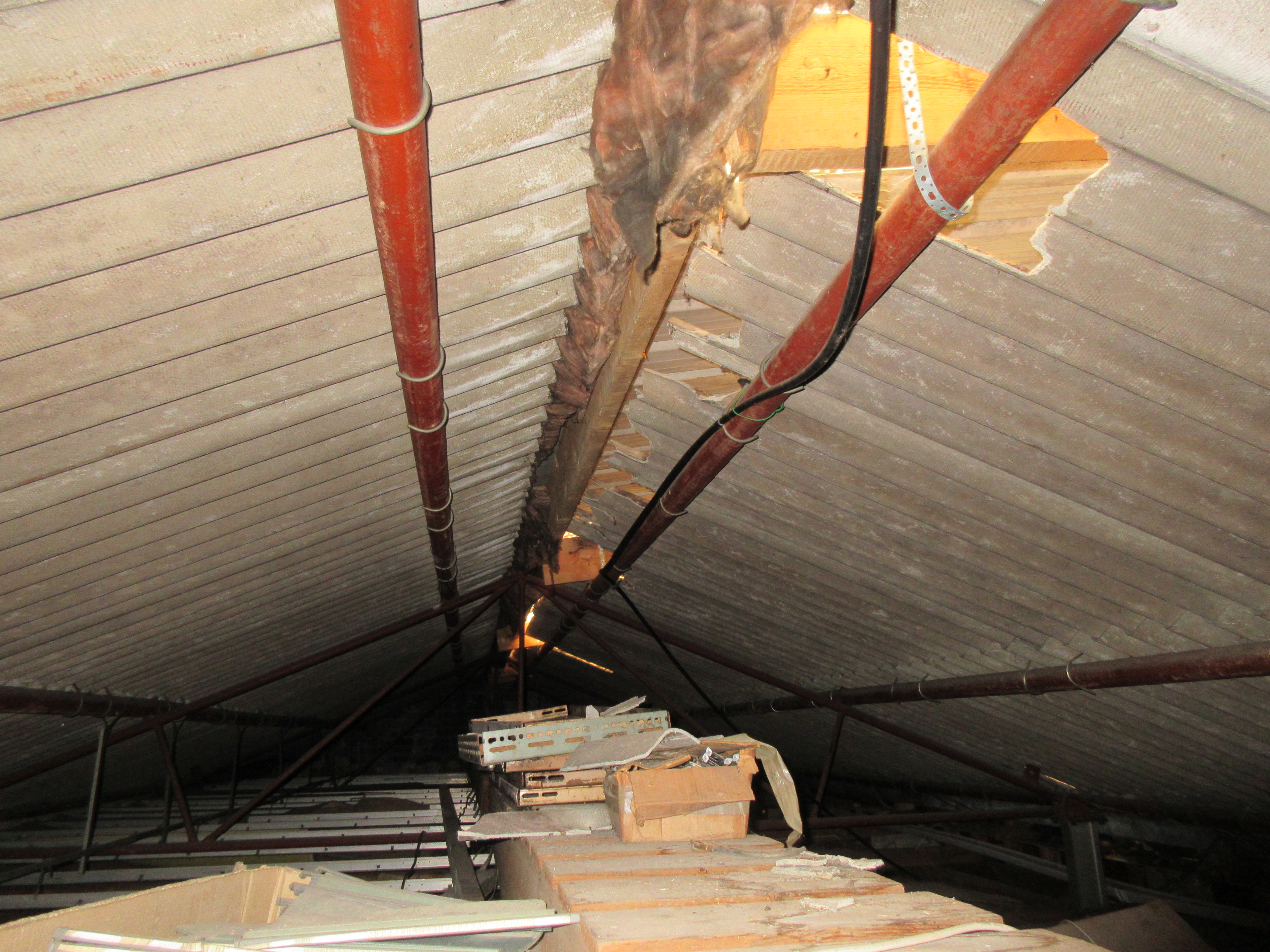
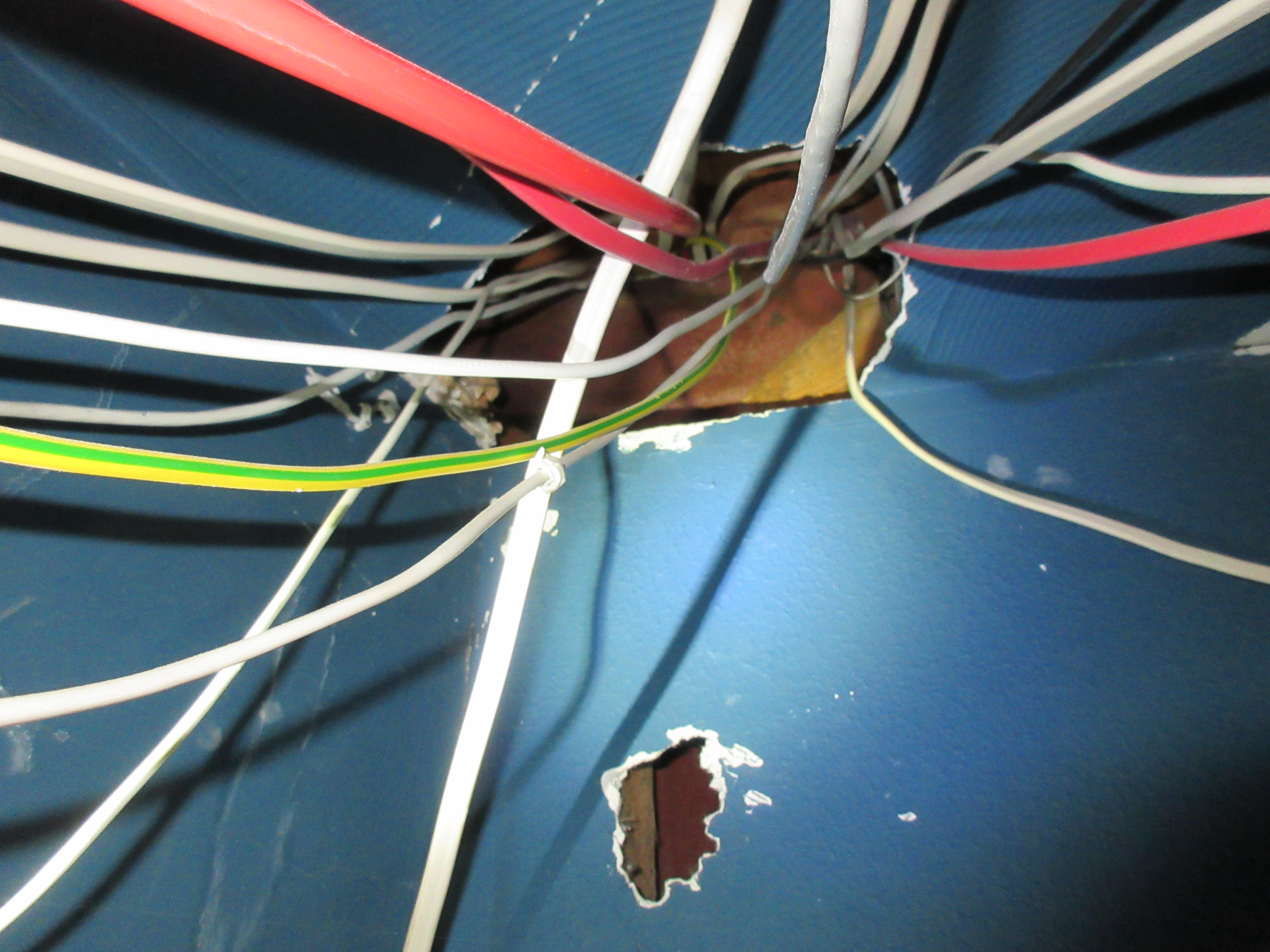
The HSE estimates that as many as 300,000 non-domestic buildings and many more homes may still contain asbestos, while in 2019 some 5,000 fatalities were recorded for asbestos-related work deaths.
As part of TDD inspections, we must review the following.
-
Asbestos-related information, such as asbestos management plans, should be scrutinised before we inspect. As surveyors, we are at greater risk than most building users as we will be inspecting spaces not normally accessed by the general occupier, such as plant rooms, risers and ceiling voids.
-
When reviewing and reporting on the presence of asbestos, we must be cognisant of the types of report available; for example, whether it is a management survey or a more thorough refurbishment and demolition survey. We also need to know whether all areas are included in the scope of the survey and, if asbestos is present, whether there is evidence that it is being regularly checked and properly maintained.
-
If asbestos has been removed, is there evidence to demonstrate that this has been done comprehensively. Are air test certificates available to confirm the spaces affected are now safe to access?
-
Even if comprehensive information is available, the inspection still matters. We cannot ignore what we see on site, and we must use our own professional judgement when inspecting. If, contrary to available reports, asbestos-containing materials are present or are damaged, concerns must be raised and further investigations undertaken. I have heard of a claim that a surveying firm fell short in its services to a client by relying on available reports contrary to evidence of damaged asbestos noted on site.
We are still inspecting properties with significant amounts of asbestos-containing materials. These are often concealed and difficult to quantify accurately by a building survey alone.
By way of warning, there are extreme examples of asbestos removal costing significantly more than initial estimates. This includes the well-publicised redevelopment of Battersea Power Station, where a removal estimated at £190,000 actually cost £44m.
Magnesium oxide prone to moisture collection
MgO boarding has become more popular over the past 20 years, particularly since 2017 in the wake of the Grenfell Tower fire, because it is non-combustible. It is also relatively lightweight and easy to cut.
Typically, MgO boards are used as sheathing in framed and panelised building systems. They can also form backing for brick slips or render, as well as being used internally.
The issue with the end product, sometimes referred to as magnesium oxychloride, is that it contains variable amounts of chloride salts and free ions that are often hygroscopic, meaning they can absorb moisture from atmospheric water vapour. As such, in locations with high-level prolonged humidity, moisture collects in the pores of the MgO boards and weeps out, forming teardrops. Such issues with MgO boards have been reported in Australia, Denmark and Canada, as well as the UK.
At TFT, we inspected a block of flats on the south west coast of the UK in 2021, where MgO boards had been used during construction for temporary protection of the timber frame and retained as sheathing. The presence of an internal vapour layer – located on the back of the board which is fixed to the structure – potentially exacerbated the problem of wind-driven moisture in this exposed location by trapping moist air and airborne chloride salts.
Water ingress was initially reported by the building owner, and following intrusive investigations we discovered droplets to the inside face of the boards that were drenching the timber frame and internal plasterboard and floor finishes. The presence of chloride ions can also corrode certain metals such as steel in facade fixings. Following the inspection, TFT continues to be involved with the necessary remedial works.
In 2017, the Magnesium Oxide Building Board Trade Association (MOBBTA) was established to ensure the consistency of boards. The association published PAS 670: 2021, a standard for the continued use of MgO boards, last year.
However, the National House Building Council (NHBC) still states that MgO boards are not covered by its warranty. The CWCT therefore recommends a thorough due diligence process for specifiers, which includes:
-
checking the view of warranty providers such as the NHBC and Local Authority Building Council
-
identifying the source of a particular product
-
consulting a materials specialist
-
carrying out random sampling of boards to ensure that their content is consistent.
MgO boards are often incorporated into building facades, meaning that these would have to be demolished and reconstructed to remove them. Ventilation to the cavity and even coating of boards are possible alternatives. However, the only certain solution as recommended by CWCT is the full replacement of MgO boards – obviously an extremely disruptive and costly exercise.
Even if boards are removed there could be further issues with prolonged damp; for example, contamination of the timber frame with hygroscopic chloride ions. Should this have occurred, decontamination works will be required. In the case of the coastal block of flats, our ongoing investigations are assessing the full extent of remedial works required.
Materials variety demands breadth of knowledge
Only a small selection of defects are covered in this and the previous article, but I hope they illustrate the variety and complexity of potentially problematic building systems and materials.
They also demonstrate the breadth of knowledge required when undertaking TDD surveys and the importance of informed advice – specifically the positive impact we as building surveyors can have for our clients by properly identifying and assessing the risk associated with defects.