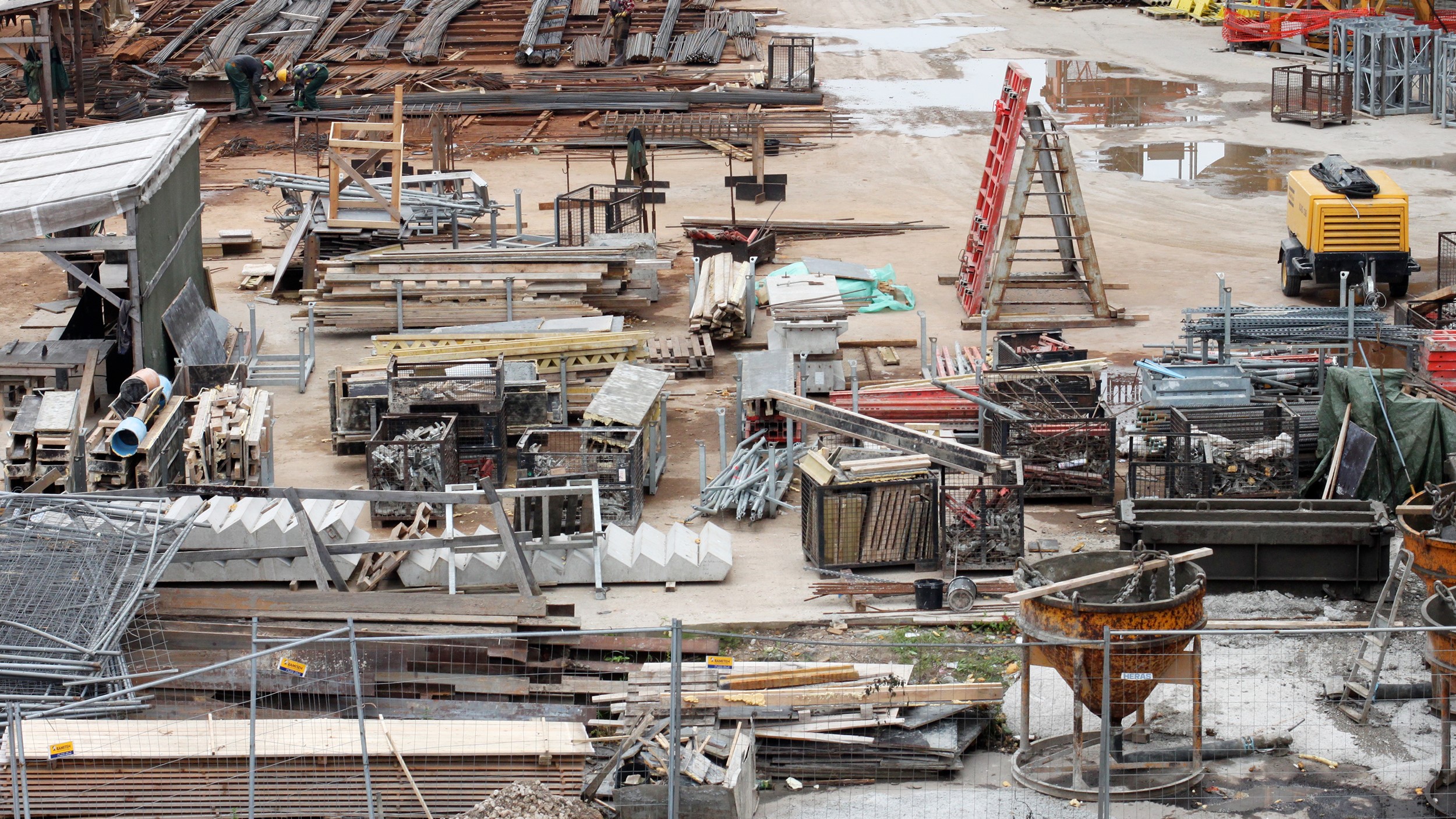
The term 'net zero' is thrown about so much it has almost lost its meaning. Nevertheless, the bar has been set and the UK is aiming to achieve net-zero carbon emissions by 2050.
The continued use of most traditional construction materials is incompatible with this goal. However, more attainable interim targets have been set by LETI, a network of more than 1,000 built environment professionals, to inform the objectives being set by the UK construction industry. Together, they have developed a roadmap to net zero by 2050, with a 2030 milestone to put the industry on the right path.
Table 1: LETI's embodied carbon targets by EPC rating. The design target was band C by 2020, which seems largely to have been achieved, and for 2030 is band A. Note: figures include all building fittings and fixtures; targets for structure alone are typically 50–65% of these values
EPC rating | Target (kg/m2 of gross internal area) | |||
Office | Residential | Education | Retail | |
A++ | <100 | <100 | <100 | <100 |
A+ | <225 | <200 | <200 | <200 |
A | <350 | <300 | <300 | <300 |
B | <475 | <400 | <400 | <425 |
C | <600 | <500 | <500 | <550 |
D | <775 | <675 | <625 | <700 |
E | <950 | <850 | <750 | <850 |
F | <1,100 | <1,000 | <875 | <1,000 |
G | <1,300 | <1,200 | <1,100 | <1,200 |
Table 1: LETI's embodied carbon targets by EPC rating. The design target was band C by 2020, which seems largely to have been achieved, and for 2030 is band A. Note: figures include all building fittings and fixtures; targets for structure alone are typically 50–65% of these values
EPC rating | Target (kg/m2 of gross internal area) | |||
Office | Residential | Education | Retail | |
A++ | <100 | <100 | <100 | <100 |
A+ | <225 | <200 | <200 | <200 |
A | <350 | <300 | <300 | <300 |
B | <475 | <400 | <400 | <425 |
C | <600 | <500 | <500 | <550 |
D | <775 | <675 | <625 | <700 |
E | <950 | <850 | <750 | <850 |
F | <1,100 | <1,000 | <875 | <1,000 |
G | <1,300 | <1,200 | <1,100 | <1,200 |
Table 1 shows that LETI's design targets differ with building typology, given varying demand for material volume. This is reflected in the carbon budget for each. From these figures we can deduce that significant improvement is required between 2020 and 2030, equivalent to a jump of at least 40% on the 2020 target.
Invariably, building projects take several years from concept to completion, so the industry should already be looking at where it needs to be in 2025; or later, depending on the programme completion date being considered.
Assessing embodied carbon in buildings
My employer, structural and facade engineering firm Eckersley O'Callaghan, pledged in 2019 to record emissions for all projects. Our first hurdle was to understand how to measure embodied carbon upfront. Structure alone can represent more than 50% of life-cycle carbon, which arises during supply and construction.
Early emissions data quickly showed us which projects were successful and which were not. We discovered that basements represent significant embodied carbon: they require a large volume of material, so as to withstand earth and hydrostatic pressures. Single-storey buildings are a close second, simply because the floorspace is relatively small and carbon is measured per square metre.
Anything using traditional framing materials such as concrete and steel will score poorly if these aren't used efficiently. Column grids greater than 10m will not meet the LETI 2030 targets either.
As taller buildings need stronger cores and foundations, this also increases the material demand and in turn their carbon footprint. We estimate that this will begin to affect the carbon intensity of buildings higher than 15 storeys in particular, where more substantial lateral stability systems are required.
We share information on buildings' carbon intensity with clients and architects. The decision-makers and project stakeholders can choose to take our advice; but beyond emphasising the commercial benefits we have little influence.
So we need to be doing more now to make sure we meet the targets in 2050. As engineers, we have to push the agenda and convince reluctant clients of what action and change is required now.
Alternatives and adaptation
We need to be more measured and thoughtful in our decisions, using materials as required rather than just doing things in the way we always have. To meet the LETI targets for 2030 and beyond, developers will have to take leaner approaches to design and use lower-carbon technologies.
Less commonly used, lean approaches for concrete framing – such as post-tensioned and ribbed-slab options – are much less carbon-intensive than the traditional flat-slab approach. These approaches were used more frequently in the late 20th century when material was more costly than labour, and will need to become more widespread if we are to continue to use concrete for our buildings. Such systems often need greater structural floor depths, though, which requires planning authorities to be understanding.
Lower-carbon technologies meanwhile can include engineered timber. A particular benefit of timber is that it can sequester carbon from the atmosphere for the long term. Replanted forests can even sequester more carbon than the project's entire carbon budget, including the basement. Although they cannot be recorded today, these long-term benefits must not be ignored. Other materials do not have the same regenerative behaviour.
We can also extend the lifespan of existing building stock by adaptation and reuse. Every floor, wall or foundation retained in a reused building represents a net saving on your carbon budget. If you can extend or reuse an existing frame, emissions will be half those of a replacement building. You will also reduce the amount of material sent to landfill.
Our recently completed project for London South Bank University is a prime example of adapting an existing building to increase gross internal area (GIA) and limit waste. A four-storey 1970s building, formerly used as teaching and office space, has become a student hub, with lecture theatres, library, sports facilities and catering areas.
Works included carbon-fibre strengthening, verifying the existing structure and making additions, including 1,000m2 of new accommodation. The project was responsible for only 50kg of carbon dioxide per square metre of development.
'We need to be more measured and thoughtful in our decisions, using materials as required rather than just doing things in the way we always have'
Reducing carbon in new buildings
New-build projects can also significantly reduce their embodied carbon. However, this needs careful specification of materials and a forward-thinking client. We are lucky to be working with such a client on the Atlassian tower in Sydney, Australia. The detailed design stage is complete, and the project is due to go on site at the time of writing.
Designed as a layer cake of timber and steelwork, the tower will keep embodied carbon to below 300kg/m2. The entirely steel framework of every fifth floor mitigates against fire spread.
Making measurement easier
Reducing embodied carbon in reused and new buildings alike can only succeed when it can be properly measured.
Using the ICE Database V3.0 and assessing the global warming potential of each material was until recently a painstaking calculation.
Before the Paris Agreement, the only incentive for engineers to measure tonnages of building materials was to identify commercial benefits for clients for procurement purposes.
However, such quantitative analysis is now more straightforward, with tools specifically created to record embodied carbon, which must be based on accurate volumes.
For instance, Eckersley O'Callaghan has developed a software plugin called EOC ECO2 for our building information models, which extracts quantities straight from the software. This gives us a sustainability value under the Structural Carbon Rating Scheme (SCORS). In a bid to move the industry forward, we have recently shared the software script on an open platform so others can use it.
Harnessing BIM to cut waste
Eckersley O'Callaghan is also developing optimisation and rationalisation tools to place the most efficient elements in each part of a structure.
Contractors and designers, both professions under time pressure, want assembly lines with matching, repeat components. However, this leads to a terrible waste of material. If we can exploit the full potential of BIM, we can overcome this challenge.
When creating building information models, we can harness the accuracy and exacting requirement for each element. This can be fed into a manufacturer's assembly lines just in time, reducing the volume of material waste.
Until recently, BIM was used to create the most elegant, materially efficient and commercially viable structures. Now it has the additional benefit of helping lower carbon intensity. The client thus gets a more sustainable building without extra effort.
Sustainability is still overlooked
To engineer a sustainable future, we still need to challenge our colleagues, clients and the decision-makers.
Our industry and its institutions continue to present awards to buildings that make little consideration for sustainability. Only days before COP26, the top award in UK architecture – the Stirling Prize – went to Kingston University's Townhouse. This project was described by The Guardian as 'a handsome concerto of concrete (for which no embodied carbon assessment was conducted)'.
This is surely not right. But there is a profound lack of courage in the industry to break the mould. One hopeful sign, at least, is the Institution of Structural Engineers' recent introduction of a low-carbon ambition award.
Of course, sustainability cannot be an excuse for bad design, and our buildings still need to delight and inspire us. But if industry fails to recognise sustainability as a fundamental design criterion, it will suffer a dangerous lack of credibility.
Duncan Walters is an associate director at Eckersley O’Callaghan
Contact Duncan: Email
Related competencies include: Design and specification