Architect’s render of the Britishvolt gigafactory in Blyth
Giant manufacturing plants known as gigafactories are needed to produce the batteries that will power a new generation of electric vehicles, and as such will provide an essential element of the global effort to reduce carbon emissions.
To date, Asia has led the world in battery production, and China already has 100 such facilities. The US and Europe have lagged far behind, with only a handful operational so far, but many more are planned. In the US, 13 will come online by 2025, according to the federal government, while Europe is expected to have 27 factories operational by 2030.
Battery industry research body, the Faraday Institution, estimates that in the UK alone 10 gigafactories will be needed to supply the automotive industry, each producing around 20 gigawatt hours (GWh) of capacity a year. Several commercial players have joined the race to produce the UK’s first large-scale battery manufacturing operation, including Nissan, which is planning a 9GWh plant in Sunderland, and the West Midlands Gigafactory near Coventry Airport.
Britishvolt is aiming to get there first by getting its £3.8bn gigafactory in Blyth, Northumberland operational by 2025. “In our assessment, this is the only UK gigafactory site that can be completed within the next five years,” claims Paul Franklin MRICS, the company’s vice president for property, infrastructure and PMO. With a 255,000m2 footprint, and 418,000m2 of total floor area, the plant will be one of the largest industrial buildings in the UK and will eventually have a planned capacity of 30GWh.
Car manufacturers will only continue to operate in the UK if there is domestic battery production to support them, argues Franklin. “Some of the statistics suggest 50% year-on-year growth in the market. These batteries are expensive and heavy, with challenges around how we transport them. And UK battery manufacturers can trade into the EU zone without tariffs, while our competitors in China or other jurisdictions will face punitive tariffs from 2027 onwards.”
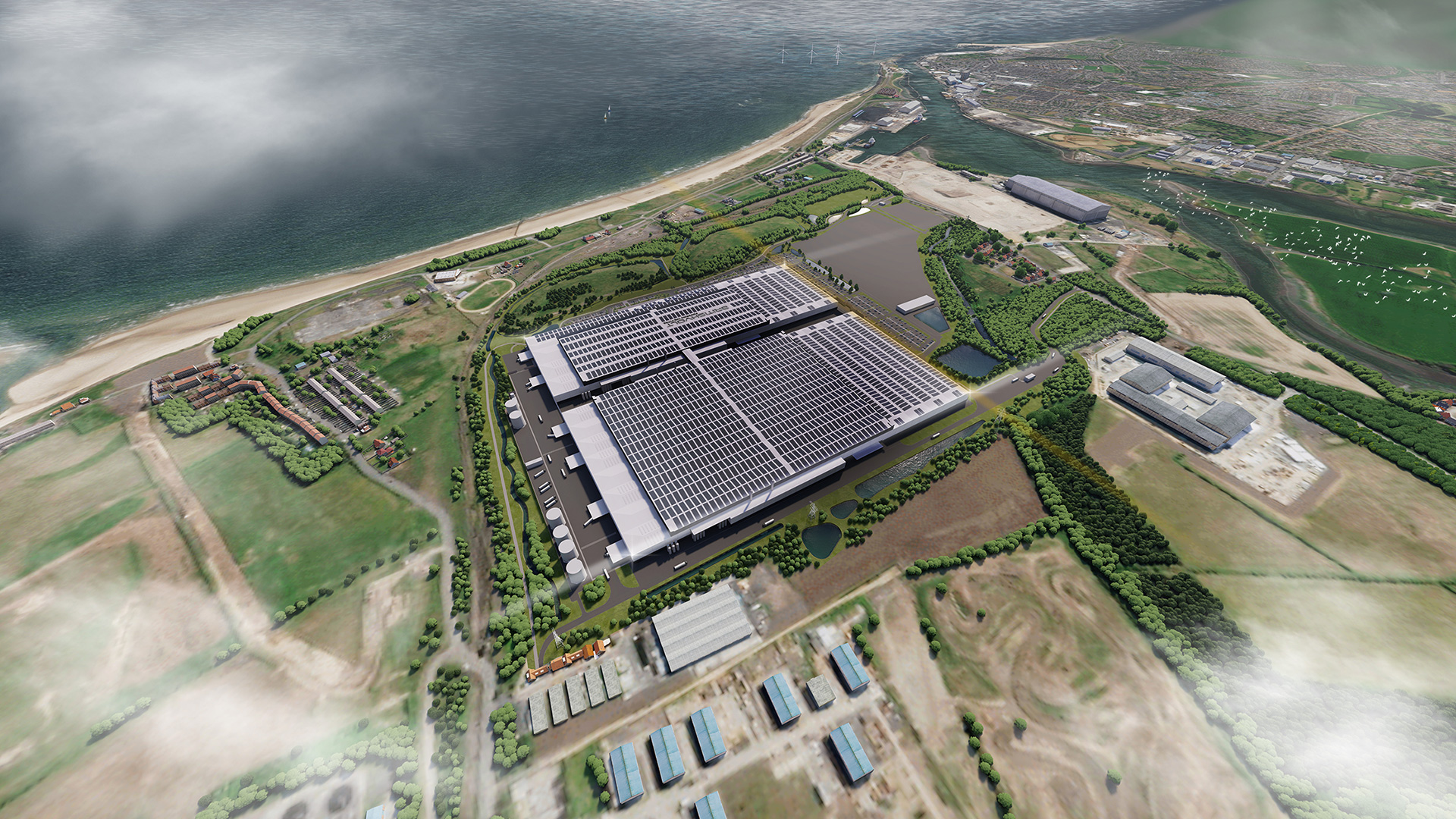
Aerial render of the Britishvolt gigafactory
Renewable energy sources
Britishvolt assessed 65 potential sites in 2019-20 before settling on a 93ha former power station site near Blyth, which it bought from Northumberland County Council. As well as being a large, flat piece of land, the site benefits from excellent connections to power infrastructure, with a full connection to the national grid. Meanwhile the North Sea Link interconnector cable, which joins the energy systems of Norway and the UK, enabling the sharing of renewable energy between the two countries, makes landfall at Blyth.
When those factors are combined with the proximity of offshore windfarms in the North Sea, and solar panels on the factory roof, Britishvolt claims that it will be able to power the factory entirely from sustainable sources.
Detailed planning permission was granted in July 2021, and contractor ISG is carrying out pre-construction works, including bringing power cables into the site, as well as remediation, site stripping, deforestation and road construction. While the enormous building envelope is scheduled to be finished in 2025, the factory’s production lines will be brought online in phases, depending on which customer is being served, and the technology that is being employed.
Mark Walker MRICS, head of process engineering, is charged with procuring the equipment that will go into the factory. “There's a lot of detailed information that the build team need from us, because ideally, what we'd like to be able to do is build the building around the equipment,” he says. To do that, data is being sourced from equipment manufacturers to create a digital twin of the factory’s environment and processes. Franklin says: “I've been told by reliable sources that it is the largest BIM model that AutoCAD [design software for architecture and engineering] have ever had on their system.”
Work at this scale creates challenges
The construction programme is highly involved, with work on the building envelope expected to still be underway while the first manufacturing equipment arrives on site. The process is further complicated by the fact that some of the technology with which the building will eventually be filled is still under development.
The sheer scale of the factory also presents challenges: “With the construction teams and our suppliers, we're looking at a point where you've got maybe 3,000 to 3,500 people working on the site at any one point as a peak, and deliveries of materials, goods and equipment coming in every two minutes,” says Walker. “There's a significant logistics exercise being created as part of the build programme, just for the first phase we're doing now.”
Funding construction is a further difficulty in a period when inflation and supply chain disruption is fuelling soaring material and construction cost increases. The government has pledged to contribute an undisclosed sum, reported to be around £100m, and work so far has been paid for by Britishvolt’s own equity. The factory was originally scheduled to open in 2023, before the date was adjusted to the end of 2024, and subsequently pushed back to 2025.
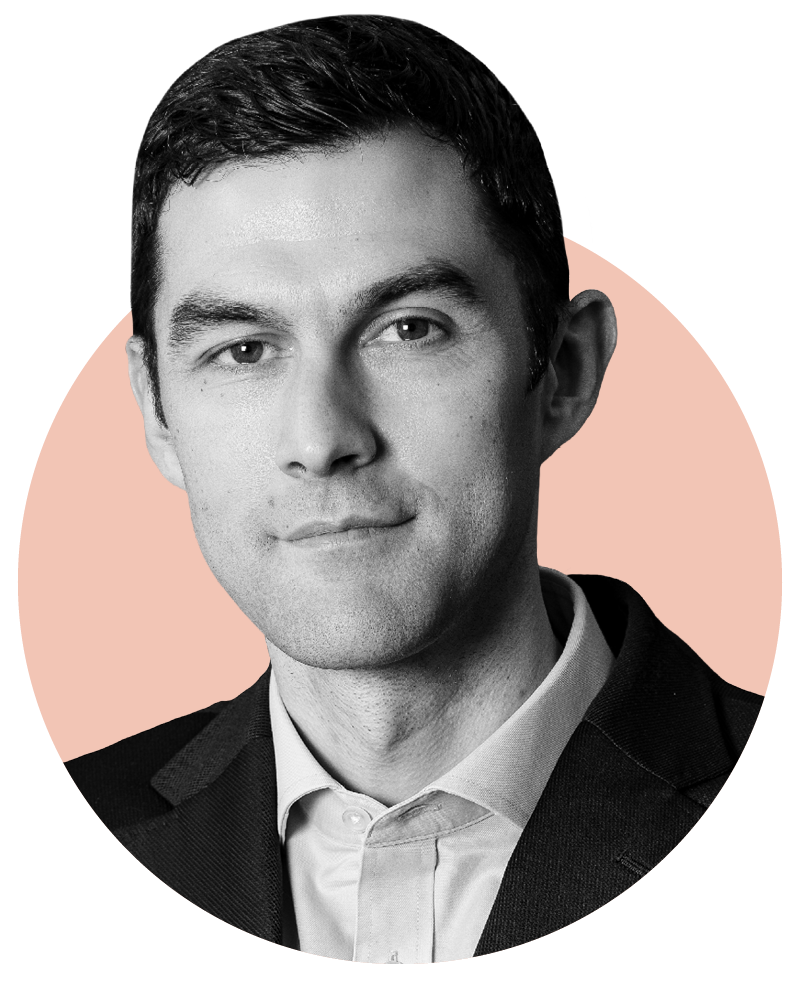
“It is the largest BIM model that AutoCAD have ever had on their system” Paul Franklin MRICS, Britishvolt
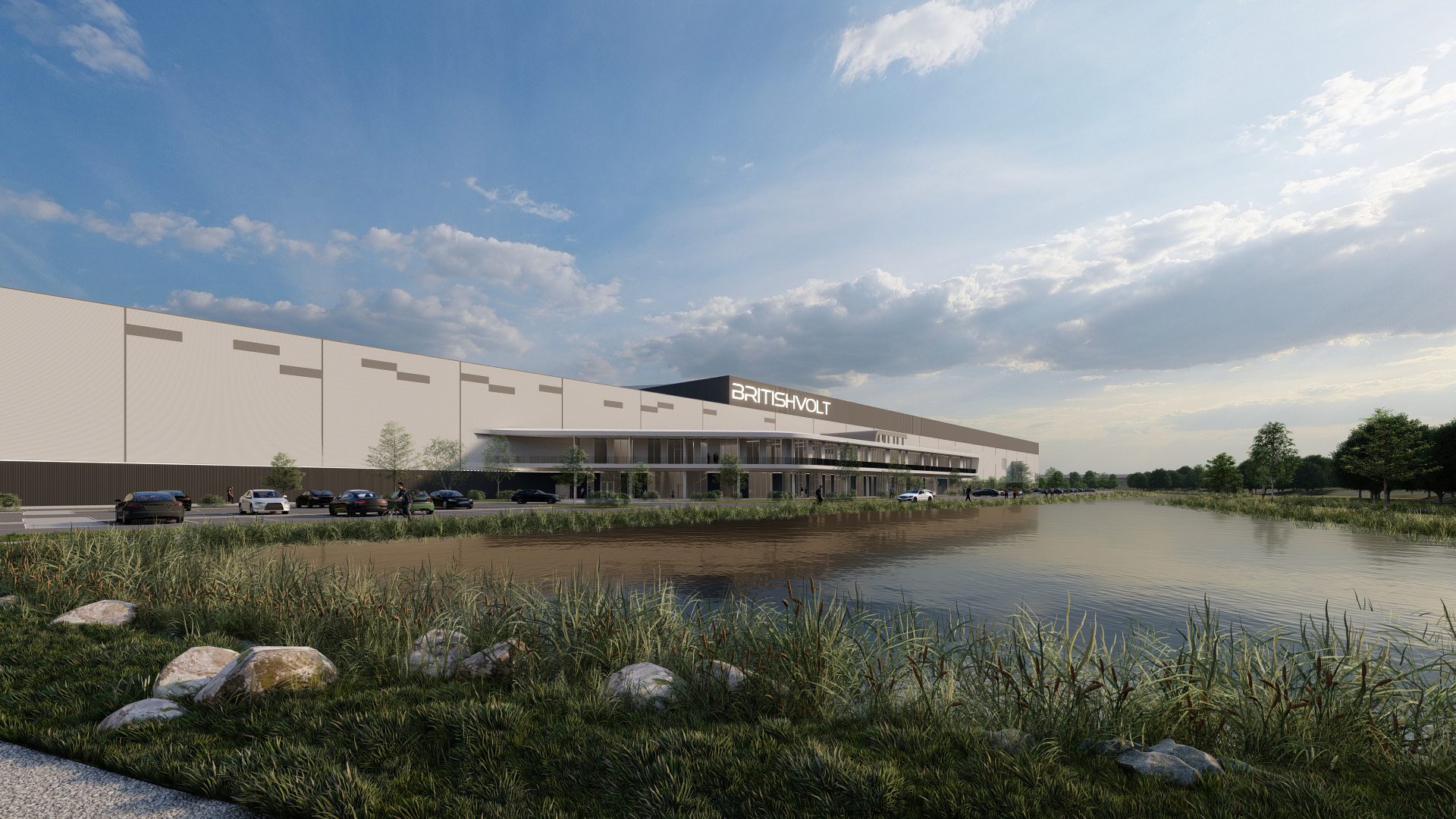
Lakeside render of the Britishvolt gigafactory
Economies of scale
While the design is being fine-tuned, Franklin’s team is taking the opportunity to value engineer the scheme, “to really understand in light of scarcity of supply and the state of the market, how we can best deliver the construction project.” The scale of the programme, he says, represents a challenge, but also an opportunity. “If we can shave a little bit off the clean and dry rooms [where lithium batteries are manufactured], for example, that is a huge saving in terms of capital, but also operational costs.”
Meanwhile, Walker is managing the setup of a “scale-up” facility, located in the West Midlands, which will act as a smaller testbed for manufacturing processes. And estates manager Rebecca Reilly MRICS is progressing plans for a supplier park alongside the main plant. “We are working very closely with Northumberland County Council, which owns the land, to bring some of the surrounding plots back into use,” she says. “We are talking to potential suppliers, including companies from America, Australia and South Korea. We will take a long leasehold on those sites, which could provide employment for around 500 people on top of 3,000 jobs in the main gigafactory.”
While it is the statistics about the gigafactory’s scale that catch the eye – Britishvolt’s website boasts that it will cover an area equivalent to 50 football pitches – the project has significance that goes far beyond “building a shed,” concludes Franklin. “We are developing something that is going to transform this part of the north-east of the UK, generating thousands of jobs in a clean and green sector, and will also support the UK in moving to net zero.”
Update, January 2023
On 18 January 2023, Britishvolt announced it was going into administration.
Update, February 2023
On 27 February 2023, it was announced that Australian firm Recharge Industries had bought Britishvolt.
Update, April 2024
On 15 April 2024, BBC News reported that plans to build a battery plant had collapsed and the site may be developed in to a computer data centre.
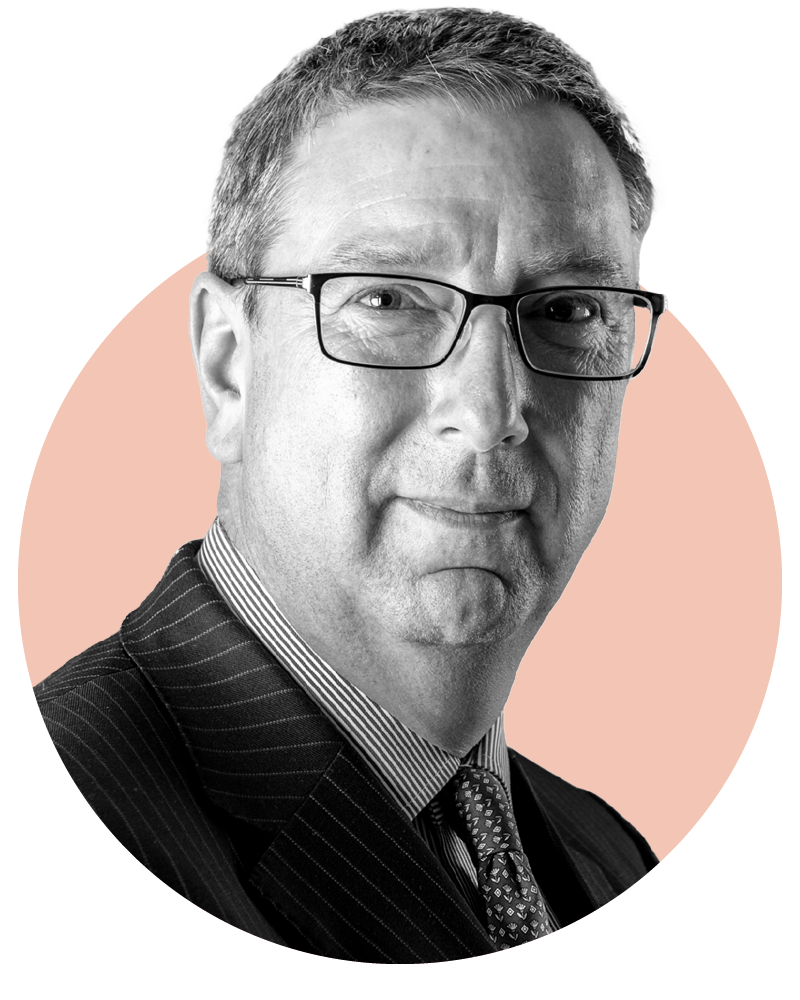
“You've got maybe 3,000 to 3,500 people working on the site at any one point” Mark Walker MRICS, Britishvolt