Thames Tideway Tunnel beneath central London
London's Victorian sewer system was originally designed to carry the waste of up to 4m people, not the dirty discharge of nearly 9m people living in the capital city today.
Overloading of the ageing network means that even a light shower of rain can cause raw sewage to spill into the River Thames and on a stormy day most of it ends up polluting the waterway.
Only the construction of a super sewer would be sufficient to tackle these problems, and at 25km long and 7.2m in diameter, the Thames Tideway Tunnel is precisely that.
The £4.1bn project, being delivered by the consortium Tideway for Thames Water and due for completion in 2025, is designed to clean up the Thames for at least the next 100 years and accommodate the combined impacts of population growth and climate change.
Roughly following the course of the river, between the Borough of Ealing in the west and Newham in the east, it will intercept Combined Sewer Overflows (CSOs) from three main 'drive sites' at Fulham, Battersea and Bermondsey, plus a number of smaller sites.
The sheer scale and cost of the project provided the catalyst to roll out around 30 innovations, including a range of new processes and technologies designed to boost productivity and efficiencies in design and delivery. A dedicated Innovation Forum was set up to identify and seed fund ideas and bring them to fruition.
Roger Bailey, chief technology officer at Tideway, says: “From the word go, we wanted to be an intelligent, informed and involved client. We weren't simply looking for a finished asset delivered by the contracting world as quickly as possible. We saw it as an opportunity to help the British construction industry put certain things right, and at the very least build on improvements introduced by other projects.”
Financial engineering
Tideway is significantly larger and more expensive than the biggest infrastructure project delivered to date by Thames Water, the £635m Lee Tunnel overflow sewer in East London.
Unable to bear the full costs itself, mainly due to the financial risks related to complex heavy civil engineering work, the utility developed a completely new method to deliver a major project – conceived to reduce risk and lower the cost of capital.
The project is financed and built by a separate entity, the Tideway consortium of investors, rather than by Thames Water itself. The regulator, Ofwat, oversees costs to ensure the taxpayer gets value for money and the government has committed to step in with financial support if expenditure exceeds a certain threshold.
The unique set up means Thames Water can collect revenue during construction, once Ofwat signs off on calculations. This is unlike other public infrastructure projects, such as a toll road or a railway, which only generate income when they are operational.
This mechanism managed to bring down the impact on customer bills, from an anticipated £70 to £80 per year in 2011, to around £20 to £25 today, “even taking into account adverse impacts to our capital costs, such as COVID-19,” says Bailey.
Nevertheless, the additional cost will be a burden to some residents and the decision to charge customers at all for the tunnel has its critics who believe shareholders should be footing the bill.
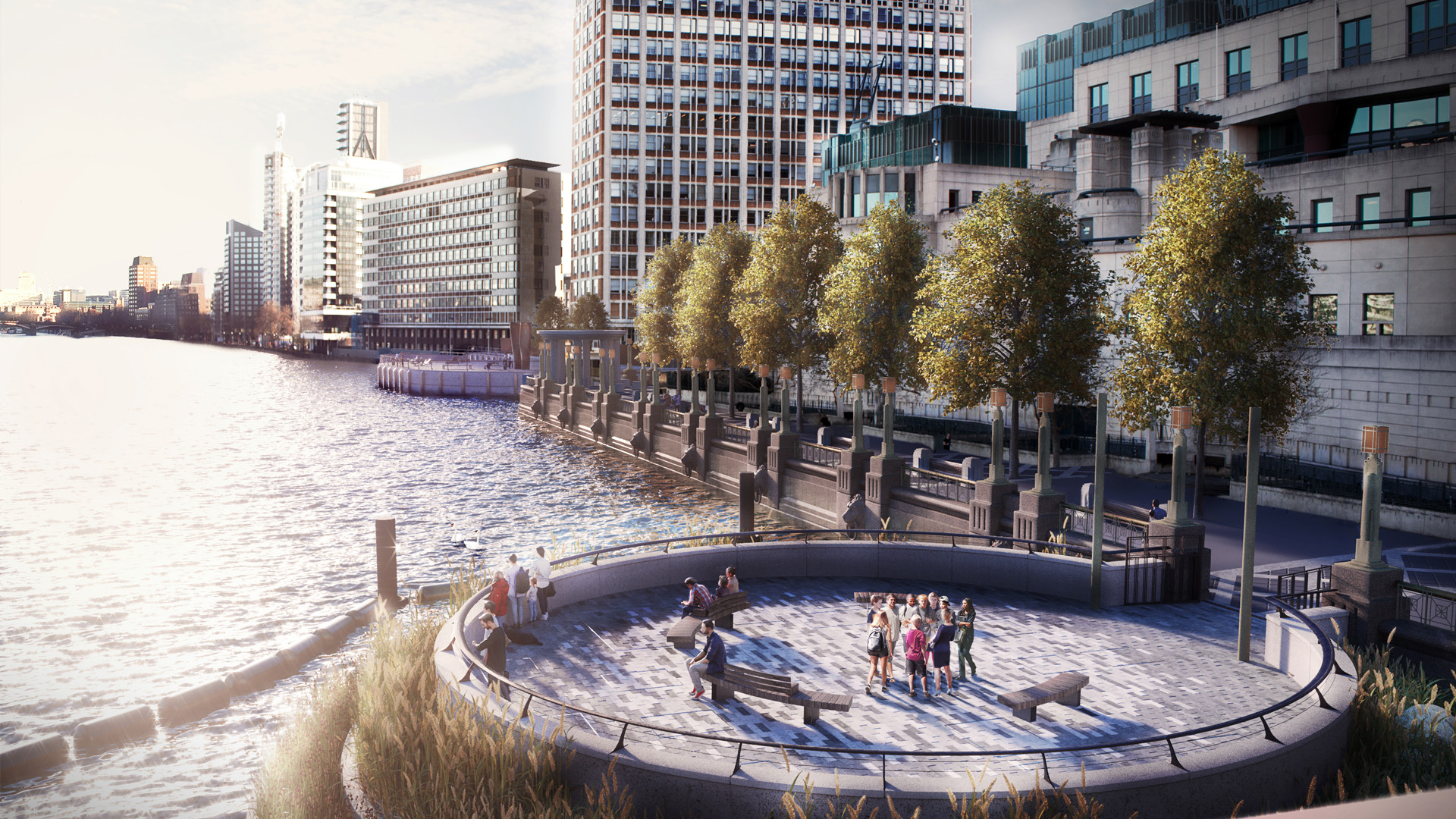
Thames Tideaway project
Built to last
Tideway will intercept at least 94% of sewage overflowing into the tidal Thames every year and capture all the ‘first flush’ from the sewers after heavy rain.
Innovation in the tunnel design focused to a large extent on the need to enable large volumes of effluent to travel long distances at speed without causing damage or erosion to the infrastructure itself.
Cavitation, caused when liquid cascades into deep intercept shafts, eroding the concrete at the base, was a particular concern. For example, the intercept shaft at Blackfriars Bridge could receive up to 50m3 of water per second, equivalent to emptying an Olympic size swimming pool in 50 seconds.
The need to transfer flow from high to low level in a more controlled manner informed the development of an innovative ‘vortex’ design. Flows entering the shaft are accelerated down a slope before being spun into a smaller tube inside the shaft, similar to tap water going down a plug hole.
Unique to Tideway is the scale of the vortex drops, the largest being over three metres in diameter. Air entrained in the flow has to be kept to a minimum as air pockets can cause serious issues.
As Bailey explains: “In the deep tunnel excess air entrained in the sewage liquid can form into highly pressurised pockets, which if left could push whole columns of water out of the top of a narrow shaft. Some cities have experienced dramatic effects, such as manhole covers blown across several blocks, or trucks and cars being flipped over.”
Tideway’s shafts are sized to allow air to escape from the flow, while in-shaft and in-tunnel deaeration, including a stilling basin at the base of the shaft, slow sewage velocities down to encourage air to exit the flow. A limit of 1% entrained air was set by Tideway, based on extensive physical modelling.
“You can't simply focus on all the great things we’ve achieved, sometimes you've got to be prepared to put some money down to find out if things work or not.” Roger Bailey, chief technology officer at Tideway
On-site streamlining
Constructing the super sewer is a herculean task and, similarly to Crossrail, tunnel boring machines (TBMs) excavate the tunnel and lay precast slabs around the inside to give it strength.
A unique digital innovation saw a 3D BIM model of the tunnelling works developed to enable crews to familiarise themselves with the route and how to reconfigure the machine when in build mode.
“It's not normal practice for a client to specify a BIM model for a piece of temporary works,” says Bailey. “The contractors found it very useful to go through processes with operatives who weren't necessarily familiar with working underground.”
A virtual reality ‘cube’ was installed at one of the three main drive sites (where the TBMs are lowered into the ground) to enable teams to carry out constructability reviews of planned work sequences. In one example, the system visualised the steel reinforcement cage for the thick reinforced concrete plug needed at the bottom of each of the intercept shafts.
When steel fixers saw the complex arrangement at one-to-one scale, they realised extra bars were required to maintain and improve stiffness. The ability to experience and adapt the design averted a potentially serious safety incident, says Bailey, and the £30,000 outlay for the technology was more than worth the estimated £1.4m it has saved in time and effort on the project.
On-site innovations didn’t stop here, efforts to improve health & safety awareness included the creation of a dedicated employers’ project induction centre where all workers experience a staged version of a fatal accident, using actors and realistic audio visuals, and see the ramifications on the person’s family and colleagues.
Tideway is using the river to transport materials at a scale unprecedented in modern times. Deploying tugs and barges will reduce total HGV journeys from over 500,000 down to just 140,000, with a corresponding impact on air quality.
Learning lessons
The best laid plans of major construction projects have been known to go awry and some innovations spearheaded on Tideway haven’t worked out.
For example, around £10m was spent on a series of trials and a prototype for a precast secondary lining for the tunnel, conceived as a much faster alternative to casting in situ and to be laid over the primary precast system installed by the TBM.
The method was validated, but its speed couldn't be verified in time to push the button on investment, so instead the team had to settle for the cast in situ approach.
Nothing ventured, nothing gained is a saying that resonates in this case, says Bailey: “You can't simply focus on all the great things we’ve achieved, sometimes you've got to be prepared to put some money down to find out if things work or not.”
With the super sewer’s completion now in sight, after significant delays brought about by the pandemic, Londoners can look forward to getting their river back in a greatly cleaned-up state. But will the water be safe enough to swim in?
“It will still be a dirty old river, there's lots of silt, it will be muddy and I wouldn't drink it. But people are definitely going to find it a much more pleasant place to be,” Bailey concludes.
"Sewage liquid can form into highly pressurised pockets … some cities have experienced dramatic effects, such as manhole covers blown across several blocks, or trucks and cars being flipped over.” Roger Bailey, chief technology officer at Tideway
A brief history of the Thames River
1608 to 1814 – In winter the Thames often froze completely and ‘Frost Fairs’ were held on its surface.
1858 – A period known as the Great Stink, when a hot July and August intensified the smell of untreated sewage and human waste on the banks of the river.
1957 – The Thames was so polluted that the Natural History Museum declared it was “biologically dead”.
1960s – Laws are made to prevent industrial discharge into the Thames, the river is cleaned and marine life slowly returns. Today it is considered to be one of the cleanest rivers to flow through a major city in the world.
1983 – The Thames Barrier is first used, to help prevent flooding.