Rain running down glass © Dr Robyn Pender
Although overall precipitation in the UK is not expected to increase as the climate changes, rainfall is predicted to arrive in much shorter and heavier bursts.
Anecdotal evidence suggests this change is already under way, with gutters, downpipes and drains overtopping much more frequently. Cathedral architects, for example, are now reporting failures of rainwater-handling systems that had hitherto coped well for hundreds of years.
Industrial systems gradually replace solid walls
In the past, rain resistance was provided by solid walls constructed from permeable materials such as earth, stone, lime-based mortars and brick, most of which were sourced locally.
However, the Industrial Revolution and the use of fossil fuels led to the introduction of new waterproof materials, such as, clear window glass, cement, steel and aluminium, production of which demanded considerable quantities of energy.
At first, these were used as particular components, such as glazed windows, in buildings that otherwise remained largely traditional.
Into and throughout the 20th century, however, permeable materials were almost entirely replaced and solid walls gave way to multi-layered systems of ever-increasing complexity.
It began to be assumed that solid-wall buildings were more susceptible to penetrating water than modern construction, even though many surveyors noted ample evidence to the contrary. Even traditional materials such as brick began to be fired at higher temperatures, making them harder and less porous.
Outside building conservation, the principles underlying solid-wall construction have now been all but forgotten in the global north. The result for older buildings has been not just poor maintenance, but also a shift towards repairs using modern materials and methodologies that not only fail to increase resilience, but too often actively induce failure.
It is useful to return to first principles, and examine the way these two very different approaches to building envelopes actually interact with water.
The traditional and modern envelope types have commonly been referred to as 'breathable' and 'non-breathable' respectively, but these terms are vague and scientifically inaccurate.
A more useful pair of terms was coined in the 1950s by the then director of the Building Research Station, Fred Measham Lea: 'raincoats' and 'greatcoats'. These are exact analogies, making any underlying complexities simple to grasp.
Impermeability failings prompt multiple layers
Raincoats are constructed using industrial materials that are all but impermeable, such as glass, metals, cement, high-fired bricks and terracotta and plastic. The idea is to create a waterproof layer like a plastic mackintosh. Rain that hits these materials will bead, collect and flow down the surface under the action of gravity.
The weak points are the joints and interfaces, which suck in the flowing rain and siphon it through the surface.
Sealing joints is extremely difficult, not least because the narrower the capillary, the more effectively it will transport water. To make things even more challenging, the materials used to make raincoat building envelopes are all thermally sensitive, changing dimension significantly as they are exposed to variations in sunlight, wind and air temperature.
Most are brittle and prone to cracking, which necessitates expansion joints and will need to be sealed. Cracks themselves make excellent capillaries. Brick veneers, for example, often suck water in through the fine fissures that form at the interfaces between bricks and the cement mortar.
Veneer walls first appeared after the First World War, in an attempt to reduce the quantity of materials used in construction. Rain ingress was quickly found to be a problem, so a second 'wythe' – or layer of masonry – was introduced, to create the cavity wall system.
Leakage proved even more problematic with the lightweight glass envelopes that began to appear around the same time: buildings such as the mid-1920s Zonnestraal Sanatorium in the Netherlands and Bauhaus Dessau in Germany, as well as the architecture of the International Style that culminated in Mies van der Rohe's design for the 1958 Seagram Building in New York, which became the standard model for commercial property.
By the 1960s, lightweight facades had evolved into 'rainscreens' comprising two, three or more separate layers, analogous to the wythes of cavity walls.
Raincoat envelopes run risk of trapping water
Because water on the wrong side of a raincoat cannot easily travel back out again through the waterproof skin, a fundamental problem is that any water collecting inside such an envelope will be trapped.
This includes not just penetrating rainwater, but any moisture generated inside the building from cooking and cleaning or from leaks in the plumbing.
Over time, therefore, interior moisture levels tend to build, not only making the buildings uncomfortable but exacerbating condensation.
Raincoat materials such as metal, glass and plastic sheeting – being non-porous and quick to cool – are highly prone to condensation, which can quickly lead to problems such as mould growth.
If condensation is extreme or prolonged, it will begin to run down the internal surfaces of the raincoat, leading to moisture-related fabric failures.
To try to control penetrating water, almost all types of raincoat envelope incorporate some form of water management in the cavities between wythes. This includes drains to collect water and channel it back to the exterior, and usually some form of ventilation. Unfortunately, these often prove ineffective, and can themselves become conduits for water to penetrate the building.
Maintenance of raincoat envelopes is not straightforward either, largely because of the innate complexity of the multi-layered construction, and the difficulty of accessing cavities to understand and remediate problems.
Just locating the origin of leaks can be challenging. A common example is a flat roof waterproofed by layers of sheet membranes or asphalt. Pooling rainwater drawn in through tiny defects in the cover will then be transported between the layers by capillary action, and may travel considerable distances before eventually becoming visible on the ceiling far from the point of leakage.
By a quirk of history, these fundamental problems of building physics were greatly exacerbated by the fashion for minimalism that began at much the same time.
Designs favoured flat roofs and were devoid of water-shedding detailing around weak points such as wall-heads, windows and doors. Gutters and downpipes were minimised, and indeed were simply not included on most tall buildings.
It should therefore be no surprise that buildings with innovative lightweight facades, such as the Lloyd's of London building, very often have serious problems with rain penetration. Such problems are likely to become much worse as driving rain increases with climate change.
'A fundamental problem with raincoats is that water inside the envelope is trapped there by the waterproofing'
Structure of greatcoats limits moisture pathways
Until the introduction of raincoat systems, building envelopes were exclusively constructed with solid walls of porous materials, which kept out the rain in a very different manner.
These so-called greatcoat envelopes act exactly like the thick woollen coats and knitted jerseys worn by sailors and others working in extreme weather.
The simplest were made of mass earth, usually built on a simple foundation of stones in earthen mortar. Even more common were rubble-filled walls, in which the space between internal and external faces of brick or stone was occupied by a mixture of rocks and pebbles, broken brick and other debris. This was all held together with mortars, commonly of earth and often with lime as a stabiliser.
The aim was to have the fewest possible voids in the core. Both systems allowed corners to be constructed easily, and the plasticity of the materials meant expansion joints were not required.
Coursing of brick and stone masonry used bond patterns that did not create direct pathways for water between the exterior and the interior. Although stability demanded occasional units that bridged the entire wall thickness, especially around window and door openings, such through-stones were kept to a minimum.
As a finishing touch, many if not most greatcoat walls were rendered with earthen or lime-based mortars, and often limewashed as well.
Air-filled pores effectively manage water penetration
To see how a greatcoat wall resists a rainstorm, it must be considered at pore level. Even the strongest rainstorm is not like turning a hose on a wall: indeed, it is highly unlikely for two raindrops to hit the same pore.
A raindrop hitting the surface does not bead or run down, as it would on a raincoat; instead, it is held within the pores it has hit. It is prevented from penetrating further by the pressure of the air it is trapping inside the deeper pores. Eventually it will evaporate, often while the storm is still in progress, since wind is the primary mechanism of evaporation.
A raindrop will only be drawn into the wall should it happen to hit a pore that is the mouth of a capillary that happens to be filled with water rather than air.
Condensation and moisture transfer within pores will inevitably lead to a small number of water-filled capillaries over the years following construction, but the risk is from water that has been able to enter the wall core in quantity, and establish liquid-filled pathways from the interior to the exterior.
This is why vernacular architecture is characterised by building details that protect weak points where water could potentially enter the core, such as the wall-heads and window and door openings: features such as wide eaves and cornices, hood mouldings, and sills.
Drips prevent water travelling back along the underside of projecting elements, and flashings and flaunchings seal around upstands such as abutments and chimneys.
For a greatcoat envelope maintained in reasonable condition, moisture-filled capillaries will be rare, and the system will provide excellent rain resistance.
Research confirms mortars' resilience
If, however, building failures result in a significant number of water-filled capillaries opening to the surface, rain absorption becomes more likely. The absorbed water can then fill more capillaries, and the system begins to fail.
The precise point where resistance gives way to exponential water uptake will depend not just on the local weather conditions and exposure but on the greatcoat's materials, its construction and – crucially – its condition.
Some 20 years ago driving rain was investigated by the Engineering Historic Futures research programme. This included field tests on the highly exposed tower of Brodick Castle on the Isle of Arran.
Only one of the four walls showed rain penetration, and it was one of the least exposed. On this wall, however, the core was wet because the flashing of the external walkway had failed.
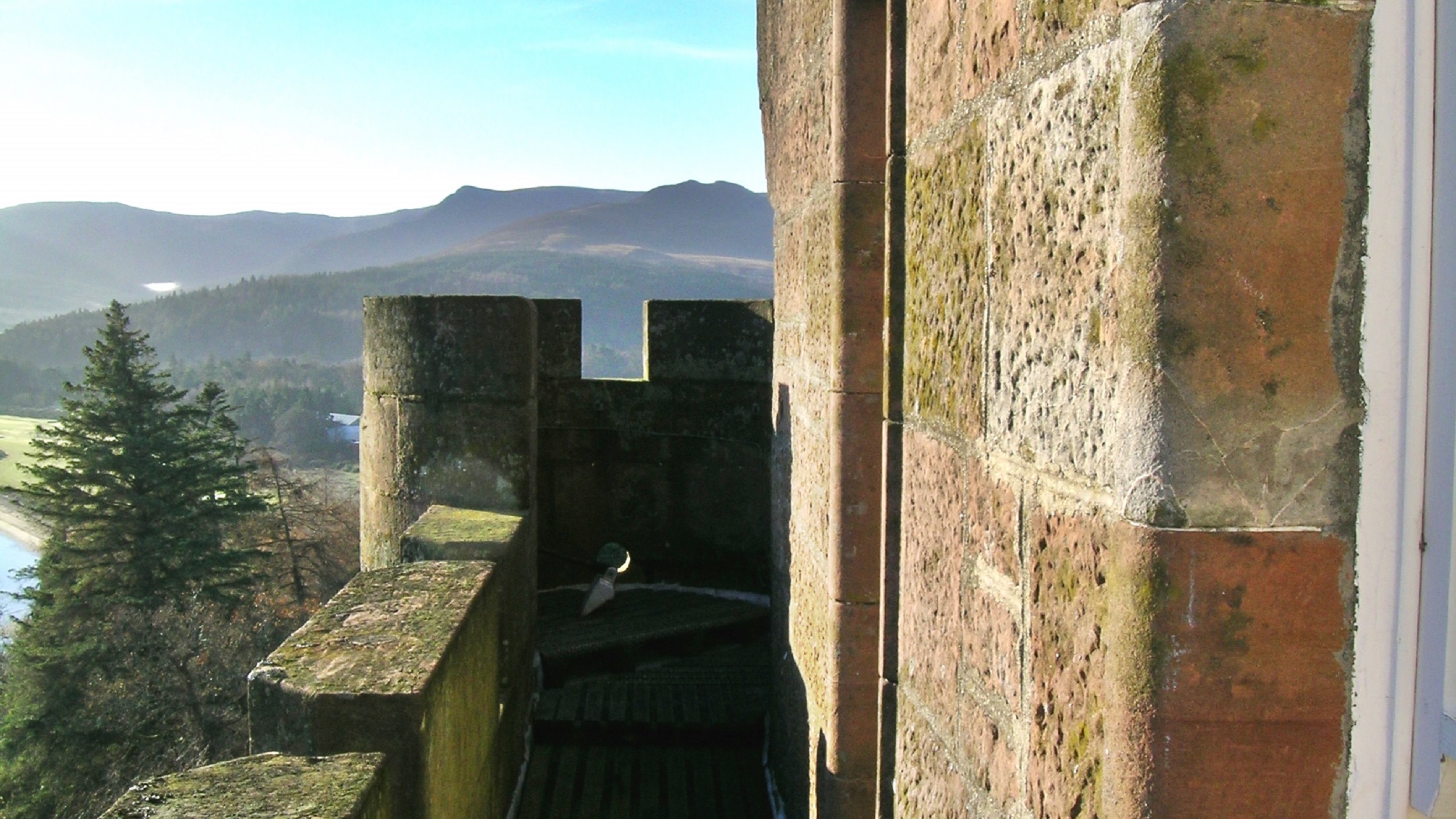
The tower of Brodick Castle © Dr Robyn Pender
Damp Towers research
Renders based on earth or lime mortars were a critical component of greatcoats, as demonstrated by the long-running Damp Towers research project conducted by English Heritage and Historic England.
Laboratory and field tests confirmed that, even when applied to walls where prolonged neglect had led to wash-out and voiding of the core, lime renders not only stop further rain penetration but help the core to dry out.
Other research has confirmed that lime mortars are exceptional at transferring water back to the wall surface, from whence it can evaporate.
It is easy to see why lime renders and limewashes were commonplace in the past, even in areas with little or no limestone of their own. There is indeed ample evidence that in the past even masonry walls that were not rendered immediately on construction were often rendered later, as soon as the mortar joints began to fail.
This is a very strong argument for reinstating lost lime renders on masonry, especially where buildings have persistent moisture problems – rather than perpetuating the current reliance on repointing.
Removal of elements increases leak risks
In the course of doing their job, the building elements designed to protect weak points degrade, and all will eventually need repair or perhaps replacement.
It is therefore worrying to realise that most building managers – and many other building professionals – now think of features such as hood mouldings and cornices as being primarily decorative. This puts them at high risk of loss or even deliberate removal, especially where a minimalist aesthetic dominates.
A particularly worrying example has been the wholesale clearance of renders to reveal the underlying masonry, an antiquarian fashion that began in the 19th century but it continues to this day. Is it any wonder that so many greatcoat buildings are currently damp?
Fortunately, even if greatcoat envelopes do become wet, their characteristics also allow them to dry out as soon as they are given the chance.
Repair is also quite straightforward, as long as the correct materials are used.
'It is worrying to realise that many building professionals now think of historic features as being primarily decorative'
Tradition offers model for modern practice
Since greatcoat mechanisms are highly rain-resistant by nature, they should never be disrupted by well-intentioned attempts to turn them into raincoats.
Waterproof coatings – whether cement renders and tanking, waterproofing compounds, or even plastic paints – are inevitably a bad idea.
Even the thickest coating cannot completely prevent water uptake, but it will dramatically reduce surface evaporation. Worse still, if the coatings change the nature of the surface so that rain begins to bead and flow rather than being held in surface pores, this will certainly lead to more absorption.
The inevitable result will be moisture levels increasing within the wall.
On the other hand, some challenging raincoat walls may benefit from greatcoat protection. For example, rendering a cavity brick wall in a lime-based mortar should significantly decrease rain uptake, not least by covering over cracked joints.
For lightweight glazed facades the problems are of course more intractable, and remediation many inevitably involve changes in appearance. Perhaps even there, lessons could be learned from the way traditional building elements were used to protect weak points from water pooling and leakage.
More importantly – if more radically – there are clear lessons for new construction. Greatcoats are highly resilient and long-lived, and their materials are low-carbon and sustainable. Is it not time we considered moving away from the raincoat approach, and returned to using tried-and-tested materials and methodologies of greatcoat construction?
'Even the thickest waterproof coating cannot completely prevent uptake, but will dramatically reduce surface evaporation'
A former advisor on both the Building Conservation and Research and the Building Climate Adaptation teams at Historic England, Dr Robyn Pender is now an independent researcher
Contact Robyn: Email | LinkedIn
Related competencies include: Building pathology, Conservation and restoration, Construction technology and environmental services, Inspection