Take a virtual 360 tour of an imagined build - zoom, rotate and explore.
With two-thirds of existing buildings in Europe still likely to be standing in 2050, upgrading them to meet modern energy and thermal standards, as well as new space and health requirements, is critical for effectively transitioning to a more sustainable built environment.
Building retrofits and renovations are recognised as fundamental to meeting net carbon targets and global efforts to fend off climate breakdown.
But in a world where data is king, the structural idiosyncrasies, distinct regional styles and energy performance of historic post-second world war properties make implementing a precise digital approach to design and construction more of a challenge than with a new build.
Creating a true picture of what designers and engineers have to work with on site is a challenge when rooftops are inaccessible or when mechanical and electrical (M&E) and structural beams are hidden in walls or voids. Building information modelling (BIM) has the potential to make retrofits more efficient, intelligent and sustainable, but efforts to accurately capture and model the complex or ornate constructions of old buildings can be time consuming and expensive to achieve.
Keen to reap the rewards of a deeper dive into digital on retrofits, measurement surveyors are exploiting a range of innovative technologies to help smooth the process of information capture, analysis and communication and ensure that existing buildings remain efficient and relevant for decades to come.
Filling in the blanks
Refurb is a beast that feeds on data. Existing drawings and documents must be digitised, structures laser-scanned, and asset information populated. However, surveyors often face challenges building up a complete picture of an asset because of the inaccessibility of certain areas, like roof tops, facades or inside confined or covered spaces like risers, or wall cavities.
Drones are increasingly used to fill in gaps in external information and new techniques and cameras extend their capabilities. High resolution digital orthophotos, that combine the image characteristics of a photograph with the geometric qualities of a map, can support a detailed assessment of the condition of a roof. Thermal cameras can reveal leaks and when combined with point cloud data they can give an accurate understanding of the location and potential cause.
These were just a few of the techniques employed by Plowman Craven during its five-year surveying term commission contract for the Palace of Westminster, home of the UK government.
“Thermal teams are skilled in how they have to collect and analyse the data,” says Peter Folwell MRICS, property director at Plowman Craven. “By mounting thermal cameras on drones, we can cover roof areas and high elements of façades that used to be unreachable. On a recent prestigious heritage project, we even used unmanned aerial vehicles (UAVs) to support the assessment of the condition of the stonework, asset tagging every stone in BIM to assess the condition and the stone cleaning regime.”
There’s an app for almost anything nowadays but Apple’s recent launch of a light detection and ranging (LiDAR) scanner for the iPad Pro 2020 revealed the potential value of consumer tech to professional surveyors. Although accuracy may fall short of a high-end LiDAR scanner, the tool can measure surfaces up to five metres away, making it suitable for use in low down or confined areas where large-scale scanners are impractical.
Faster data capture
The laser scanner, a surveyor’s main weapon of choice for capturing existing assets, typically involves a trade-off: static devices are highly accurate but slow to set up and operate. While mobile scanners deliver results faster but with poorer data quality.
Recent years have seen greater convergence between the two as innovations such as SLAM technology (Simultaneous Location and Mapping) enable real-time data capture on the move with a much higher degree of precision.
The NavVis M6 and wearable VLX mobile mapping systems exploit SLAM algorithms to produce survey-grade point clouds of large projects. In a recent trial with English Heritage, NavVis was able to map a 56,000m2 castle in just 2.5 hours, whereas a static scanner might typically only manage a few thousand square metres a day.
Looking like something from a sci-fi movie, Leica’s dome-shaped handheld SLAM device BLK2GO generates point clouds accurate to around 20mm, making it most suitable for 3D mapping applications where the highest accuracy isn’t always required, like a 3D floor plan, area survey or model. According to the firm, it only takes a few minutes to scan an entire house compared to an hour or more using the static BLK360.
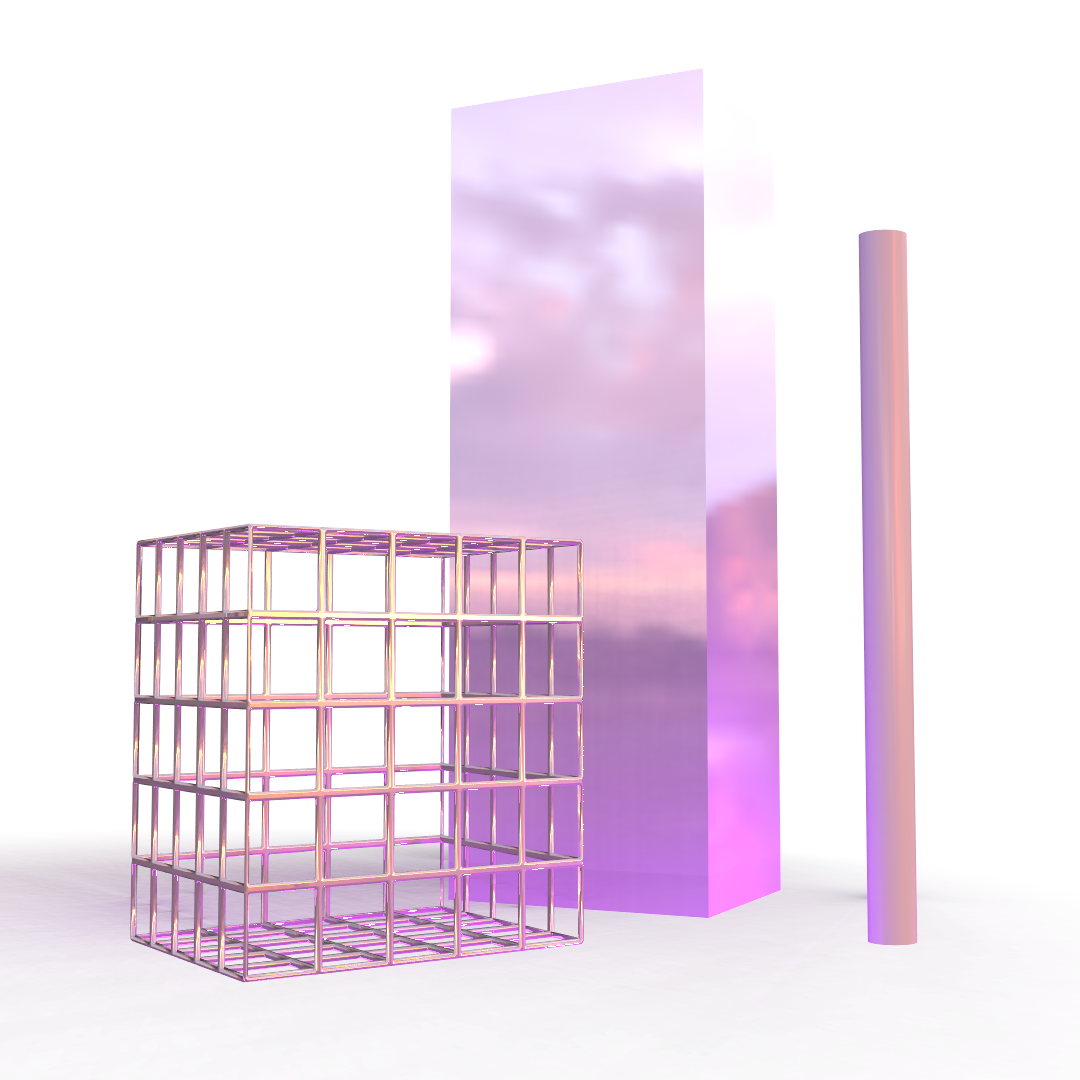
In a recent trial with English Heritage, NavVis was able to map a 56,000m2 castle in just 2.5 hours
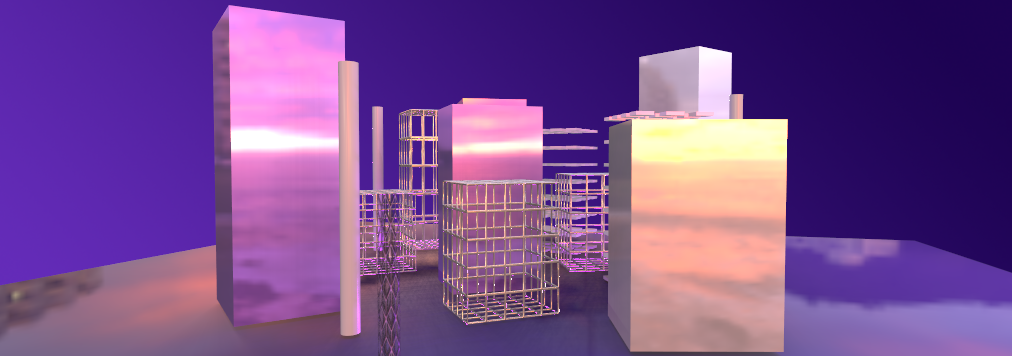
Automating retrofit design
The non-uniform nature of existing buildings, where additions have often built up in stratified layers over time, can cause a headache for designers used to the high level of automation and repeatability possible when developing new build projects.
BIM software tools typically hit a stumbling block when it comes to existing buildings, as humans are required to draw in 3D structures and objects manually with time and cost implications.
PointFuse software tackles this problem by harnessing cloud computing to automatically generate 3D mesh models from masses of point cloud data to depict objects that can be selected, classified and manipulated. This reduces the size of 3D models by a factor of up to 100, says the company, enabling project stakeholders to share and collaborate on projects without the need for expensive computer hardware.
Point cloud registration – the process of aligning the many scans needed to complete a survey – is another traditionally labour-intensive process that requires surveyors to either use artificial targets or engage in laborious cross-checking and guidance to align adjacent scans.
The cloud-based platform Vercator, by Correvate, exploits algorithms to automate the registration process, accurately aligning point clouds from a series of overlapping scans.
The system spots multiple features within each scan and auto-aligns the data, delivering a service the company claims is 60-80% faster than manual alignment.
Capturing construction
When a project hits site, survey teams are increasingly asked to carry out construction verification to ensure accuracy against design intent as well as produce final as-built documentation before project handover.
“We're doing more and more construction verification on refurbishments,” says David Norris, technical director at Plowman Craven. “We might scan the building to support the original plans, then rescan post-strip out, for example, to check that the design of a new heating and ventilation system will fit. It means off-site manufacture becomes a really efficient process.”
Progress tracking tools, such as those provided by Buildots and Oculo, stitch together images captured by a 360-degree camera mounted on a hard-hat as an individual walks a designated daily route through the site. Using computer vision and AI, Oculo creates walkthroughs that users navigate through in a similar fashion to Google Street View.
Robotic dogs may even become a regular feature on construction sites soon. Autonomous machines like Spot, a canine robot by Boston Dynamics, or Scaled Robotics’ four-wheeled robot, can roam the site at night, carrying out detailed surveys when workers are tucked up in bed.
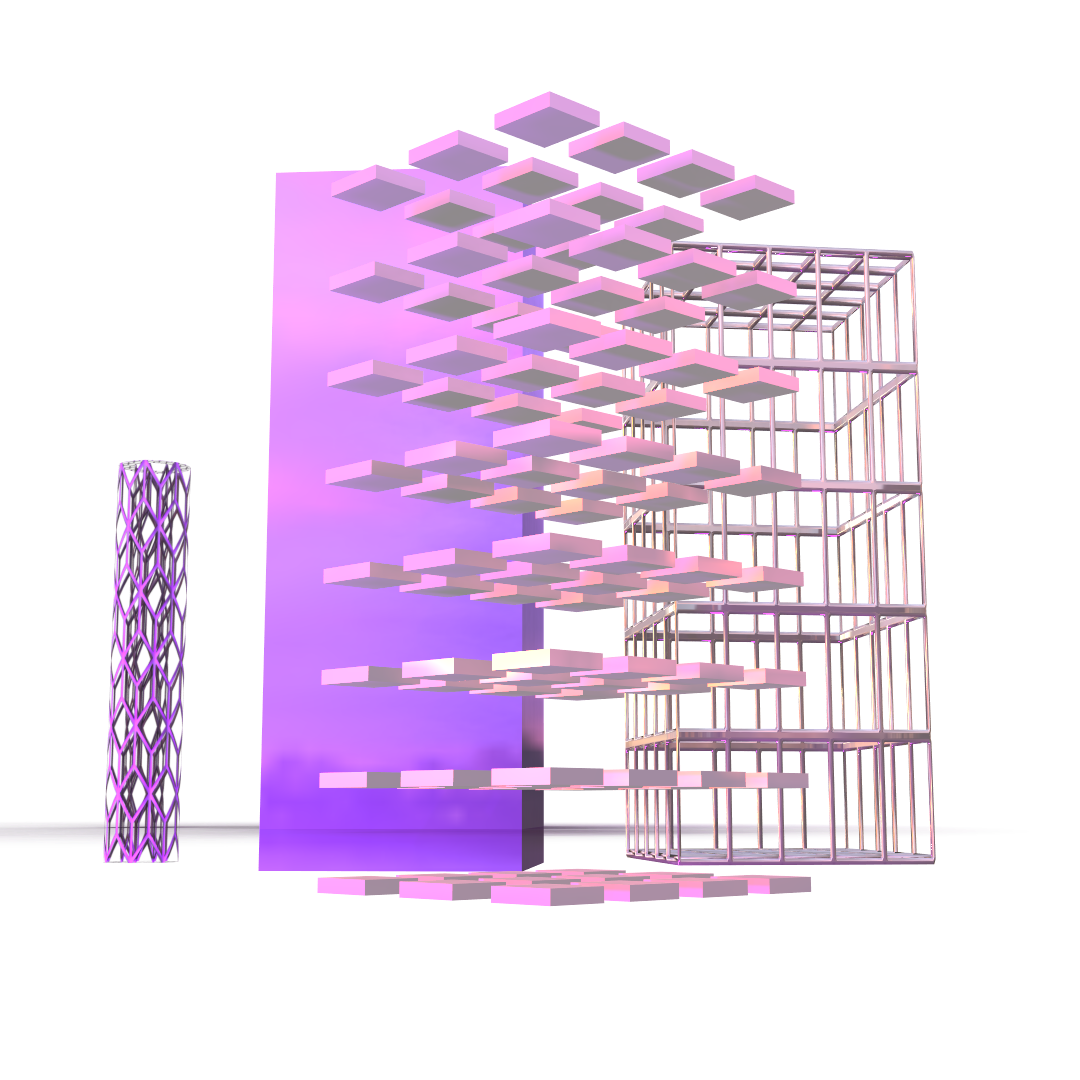
Progress tracking tools stitch together images captured by a 360-degree camera mounted on a hard-hat

Making historic buildings more sustainable
These five sites have benefited from sensitive retrofitting. Read more
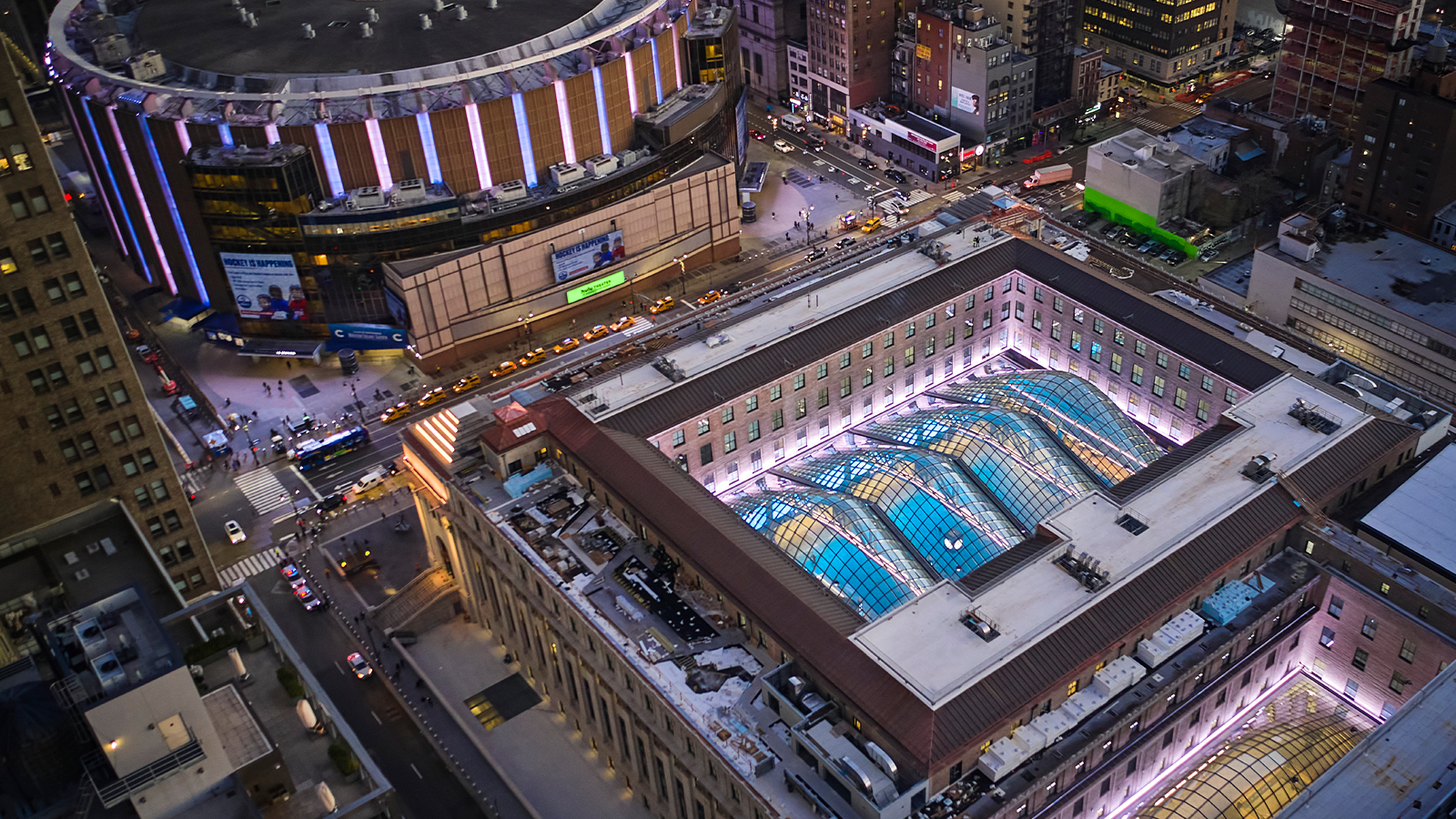