Juf Nienke, courtesy of SeARCH
When Legal & General (L&G) announced in May 2023 that it was ending production at its factory near Leeds, commentators said the writing was on the wall for modular housing companies in the UK. Not only that, but there would be an impact on the wider MMC (modern method of construction) sector.
The move by the financial services and asset manager to call time at the 51,100m2 factory in Selby, West Yorkshire, was put down to planning delays and economic woes. Estimates suggested the modular housing business had suffered losses of £176m since it began in 2016. In a statement, L&G Modular Homes said it had “not been able to secure the necessary scale of pipeline” to reach its 3,500 homes a year target.
In recent years, a slew of other closures has also hit the UK’s off-site manufacturing market. In May 2022, Urban Splash’s modular joint venture with Japanese company Sekisui and Homes England collapsed – with administrators citing “operational issues” at its Alfreton factory. Caledonian Modular entered administration in March 2022, with F1 Modular seeing the same fate two years earlier, as both struggled with costs. And as recently as June 2023, Yorkshire-based Ilke Homes entered administration with the possibility that the majority of the company’s 1,100 staff would be made redundant.
This has all added up to questions about the long-term future for a sector still considered fledgling in the UK, against more mature and established sectors in Scandinavia, Japan, China, and South Korea. Globally, the modular construction market size was worth $75.9bn in 2021, and that is expected to jump to $114.8bn by 2028, according to Fortune Business Insights.
However, many working in the UK MMC sector believe it’s in better shape than L&G’s travails would lead you to believe.
Still on track
“We’ve run our numbers, and the sector is still in a good place,” says Steve Cole, director of Make UK Modular, the trade body that represents the UK’s largest modular firms. “We have this target, and our mission is to enable the sector to deliver 30,000 modular homes a year by 2030, and we still think that is still very much on track.”
Richard Valentine-Selsey, head of European living research and consultancy at Savills, echoes the positive sentiment. The L&G Modular Homes (LGMH) news is “obviously going to lead to an element of reflection in the market,” he says, with developers and investors looking carefully at who they’re working with, as well as the potential risks.
But, he adds, “it’s not going to change the overarching direction of travel that more people will eventually be using MMC.” An ageing workforce, climate crisis, and the need to deliver more homes quickly are all macro-economic elements pushing the housebuilding industry to look at different ways of construction.
Governments around the world have favoured MMC to supplement skills gaps in traditional construction, says Timothy Snelson, director at Arup. He adds that a “presumption in favour of MMC has helped change perceptions and open minds to the opportunities.”
“It’s the way forward, not only for speed and quality but also health and safety” Tim Harris MRICS, JLL
Photos of Hotel Jakarta, courtesy of SeARCH
Growing the sector
Pointing to the amount of investment coming into the sector, Valentine-Selsey says: “There are a lot of positives to look at.” But, he adds, for the sector to be a success “you need to have a large pipeline of work coming through the factory to make sure it’s running at a high enough level to make it financially viable.”
Last November, Sir Nigel Wilson, L&G’s chief executive, admitted the company was at “20% of where we want to be,” when speaking about the impact of planning delays on LGMH’s long-term growth trajectory.
Valentine-Selsey’s prediction is that the market will become consolidated with “a handful of large manufacturers who are able to deliver those [bigger pipelines] … and smaller niche ones doing bespoke projects.”
He adds: “You could potentially see hybrid models becoming more attractive because you’re not signing everything up to one manufacturer. You are spreading your risk from being reliant on a single company that if they go bust for whatever reason, or have issues, then your whole project is stuck.”
When asked if surveyors can expect to see more buildings constructed in the hybrid method – a combination of modular and site construction – Tim Harris MRICS, operations director, UK PDS at JLL, says: “I hope so. It’s the way forward, not only for speed and quality but also health and safety. However, the forces of supply and demand take over and likewise viability of the end product. We need to embrace the MMC mindset or re-invent it.”
“The big picture stuff, the main drivers for modular, are still firmly in place,” says Cole. “That’s reflected in several other providers ratcheting up their delivery and investment levels. So no, I don’t think the writing is on the wall for the sector.”
Case study: Hotel Jakarta, Amsterdam
The Netherlands is enjoying the continued success and influence of being a modular pioneer.
In 2018, the 16,500m2 200-bed Hotel Jakarta, designed by SeARCH architects for WestCord Hotels, was opened on Amsterdam’s Java Island on the city’s IJ river. It set a precedent both for hybrid modular standards and being the Netherlands’ most sustainable hotel.
And earlier this year, SeARCH followed-up with Juf Nienke, one of Amsterdam’s first timber housing projects.
“The Dutch tendency is to be entrepreneurial, which is why you see innovative buildings like Hotel Jakarta, that was pioneering in wood construction,” says Iris Kampers, ESG advisor at Savills, Netherlands. “People do tours of the building to get inspiration and to ask, ‘how does that really work?’”
Hotel Jakarta came to be when the city council wanted a special hotel concept, both architecturally and as part of its public programming and sustainability plans. As a company, SeARCH has already designed a lot of timber buildings.
The first two floors of the hotel, including the swimming pool are built on concrete. Floors three to nine are made up of 176 modules, with a wooden support structure, that went on site in 28 days.
“We took a long time to design the modules up front,” says Kathrin Hanf, project architect for Hotel Jakarta for SeARCH. “It was at the start where most time was spent because we were building in the river, and you didn’t see any progress. But as soon as we went above ground, and used the timber modules, they were all placed on site in three weeks.”
Jakarta’s sustainability credentials start with a subtropical garden at its heart, that regulates temperatures, while the four-star hotel is an energy neutral building and rated BREEAM Excellent, helped by 350 solar panels.
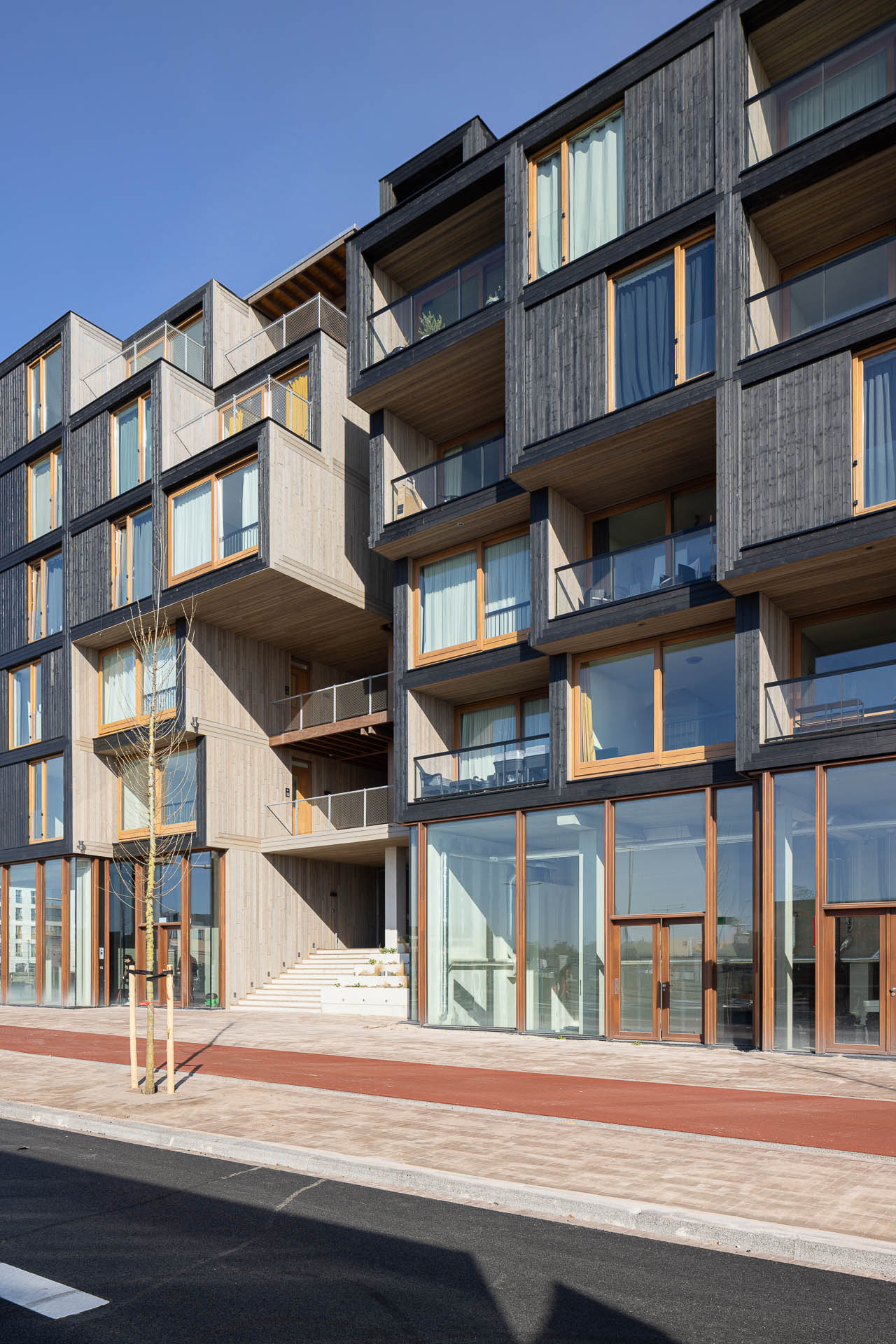

Photos of Juf Nienke, courtesy of SeARCH
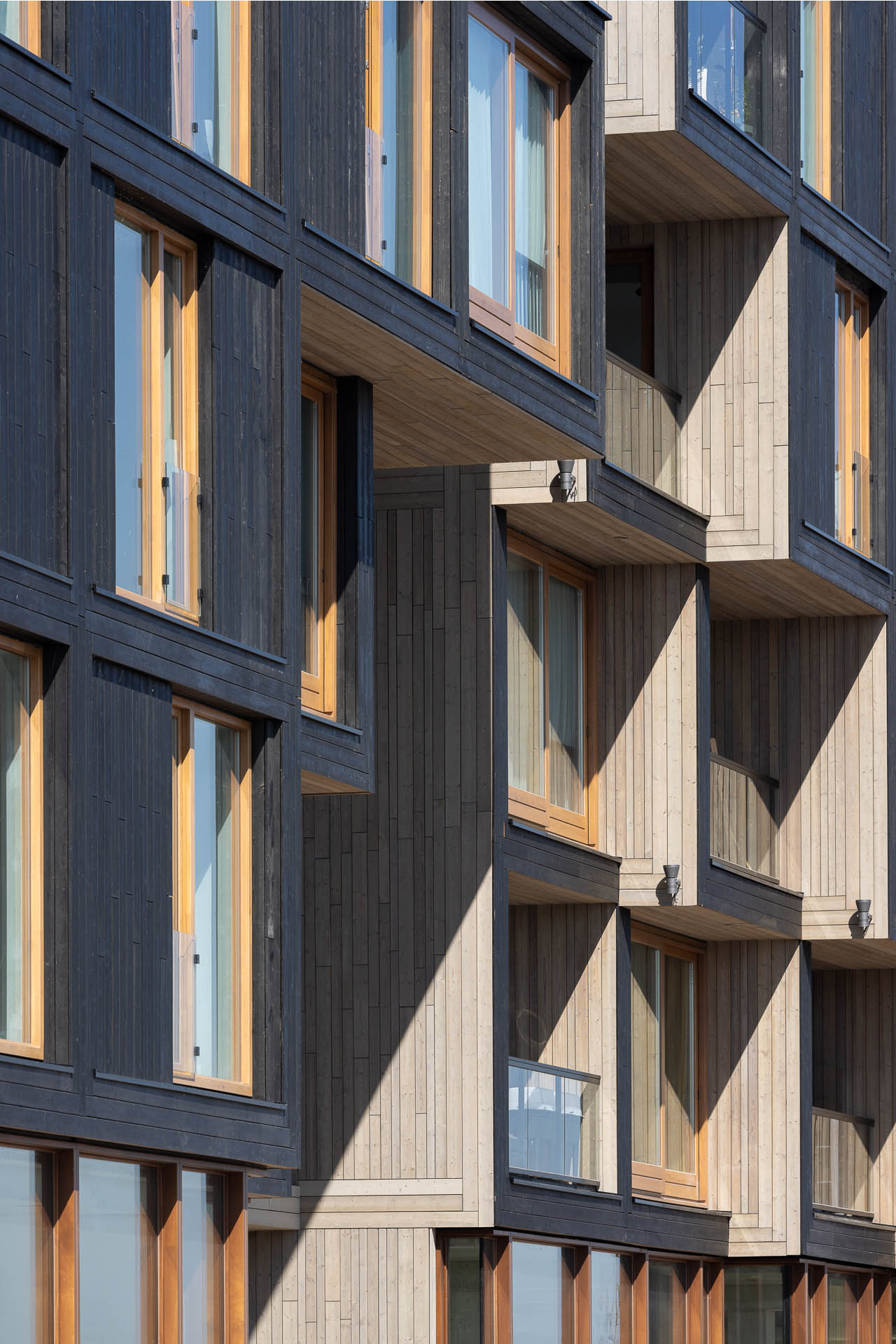
The way forward
Setting another milestone is Juf Nienke, a 61-unit residential hybrid modular development for essential workers and private family rental. The project is a circular apartment building, with fully timber modules stacked in different ways high above a grand staircase creating a large vertical void.
There are both single module apartments and multilevel homes, and the main 15-metre-high wooden structure sits on concrete base of parking and a commercial plinth.
Hybrid modular “is definitely a way forward in construction,” says Kampers. And with the government in the Netherlands pushing for more of these types of buildings, all eyes will be on the country as it continues to advance in hybrid modular development.