Stadium 974, Doha
Battered by harsh weather and waves, the humble steel shipping container has been a critical enabler for world trade for more than 70 years.
That physical resilience has also given it a successful second life as the structure for many types of building. ‘Cargotecture’ started out as an exciting low-cost, lightweight form of construction and, since the mid-2000s, has accelerated to become a ubiquitous feature of modern life.
Shipping containers are now used to build everything from restaurants, to shopping malls to housing, hotels and art venues, with a greater focus on permanent in situ projects.
The 12m x 3m x 3m steel boxes offer an ‘edgy’ urban design aesthetic and several advantages over traditional construction methods. They are strong, durable, mobile and adaptable, with a modularity that allows them to be stacked or combined in different ways. Reappropriating used containers is better for the planet, avoiding the need for new materials, especially energy intensive steel and concrete.
But this unique form of construction also faces challenges. Containers may be good for transporting fruit, veg and electronics, but according to some critics, not for housing people because of their minimal space and issues with poor insulation, ventilation, and comfort. Investigations have uncovered problems with detailing and quality control, with sustainability called into question when new containers are specified over redundant boxes.
Chris Medland, director of UK-based architect One-World Design says: “When the shipping container presented itself as a cost-effective solution for housing it was jumped on and architects tried to make it work as best they could. That such homes are now being described as unfit for human occupation is of no surprise, the fad was destined to fail.”
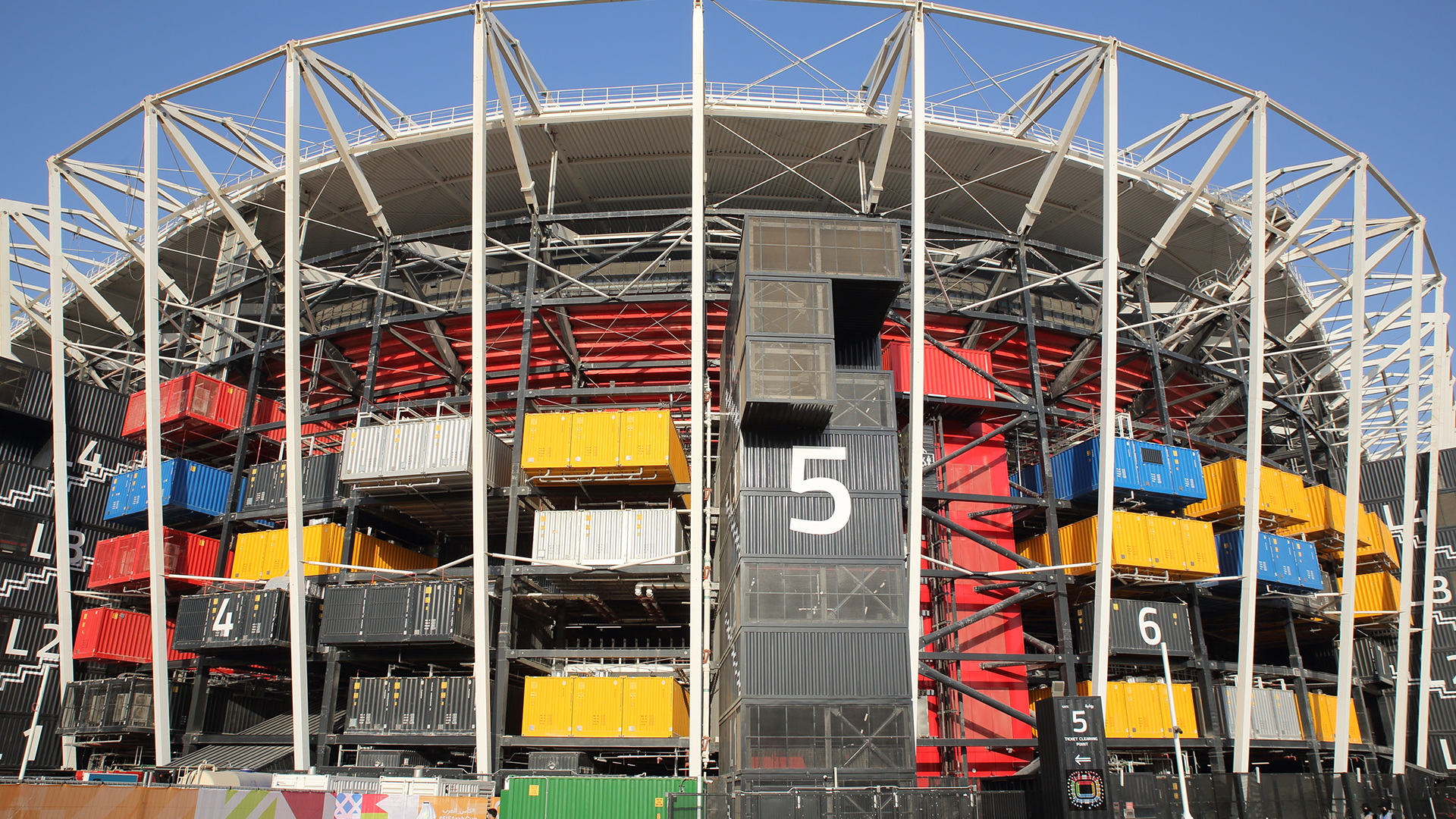
Stadium 974, Doha
Boxing clever
As the number of redundant shipping containers worldwide continues to increase – many sit idle in ports due to the expense associated with shipping them back to exporter – so does the number of construction projects looking to use them in creative new ways.
According to Conexwest, a US-based company that sells and rents shipping containers to commercial construction, there is a growing focus on the hospitality sector. Particularly hotels and entertainment venues, as travel and tourism continue to rebound from the pandemic.
“The public services sector has also seen increased container usage,” says Kyle Gier, marketing director at Conexwest. “Hospitals, schools and other infrastructure projects are turning to containerised solutions for both temporary and permanent needs.” This, he says, reflects broader economic and societal trends, with an increasing demand for flexibility, speed, and cost-efficiency in building solutions.
Recent years have seen containers deployed at an unprecedented scale, as demonstrated by Stadium 974, one of seven grounds built for the 2022 FIFA World Cup in Qatar, incorporating 974 shipping containers.
At the opposite end of the scale, small-scale cargotecture is entering new territory. Take for example, Barney’s Ruins in Ireland, a home formed from a single reclaimed shipping container that ‘floats’ elegantly above the 200-year-old ruins of a farm.
Intermodal containers find particular relevance in a maritime context, helping to inform the placemaking agenda. The MediaCity development at Salford Quays in Manchester features street food venues housed in shipping containers, as a nod to the former docks.
Leisure venue operator Stack advised on MediaCity and has used repurposed containers on several of its own schemes. Most recently in plans for an entertainment and leisure hub, in Manchester, housed in a two-storey shipping container complex.
According to Paul Wright, property director at Stack, the “real opportunity” is to use containers to create ecosystems where small businesses can learn to grow.
“The cost of the containers is less than a traditional build, which makes them more accessible to independent traders [when renting them],” he says, adding that this can help tackle the recent strains put on retail and hospitality businesses.
Housing solution
Around 1.6bn people worldwide lack adequate housing, according to a United Nations report, a figure that could rise to 3bn by 2030. That translates into a demand for 96,000 new affordable and accessible housing units every day.
Shipping containers have emerged as a potential solution for low-cost housing because they are typically much cheaper to build than conventional homes, avoiding much of the associated labour and materials costs.
Containers were used to create 232 housing units for homeless people in the Hilda L Solis Care First Village apartment block in Los Angeles. Another project, Watts Works, in one of South Central LA’s most underprivileged neighbourhoods, used 58 containers to create studio apartments for those experiencing homelessness.
Meanwhile, UK charity Help Bristol’s Homeless has created a village of 10 converted container ‘micro-flats’ in Bedminster each with its own mini-cooker, white goods, plumbing and electricity.
Several councils in the UK, including Brighton, Cardiff, Ealing (west London) and Bristol, have encouraged the deployment of container pods as temporary accommodation while residents find a permanent housing solution.
However, critics have questioned this approach. A report by the Children's Commissioner for England, entitled Bleak Houses, criticised temporary container homes for their cramped conditions and inhospitable temperatures.
Ealing Council was forced to decommission the Marston Court estate of temporary container homes in Hanwell, several years after it opened, after it was found to be not fit for purpose. Residents and former residents at its sister site, Meath Court in Acton, are now seeking compensation – claiming homes are unfit for human habitation, too hot in the summer and too cold in the winter, and mouldy due to poor insulation and leaks.
“That such homes are now being described as unfit for human occupation is of no surprise, the fad was destined to fail” Chris Medland, One-World Design
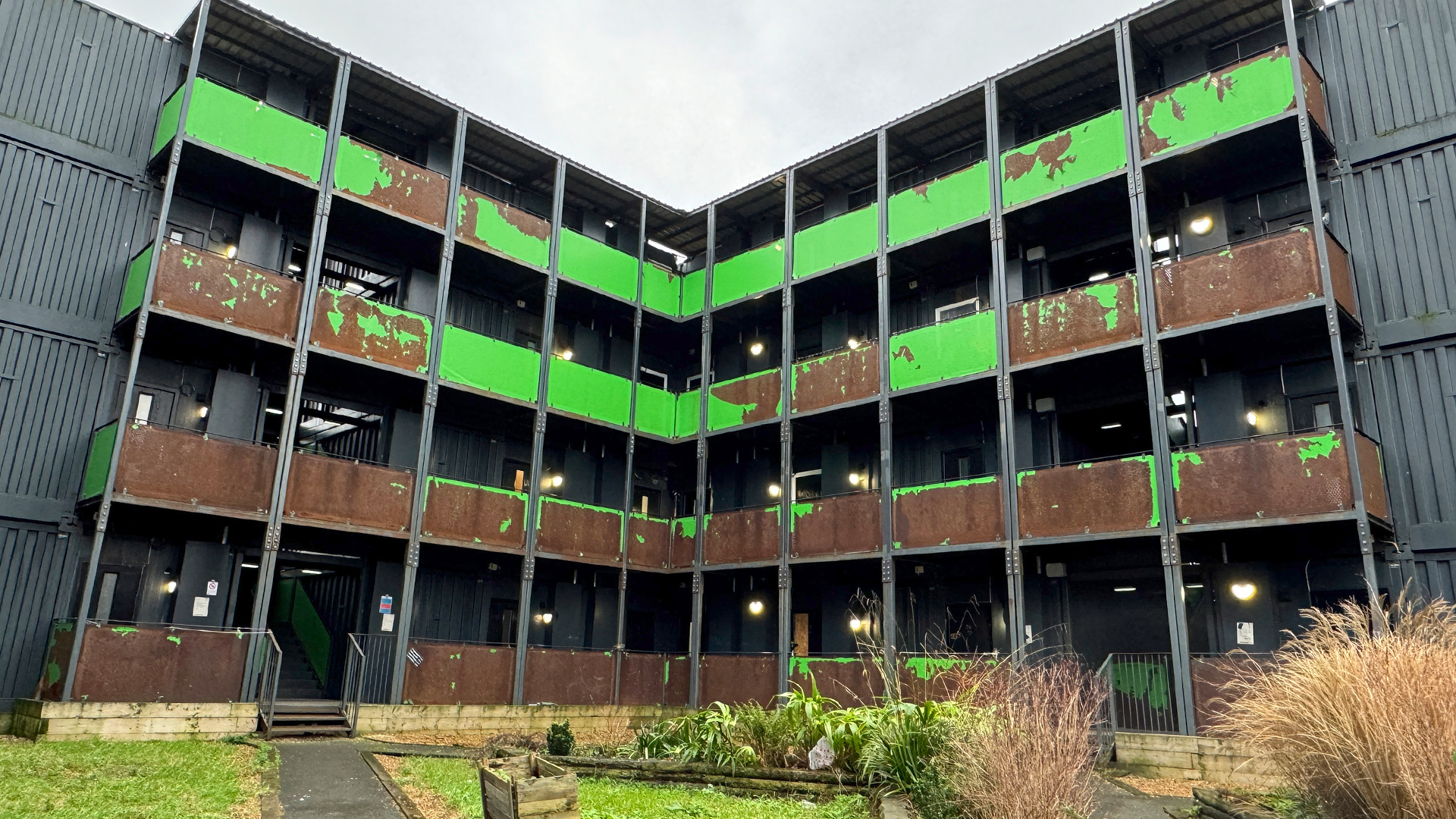
A view of Meath Court estate in Acton, West London. First launched in December 2017, the accomodation was made from shipping containers to house 60 families. Since then, the estate has fallen to disrepair. Photo credit: London News Pictures
It’s not difficult to see how such issues can emerge. Surrounded by corrugated metal, containers are ripe for condensation if not properly insulated, but insulating on the inside has the undesirable effect of reducing the amount of usable space. Alternatively, adding insulation to the exterior means adding cladding, potentially increasing costs, and eradicating the shipping container aesthetic.
According to Mark Hogan, founder of California-based architect OpenScope Studio, container floors also require a layer of insulation to prevent significant thermal bridging.
“Using metal boxes for structure, with only seven feet clear inside a built-out container, you are left with the Building Code minimum room width as your typical condition,” says Hogan. “That’s hardly ideal. If you are going through the trouble of building in a factory, why not build to a dimension that is appropriate for human habitation? It’s not difficult to create wider modular units offsite.”
Medland believes making containers habitable to modern standards means completely re-engineering them, in which case you are no longer dealing with a shipping container but “just material - a frame with some sheet cladding.” It’s better to design buildings from first principles, he adds.
Developers are drawn to containers, in part, because they provide a robust modular structure needed to build vertically or horizontally. However, this inherent benefit can fall away if significant alterations are made to the structure, or if containers are not stacked uniformly.
“Proposals for container schemes with cantilevers are common,” says Hogan, “but if you don’t stack containers on their corners, one above the other, their structure needs heavy steel reinforcement.”
It's common sense that used containers may have structural and stability issues that need to be resolved, but according to Wright, the fact they essentially provide a steel frame means buildings can easily have a lifespan of 25 years or more if they are looked after properly.
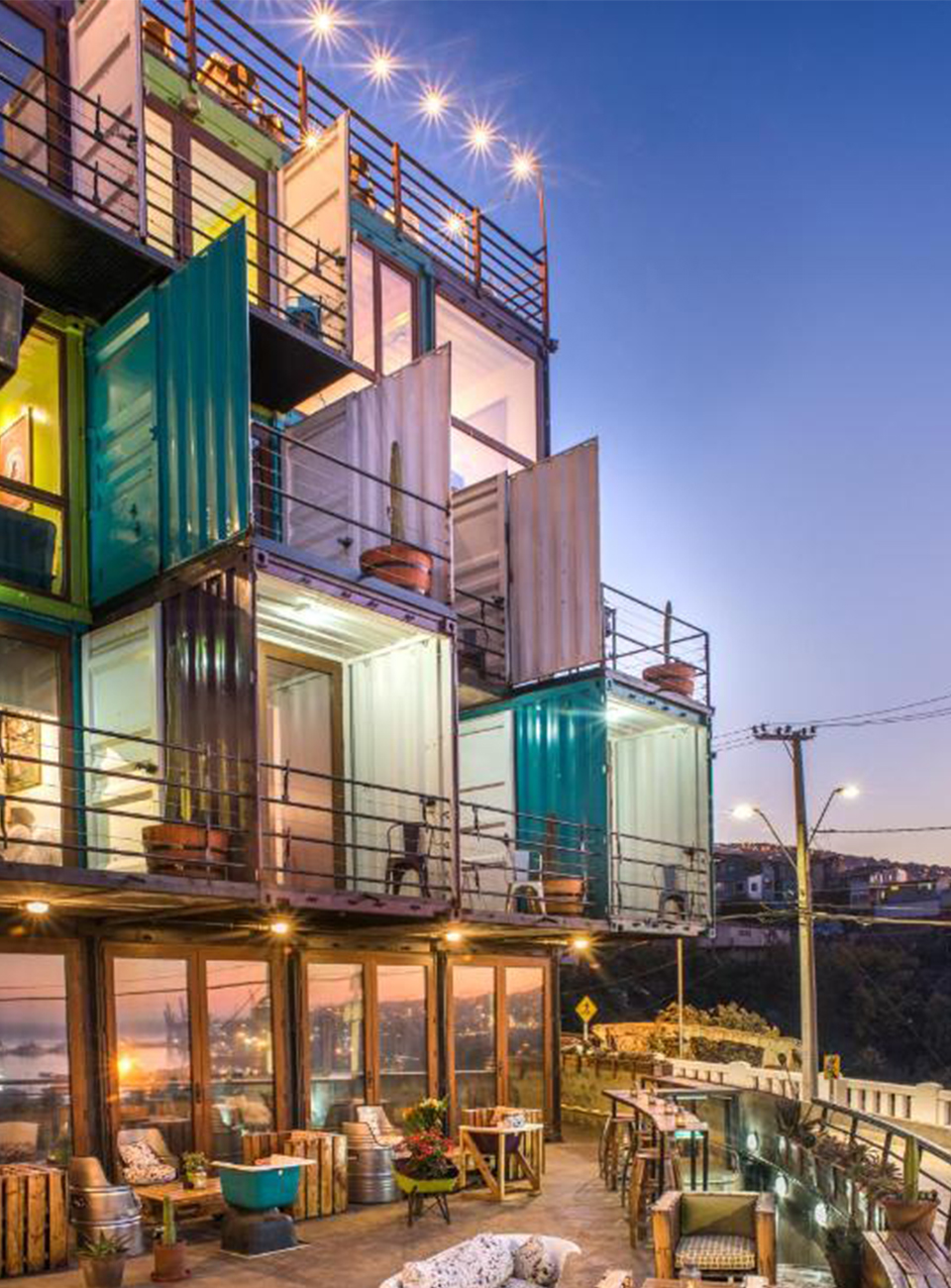
Winebox Valparaíso hotel, Chile
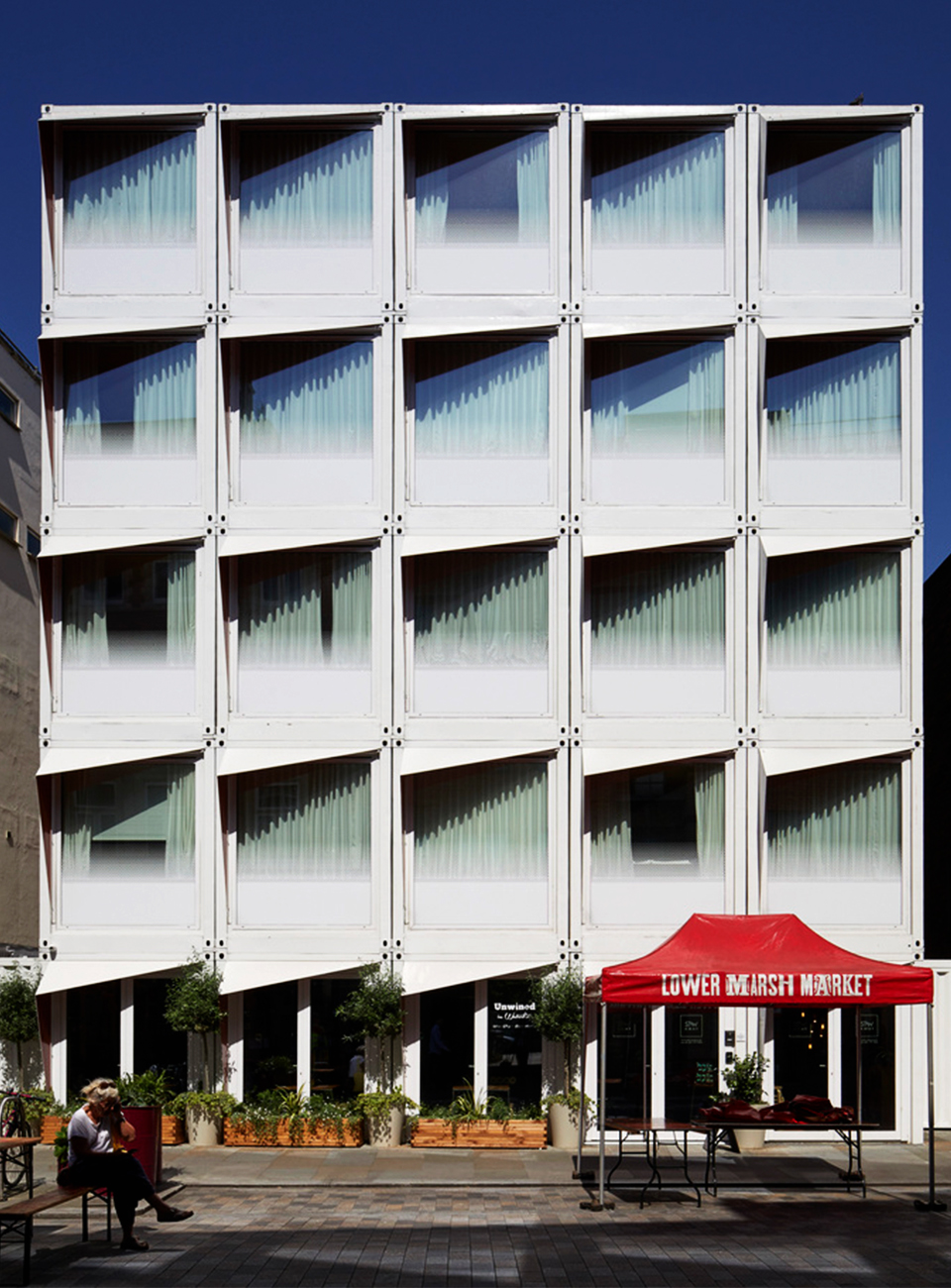
StowAway Hotel, London. Photography by Edmund Sumner

Geneseo Inn, California. Photography by Paul Vu
Due diligence
Structural problems and space constraints aren’t the only issues being uncovered on projects using shipping containers though, analysis has revealed issues with detailing, product testing and quality control.
Property and construction specialists Watts Group recently reviewed a student housing scheme in the UK constructed from converted shipping containers made in China. Among other things, the firm observed a lack of cavity barriers around windows and between containers, and ‘questionable’ fire protection to structural steel elements. There were missing or incomplete fire-stopping around services and ventilation ducts to containers and corridors, missing bolts to steelwork connections. In addition, alignment issues with containers had caused problems for site-assembled cladding.
Trevor Rushton FRICS, chairman at Watts Group, says: “There were problems, in some cases, in the alignment of levels between the concrete lift core and containers, and with buildings not complying with the planning consent and needing to be altered. In places they had to cut off the front of some containers and reduce the building height, taking the lids off some containers, which was perhaps due to mistakes made during the construction process.”
Another area of concern uncovered by the investigation was a lack of accurate as-built information, or adequate certification for things like fire testing and the performance of different combinations of materials. There were also missing technical approvals, such as those from the Water Regulations Advisory Scheme for plumbing and mechanical and electrical fittings.
According to Rushton, a combination of factors had likely contributed to problems, including tests applying in China not necessarily being transferable to the UK; mistakes made during construction, and poorly thought-out details.
“For anyone taking on this type of job, I'd be particularly wary to make sure that the paper trail is in place; that site quality control measures are properly applied, and that the detailing of external cladding is properly considered,” says Rushton.
Squaring the circular
Building with boxes poses challenges but there’s little doubting the scale of the resources available. According to the World Shipping Council there are around 17m shipping containers in circulation globally, and a large percentage of those sit unused in ports.
Repurposing them for construction should help cut demand for new building materials, with the added benefit that containers can be reused on future projects or recycled at end of life.
However, evidence suggests that some projects are buying new containers, rather than repurposing old ones, mitigating the environmental benefits.
While the majority of Conexwest’s construction clients purchase used containers, new containers are favoured on projects with “specific, long-term requirements”, says Gier, such as where containers require custom modifications or alterations like “insulation, ventilation systems, or electrical outlets.” New units are also purchased when “a pristine appearance” is needed.
Certain regional building regulations may also be holding back container reuse. For example, certain states in the US, including Los Angeles, don't allow the use of damaged or previously repaired containers, or those that are more than two years old.
Cargotecture remains hugely popular as a ‘cool’, low-cost and sustainable form of construction. Learning lessons from previous projects and experiences, such as those outlined here, will be crucial if it wants to ride that wave into the future.