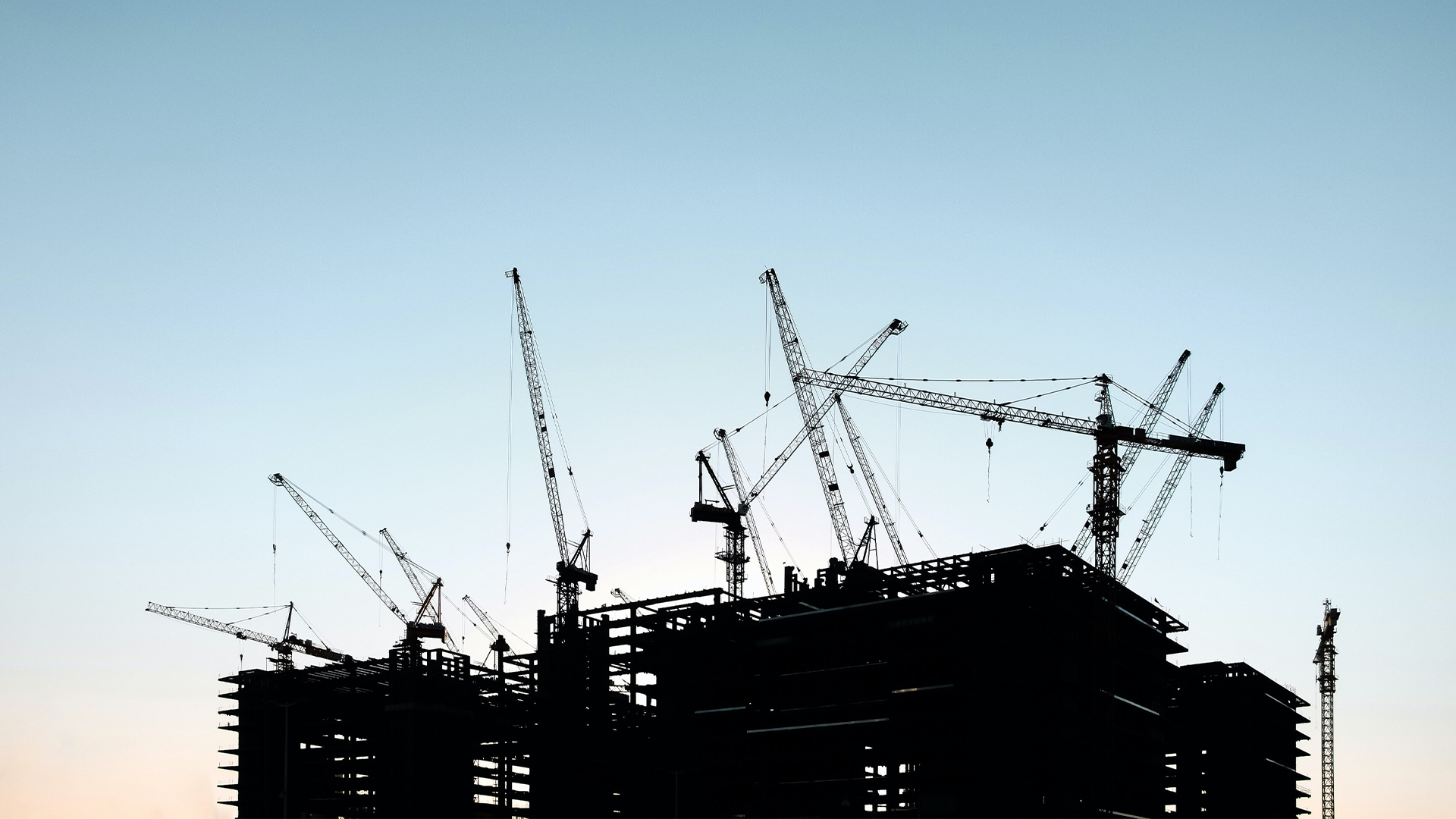
It’s been two years since the first lockdowns were introduced around the world, in response to the COVID-19 pandemic’s emergence in 2020. It hit the construction industry hard and national governments opted to tackle the problem in different ways with a variety of new regulations.
Modus has spoken to industry experts on four continents to find out what measures each region took and the impact it had on keeping things moving, even when life in many areas of society seemed to be grinding to a halt. How did employers keep a workforce together, what was the impact on supply chains and how were companies expected to mitigate the spread of COVID-19 within their own staff?

Hong Kong
FC Lee MRICS works for the Architectural Services Department of the Hong Kong Special Administrative Region government
When COVID-19 first appeared in January 2020, a lot of Hong Kong workers had been on the mainland celebrating Chinese New Year and seeing their relatives so, when the borders closed, they were stuck. We went into a very strict lockdown because the government has always pursued a zero COVID-19 policy – people coming in from outside had to go through 21 days quarantine in a hotel. That meant a lot of people, especially European and American consultants in the construction industry, decided to stay away.
The major impact was on the supply of materials and, of course, working on site. For two or three months at least, workers weren’t allowed on site at all, but gradually the government and industry implemented a lot of safety measures such as check-in systems and the Leave Home Safe app to check people’s movements. This let things get back to normal reasonably quickly. The past year of restrictions hasn’t had much impact on construction work as our new working practices had been adopted already – we had to stay 1.5m away from each other at first, then restrictions eased because of mask-wearing. Things were perhaps progressing at a slower pace, but that was partly down to the supply chain.
We’re in our fifth wave of coronavirus now and many of us are working from home. The professionals in construction have been able to use project management tools to minimise social interaction. Before it could be a real problem getting all the professionals together on site but now we just arrange a Zoom meeting and it’s far easier – we can have five or six meetings in a day instead of one or two.
Many of us quite liked the change and we have tried to digitalise the sector. There has been a lot of CCTV installed on sites so that the architect or surveyor can supervise remotely. We are also investing in more Modular Integrated Construction (MIC) to reduce the workforce on site; we can construct the major parts of a building in a factory which really cuts down on the labour needed.
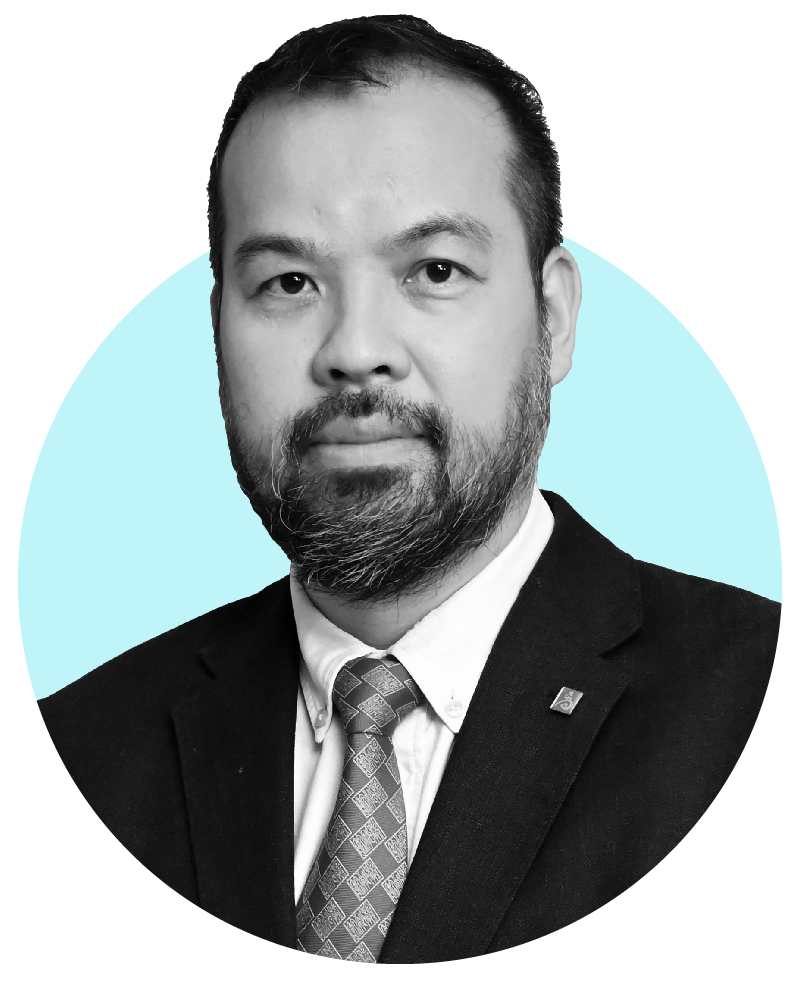
“Before it could be a real problem getting all the professionals together on site but now we just arrange a Zoom meeting and it’s far easier” FC Lee MRICS, Hong Kong

UK
Russell Lloyd MRICS and Roger Hogg FRICS work for the construction consultancy Rider Levett Bucknall
Roger: We were getting a lot of feedback from around the world that coronavirus was going to be big and, in March 2020, we were already running COVID-19 surveys. We knew it was a global issue and it was something that would affect everyone.
Russell: The industry went into defence mode immediately, but the outcome wasn’t as bad as initially thought. We started off with staff furloughs and then took our people off furlough pretty quickly. That was true of most of the construction sector. Almost without exception, sites closed during the first lockdown but were soon up and running in accordance with the Construction Leadership Council (CLC) safe operating procedures.
We were on the working party of the CLC, looking at the effect of safe working practices on productivity. There was a productivity drop because of the new social distancing protocols and productivity shortages but that got ironed out quite quickly through initiatives such as shift-working.
Roger: There was a concern from contractors that, although they could see their costs going up because of COVID-19, they weren’t necessarily going to pass them on in full. Some took a view on how much of those increased costs to pass through to bid but there’s been a danger also of winning too much work and then not being able to resource it.
Russell: It’s a complex scenario where input costs go up and there are companies going into receivership because of it. Supply of materials and labour became issues but, from a UK perspective, this was compounded by Brexit. There’s been a real interplay between COVID-19 and Brexit and I’d say Brexit is now presenting more problems. Design coordination has also suffered – architects working with engineers working with quantity surveyors, and that’s where coming out of COVID-19 restrictions has shown that there is no substitute for face-to-face workshops in some situations.
The impact on our graduate trainees has been hard, it’s a hands-on profession and it’s been very difficult training them remotely. Generally, it’s been hard to spread a company’s culture during the pandemic because there hasn’t been that workplace rapport – we’ve employed people who have come and gone during COVID-19 without even having a proper introduction to our office and company culture.
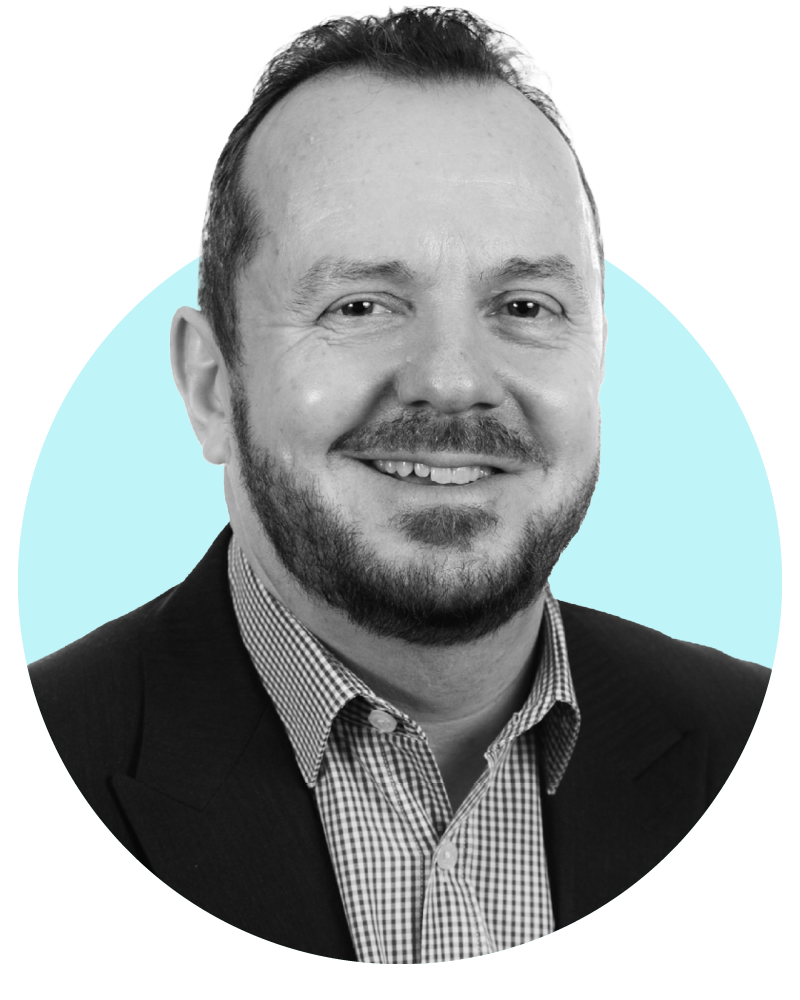
“There’s been a real interplay between COVID-19 and Brexit and I’d say Brexit is now presenting more problems” Russell Lloyd MRICS, UK
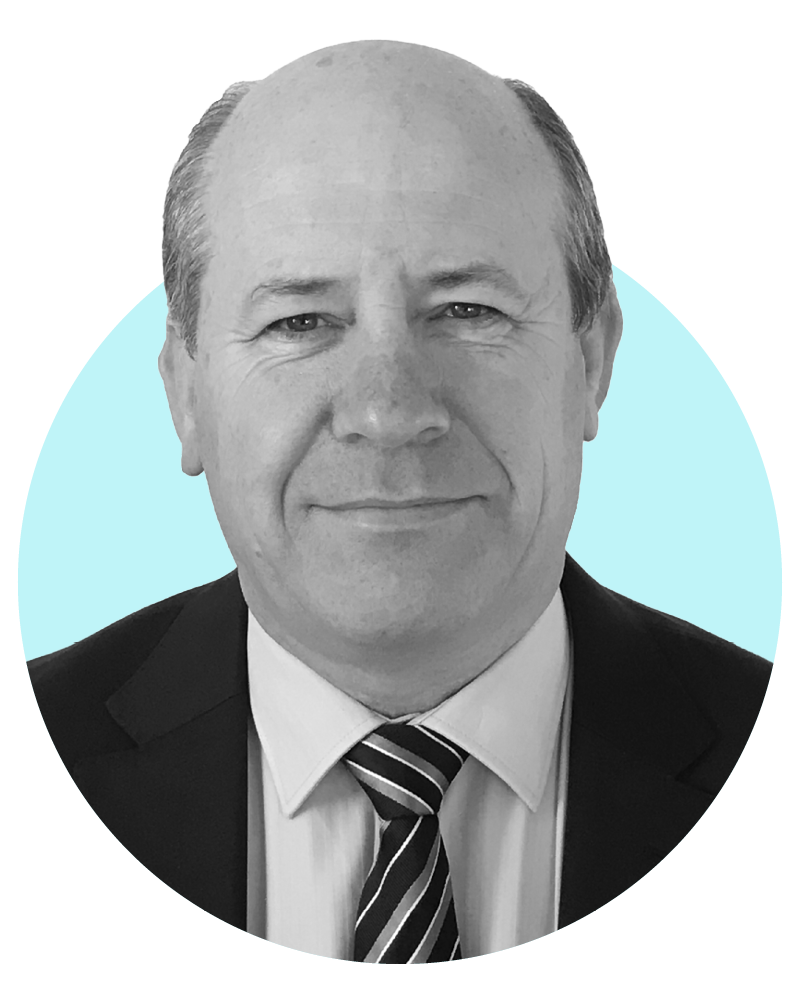
“There’s been a danger of winning too much work and then not being able to resource it" Roger Hogg FRICS, UK

Australia
David Chittock MRICS is a quantity surveyor and commercial manager working on Laing O'Rourke projects in Victoria
Melbourne and Victoria have been hit really hard by the pandemic. We’ve lived through one of the toughest lockdowns in the world but there was always a desire to keep the construction sector going. It’s a huge part of the economy so the Victorian government managed to keep state-critical infrastructure projects open and private projects went down to 25% of workforce on site at any time. We used a permit system to allow people in and out.
A lot of migrant workers went home and closing our borders has made this very challenging. We have a lot of people who want to come in to work but until recently there were very few skillsets being accepted. For example, quantity surveyors weren’t on the exemption list until recently and that has been very tough with the amount of infrastructure projects going on in Australia. There is the 2032 Olympics in Brisbane and a huge push to upgrade road and rail connections all over the country. We really need that workforce – white collar and blue collar.
Sometimes we were only given very short notice periods before a lockdown, which made it much harder to plan for them. You didn’t know if a lockdown was going to be a few days or four months. It was tough for everyone.
We implemented safe ways of working unbelievably well. All of the accommodations we made: putting workers into bubbles; the permit system; and the flexibility of working for white-collar workers, means we no longer have to be on site all day every day.
Our zero COVID-19 strategy stopped in about November last year [when Omicron first emerged]. We have more than 90% of people vaccinated, and to work in construction in the state of Victoria you have to be double vaccinated.
Despite all the challenges faced over the last couple of years, the construction industry has continued to grow at a rapid pace which has been a credit to everyone involved.
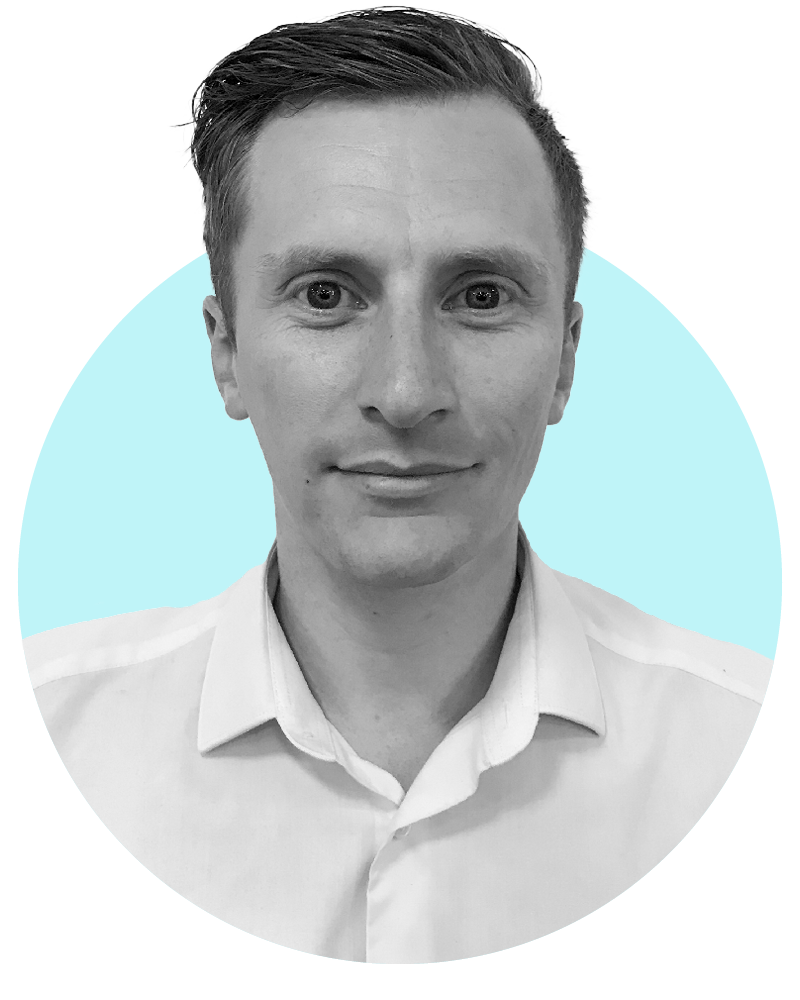
"To work in construction in Victoria you have to be double vaccinated" David Chittock MRICS, Australia

US
Eric Orquiola is chief estimator with PCL Construction based in Denver, Colorado
The pandemic really drove home how important it is to communicate. It opened the lines of communication with our clients, which has been a great outcome – speaking with them remotely has become normal. Having the right decision makers on the Zoom call, hearing what other people had to say rather than us relaying it to them, really helped facilitate decision-making.
Sometimes it meant we had to share some of the challenges that were facing the project. But bringing the owners and design teams into those conversations with suppliers and contractors was a positive – having the trades and the suppliers at the table gave everybody a voice. It became more collaborative and it turned out really well. Having the conversations with our clients and keeping communications open, so there were no surprises when it came to schedule milestones, was key.
[In Colorado] we were able to keep working, there were no site shutdowns as long as we complied with Occupational Safety and Health Administration (OHSA) rules and looked out for the wellbeing of workers. We were limited on the spacing, there were mask mandates and we had to change the order of some work because we couldn’t have all the workforce on top of each other, but it was an opportunity to identify lean practices – we could still be productive.
There was good communication around the supply chain and we came up with some great solutions for securing alternative materials domestically, to cut down on international procurement.
From our backlog, we’re seeing quite a bit of recovery – there are a lot of developments coming out, we’re seeing hospitality and retail rebound. There are great opportunities for recruiting, we’re looking for people in all positions.
The other positive is the continual assurance of making sure that we are complying with OSHA and making sites safer.
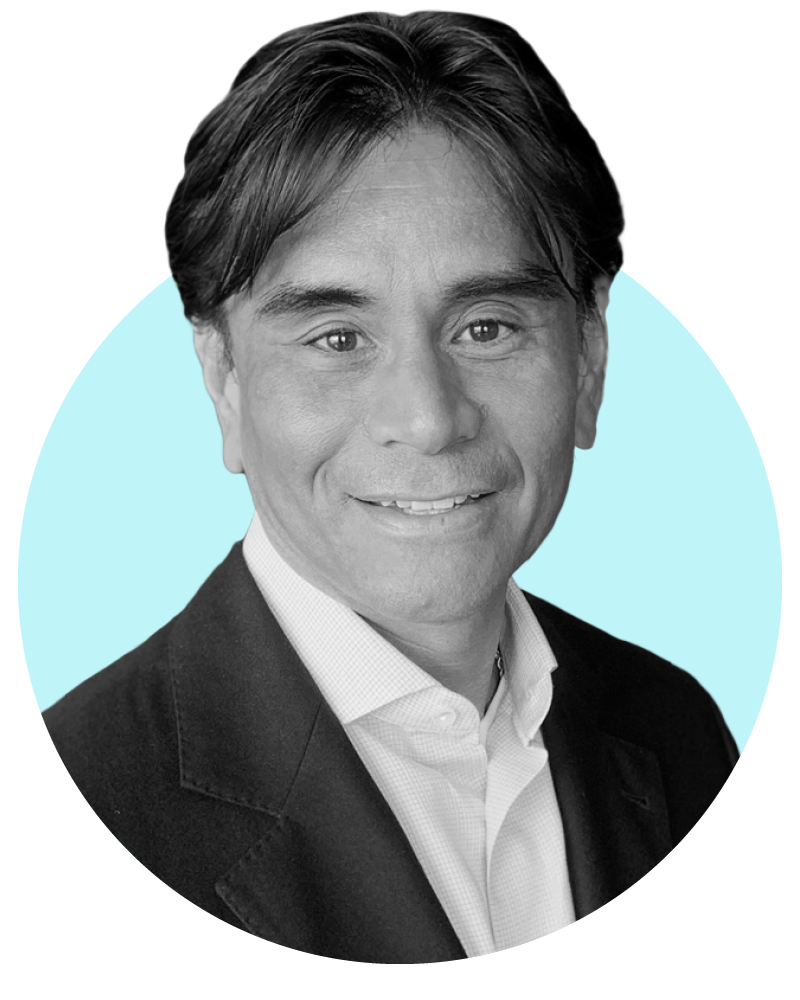
“We came up with some great solutions for securing alternative materials domestically, to cut down on international procurement” Eric Orquiola, US