This is the second part of a series of articles examining efforts by heavy industries to cut emissions associated with energy intensive construction materials. In part one we looked at steel and now we’re putting the spotlight on concrete, the most widely used building material on the planet.
A go-to material for construction since it first became commonly used by the Romans some 2,000 years ago, concrete today is responsible for roughly 8% of global carbon dioxide emissions, substantially more than the aviation industry, which accounts for about 2.5%. It's a significant factor in what Bill Gates calls the ‘75% problem’ – how do we cut three-quarters of global carbon emissions to avoid catastrophic climate change?
As populations in developing countries continue to grow, the need for concrete for new housing, tower blocks, car parks, bridges and dams has risen in line with severe implications for the climate and ecosystems. Heavy industries for cement manufacturing are a major contributor to emissions and particularly tough to abate using traditional renewables – due to the super-hot temperatures needed to run furnaces, which has perpetuated reliance on coal and coke, and high emissions from the chemical process of calcination.
Various research and development projects around the world are exploring how alternative energy sources can be exploited to power industrial plants. A £6m pilot project in the UK, run by the Mineral Products Association (MPA) and funded by the Department for Business, Energy and Industrial Strategy, will investigate how a combination of hydrogen and plasma technology could slash emissions in cement and lime production.
Trials at plants operated by Tarmac and Hanson Cement will gauge how electrical energy delivered by plasma torch can boost the combustion of biomass in a kiln to generate higher temperatures.
Alongside the use of green hydrogen, this could deliver a net zero fuel source, says the MPA, and if fully deployed it would save about 0.6% of UK CO2, equivalent to the emissions of about 266,000 homes.
“This is groundbreaking stuff never done anywhere else in the world,” says Richard Leese, director of MPA Cement. “A plasma torch puts heat into specific parts of the process to enhance combustion of the biomass. Fully electrifying cement manufacturing would require a complete redesign of the kiln system, but this technology requires only minor modifications.”
Solar power has never been capable of generating the incredibly high temperatures required in heavy industry, but a renewable energy technology company called Heliogen (backed by Microsoft co-founder Bill Gates) appears to have found the solution.
Heliogen exploits a combination of AI-based computer vision and sophisticated software to automatically align a giant array of mirrors to reflect sunlight onto a small target mounted on a tower. The concentrated solar power can generate temperatures up to 1,500oC, enough to replace fossil fuels in cement manufacturing, which has been identified by the company as a priority market.
An initial agreement with mining company Rio Tinto is expected to see the technology deployed at a mine in California to generate and store carbon-free energy to power various operations. And over on America’s east coast, New York has passed bill S-542A which encourages the use of low-carbon concrete and cement by awarding future building contracts to companies based on their environmental performance, as well as price.
Cement production isn’t only about the energy you have to put in, the calcination reaction needed to produce clinker, the active ingredient in cement, accounts for around two-thirds of direct emissions in the sector. Tackling this pollution either means a shift away from conventional production or using alternative binding agents in cement, which are currently limited in supply and typically more expensive.
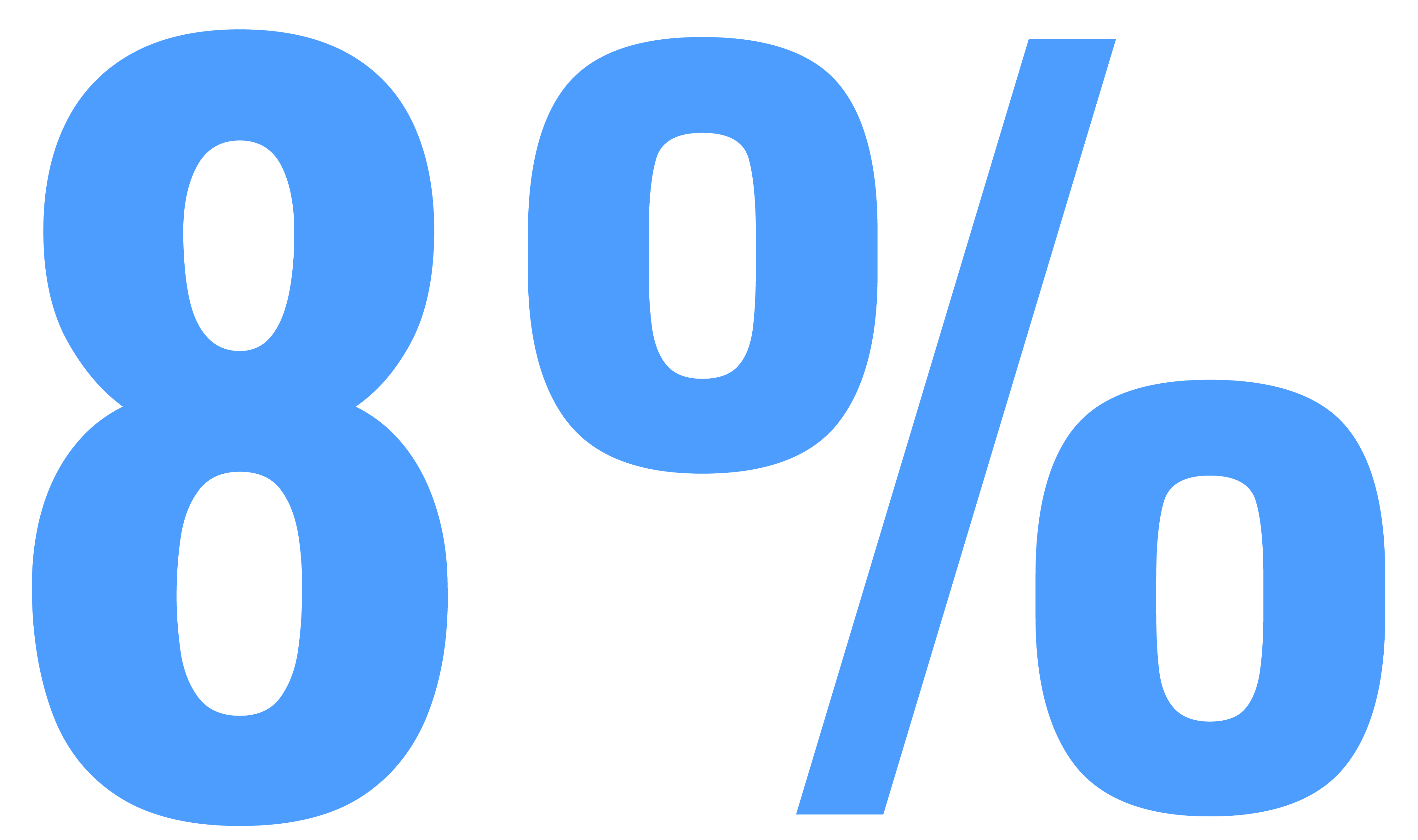
of global carbon dioxide emissions come from concrete
Carbon capture usage and storage
Carbon capture storage (CCUS) is an innovative, if unproven, technology backed by billions of dollars of investment and 20 pilot projects worldwide. It sucks climate-heating gas from the air and either stores it underground or transforms it into new chemical products.
Norway is launching the world’s first full-scale CCUS project, named Longship, that will initially capture CO2 emissions from the NORCEM Heidelberg cement plant in Brevik, near Oslo.
The CO2 will be transported by ship as a liquid to an onshore temporary storage facility on the country’s west coast before being moved by pipeline to a subsea reservoir in the North Sea.
Corporate titans Amazon and Microsoft are among investors in CarbonCure Technologies, a company that cuts the emissions of concrete companies by injecting waste CO2 into their mixes to produce stronger structures.
It now plans to source the CO2 it uses from cement production, creating a closed loop, with a goal to cut global concrete emissions by 500m metric tonnes by the end of the decade.
But CCUS technologies face major challenges that could hamper their widespread deployment. Energy requirements are an issue – a coal plant equipped with CO2 capturing equipment can require about 25% more fuel to generate the same amount of power as a conventional plant.
Time is another factor given the fledgling state of development, says Stephen Richardson, director for the Europe Regional Network at the World Green Building Council: “Lots of pilot plants are testing these technologies, but we still have quite a long way to go in terms of getting them to a scale where they can be rolled out at every single cement plant across the world that needs this technology.”
With around 90% of future cement production expected to take place outside of wealthy OECD countries, the path to cutting emissions needs to be both efficient and cheap.
“Ultimately there is no silver bullet solution to these issues,” says Richardson. “You have to take a holistic view and realise that, rather than keep consuming concrete at the rate we are today we have to do all we can to both reduce our use of it in the first place and to decarbonise it.” This multi-pronged approach to the climate emergency will consume designers and engineers for many years to come.
For more must-read Modus articles, sign up for the newsletter.
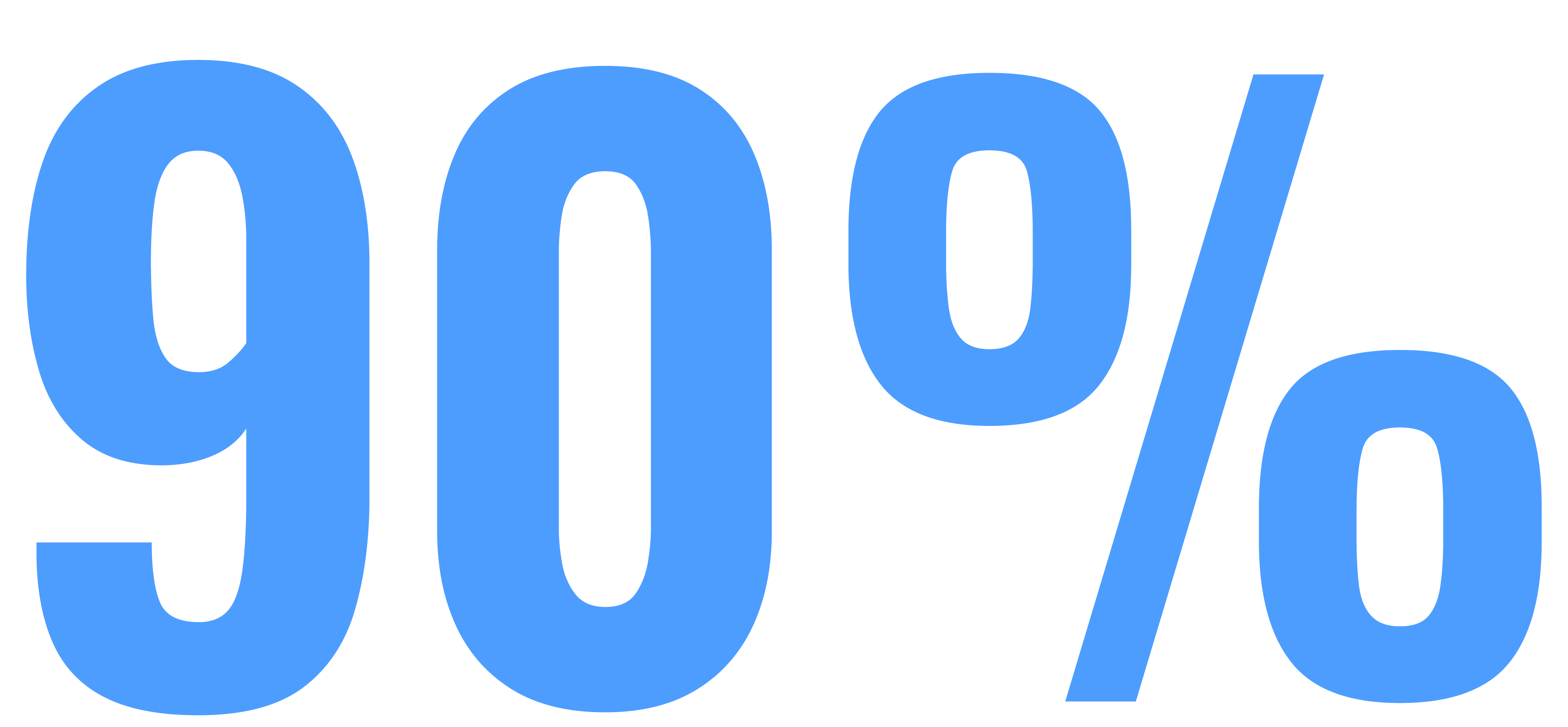
of future cement production will take place outside wealthy OECD countries