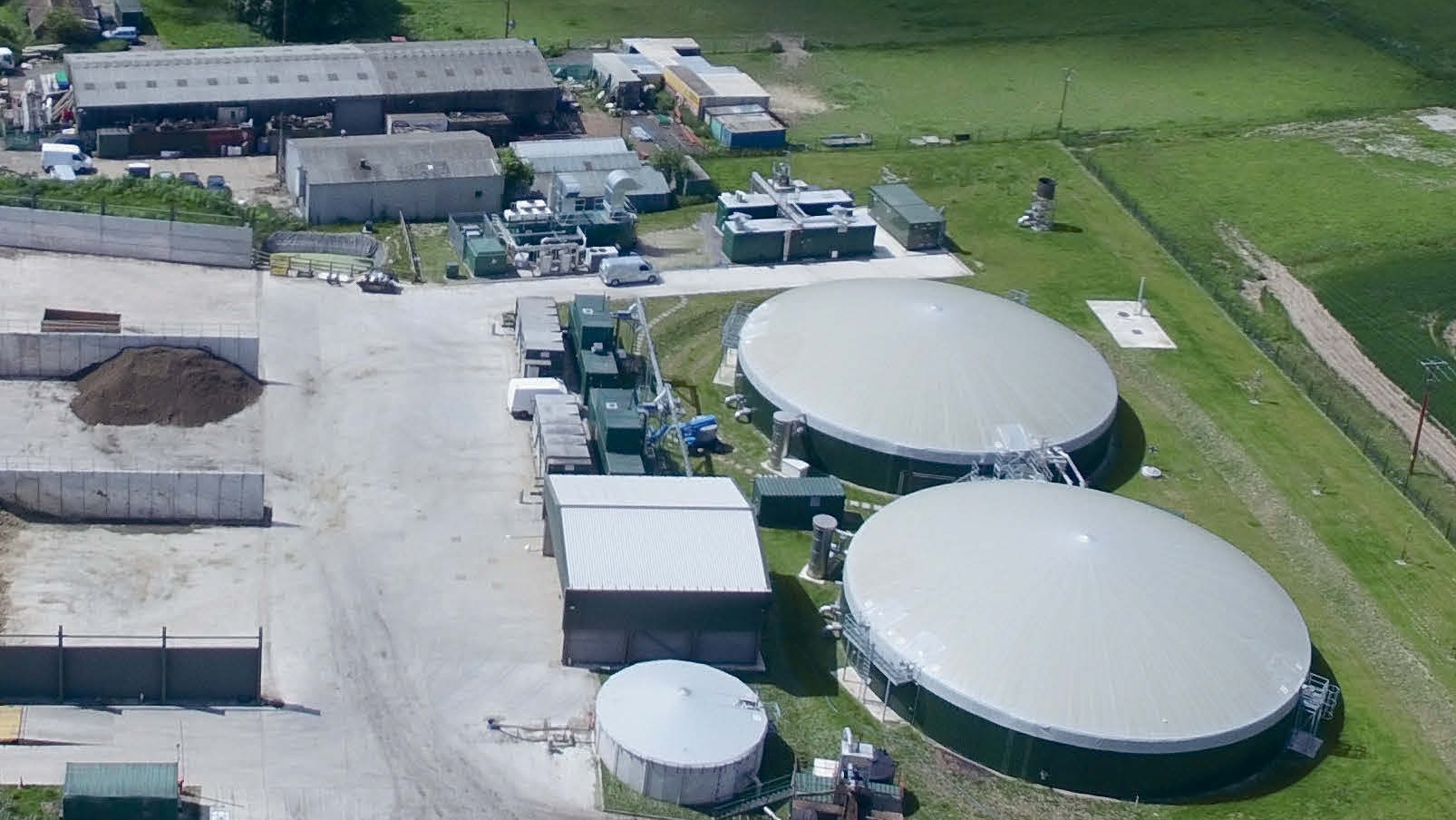
Aerial view of Icknield Farm biogas plant; the digesters are the two circular units on the right, © Envitec Biogas UK Ltd
Farmer Guy Hildred works the mainly arable 700ha Icknield Farm between Goring-on-Thames and Wallingford in South Oxfordshire. He also works with a nearby farm, servicing more than 3,000ha of mainly cereal-growing land. However, the Hildred Partnership was looking to diversify to ensure long-term regular income.
David Bermingham of DB Consulting, which is also based in Goring-on-Thames, wanted a suitable location for an anaerobic digestion plant that would produce biomethane to feed into the local natural gas pipeline, which serves villages along this stretch of the Thames Valley. Icknield Farm was the optimum site, with its existing farm buildings only 80m from the gas grid connection point, and thus a new partnership was formed. DB Consulting managed the project, carried out the feasibility stud,y prepared the business case, chose the company to build the plant, prepared the planning application and oversaw construction. The size and feedstock requirement was calculated to add value to the existing farm enterprises rather than changing the system to feed a digester.
Fisher German chartered surveyors and property consultants helped submit the planning application, including instruction of all the necessary surveys. Permission was granted in January 2014. The key to making a successful application in the Chilterns Area of Outstanding Natural Beauty was in the preparation, and the documents assembled to accompany the submission. In-depth consultations were held with parish councils and local residents, who along with South Oxfordshire District Council and various non-governmental organisations were invited to see plants in operation to dispel misconceptions about odour, noise, land, air and water pollution and congestion of local rural roads.
The plant consists of two 28m-diameter digester tanks sunk 5m below ground to minimise any visual impact. Three storage clamps were constructed for maize and hybrid rye silage so that feedstock would be available throughout the year to maintain production. The biofertiliser is stored above ground in two ultra-flexible polyethylene storage bags on the farm, from which it is piped to fields during spring and autumn for spreading by dribble bar. To fertilise a more distant field, a tanker takes it to be stored nearby and then again spread by dribble bar. The plant that upgrades the biogas into biomethane of a quality that can be injected into the local gas grid is in a container beside the soundproofed, containerised, combined heat and power (CHP) engine.
"The plant consists of two 28m-diameter digester tanks sunk 5m below ground to minimise any visual impact"
The biogas is produced from a total annual input of 34,000 tonnes, grown on the farm and supplemented locally according to need. This comprises 11,000 tonnes of cereals and grain screenings, 13,000 tonnes of maize and rye silage and 10,000 tonnes of pig manure. Manure from a nearby farm has a low dry matter content that dilutes the mass in the digester tank to produce the most conducive environment for the millions of bacteria that break down the solids in the absence of air and enable them to thrive and to produce the biogas. Annual output is 10m cubic metres of biogas, which in turn produces some 4.75m cubic metres of biomethane with an energy value that amounts to 51.3m kWh thermal as well as 2,700MW of electricity from the CHP engine.
Building the plant
Envitec UK Ltd built the plant in 2014, using the EnviThan polymer membrane, to upgrade the biogas to biomethane with a purity of around 99% and pressure sufficiently high to inject directly into the natural gas grid without any additional compression. The innovative technology exploits the small carbon dioxide molecules that migrate quickly through the membrane, a simple, environmentally friendly treatment that is cost-effective because there is no need for further processing, chemicals or water.
The biomethane is injected into the Scotia Gas Networks distribution grid and sold under contract to third-party gas shippers. It is also eligible for regular payments through the government's Renewable Heat Incentive to encourage innovative low-carbon technologies. Together, these payments will provide a regular income for the farm for the next 20 years. The containerised 360kW CHP engine provides all the heat and power needed to operate the plant. Any surplus power is then exported to the electricity distribution network.
- year 1: wheat
- year 2: wheat
- year 3: barley
- year 4: oilseed rape
- year 1: wheat
- year 2: rye and/or barley
- year 3: turnips as catch crop, then maize
- year 4: wheat
Turnips are planted after harvest, and before the maize is planted. The root vegetables serve as a crop to provide winter grazing for 2,000 ewes from a neighbouring farm, which yields another income stream thanks to the land rent. Another advantage of grazing the sheep is that they trample and dung the mainly gravel soils over chalk. A breakdown of the area used for crops is shown in Table 1.
Crop |
Area before (ha) | Area after (ha) |
Wheat |
420 | 434 |
Barley | 140 | 147 |
Oilseed rape | 140 | - |
Maize | - | 77 |
Rye for silage | - | 42 |
Table 1.
Crop area before and after installation of biomethane plant
Crop |
Area before (ha) | Area after (ha) |
Wheat |
420 | 434 |
Barley | 140 | 147 |
Oilseed rape | 140 | - |
Maize | - | 77 |
Rye for silage | - | 42 |
The installation of the plant has changed the farm output from oil for margarine and cereals for bread to cereals for bread, meat and energy. The area sown with oilseed rape is gradually being reduced. This crop rotation also reduces the occurrence of herbicide-resistant black grass: any emergent young black grass that establishes in the stubble after harvest is either grazed off by the sheep or stifled by the turnips. The maize, established as a spring crop, creates a high-density canopy that further prevents the growth of any surviving black grass. After the maize has been harvested, turnips are planted for sheep grazing. The fields are left clean for the spring sowing of cereals.
The plant produces a significant quantity of biofertiliser, or digestate, which replaces a proportion of the minerals that were previously bought and applied (see Table 2). Early unpublished research by Prof. Richard Dinsdale in the Faculty of Computing, Engineering and Science at the University of South Wales shows that some digestates from crops have levels of plant growth hormones that can enhance root growth. Further research is needed, but if these results can be validated at the operational plant scale it could mean reduced use of fertilisers and pesticides.
- reduced need to buy nitrogen potash and phosphate fertiliser or trace elements
- a new regular income for lifetime of the plant from sales of biomethane and electricity
- income from land rent for winter grazing of 2,000 ewes
- guaranteed markets and stabilised income for crops that would otherwise fall below market price and quality and cereal screenings too poor quality to use elsewhere.
Better yields and lower production costs have increased the gross margin per hectare. The plant was funded by equity from private individuals under the Enterprise Investment Scheme for start-ups. Total costs from conception to commissioning were 2% of the total capital cost of around £7m, while an extra £1.2m was spent in 2016 to increase the capacity of the upgrading plant.
Clare Lukehurst OBE is UK team leader at International Energy Agency Bioenergy Task 37 Biogas clare.lukehurst@green-ways.eclipse.co.uk
Related competencies include: Agriculture, Energy and renewable resources, Land use and diversification
The case study Icknield Farm biogas: An integrated farm enterprise was published by the International Energy Agency Bioenergy Task 37 Biogas. Information from that study is incorporated here.
https://www.ieabioenergy.com/publications/icknield-farm-biogas-an-integrated-farm-enterprise/