The Irish town of Drogheda is the unlikely setting for a building revolution. About 34 miles north of Dublin, it’s best known for a church that houses the head of Catholic martyr, Saint Oliver Plunkett. However, Drogheda is also home to the training centre for Harcourt Technologies (HTL), a company licenced to provide 3D printing methods in the UK and Ireland.
But these are no normal 3D printing methods – the sort used to manufacture, say, precisely calibrated medical implants or specialist engineering parts. HTL’s equipment was developed by the Danish firm COBOD (Construction of Buildings on Demand) and is currently able to print buildings up to three storeys high.
This enormous apparatus is, in essence, a nozzle that is connected to a pipe pumping through the printing mixture hung from a giant gantry that controls its movements. The gantries are able to slide as the building plan demands and the nozzle works its way along them, creating consistent layers of wall as it goes, like a giant cake icer. Surprisingly for equipment this size, there is something almost balletic about the nozzle’s movements, as it pivots and pirouettes. The walls, that have a distinctive layered finished can, if desired, be rendered to a flat finish or clad.
But it’s the speed of the process that promises a revolution. Once the apparatus has been set up – and COBOD says that this can be done in four hours by experienced technicians – the system can build a storey a day for an average-sized family house. That’s the outer walls and all the inner partitions too, with cavities left for insulation and openings for windows or doorways.
No labourers, no problem
“It addresses the labour shortage,” says Paul Kelly of HTL. “No one knows a bricklayer under the age of 45, no one wants to go into it. This gets around a major problem in construction.”
What is more, Kelly says, even the best bricklayers usually create very minor differences to the original plans – making the window openings, for example, slightly narrower than stipulated by cutting bricks unevenly due to natural human error. The developer must then wait until the shell of the building has been finished and all the openings can be remeasured before the windows and other fittings can be ordered. This could add several weeks to the completion date. Using a printer, however, is extremely precise and everything can be ordered in advance with confidence that it will fit. The building can be made watertight in days rather than weeks or, given supply line problems, even months.
There are also claims made about the technology’s sustainability. Essentially, the COBOD printer uses cement to build its walls. Kelly concedes that this material has huge amounts of embedded carbon but argues that the fact that it can generally be bought locally means that it has fewer transport miles.
“Our mission is to build faster, cheaper, better and more sustainably,” says Philip Knudsen, COBOD’s CMO, from the company’s HQ in Denmark. “The CO2 footprint [of our buildings] has gone down 50% in the past few years and it will go down a further 50% [from its current point] in the next year or two.”
The company is able to do this by having developed a technology that allows concrete rather than pure cement to be used for printing (this is more complicated than it sounds as it is difficult to balance out the smooth printing of the material with the aggregates typically found in concrete). “It’s cheaper as well as having a smaller carbon footprint,” says Knudsen.
Kelly says that the National Graphene Institute in Manchester is also researching whether graphene can be used in the printing mix – graphene has exceptional insulating properties as well as strengthening concrete.
There is also research being done into making the concrete mix more sustainable. In India, Sobha Rani FRICS, a research scholar at RICS School of Built Environment, says there are studies looking at incorporating bamboo and recycled plastic to bring down the embedded carbon. Likewise, costs are coming down as the technology becomes more widely available. “The price is probably the same [as a conventionally built house],” says Knudsen. “In a couple of years, I expect it to be 20% below that.”
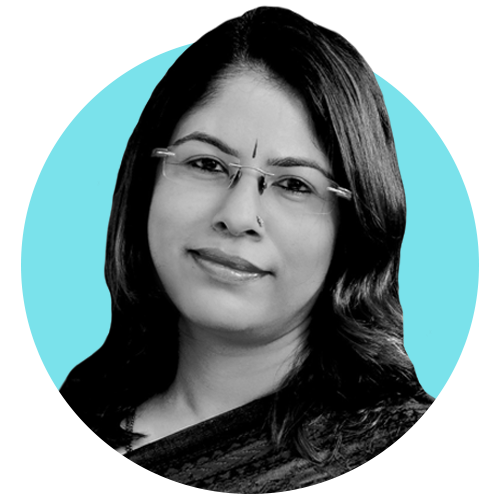
“The training of skilled workers is a problem that will affect viability” Sobha Rani FRICS, RICS School of Built Environment
Slowly gaining attention
Costs and speed of construction make it very attractive. “It connects very well to BIM,” says Rani. In India, where the government has set ambitious house-building targets, such technology would seem a natural fit. There was a two-storey, 65m2 unit built recently in Chennai, but the system has yet to be rolled out on anything approaching a commercial level. “The training of skilled workers is a problem that will affect viability,” Rani concludes.
It's a similar story in the UK and Ireland, where COBOD projects lag well behind many other countries. There are videos of COBOD builds that have taken place from Angola to Borneo. In the US, the gantries are being set up in remote areas to build in situ enormous wind turbine bases too large to transport by road.
So why, given its falling costs, shrinking carbon footprint and impressive speed aren’t COBOD gantries a common sight? HTL had a large 46-unit housing association project lined up near Accrington, Lancashire, in north-west England, only for it to be delayed by increased funding costs. Kelly says that another project is in the process of being finalised in Ireland but, as yet, nothing has been built.
Knudsen and Rani both feel that until specific building regulations are adopted for COBOD projects, then developers can be nervous of the system. For example, although the structures can be self-supporting up to three storeys, some jurisdictions have insisted reinforcements are used. There is also a general suspicion of automation in an industry that has – traditionally – relied on having workers skilled in specific areas.
This is not stopping COBOD: Knudsen says that the company is looking at ways of further automating the build process so that, say, insulation can be done by machine. Kelly, meanwhile, says that it has the potential to open up construction to a wider workforce: “It’s very inclusive. We want to get to an even split of male and female workers. Ultimately, someone in a wheelchair can operate the laptop that controls COBOD.”