In the latest in a series of articles examining efforts by heavy industries to decarbonise the production of building materials, we consider aluminium, a metal increasingly relied on for construction around the world but responsible for 2% of all human-caused greenhouse gas emissions.
Aluminium is often referred to as the ‘green metal’, thanks to its high strength-to-weight ratio, long lifespan, corrosion resistance, and the fact it can effectively be recycled forever, melted down and reformed without losing quality.
But the environmental credentials of the versatile material are severely let down by its carbon footprint. The aluminium sector generates around 1.1bn tonnes of CO2 per year, largely because of reliance on energy-intensive smelters.
With demand for aluminium expected to grow by more than 50% by 2050, driven by major industries including construction, transportation and power transmission, efforts to clean up its heavy industrial processes are more pressing than ever.
According to a new report by the International Aluminium Institute (IAI), which represents more than 60% of global aluminium production, most CO2 emissions (more than 60%) derive from electricity consumed during smelting. China is a particular offender because of its heavy reliance on captive coal-fired power plants.
Decarbonised electricity generation therefore offers the biggest opportunity to reduce emissions in the sector to near zero by 2050, according to the IAI, alongside the deployment of carbon capture utilisation and storage (CCUS) technologies, still in development, that suck up emissions and either store them underground or turn them into new chemical products.
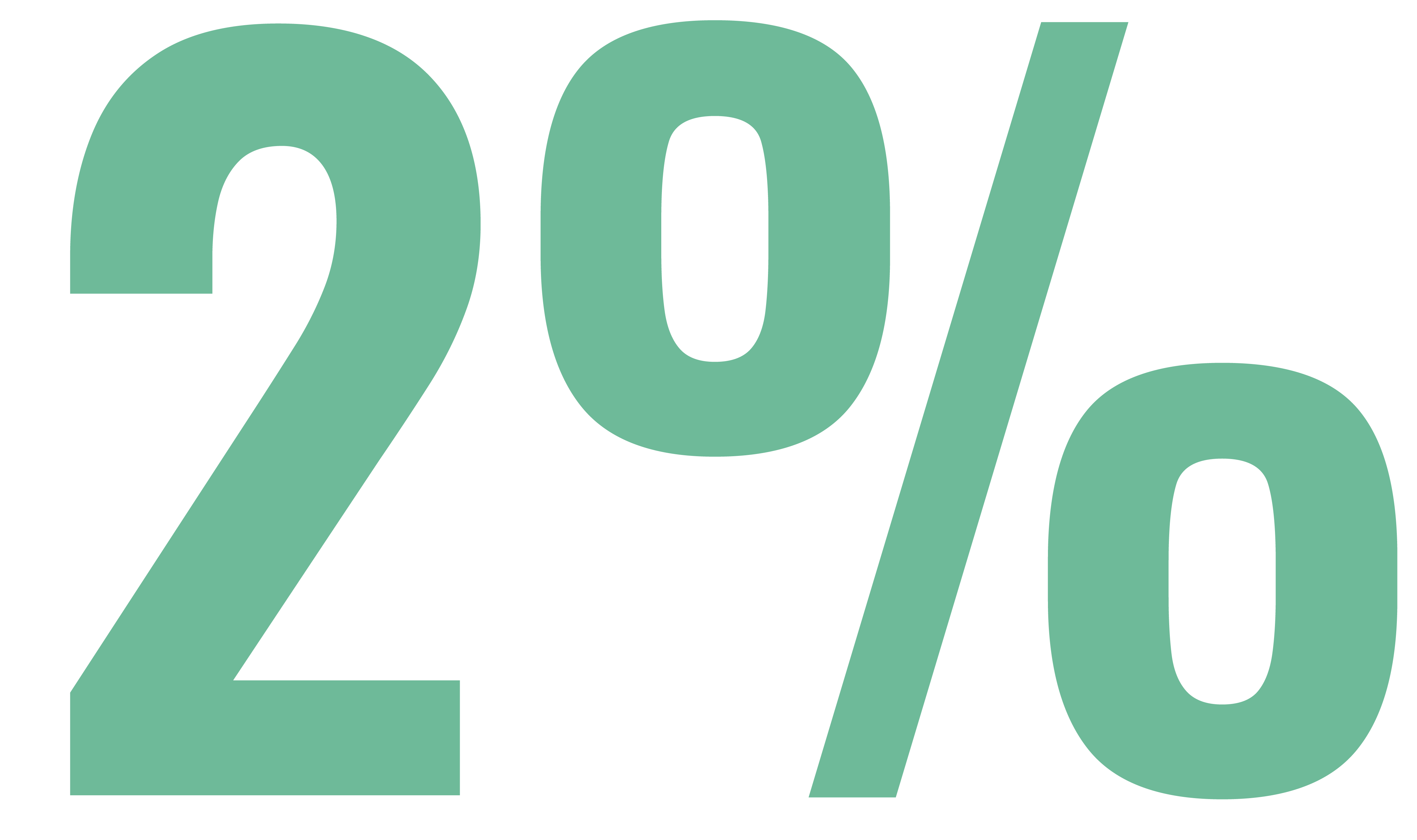
Aluminium accounts for 2% of all human-caused greenhouse gas emissions each year
Renewable energy is the key
Renewable hydropower and geothermal energy can provide continuous 24/7 power and have a key role to play, says Pat Hermon, technical lead on sustainable products at The Building Research Establishment (BRE): “Aluminium production has always been an electricity-heavy manufacturing process and smelting plants are often located close to hydroelectric schemes because they are the only place to get power affordably. We need to be building factories close to sources of renewable energy. Iceland has vast access to geothermal energy that can potentially be used very cheaply.”
The world's largest aluminium producer China Hongqiao Group started production at a new hydro-powered aluminium smelter in Yunnan last September. It is the first of several projects to relocate Chinese aluminium production close to hydropower sources to support the nation’s decarbonisation targets.
Massive solar arrays (collections of multiple solar panels) are also transforming generation in many locations around the world. The Mohammed bin Rashid Al Maktoum Solar Park in the UAE will be used by metals group Emirates Global Aluminium to manufacture the world's first ‘solar aluminium'. Its smelter will draw 560GWh from the park annually and produce 40,000 tonnes of green aluminium, for export to markets worldwide, in the first year.
CCUS is often regarded as a ‘magic bullet’ solution, able to remove harmful gases while simultaneously allowing plants to remain dependent on fossil fuels. However, most CCUS technologies remain at pre-commercial scale and years away from mass adoption, which potentially make them unfeasible in the current climate emergency.
Runeel Daliah, analyst at Lux Research says: “With the right market conditions (such as low-carbon incentives), CCUS technologies can be successfully scaled up and validated by the mid-2030s, which leaves around a decade or two for widespread adoption. However, other technologies, such as electrification of industry, provide higher decarbonisation potential.”
Outside of power consumption, direct emissions from aluminium processing are another high-impact activity, which in 2018 accounted for a combined 25-30% of sectoral emissions. These are principally caused by the electrolysis of alumina using a carbon anode during smelting, as well as fuel combustion during refining to produce heat and steam.
Using an inert material in place of carbon in anodes could eliminate direct emissions from electrolysis and several aluminium producers are working to develop anodes that produce oxygen instead of CO2. Phone maker Apple is a major investor in one such joint venture.
The capital costs of inert anodes are projected to be 10–30% less than carbon-based equivalents, however this clean form of electrolysis is more energy-intensive, further underlining the need for renewable sources of power.
Heat and steam, needed to convert the raw material bauxite into alumina, are primarily generated using fossil fuels, which could be substituted for solar water heaters, biomass, geothermal, green hydrogen and concentrated solar power, all of which are being investigated.
Canadian start-up Eavor Loop is aiming to commercialise affordable and dispatchable baseload geothermal energy by 2030. Unlike conventional geothermal methods, the closed-loop system allows water to be pumped 3–5km into the ground and circulated to convert it into steam to spin turbines. According to the firm, it requires no fracking, no water use and no dangerous aquifer contamination.
Aluminium is an almost infinitely recyclable material and around 80% is already taken back into production. But according to IAI estimates, optimising efforts to capture the remaining end-of-life scrap could reduce the need for primary aluminium by 15% and save an estimated 250m tonnes of CO2 each year. Such initiatives, coupled with necessary R&D investment and wider stakeholder support, will be crucial if aluminium is to truly fulfil its potential as the green metal of the future.
Get Modus features sent straight to your inbox by signing up for the newsletter.
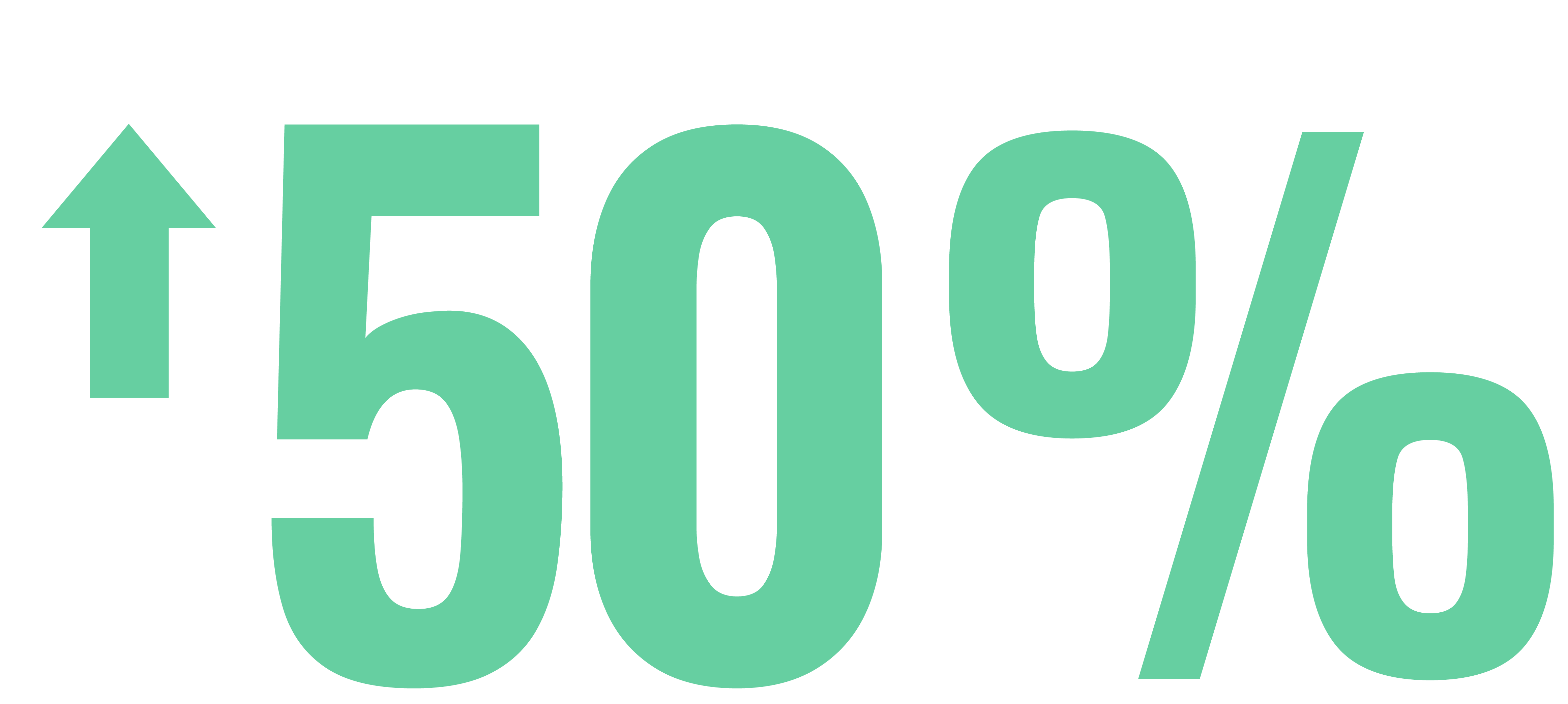
Demand for aluminium is expected to grow by more than 50% by 2050