In the first of a series of articles examining efforts by heavy industries to cut emissions from energy intensive construction materials we put the spotlight on steel producers, responsible for around 8% of global carbon dioxide emissions.
As global populations continue to grow in prosperity and number, demand for energy sapping materials, like steel, concrete and glass, used in the construction of new buildings and infrastructure, is on the rise.
It's part of what Bill Gates calls the ‘75% problem’. How do we cut the three-quarters of emissions, mostly generated through large-scale industrial and agricultural processes that are intrinsic to many commonly used products?
Heavy industrial processes relied upon to manufacture construction materials are a major source of pollution. According to the World Steel Association, every tonne of steel produced in 2018 emitted 1.81 tonnes of CO2, equivalent to about 8% of global emissions, yet traditional renewable technologies are inadequate to mitigate their impacts.
That’s because many industrial processes require high temperature heat that’s currently almost exclusively provided by burning fossil fuels. Furthermore, recently-built plants are typically operational for 30-40 years, so emissions are considered ‘locked-in’, unless effective retrofit solutions become available.
Fundamental changes to steel manufacture will be critical to meet our climate commitments, and major players are using investment and innovation to help the sector clean up its act.
The first market-ready zero-carbon steel in Europe is expected to leave the factory gates in Sweden some time in the mid-2020s, thanks to a high-tech production process powered by green hydrogen.
The HYBRIT (Hydrogen Breakthrough Ironmaking Technology) pilot plant and storage facility, operated by steel maker SSAB, iron ore producer LKAB and energy company Vattenfall, opened last year – it has the potential to cut the country’s total CO2 emissions by a whopping 10%.
Hydrogen will replace traditional coal and coke as the reducing agent to remove oxygen from iron ore in the plant, with water the only byproduct. The system will initially run in test mode for four years, starting on natural gas before switching to hydrogen to compare the results.
The production of green hydrogen at scale is itself a challenge, as the process relies on the energy intensive electrolysis of water, so renewables are key to making it effective. So-called grey and blue hydrogen have significant carbon footprints.
Tata Steel recently teamed up with electrolysis expert Nobian and the Port of Amsterdam to investigate setting up a 100MW hydrogen plant at IJmuiden, able to produce up to 15,000 tonnes of green hydrogen each year using sustainable electricity.
Barry Rust, marketing manager for energy & sustainability at Tata Steel says: “Green hydrogen could become viable if electrolysis is powered by a renewable energy source like an offshore wind farm. Electrolysis is proven at small scale, but nobody has done it yet at large scale, the technology has to take itself forward.”
Another environmentally damaging aspect of steel manufacture is the smelting process, which typically occurs in a coal-dependent integrated blast furnace or a basic oxygen furnace.
Electric arc furnaces (EAFs), that use steel scrap or direct reduced iron (DRI) as their main raw materials, offer a more environmental alternative. And EAFs that maximise secondary flows and recycling by melting more scrap, are expected to play a key role in future decarbonisation.
Pat Hermon, technical lead on sustainable products at the Building Research Establishment (BRE), says: “EAFs are an established technology and cheaper, in some cases, than blast furnaces. Environmental product declarations (EPDs) from countries with low-carbon grids using EAFs for things like rebar, have a fraction of the embodied carbon of those coming from blast furnaces. The best EPD I saw was about 350kg/tonne of CO2, versus around 1,000-2,000kg/tonne from a blast furnace.”
However, a significant shift to EAFs will require energy grids that run on renewable power rather than fossil fuels, and a sufficiently robust supply of high-quality scrap, which could be a challenge depending on the location.
“Electric arc furnaces can't produce all current steel products,” says Rust. “Using more recycled content means managing the scrap pool very closely, especially when you are producing the high performing steels used in construction, which require very clean steel with few inclusions.”
Even 100% green-running furnaces can’t tackle emissions associated with the process of burning coke to convert iron oxide into iron, which becomes steel. But innovation could remove this source of harmful gases too.
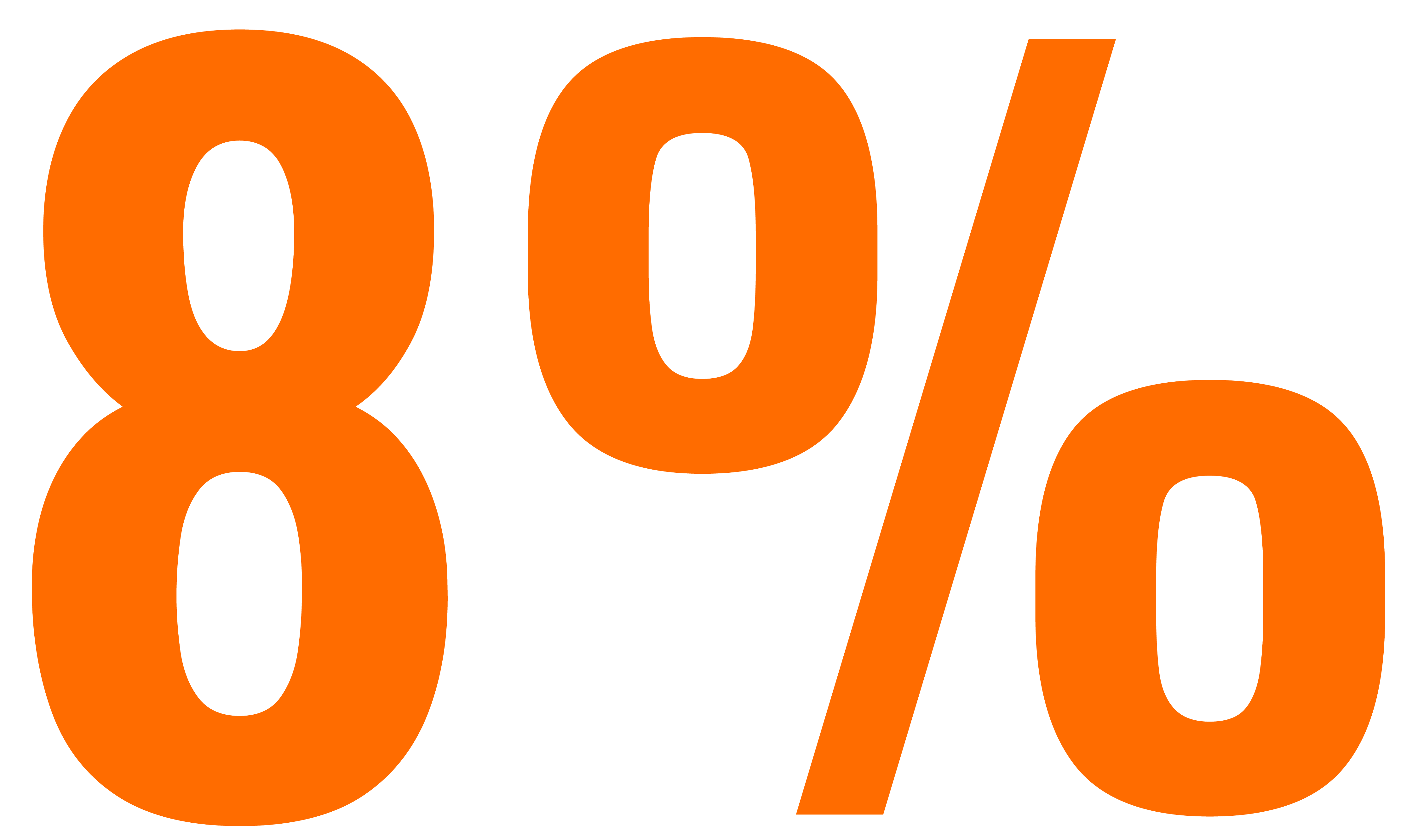
of global emissions come from steel production
Huge amounts of money are being channelled in carbon capture usage and storage (CCUS) technologies, designed to suck CO2 out of the air then store or convert it into new products for other industries (more on that in our next article on concrete).
Steel makers in Australia are using recycled polymers, such as car tyres, as a 50% replacement for coke in EAFs to deliver an 80% cut to emissions.
A prototype technique, developed by professor Veena Sahajwalla from the University of New South Wales, removes the need for coke entirely by adding carbon from spent coffee grounds to tyres in the kiln. She is now in discussions with mineral processing firm Molycop about potential commercial applications.
As steel producers evaluate decarbonisation strategies, we can expect a combination of different approaches and technologies in the coming years. Tightening carbon emission standards and the increasing cost of emission quotas are key causes of change. Recent studies have forecast that roughly 14% of steel companies’ potential value is at risk if they fail to decrease their environmental impact.
The widespread transition to zero-carbon steel now seems inevitable, the question is will it happen fast enough to avert a climate catastrophe?
Get Modus features sent straight to your inbox by signing up for the newsletter.
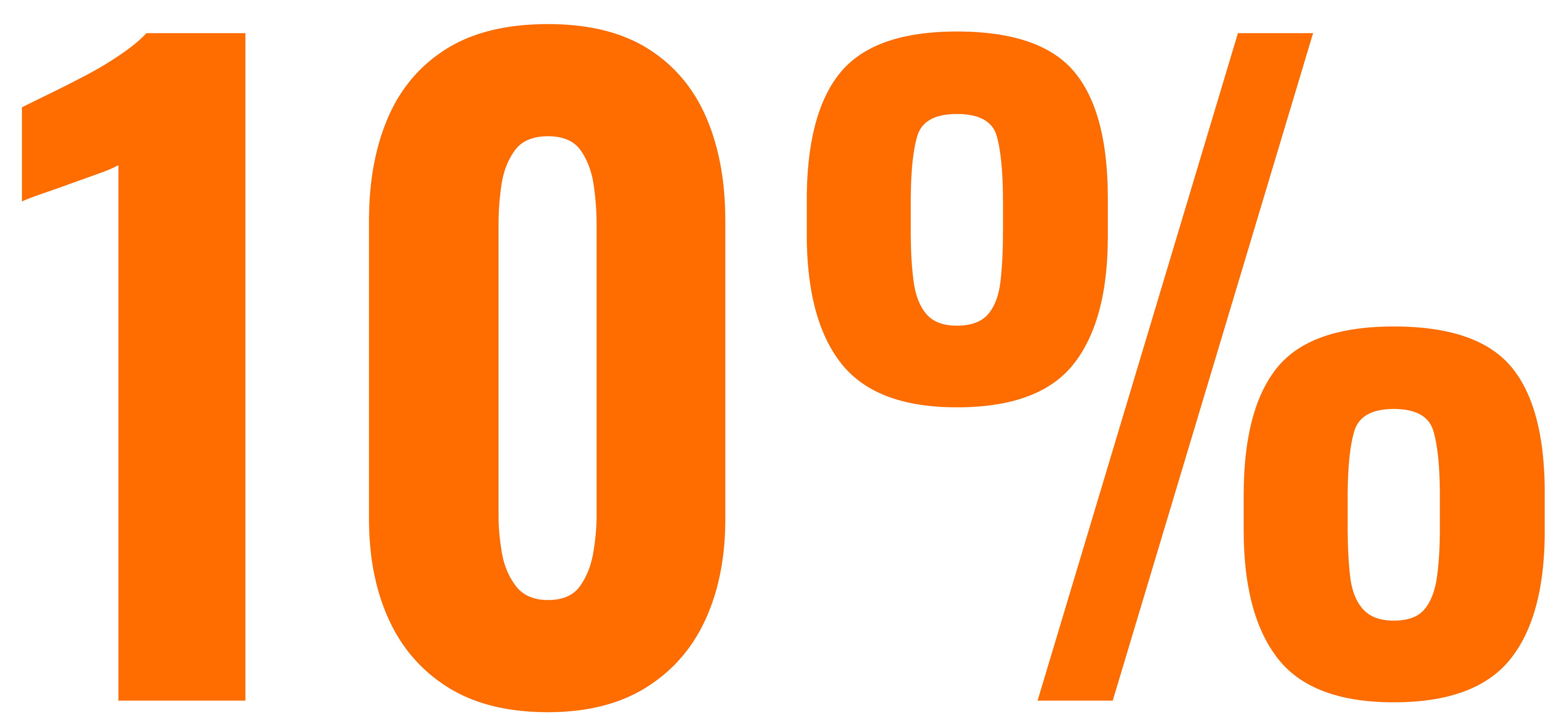
of Sweden's total CO2 emissions could be cut thanks to the HYBRIT plant