Glass windows date back to Roman times, when the earliest examples were often a greenish-blue colour with the aim of letting light in rather than letting people look out. However, centuries of product innovation later, the key area we have failed to address is significantly reducing greenhouse gas emissions associated with glass production. This remains high and difficult to abate using existing technologies.
Flat glass manufacture is energy intensive due to the high temperatures required to melt the raw materials, including sand, soda ash, limestone and dolomite, as well as the fact that kilns have to run continuously for up to 50 hours. Temperatures of around 1,600oC are needed to make float glass (which comprises 80% of all flat glass) and minimise defects that can alter light transmission and transparency.
Burning fossil fuels to heat furnaces accounts for 75–80% of CO2 emissions in the sector, so switching to a carbon neutral energy source would represent a significant reduction, but it faces challenges.
The viability of three renewable power options are assessed by Glass for Europe, the trade association for the EU’s flat glass sector, in a report published last year. It considers biogas technically possible, but the limited quantities currently available make it unfeasible.
The supply of hydrogen, through a modified gas grid, would require research to adapt furnace technology, said the report, and the flames produced would provide relatively low radiation heat transfer needed to contribute to the efficiency of flat glass making.
Electric melting is available for small furnaces, with a capacity of under 200 tonnes a day. But it still needs to be demonstrated successfully using renewable energy sources in large furnaces, such as those used in float glass production.
To support net zero targets, Glass for Europe calls on governments to develop a strategy for the production, storage and distribution of biogas, hydrogen and carbon-neutral electricity to ensure a reliable and cost-efficient supply for the future.
Glass Futures, a not-for-profit company creating a global centre of excellence for glass making, is working with flat glass producers worldwide to reduce the carbon intensity of glass manufacture.
Rob Ireson, innovation and partnership manager at Glass Futures, says: “We are seeing a collective movement from the glass industry towards low carbon melting technologies. By moving primary melting energy towards electrification, hydrogen and biofuels we will see a drastic reduction in carbon emissions from glass manufacture over the coming years.”
Other international research aims to spearhead innovation in this area. As part of a £166m UK government funding package to support industrial decarbonisation in the UK, £4.7m will be used to establish a new research and innovation hub, led by Cranfield University, to support industries including glass, cement and metal.
Under the same initiative, Yorkshire-based Saint-Gobain Glass will receive £1.4m to build a new flat glass production furnace to improve the efficiency of its UK plant and cut emissions.
Capturing industrial emissions
Even if carbon neutral power sources are identified and implemented, they do not address process emissions resulting from the decomposition of raw materials, mainly sodium carbonate, limestone and dolomite, which are responsible for 15–25% of emissions in flat glass manufacture.
Many in the sector are pinning their hopes on carbon capture usage and storage technologies (CCUS) as a potential solution with various research and pilot projects currently underway.
The company C-Capture recently agreed to work with glass manufacturer Pilkington to assess the possibility of using its unique and relatively inexpensive CCUS technology to capture CO2 emissions from glass production.
It claims the approach uses 40% less energy than other commercially available technologies and addresses the difficulties associated with capturing CO2 emissions. These emissions in glass production are caused by high levels of impurities from nitrogen oxides and sulphur oxides.
The glass industry has long understood how increasing the use of cullet (recycled glass) in its processes can reduce emissions by lowering melting temperatures and the volume of virgin raw materials required. Greater use of mineral waste streams from other processes, such as carbonate-free slag from the metal industry, could generate further carbon savings.
However, recyclable material is often under-utilised in the sector due to poor segregation of waste throughout the supply chain. The glass industry is working with glass recyclers and other stakeholders to see how additional sources can be made available.
“The advent of building deconstruction and design for circularity will pave the way for much higher recycled content within flat glass manufacture, which currently lags behind the packaging sector in recycling rates due to poor cullet availability,” says Ireson.
“Glass makers need to figure out how to get products to last five or more times the life expectancy of today.” Simon Sturgis, Targeting Zero
Longer lasting glass
Recycling is the least effective option in the ‘Reduce, Reuse, Recycle’ hierarchy of waste management, so a greater focus on extending the longevity of manufactured flat glass products, avoiding replacement, could significantly cut carbon.
Simon Sturgis, founder of carbon consultancy Targeting Zero, who has written official policy on embodied and whole life carbon for RICS, says: “Glass makers need to figure out how to get products to last, not just double or triple, but five or more times the life expectancy of today.
“Double glazed units are a big embodied carbon problem because suppliers won't provide a warranty for more than 15 to 20 years, and windows are not expected to last more than 30-40 years. Consequently, buildings have to remove all their windows very frequently, it’s an incredibly carbon intensive business.”
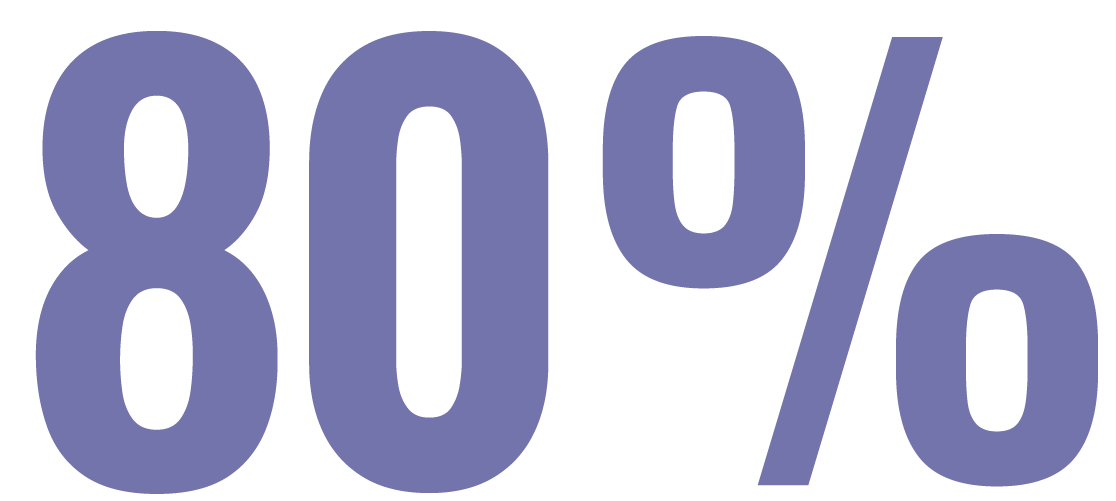
Up to 80% of CO₂ emissions in the glass sector come from burning fossil fuels to heat furnaces
More in this series
This article is part of a series on the 75 per cent problem posed by Bill Gates – how the world can reduce three-quarters of man-made emissions by 2050 to avoid catastrophic climate change.