Project Milestone
Three-dimensional (3D) printing first surfaced in the 1980s and has promised transformational applications in manufacturing and construction ever since. Those promises have been a long time coming for home building, but the signs are that both demand and enterprise are beginning to deliver for the technology.
It has been at the centre of a rash of innovative projects that have cropped up around the world in the past year. In California, Pallari Homes and Mighty Building offer a range of houses made up of rapidly-produced 3D-printed components which have been snapped up, leaving a long waiting list of keen buyers. Meanwhile, in Malawi, 14Trees, a joint venture between cement maker Holcim and CDC, a British government development-finance operation, can print a home in just 12 hours at a cost of less than $10,000.
And last year, in the Dutch city of Eindhoven, Project Milestone became the world's first commercial housing project based on 3D-concrete printing. The buildings’ futuristic design by architects Houben/Van Mierlo, showcases the technology's possibilities.
“Concrete printing has a universal application,” says Peter Paul Cornelissen, business unit manager at Saint Gobain, the firm that partnered with Project Milestone to undertake its concrete printing. “Alongside concrete printing, there are also some companies exploring the possibilities of reinforced plastics to print stairs, for example, or make specific custom parts for a house.”
Close on the heels of Project Milestone, India also saw its first 3D-printed concrete house built last year by start-up firm Tvasta Manufacturing Solutions; the structure is a single-storey 600ft2 house that took five days to build.
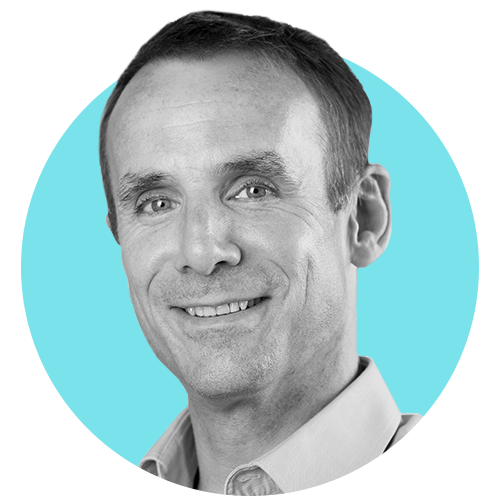
"One lesson from this process is that a design must be optimised for the technology you will be using” Peter Paul Cornelissen, business unit manager at Saint Gobain
Vinod Anand Bijlani, a sustainability and smart cities expert, believes that the completion of this project aligns well with the Pradhan Mantri Awas Yojana (housing for all) initiative set out by the Indian government which aims to provide 21.4 million affordable new homes by the end of 2022. The right combination of BIM with the potential of 3D printing in the construction industry presents a huge opportunity to address India’s acute housing shortage.
But Sobha Rani FRICS, managing director of Veadhik Cost Consultants based in Bengaluru, sounds a note of caution: "3D-printed homes are only slowly emerging. Construction firms are being more serious about it, but it is not yet at full scale."
She believes construction firms are becoming more aware of the benefits of 3D printing but need to get to grips with the technology to harness its enormous opportunities and potential. In particular, it could mean less reliance on a poorly-skilled workforce and fewer material supply issues both of which cause many of the issues that plague conventional sites.
The technology may also offer environmental benefits. While concrete as a material carries a large carbon footprint, 3D printing as a process stacks up well for sustainability creating greater precision and flexibility, allowing for less wastage and, if the mix is tweaked to include the use of local materials, reduces the need for transportation over long distances.
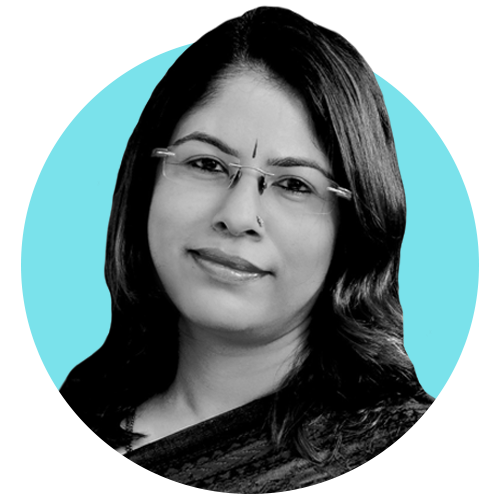
“Acceptance for any construction technology improves when it also appeals to the luxury market level; that way it can build trust across society” Sobha Rani FRICS
Broadening the appeal
While the social and commercial benefits of 3D printing are clear, the process and formats have some way to go before 3D-printed homes become a driving force in property markets.
Rani believes 3D homes in India should not be aimed at just one demographic but must carry broader appeal. "Looking at it as a business, you need to see the versatility of occupation, not just as a solution to affordable housing,” she says. “Focusing on affordable housing design only could be limiting, so builders need to look beyond that. Acceptance for any construction technology improves when it also appeals to the luxury market level; that way it can build trust across society."
The printers themselves can also be an expensive initial investment for construction firms and require a particular skill set which means that developers and contractors will take a keen interest in how concept homes perform once built and how much interest they generate.
Bridging the technical skills gap
Knowledge about the technology is also proving to be a limitation. "One lesson from this process is that a design must be optimised for the technology you will be using,” says Cornelissen. “If you don’t keep this in mind it will become quite hard to make use of the full benefit of the technology. This selection should be made as early in the development process as possible. People were calling us and saying, 'We're building a house, can you print it for us?' and what happens is the design does not necessarily fit the technology, and you won't get the best from it."
He believes one of the biggest challenges is disseminating knowledge, so people become aware of what is possible to be included when they research their design. The other big challenge is the rules, regulations and standards governing each jurisdiction. This means that 3D-printing pioneers have to certify all the processes and provide safety and materials guidance, for example – standards that have already been established with traditional builds.
Calum Gillhespy MRICS, director of planning and development at consultancy CSG Grays, thinks UK interest in 3D-printed homes may first develop within the high-end, self-build market. He is sceptical about how quickly volume builders will adopt the technology given how reluctant they have been to adopt other modern methods of construction (MMC) at scale.
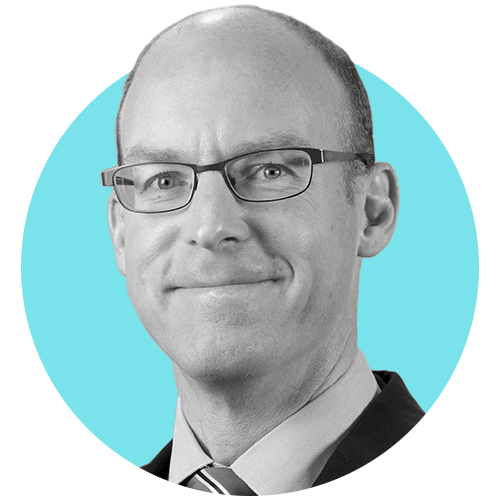
“If 3D printing is ever going to be adopted by the mainstream, it has to be an insurable product and you have to get the banks comfortable lending against that construction.” Calum Gillhespy MRICS
"If 3D printing is ever going to be adopted by the mainstream, it has to be an insurable product and you have to get the banks comfortable lending against that construction. Therein lies the rub for the valuer,” he says. “If you have regulatory and warranty issues sorted out, the next question is what figures you put on buildings. Like everyone else valuers will be relatively conservative in their approach, especially if they have PI concerns related to public perception, lack of comparables and proven performance."
Homebuilders and homeowners in the UK tend to err towards modified designs that have their roots in the buildings of the distant past. This is why both culture and land use will also play a factor in how 3D homes develop worldwide. The Netherlands, for example, has a history of embracing modern designs and variety in its home building. In other countries, the availability of land makes it relatively cheap, allowing developers there to take more risks experimenting with design.
Gillhespy believes that a stepping stone to getting 3D printing into the mainstream will involve more MMC with 3D-printed components within those buildings. "This could force more innovative designs, and you will begin to see the acceptance that we don't need homes that our great-great-grandfather would recognise as a house of his time."
Hyperlocal 3D printing
One of the advantages of concrete printing in construction is that the products used in the concrete mix can be tweaked according to the quality, cost and availability of materials locally or their suitability for a particular location.
This hyper-localism is an approach that Dr Sarbajit Banerjee at Texas A&M University has taken further, crushing to a powder whatever clay and rock materials are lying near the construction site and combining them with silicates that can be squeezed through a printer nozzle. It removes the need for cement and limits the transport requirements to the site. Pushing his methods to their logical limit, he has used soil from his back garden in the printing process.