Supplementary steel joists below Frazzi floor © TFT
An important consideration when undertaking technical due diligence (TDD) surveys on existing properties is the presence of materials, products or fixing methods that are generally no longer considered suitable for use in new builds.
In recent years, issues have arisen with the use of these features, which have been commonly identified during TDD. Potentially, they can require major remedial works, or even present significant health and safety concerns.
Frazzi floors at risk of water ingress
One such feature is the Frazzi floor, a proprietary system of steel filler joists cast in coke-breeze concrete. Hollow clay pots act as permanent formwork, and clay cover pieces are fitted to protect the bottom flange of the joists.
Introduced in the 1890s the floor type was used in construction until the end of the First World War, and possibly – according to one source – as late as the 1950s. The main concern with this system is that, in moist conditions, coke breeze deteriorates and forms sulphuric acid, which can damage the embedded steel.
In 2021, TFT was instructed to survey a large grade II listed hotel in the West End of London, which had been constructed in the early 1900s and had Frazzi floors throughout. Water ingress had been ongoing for a long period through asphalt-covered flat roofs, from bathrooms and kitchens apparently lacking waterproofing, and through the basement perimeter walls.
The latter were typically lined with a perimeter drainage system, and so presumably some water ingress had been anticipated and addressed during the original construction. However, this had become worse over time, with several floods having taken place.
The water ingress had corroded the embedded steel, which had ultimately cracked, and some ceilings in bedrooms and the back-of-house area had partially collapsed.
The careless fixing of mechanical and electrical services to soffits had also caused widespread damage to clay pots, and there was extensive damage to the flange cover pieces that meant the steel joists lacked fire protection.
Destructive, intrusive investigations were required to assess the condition of the upper steel flanges in the coke-breeze concrete accurately – though in this case, deterioration of the lower flange and concrete soffit already provided a clear indication.
The defects were the result of the way responsibility for the building had been allocated. The hotel was not the owner of the long leasehold on the building, and thus not liable for repair to the floor structure. The head lessee had therefore undertaken numerous repairs, including the introduction of fire-rated board and intumescent paint coatings to the steel, where protective clay pieces had been damaged. It had also supplemented the structure by inserting new steel joists below, where structural inadequacies were identified.
Further intrusive investigations were therefore necessary, to be undertaken by the separate professional team managing the project works to follow up the findings of the TFT survey, as recommended by the hotel's appointed structural engineers.
Although Frazzi floors are not problematic if well maintained, this example does highlight that where there is water ingress and alterations are made without proper care, significant issues can arise. That said, the floors of the hotel had provided more than 100 years of reliable service and were still going.
'The main concern with this system is that, in moist conditions, coke breeze deteriorates and forms sulphuric acid, which can damage the embedded steel'
Understanding and assessing RAAC risks
Reinforced autoclaved aerated concrete (RAAC) floors are another source of concern, highlighted by the Standing Committee on Structural Safety in a May 2019 alert. This noted that the Department for Education had contacted all schools in late 2018 to draw attention to the failure of a flat roof constructed with RAAC planks.
Such planks were widely used in the construction of floors and roofs for certain types of building, for example schools, from the mid-1950s to the 1980s. In its most common form, however, RAAC is used in lightweight thermal blocks for retail and office buildings.
A concrete compound made up of fine aggregates and gas bubbles, RAAC is less dense than normal concrete mixes and – importantly – is not as strong in compression. It has a lower capacity for bonding with embedded steelwork, so the steelwork itself will need hooks or welded crossbars to affix to RAAC securely, as well as corrosion protection, such as a latex or a bitumen coating.
The particular concern with RAAC planks is their potential for sudden shear failure: if a building structure is going to fail, it is preferable that this happens by degrees so there are warning signs rather than immediate catastrophic failure. Shear failure occurs due to inadequate steel reinforcement, typically at the end of the plank elements.
To compound this risk, RAAC planks are also prone to deflection and sagging because they have are less rigid than normal concrete, so will more easily, and permanently, deform under stress. This is a particular risk when they have been incorrectly detailed, working loads have been underestimated, elements are undersized, or reinforcement is inadequate.
Furthermore, with sagging there is the potential for cracking, and for the steel reinforcement to become exposed to moisture and thus susceptible to corrosion. Ponding may also occur on a roof where there is sagging, increasing the load on an element or elements and the risk of cracking, moisture ingress and corrosion.
As a result of these concerns over its structural performance and durability, production of RAAC in the UK stopped in 1982. If RAAC is discovered during TDD, the risk must therefore be assessed, considering the use of the space and evidence of structural deterioration. The location of reinforcement can be detected using a cover meter, while samples of concrete can be tested for carbonation because if present this can result in cracking.
Structural engineers can recommend that RAAC planks are either removed or strengthened wherever they are found – regardless of condition – because of the risk of sudden catastrophic failure. In any case, planks have a life expectancy of around 30 years, according to BRE Report 445, and are likely to have exceeded this in most instances. Other professionals may however recommend a more proportionate response that fully considers the specific circumstances.
If strengthening is a consideration, timber joists or steel beams can be constructed underneath RAAC elements, or a replacement structure such as, for example, a new roof or floor slab can be constructed over them.
Brick slip movement can pose problems
As a consultancy, TFT also still sees issues with brick slips, most notably in concrete-framed buildings constructed in the 1960s and 1970s. Brick slip and brick panel systems have evolved, though, and are still used in present-day construction; however, concerns about adhesive fixing and ill-considered detailing remain.
Defects occur due to differential movement between the frame and bricks. Typically, concrete is affected by drying shrinkage and axial and horizontal loading – and thus shortening in compression – while clay brickwork expands when drying and will be affected by moisture and thermal changes. As a result, brick slips secured to the structure with adhesive alone are widely considered to be deleterious, because they are prone to delaminating, with a risk of falling.
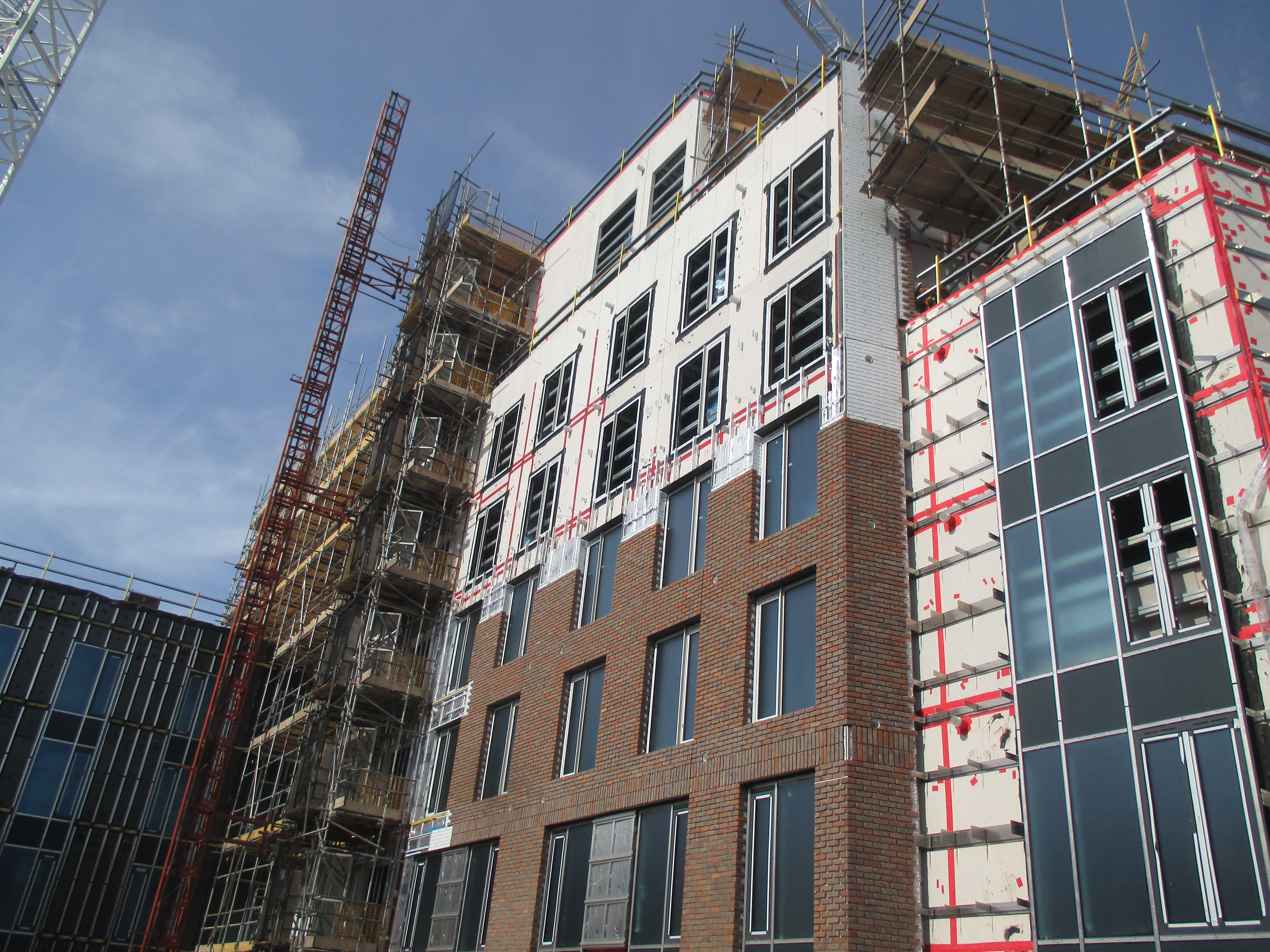
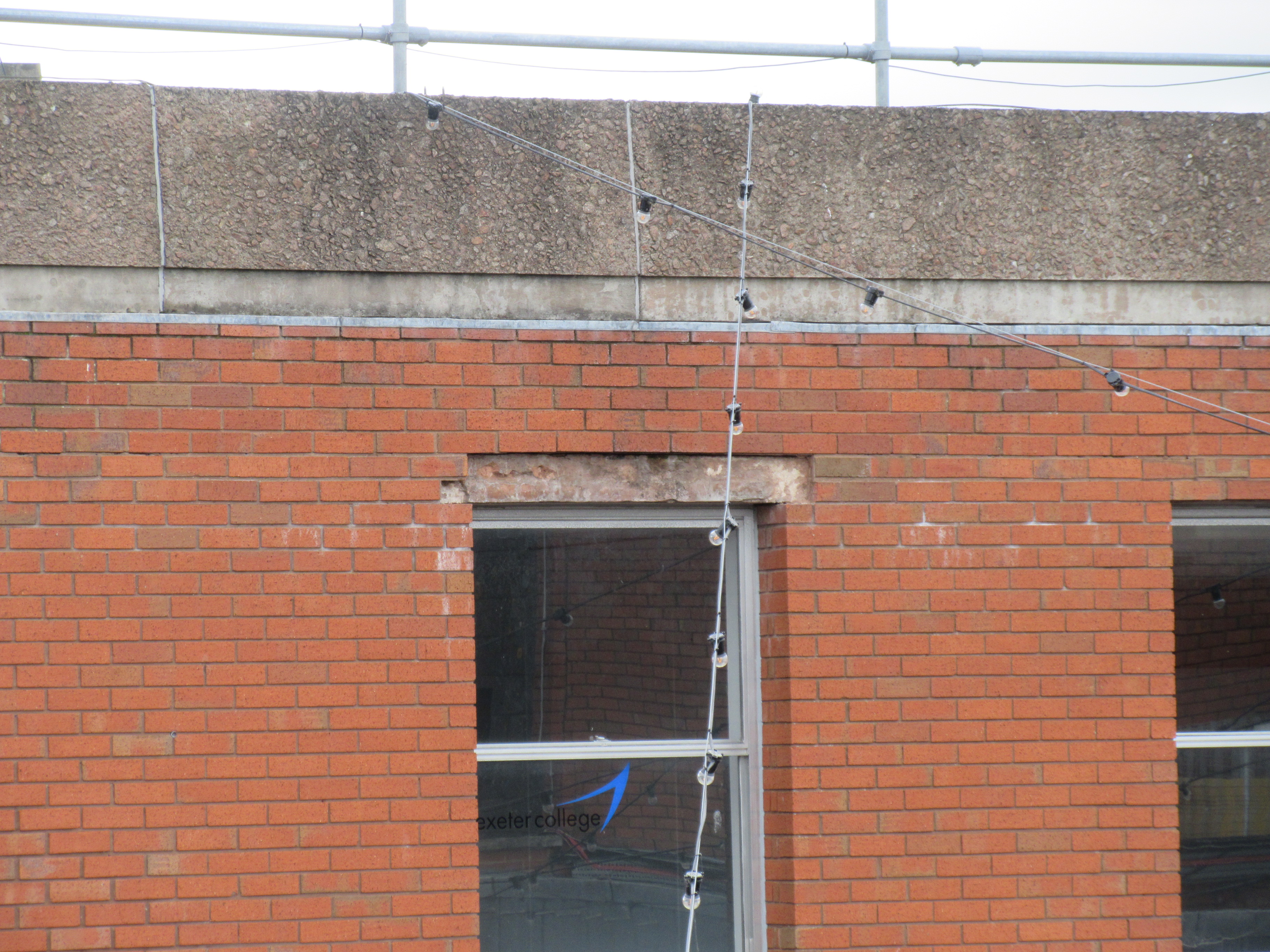
There are several forms of brick slip to look out for. As well as being applied to conceal concrete frames and lintels, they can also be used for a high-quality finish across whole facades or in brick panels. This is a good example of a product that continues to be used in modern construction despite negative perceptions, because designers believe they understand the inherent material properties and can design out some risks. Presumably because designers and manufacturers believe factory made panels and proper detailing overcome concerns regarding potential delaminating and bowing brick slip panels.
Modern brick panels present a risk if detailing is not properly considered. Panels need to be installed in a way that allows for building movement, minimising inaccuracies in construction. For example, excessive overhanging of bricks can result in eccentric loadings, and coupled with restrained movement can cause bowing and loosening of bricks.
We do see some clients prohibiting brick slips in their technical due diligence criteria. However, we also see structural engineers advising that slips are satisfactory if mechanically fixed back to the structure.
Many modern panels use bricks cast into concrete in the factory; for instance, perforated bricks provide a key for casting into the concrete. Such panels are mechanically fixed using rails, and are thus less likely to prompt concerns that they will detach. Nevertheless, modern panels and brick slips still require movement joints, as you would incorporate in traditional brick construction, as well as proper detailing.
It is important to remember that there can be fundamental issues with brick slips in a facade even if few defects are evident from a visual inspection at ground level. As such, it is vital that we as building surveyors are cognisant of the risks relating to brick slips, particularly as they continue to be used in construction.
The defects described are an example of some of the problematic materials that we typically see when undertaking TDD. Interestingly, as with most materials, when well designed, constructed and maintained, with the proper knowledge of how these materials behave, then these forms of construction can perform satisfactorily. Good TDD surveyors are particularly valuable in helping clients to understand potentially significant and costly issues, where visible signs are not necessarily obvious, and in providing practical advice to better understand and remedy a problem.
Inevitably, not all problematic materials can be discussed in one article. However, the second piece in this pair will look at particular issues associated with three other materials; namely toughened glass, magnesium oxide boards and asbestos.