The cost of building materials remains volatile around the world, as global economies swing back into action after a year of lockdowns. Supply isn’t meeting demand but it’s not just the increased number of building projects creating a shortage, there are political and trade issues at play too.
To find out more about what’s behind the increased cost of essential materials, we asked three experts, based in the US, Hong Kong and Australia, to explain.
The view from North America
“What’s happening is that a number of projects are coming back on-line as developers feel more confident about the easing of the pandemic and, as a result, we’re seeing an increased demand on resources,” says Mark Fergus FRICS.
“Here on the West Coast, we build using timber frames because of the seismic needs of the area and the impact of the pandemic on lumber has pushed costs up by 56%. This is partly due to the US not ratifying an agreement with Canada for the supply of soft timber but also, of course, during the pandemic, many of the sawmills here were closed down and then we had wildfires that stopped production too.
“There was a hope that there would be a softening in the price of materials as China came back but a lot of the materials manufactured there are staying. Steel is starting to rise, but on the flipside, domestically-produced elements such as glass aren’t increasing very much, maybe 2%, so that’s a little bit more secure. Then you add in the effect of disruption in logistics – only about 25% of containers are in the right place so that means an increase in costs from about $900 pre-pandemic to $3,000 now.
“Even though construction has been considered an essential business and has largely continued, it’s the supply chain impacts that are causing these increased costs. The AGC [Association of General Contractors] issued a warning a couple of months ago that, as material costs grow, you could see margins being eroded for contractors who have been very aggressive in their pricing. There is a fear that some of them could be heavily impacted and making a loss and perhaps they have to increase pricing to cover some of these short-term losses.
“What we’re going to see over this next quarter are increases in pricing, perhaps into the third quarter, and then I think we’ll be into a normal environment of 3-4% increase in the prices of materials and other demand-led resources. It’s basically the restart of [the economy] that’s creating this spike at the moment, but I think it should start to level out at the end of this year, beginning of next.
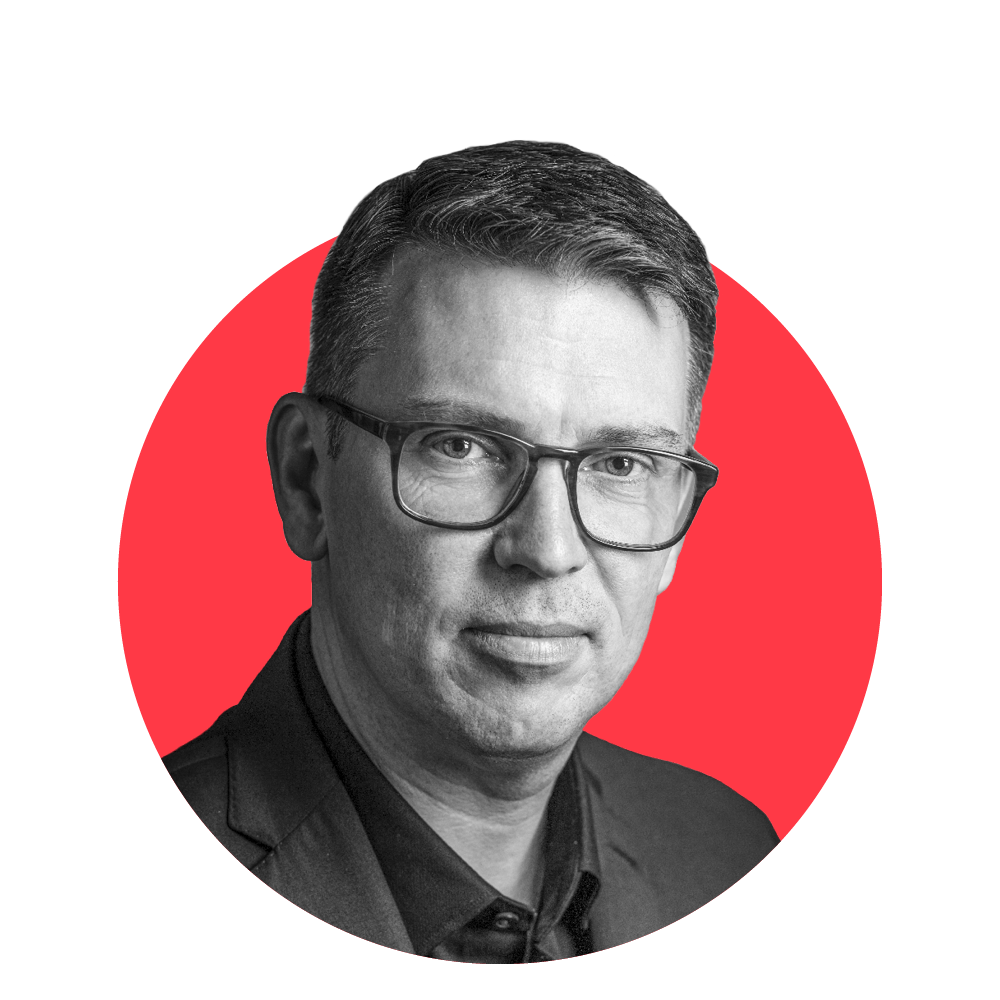
Mark Fergus FRICS is regional vice president at construction management consultancy Cumming, based in Los Angeles.
The lay of the land in Hong Kong and China
“It’s a tale of two halves,” says Rodney Moulder MRICS. “If you look where we were at the start of the pandemic, there were a lot of lockdowns across China, and the impact was across the supply chain as factories shut down, culminating in extended lead times for products sourced from the mainland.
“Where we had got to by the end of last year was that China had opened again and production was pretty much getting back to full capacity. There have been some spikes and hotspots in China in terms of COVID-19 cases since the end of the first quarter of 2021 and what that’s done is increase the lead times. But generally, while the small intermittent lockdowns have increased supplier inventories, production has continued returning to normal.
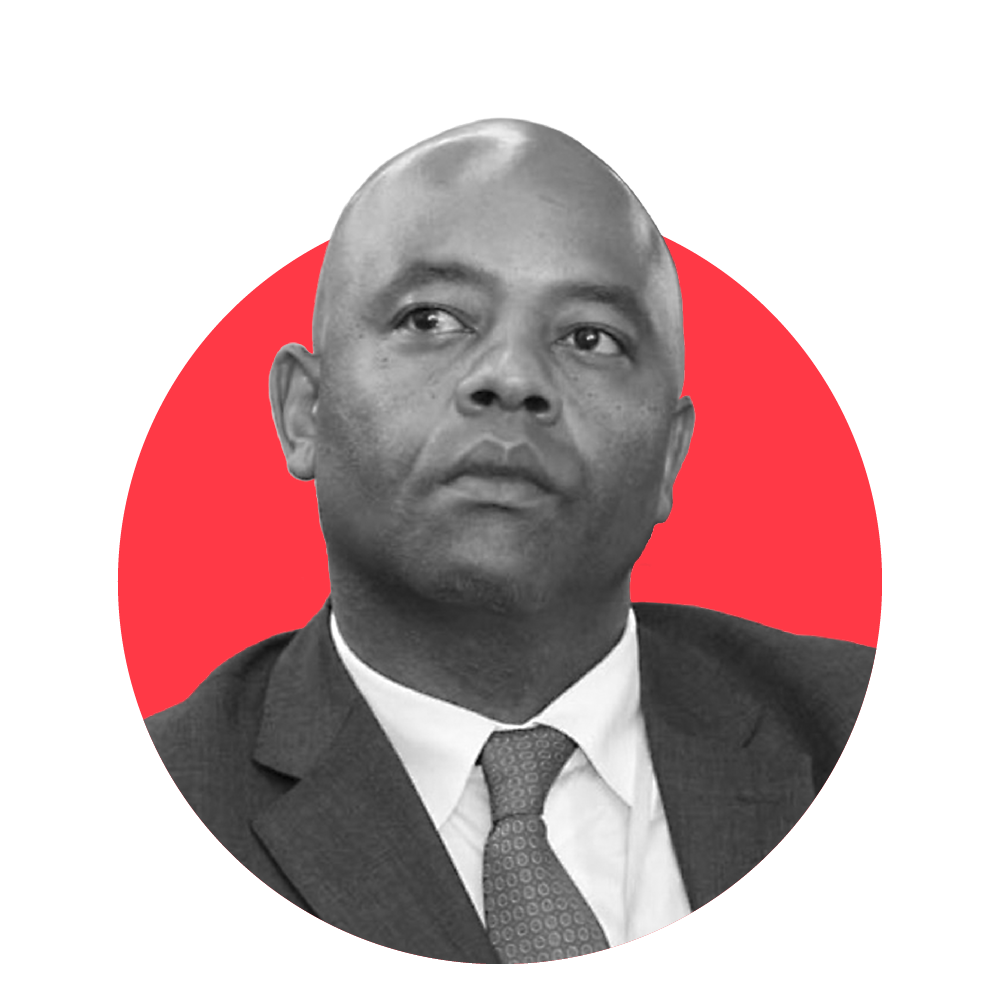
Rodney Moulder MRICS lives in Hong Kong and is head of real estate for the consultancy Turner & Townsend, focusing on China’s Greater Bay Area.
“Although China is quite a big producer of steel, the reduction of raw materials coming in from say Australia in the past few months has had an impact both on supply and cost. We’ve also seen other materials such as low-iron glass increase in price in the past year so there’s been an impact on facades with upward price movement of maybe 5-10% during the last quarter of 2020.
“In some parts of the country, we have seen transportation and logistics being affected by highways being closed because of mini-lockdowns. This has resulted in some factories being more cautious around the rate of production - they’re trying to avoid cash-flow problems tied up in building up inventories that they might not then be able to export out quickly enough. The benefit for China is that we’re in the same jurisdiction so it’s not a problem getting materials from one part of the country into, say, Hong Kong.
“Now, there are some products seeing lead times increase from 6-8 weeks to around 10-12 weeks, but this is not happening across the board and with all the government support and commitment to stimulating the economy, the projects are there and still going on so, at worst, it’s resulting in slightly longer project durations.
“The impact on materials is probably more pronounced in western markets with a heavy reliance on products coming from China – I would estimate about 30% in the US and Europe although it depends on the material: steel or electrical products are heavily reliant on supply chains in China. There is likely to be pressure on building suppliers in those regions as they come out of lockdowns and they look to replenish their stocks which could see upwards pressure in prices from a supply and demand perspective. Parts of Asia have in part been somewhat more fortunate in relation to the severity of the lockdowns – which has allowed our economies to remain relatively open.”
The situation in Australia
“At the end of January 2020, we heard about this thing called COVID-19,” says Nick Deeks FRICS. “A lot of Australia’s building materials come from China so, when their factories shut down, there was a scramble by contractors to order from Europe. But the pandemic spread so fast that the lead time between placing an order and waiting for it to arrive from Europe increased and then Europe suddenly became a COVID-19 hotbed. Fortunately, China got on top of the pandemic quickly and it wasn’t too long after that that the Chinese factories started to reopen.
“In Australia, the government moved quickly and closed the country off to overseas travel. We stayed pretty coronavirus-free so by 4 May 2020, our Perth offices started to reopen and others soon followed apart from Melbourne which remained in lockdown. Construction was classified as an essential service, so it just continued albeit with social distancing requirements. There really weren’t that many delays and, as strange as it might seem, there wasn’t a major impact.
“There hasn’t been much price escalation for materials. As we stand today, all sectors are looking busy and there’s a labour shortage because we can’t bring people in, and that, together with EBA bargaining [collective negotiations] means productivity issues and labour prices increasing. It’s labour costs that are our problem – we have a huge amount of activity in the mining sector, workers can go to the mines and get a huge increase in wages so, to retain staff in other sectors, we need to pay more.
“Material prices, particularly steel have started to rise in the past couple of months, due in part to South American iron ore mines shutting down. It’s up about 5-10% on everything from sheeting to nuts and bolts. But generally, it isn’t dramatic: we might be at 2.5 to 3.5% - but the long-term average (over a 10-year period) in price rises in Australia is about that every year anyway.
“The Australian fires caused more of a problem because there was so much housing that needed repair and replacement, parts of New South Wales were decimated. Materials required for domestic housing are in demand down there – there is a global shortage of black butt timber [which is used extensively in Australian homes] as it’s being bought up by the US to feed their housebuilding boom. It’s really hard to get materials into the country by container ship because the government has brought in measures that disincentivise transporting waste materials overseas and that has meant freight costs have risen dramatically and we have containers piling up over here, not going back to the destinations that we need to import from.
“There have also been a few trade skirmishes with China over the past year or more and that will start effecting building materials, but not so far. We do have a huge reliance on Chinese materials, and this whole situation should open our eyes to the dangers of putting all our eggs in one basket. We should diversify our supply chains and our manufacturing too. But part of the problem is that it is so expensive to do it here because labour prices are going up so much and we need to get materials from the cheapest possible source.”
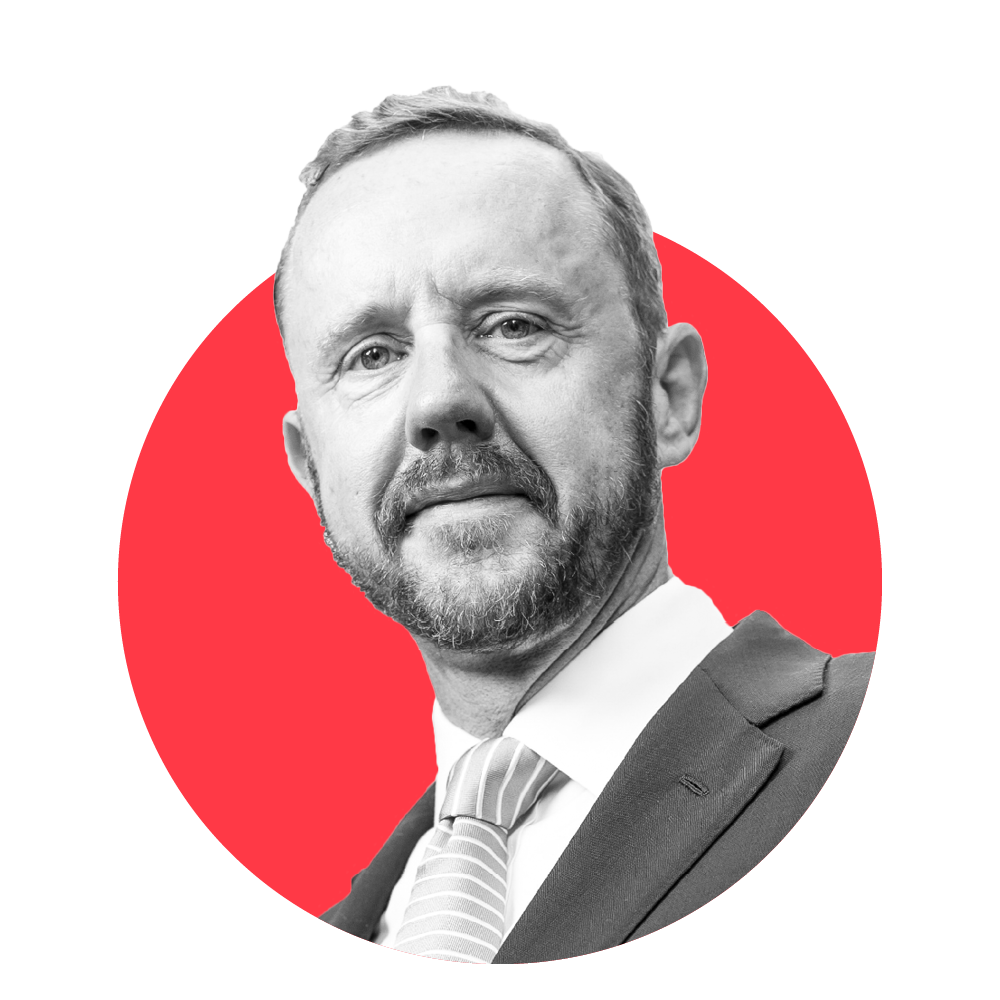
Nick Deeks FRICS is based in Sydney, where he is managing director of WT Partnership Quantity Surveyors and Construction Cost Consultancy.

Construction materials: December 2021 latest
The RICS Construction Journal updates on the perfect storm of demand, delivery delays and COVID-19 Read more
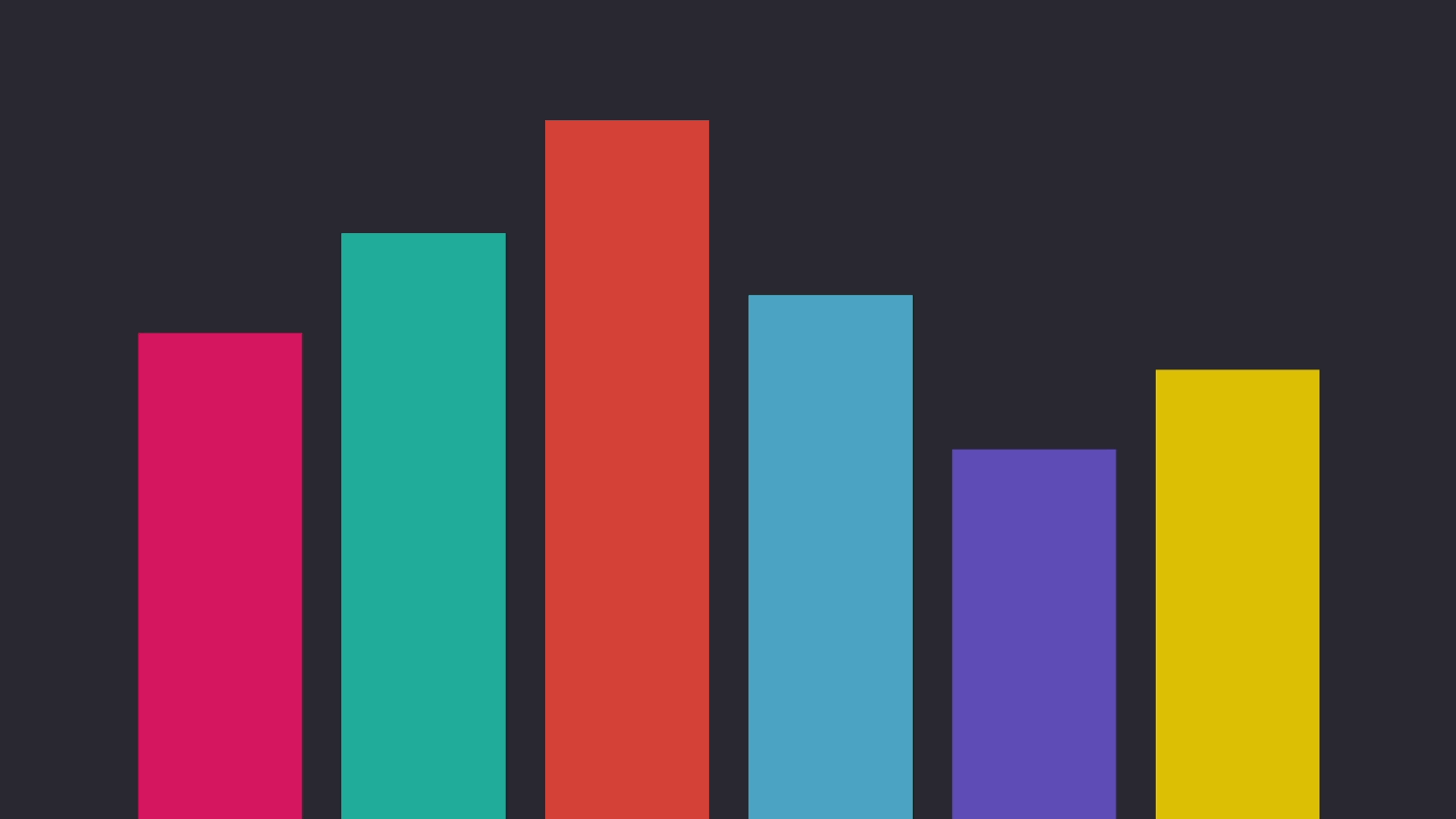